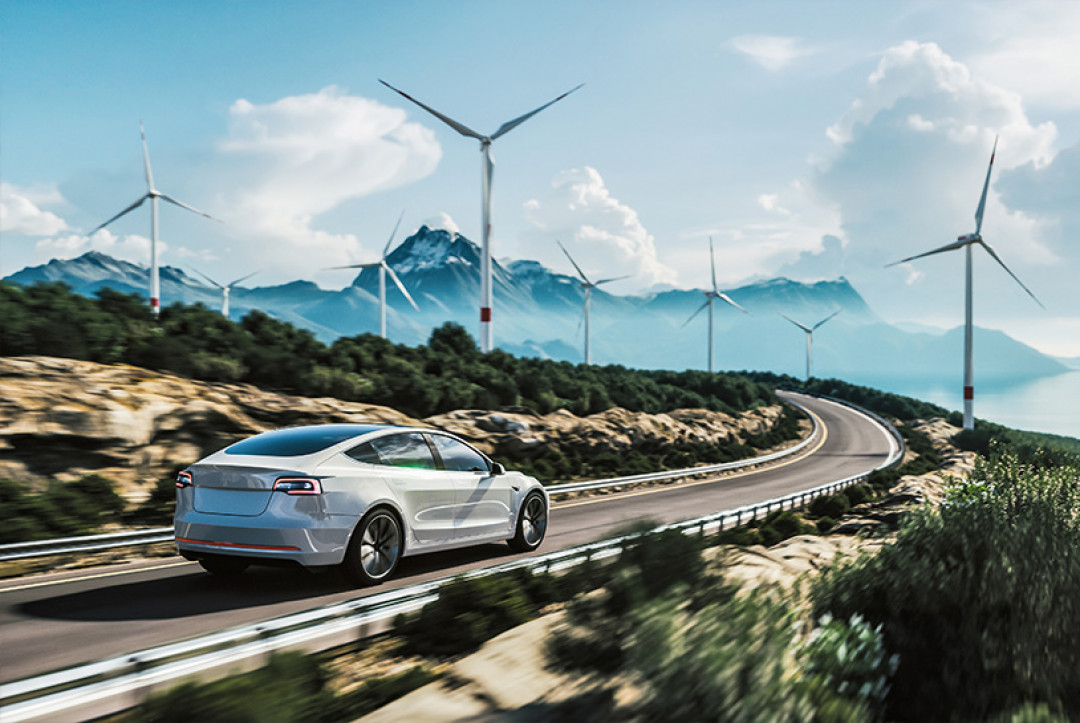
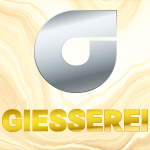
Neue und größere Druckgießmaschinen machen es möglich, die gesamte Rohkarosserie eines Fahrzeugs in einem Stück zu produzieren. Automobilhersteller versprechen sich dadurch eine einfachere Produktion, geringere Kosten und insgesamt mehr Nachhaltigkeit. Ist das sogenannte Megacasting also eine überzeugende Alternative zur Fertigung aus Einzelteilen?
Von Martin Lagler
Für Automobilhersteller ist Nachhaltigkeit von herausragender Bedeutung. Bisher lag der Schwerpunkt auf der Reduzierung der Emissionen während der Nutzungsphase ihrer Fahrzeuge, also auf den Scope-3-Downstream-Emissionen. Zunehmend richtet sich der Fokus jedoch auch auf die Emissionsminderung in der Herstellung der Fahrzeuge einschließlich der Emissionen des dafür benötigten Rohmaterials, den Scope-3-Upstream-Emissionen.
Viele Automobilhersteller verfolgen das Ziel, ihre Emissionen bis 2035 um 30 bis 50 % zu reduzieren, während sie langfristig eine Netto-Null-Emission in der Fahrzeugproduktion anstreben. Volvo beispielsweise will sich nach eigenen Angaben bis 2040 klimaneutral aufstellen.
Dieser Beitrag befasst sich mit dem CO2e-Fußabruck eines mit Megacasting hergestellten hinteren Unterboden (Englisch: Rear underbody) im Vergleich mit einer konventionellen Stahlblech-Bauweise. Zudem werden Möglichkeiten zu weiteren Emissionsreduktionen in der Produktion der Bauteile aufgezeigt.
Vorteile der Megacasting-Technologie
Der Karosserierohbau stellt einen zentralen Aspekt der Fahrzeugproduktion dar und ist somit ein bedeutender Faktor für die Kosten und die Emissionen während der Fahrzeugherstellung. Megacasting bietet vielseitige Vorteile und ermöglicht eine ökonomische und nachhaltige Herstellung der Fahrzeugkarosserien der Zukunft.
Wirtschaftliche Vorteile
- Reduktion der Montagekomplexität: Die Megacasting-Technologie ermöglicht durch Funktionsintegration eine massive Komplexitätsreduktion in der Montage. Bis zu 100 einzelne Blechteile können durch ein einzelnes Gussteil ersetzt werden.
- Vereinfachung der Lagerhaltung: Durch die Konsolidierung vieler kleinerer Teile aus diversen verschiedenen Stahlgüten zu einem Aluminium-Gussteil vereinfacht sich die Beschaffung und die Lagerhaltung im Montagewerk.
- Reduktion der Investitionen in Produktionsanlagen: Die Investitionskosten für eine Rohbaufertigung können gesenkt werden. Es werden bis zu 300 Roboter weniger benötigt und entsprechend wird die Produktionsfläche um ca. 30 % reduziert.
Vorteile in Bezug auf Nachhaltigkeit
- