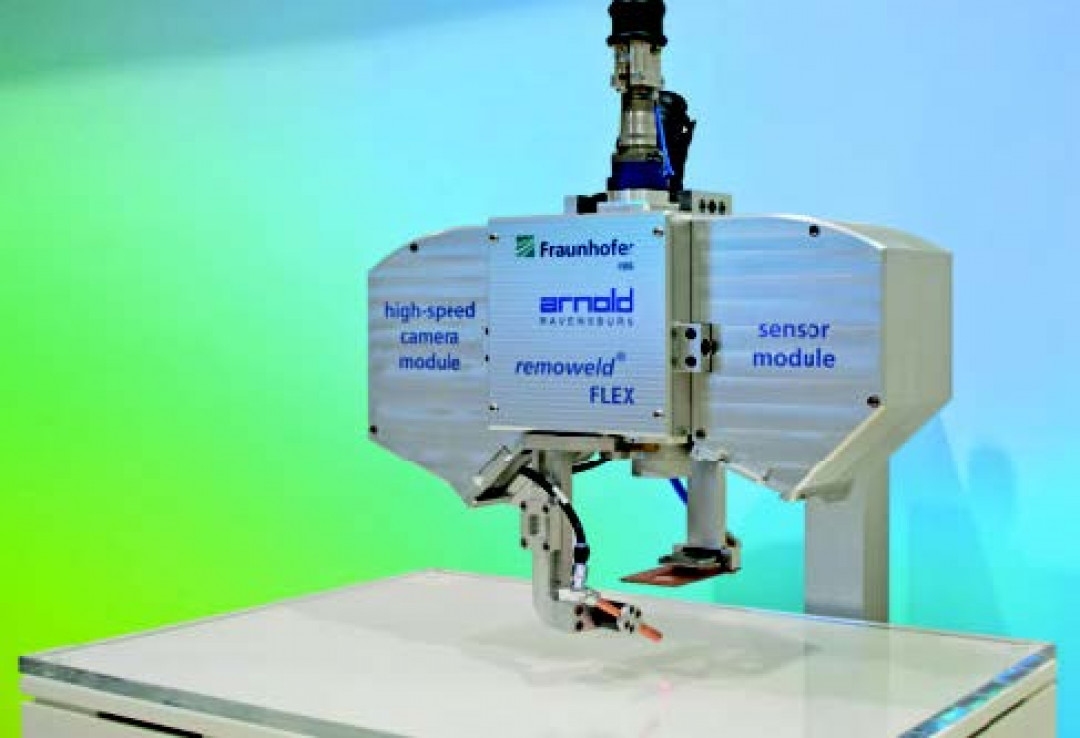
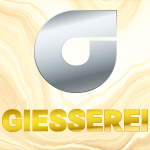
Gussbauteile aus Aluminium werden in der Serienfertigung in vielfältigen Bereichen und hohen Stückzahlen eingesetzt. Immer wenn derartige Gussbauteile in bestehende Konstruktionen eingesetzt werden, entstehen zwangsläufig vielseitige fügetechnische Fragestellungen. Druckgussbauteile gelten bisher als schwer bis nicht schweißbar. Dies liegt insbesondere an den eingeschlossenen Gasen, die während des Schweißprozesses zu großen Poren und Auswürfen führen können. Die erzielbare Nahtfestigkeit wird dadurch stark herabgesetzt. Neue schweißtechnische Verfahrensvarianten können diesem Umstand entgegenwirken und die erzielbaren Verbindungsfestigkeiten deutlich steigern. Bei diesen Technologien handelt es sich einerseits um das Laserstrahlschweißen (LBW) und andererseits um das Rührreibschweißen (FSW).
Moderne Leichtmetall-Gusskomponenten tragen in entscheidendem Maß zum konstruktiven Leichtbau bei gleichzeitig hoher Funktionsintegration der Bauteile bei. Insbesondere die Erzeugung filigraner Rippen zur Erhöhung der Bauteilsteifigkeit von strukturrelevanten Gussknoten und die Ausformung von dünnwandigen Pumpen- bis hin zu komplexen Kurbelgehäusen mit hervorragender mechanischer und thermischer Belastbarkeit, sind für die Automobilbranche zum technischen Standard geworden. Für Leichtmetall-Legierungen auf Al-Basis wird dabei überwiegend das Atmosphären-Druckgießverfahren eingesetzt. Limitierend für die weitere Verbreitung solcher Komponenten im konstruktiven Leichtbau sind fehlende fügetechnische Möglichkeiten mit effizienten Verfahren. Der Einsatz von Strahlverfahren, insbesondere mit dem Elektronenstrahl, eröffnete in der Vergangenheit Insellösungen. Diese waren jedoch aufgrund der unzureichenden Weiterentwicklung des Verfahrens mit hohen Kosten verbunden. Zudem standen fehlende Ansätze zur Steigerung der realisierbaren Stückzahlen, insbesondere im Hinblick auf die zunehmende Gleichteileproduktion, der Verbreitung des Verfahrens entgegen. Große Vorteile für die Produktion bieten hier Laserstrahlschweißverfahren, wie sie in der Massenproduktion flächendeckend eingesetzt werden. Als problematisch galt bisher das Handling der schmelzflüssigen Phase, bedingt durch den hohen Gasgehalt im Druckgussbauteil, der zu starker Porosität und stochastisch auftretenden Auswürfen der Schmelze führte. Druckdichte Schweißverbindungen konnten nicht garantiert werden [1, 2, 3].
Anders stellt sich die Situation mit der gegenwärtigen Entwicklung der Laserstrahlquellen dar. Getrieben durch die kontinuierliche Weiterentwicklung der Strahlwerkzeuge in den letzten Jahren und den erheblich reduzierten Investitionskosten pro Kilowatt Laserleistung steigt dessen Attraktivität für die Massenproduktion weiter. Ergänzt durch die Verfügbarkeit von effektiv arbeitenden Optiksystemen zur Strahlablenkung eröffnen sich neue Lösungsansätze, insbesondere für den Einsatz bei schwierig schweißbaren Werkstoffen. Beim Laserstrahlschweißen (LBW) können nun Strahlquellen höchster Qualität eingesetzt und durch geeignete Strahlablenkoptiken eine hochfrequente Strahloszillation im Schmelzbad erzeugt werden. Dies ermöglicht reproduzierbare, qualitativ hochwertige Schweißverbindungen. Motiviert von der Idee, die Prozessführung so weiterzuentwickeln, dass bestehende Qualitätseinschränkungen überwunden werden, war das Forschungsziel des am Fraunhofer-IWS entwickelten Ansatzes, den Schweißprozess aktiv durch hochfrequente Strahloszillation zu beeinflussen und dadurch die Schweißnahtqualität deutlich zu erhöhen.
Weiterhin stand die drastische Reduzierung von Poren im Schweißgut sowie die sichere Vermeidung von Schmelzbadauswürfen im Mittelpunkt der Untersuchungen, um qualitätsgerechte Schweißverbindungen zu ermöglichen. Neben dem LBW steht mit dem Rührreibschweißen (FSW) ein weiteres Verfahren zum Schweißen von Aluminiumdruckgussbauteilen zur Verfügung. Das neuartige Verfahren eignet sich hervorragend für das Schweißen von Aluminiumdruckguss, da das Schweißgut prozessinhärent nicht aufgeschmolzen, sondern thermomechanisch bearbeitet wird. Dies verhindert die Freisetzung der im Gusswerkstoff vorhandenen Gase in den Fügebereich, sodass ein nahezu porenfreies Schweißgut entsteht. Abhängig von Bauteilgeometrie und -wandstärke birgt das Verfahren enorme Vorteile im Sektor der medien- und druckdichten Schweißanwendungen an gleichartigen und ungleichartigen Metallen. Je ein Beispiel des LBW und des FSW verdeutlichen im Folgenden die fügetechnischen Möglichkeiten zum qualitätsgerechten Schweißen von Aluminiumdruckgussbauteilen.
Stand der Technik
Laserstrahlschweißen
Ein Spezifikum für das Laserstrahlschweißen von Druckgusslegierungen sind Schmelzbadauswürfe, die unter anderem durch den explosionsartig freiwerdenden Gasdruck aus den herstellungsbedingt in der erstarrten Matrix vorhandenen Poren entstehen und in stochastischen Abständen auftreten. Druckguss weist darüber hinaus prozessbedingt sehr hohe Wasserstoffgehalte auf [4], wodurch beim Laserstrahlschweißen vermehrt Poren im Schweißgut entstehen (Bild 1).
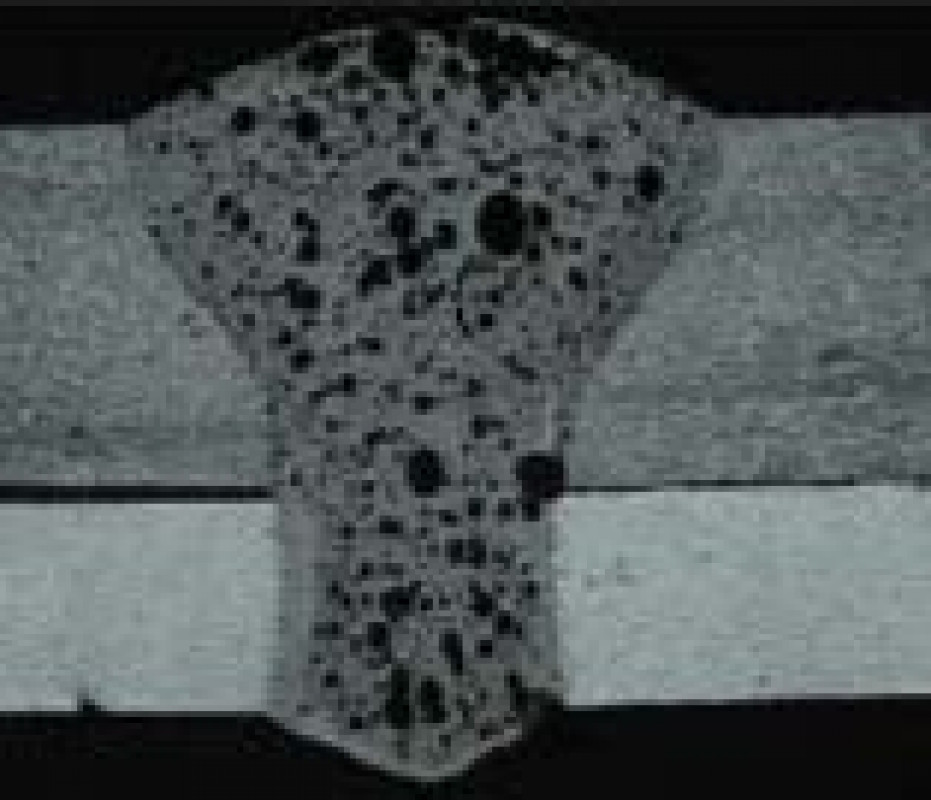
Ursachen für die bei Aluminium typischen Poren im Schweißgut sind vergleichsweise kleine Schmelzbäder mit geringer Lebensdauer und beschränkten Ausgasungsbedingungen sowie verhältnismäßig geringe Schmelzbadbewegungen. Der klassische Ansatz beim Laserstrahlschweißen technischer Al-Legierungen verwendet eine statische Strahlführung, bei der die eingebrachte Energie unterschiedliche Schmelzbadgrößen hervorruft. In der Forschung untersuchte oder als praxisnahe Lösungen beschriebene Verfahren zur Vermeidung von Poren sind gekennzeichnet durch statische Strahlformung oder dynamische Strahlführung. Die statische Strahlformung als Doppel- oder Mehrfachfokus hat die Verlängerung der Schmelzbadlebensdauer zum Ziel, um die Ausgasung der Schmelze zu gewährleisten. Darüber hinaus wird seit einigen Jahren das LBW unter Vakuum zur Erzeugung qualitativ hochwertiger Schweißverbindungen erprobt. Die komplizierte Prozesstechnik und –führung stellen jedoch die bisher bekannten Vorteile des LBW und dessen Wirtschaftlichkeit in Frage. Auch sind diese Ansätze ungeeignet, um massive Schmelzbadauswürfe zu schließen und eine homogene Nahtausbildung ohne Schweißnahtunterbrechungen zu gewährleisten. Hier greifen unter anderem dynamische Methoden, wie zum Beispiel die Strahloszillation, an. Durch eine schnelle Schmelzbadströmung soll eine Beschleunigung der Schmelzbadausgasung ermöglicht werden [1, 2, 3, 5]. Limitierend bei diesen Ansätzen sind die fehlende Möglichkeit, die Schmelzbaddynamik über eine Steuerung des Laserstrahls ausreichend zu beeinflussen, um Gasblasen zu entfernen sowie die ungenügende Führung der Schmelze zur Glättung der Nahtoberfläche nach einem Schmelzbadauswurf.
Bisher verfügbare Strahlablenkoptiken waren im Wesentlichen dafür konzipiert, einen statischen Strahl zu verschiedenen Schweißpunkten innerhalb eines definierten Feldes zu bewegen. Die dafür erforderliche Scan-Frequenz liegt bei maximal einem Kilohertz. Durch die bisher genannten Ansätze wurde weiterhin nicht sichergestellt, dass die Keyhole-Stabilität während des gesamten Schweißprozesses gewährleistet wird. Das Kollabieren des Keyholes und somit eine stark fluktuierende Schmelze während der Prozessführung, kann nicht verhindert werden und zusätzliche prozessbedingte Poren sind nicht vollständig auszuschließen. Das Ergebnis der genannten Ereignisse sind feine Spritzer, massive Auswürfe und eine Vielzahl von Poren im Schweißgut (Bild 2).
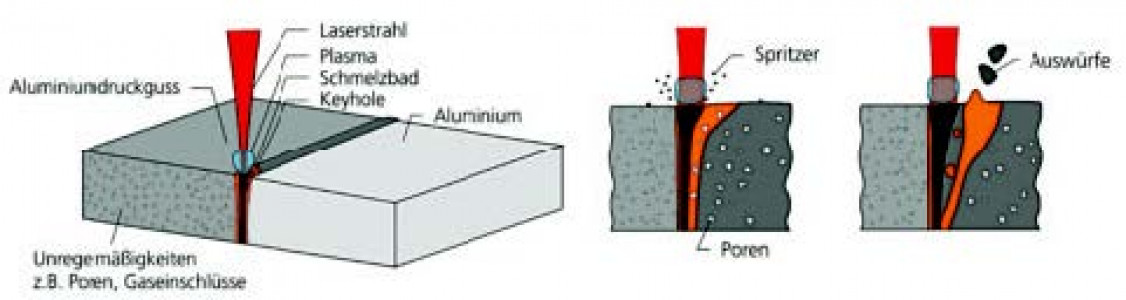
Rührreibschweißen
Das Rührreibschweißen (FSW, engl. Friction stir welding) ist ein Festphasenfügeverfahren, das sich insbesondere für das Schweißen von Aluminiumlegierungen und Al-Mischverbindungen [7] immer mehr durchsetzen konnte. Das Verfahren zeichnet sich durch einen geringen Wärmeeintrag aus und eignet sich zum Schweißen aller Aluminiumlegierungen [6].
Das FSW erfordert in der Regel ein rotierendes Schweißwerkzeug, ein Spannsystem zum sicheren Einspannen der Fügepartner und eine Schweißunterlage (engl. Backing), (Bild 3, links). Das rotierende Schweißwerkzeug (Bild 3, rechts) besteht aus einem Pin und einer Schulter. Zu Prozessbeginn wird das rotierende Werkzeug in das Werkstück gefahren, bis die Schulter die Werkstückoberfläche berührt und minimal eintaucht. Im Übergang von der Schulter zum Werkstück sowie im Pinbereich wird die erforderliche Prozesswärme durch Reibung und Deformation des zu schweißenden Werkstoffs erzeugt. Das Material wird hierbei nicht geschmolzen, sondern plastifiziert und in einen teigigen Zustand überführt. Durch das permanente Verrühren des Werkstoffs kann somit eine hochbelastbare Schweißnaht mit einer Festigkeit nahe der des Grundwerkstoffs erzeugt werden. Die dabei entstehenden Prozesskräfte werden über das Werkstück in das Backing abgeleitet.
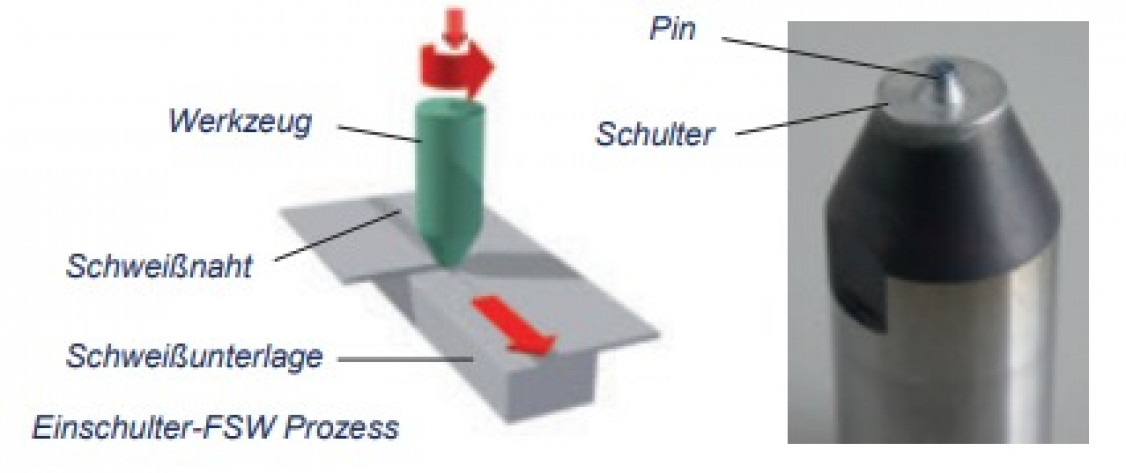
Laserschweißen von Al-Druckguss
Statt wie bisher Laserstrahlen mit großem Spot (bis zu 600 μm bei 4-6 kW Laserleistung) einzusetzen, findet für den neu entwickelten technologischen Ansatz ein Single-Mode Faserlaser mit sehr kleinem Spot (< 100 μm) und geringer Leistung (ca. 1 kW) Verwendung. Manipuliert wird der Strahl über einen für die Makrobearbeitung konfektionierten Scanner, der eine Strahloszillation im Bereich der Schmelzbadgröße zulässt. Somit steht ein neues Strahlwerkzeug zur hochdynamischen Modulation des Laserstrahls zur Verfügung. Die erarbeitete Hardware-Lösung ermöglicht die Strahloszillation im Kilohertz-Bereich auf einer dem Schmelzbad angepassten Größe von ca. 1,5 x 1,5 mm² (Bild 4).
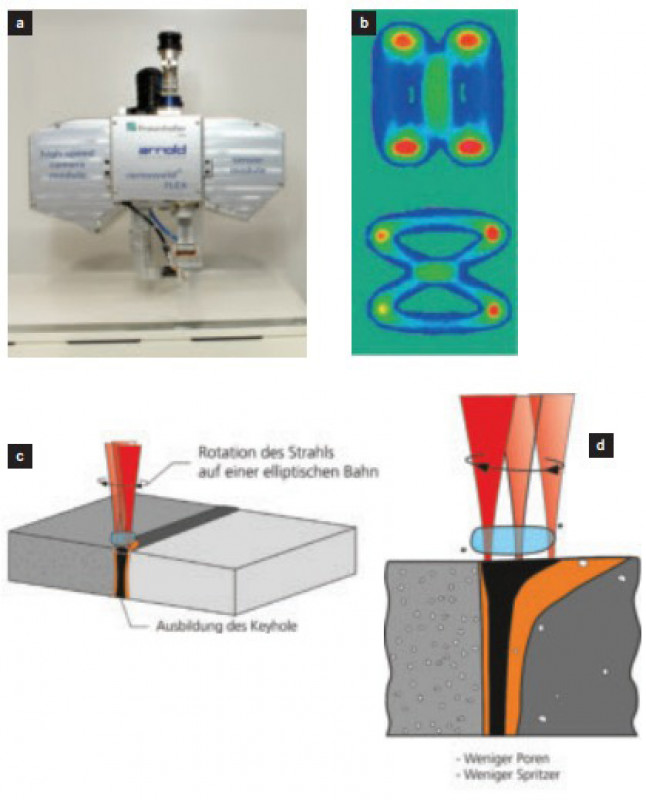
Zudem kann eine an die speziellen Bedingungen im Schmelzbad angepasste Oszillationsfunktion mit abgestimmter Laserleistungsregelung angewendet werden. Durch diese hochfrequente 2-D-Strahloszillation sind sogenannte Lissajous-Figuren abbildbar, die der Schweiß-Vorschubbewegung überlagert werden und somit eine gezielte Beeinflussung der Wechselwirkung zwischen Schmelzbad und Laserstrahl ermöglichen. Unter Berücksichtigung der hohen Schmelzbadviskosität von Aluminium lässt sich eine andere Schmelzbaddynamik erzeugen als es mit statischer Strahlführung möglich ist. Damit besteht die Möglichkeit der Keyhole-Stabilisierung, insbesondere bei akzeptablen Schweißgeschwindigkeiten. Die prozesstechnische Herausforderung hier liegt in der Ermittlung geeigneter Strahloszillationsparameter, die im Zusammenspiel mit der Schmelzbadviskosität eine angepasste Schmelzbaddynamik bewirken und die Stabilität des Keyholes erhöhen sollen.
Überführung in die Praxis
An einem Kundenbauteil aus Al-Druckguss (AlSi9Cu), welches mit einem Rohr der Knetlegierung AlMg5 zu verbinden war, wurde das LBW mit hochfrequenter Strahloszillation optimiert und konventionellen Laserschweißverfahren gegenübergestellt. Die Herausforderung lag in der Sicherstellung einer hochbelasteten, druckdichten Fügeverbindung, die auch nach Jahren im Betrieb mediendicht sein sollte. Das LBW stellt für diese Randbedingungen den idealen Verfahrensansatz dar, um stoffschlüssige und über die Lebensdauer druckdichte Fügeverbindungen zu erzeugen. Mit den zuvor durchgeführten Untersuchungen am gewalzten Blech war die Basis für das Verständnis der Wechselwirkungen zwischen hochfrequent oszillierendem Laserstrahl und Werkstoff gelegt.
Frühere Schweißergebnisse mit feststehendem Strahl bestätigten die bisher bekannten Erkenntnisse. Im Ergebnis des Schweißprozesses entstand eine Schweißnaht mit extrem vielen Poren (Bild 5). Die Aufnahme wurde einem Bereich entnommen, der auswurffrei ist. Die Schweißnaht wäre an dieser Stelle vermutlich druckdicht, es ist jedoch zu befürchten, dass unter zyklischer Belastung die Stege zwischen den Poren versagen und ein verzögerter Mediendurchtritt stattfindet.
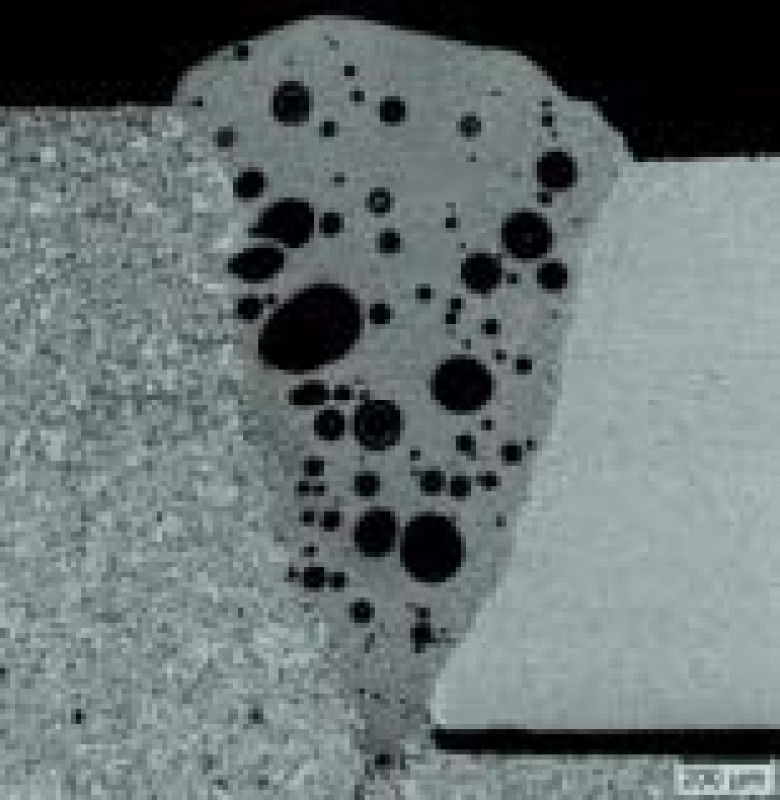
Die neuartige Schweißtechnologie des hochfrequenten Strahloszillierens wurde experimentell auf das Bauteil adaptiert und prototypisch bewertet. Die verbleibenden Poren ordnen sich vermehrt im Bereich des Druckgusswerkstoffs an. Weiterhin sichtbar wird, dass die überwiegende Anzahl der Poren nicht größer ist als die in der Grundmatrix präsenten Fehlstellen und gusstypischen Lunker. Die Gefahr eines Durchbruchs der Stege zwischen den verbleibenden Poren und damit das Versagen der Schweißnaht sind somit drastisch reduziert. Die Bauteile, die mit dieser Technologie geschweißt wurden, waren nach Vibrationstests beim Kunden weiterhin druckdicht. Der neue Technologieansatz zeigt für die Verarbeitung von Druckguss eine hohe Prozesskonstanz verbunden mit einer geringen Fehlerrate. In Bild 6 sind ein typischer Querschliff und ein Segment des rotationssymmetrisch aufgebauten Bauteils dargestellt.
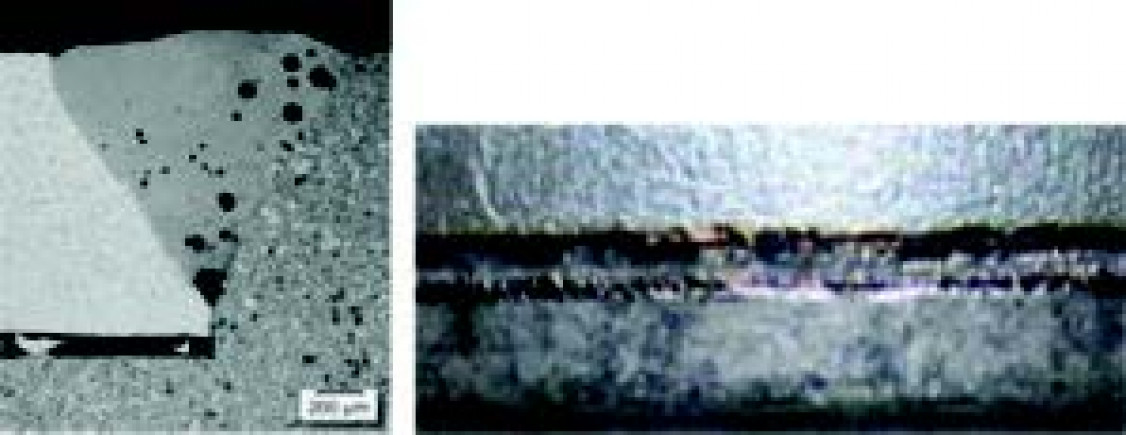
Rührreibschweißen am Beispiel von Al-Druckguss
In das Gehäuse eines Aluminiumdruckgussbehälters soll ein Deckel eingesetzt und druckdicht verschweißt werden. Der Deckel (Dicke 2,0 mm) wird hierzu in das Gehäuse eingelassen und mit einer geeigneten Spanntechnik fixiert, um ihn in Stumpfstoßkonfiguration zu schweißen. Die Schweißversuche wurden auf einer parallelkinematischen Anlage (Pentapod-PG-2000) durchgeführt (Bild 7). Diese multifunktionale Anlagentechnik eignet sich zum Rührreibschweißen, aber auch zum Fräsen und zur Anwendung laserbasierter 2-D- und 3-D-Bearbeitungsverfahren. Sie verfügt über einen Arbeitsraum von 6,5 m x 2,5 m x 1,5 m und eine Positioniergenauigkeit von +/- 10 μm. Für das FSW stehen hierbei neben der Kraft- und Wegregelung auch eine Drehmomentregelung zur Verfügung.
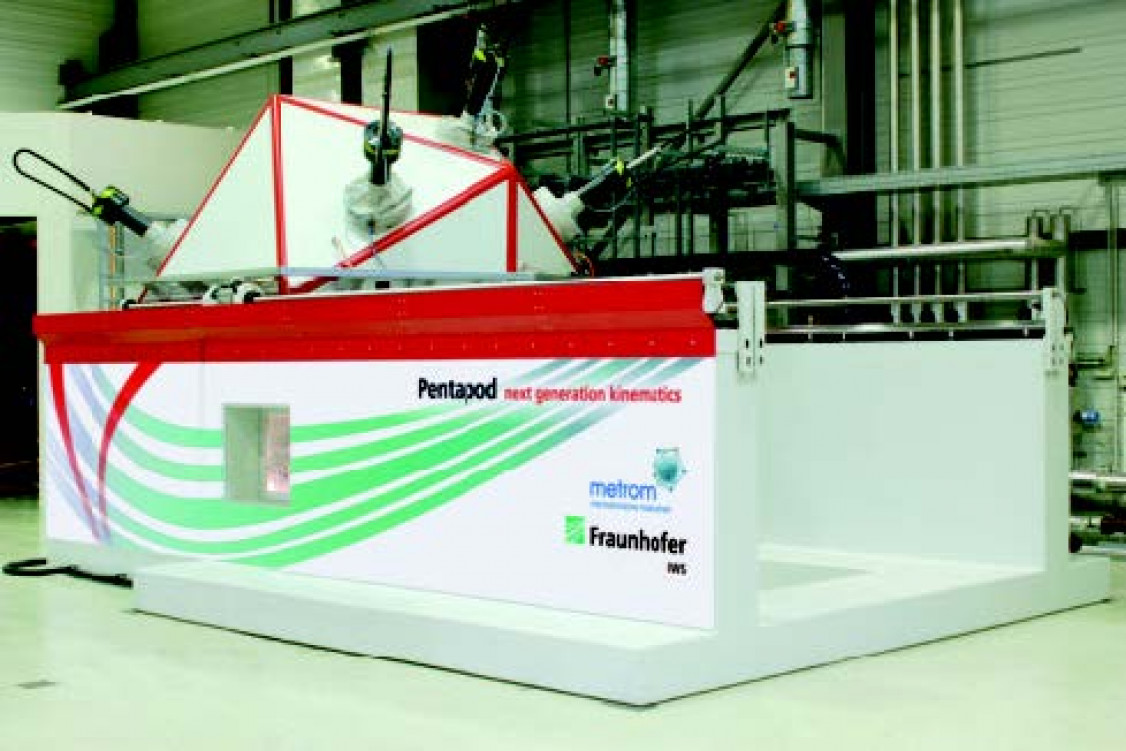
Beim FSW von Aluminiumdruckguss wird das porenbehaftete Material in der Fügezone durch die Rotation von Schulter und Pin des Schweißwerkzeugs verrührt. Unter Verwendung optimierter Schweißparameter wie Drehzahl, Vorschub und Prozesskraft wird das plastifizierte Material dabei mehrmals um den Pin bewegt, bevor es sich abkühlt und wieder in der Schweißnaht anlagert. Während dieses thermomechanischen Prozesses können die Gase aus den Poren entweichen bzw. werden auf ein unkritisches Maß feindispers in der Schweißnaht verteilt. Für das Schweißen des Druckgussbehälters kam ein Standard-FSW-Werkzeug, bestehend aus einer Schulter mit einem Durchmesser von 10 mm und einem konischen Pin mit einer Pinlänge von 2,0 mm zum Einsatz. Da es sich bei der Schweißaufgabe um eine kreisförmige Schweißnaht (Bild 8, links) handelt und ein druckdichtes Bauteil erzeugt wird, muss das Ende der Schweißnaht samt Pinaustrittsloch in einen unbelasteten Bereich des Bauteils außerhalb der Fügestelle gelegt werden. Im Ergebnis konnten Schweißnähte erzeugt werden, die einen sehr geringen Porenanteil aufwiesen (Abb. 8, rechts). Die Schweißnahtoberfläche besitzt die für das FSW typische feinschuppige Struktur. Das geschweißte Bauteil wurde einem Dichtigkeitstest unterzogen, bei dem es Maximaldrücken von über 20 bar unbeschadet standhielt. Die beispielhafte Anwendung zeigt das enorme Potenzial des FSW-Verfahrens für Druckgussbauteile.
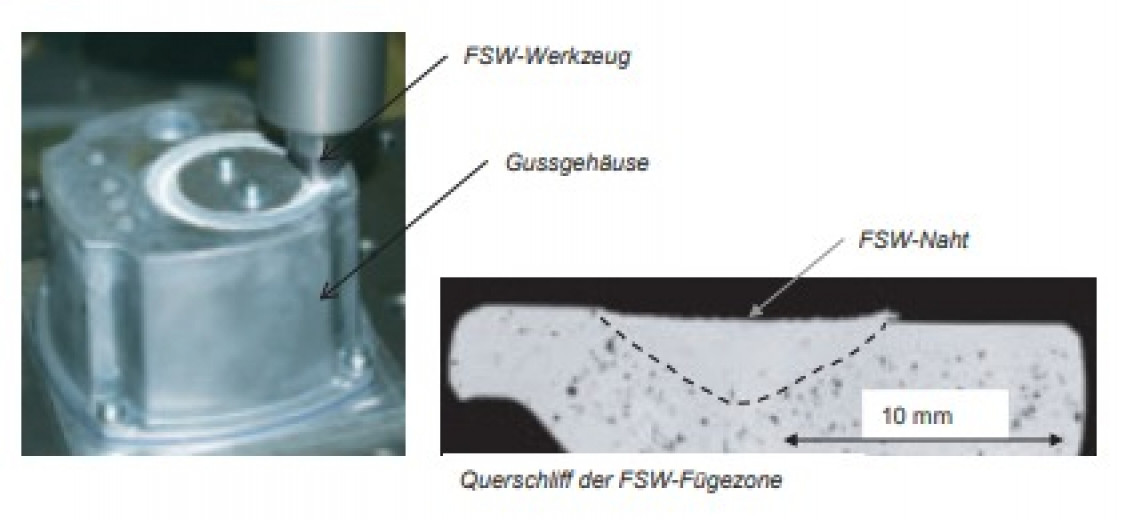
Zusammenfassung
Aluminiumdruckgussgehäuse werden im Apparatebau und in der Automobilindustrie häufig eingesetzt. Anwendungen in der Leistungselektronik, aber auch in der Elektromobilität erfordern immer häufiger eine druck- und mediendichte Fügeverbindung, um beispielsweise Elektronikbauteile von Kühlmedien, die in benachbarten Kühlkreisläufen zirkulieren, sicher zu trennen. In vielen Fällen war die bisher eingesetzte Schraubverbindung nicht mehr einsetzbar, sodass alternative Fügeverfahren gefunden werden mussten. Neuartige Ansätze des Laserstrahlschweißens und des Rührreibschweißens ermöglichen nun das sichere Verbinden derartiger Bauteile.
Mit der präsentierten LBW-Technologie steht ein leistungsfähiges Schweißverfahren für Al-Druckgussbauteile zur Erzeugung druckdichter Schweißverbindungen zur Verfügung. Der erarbeitete Ansatz ermöglicht über eine gezielte Schmelzbadführung die Beeinflussung der Schmelzbadströmung und führt somit zu einer weitgehenden Eliminierung von Poren im Schweißgut. Damit steht erstmals ein industrietaugliches Fügeverfahren zum Laserstrahlschweißen von Leichtmetalldruckgusslegierungen in der Großserie zur Verfügung, wie eine erste Serienapplikation bei einem Automobilzulieferer zeigt. Der Schweißprozess ist sehr effizient und stabil, wodurch kurze Taktzeiten möglich werden. Weiterhin gestatten der lokal begrenzte Energieeintrag und die geringe Laserleistung die Darstellung verzugsarmer 3-D-Bauteile.
Das FSW-Verfahren ermöglicht das gas- und druckdichte Verschweißen von Aluminiumdruckgussbauteilen. Der große Vorteil dieses Verfahrens liegt darin, dass es sich zum Verschweißen jeglicher Aluminiumlegierung eignet und trotz des hohen Porenanteils in Aluminiumdruckgussbauteilen eine porenarme Schweißnaht erzeugt werden kann. Anhand einer Beispielanwendung konnte die Druck- und Mediendichtheit solcher Verbindungen nachgewiesen und so die Leistungsfähigkeit einer FSW-Naht in Aluminiumdruckguss gezeigt werden. Die für das Verfahren eingesetzte Anlagentechnik, der parallelkinematische Pentapod-PG-2000, ist industriell etabliert und sowohl für 2-D als auch 3-D-Anwendungen geeignet.
Literatur
[1] Gref, W.: „Laserstrahlschweißen von Aluminiumwerkstoffen mit der Fokusmatrixtechnik“, Diss. 2005, IFSW Stuffgart, Herbert Utz Verlag, München.
[2] Seefeld, T., Gumenyuk, A.: „Prozessverständnis beim Strahlschweißen von Aluminium“, DVS-Bericht, Band 266, (2010), S. 45–51.
[3] Nörneberg, K., Runge, J.: Wasserstoffporosität beim Schmelzschweißen von Aluminiumwerkstoffen (Teil 2); Aluminium 68, Jahrgang 1992.5.
[4] Jüttner, S.: „Untersuchungen zum Schutzgasschweißen von Magnesiumlegierungen für Konstruktionsbauteile im Automobilbau“, Diss. 1999 Tu-Braunschweig, Shaker Verlag Aachen 2000.
[5] Klassen, M., Skupin, B., Sepold, G.: „Process instabilities by laser beam welding of aluminium alloys generated by laser modulations“, proceedings of the 13th Int. Congress on Laser and Optics in Manufacturing, Laser 97, SPIE Vol. 3097, S. 137-146.
[6] Sheikhi, S., dos Santos, J. F.: “Rührreibschweißen von Aluminium Druckguss, Geesthachter Schweißtage ’06, Festphasenfügeverfahren, pp. 13-22.
[7] Chen, Y., C., Komazaki, T., Kim, Y. G., Tsumura, T., Nakata, K.: Friction Stir Lap Joining of AC4C Cast Alumi-num Alloy and Zinc-coated Steel, Materials Science Forum, Vols. 580-582, pp. 371-374.
Autor
Dr.-Ing. Dirk Dittrich
Gruppenleiter Laserstrahlschweißen / Geschäftsfeld Fügen
Fraunhofer-Institut für Werkstoff- und Strahltechnik IWS
www.iws.fraunhofer.de
Den kompletten Artikel finden Sie in der GIESSEREI-Ausgabe 03/2019.
Schlagworte
AluminiumAutomobilindustrieDruckgussFertigungForschungGussKonstruktionLeichtbauMagnesiumMesseProduktionSpanntechnikSteelStrahlenStrahltechnikVerlagWerkstoffe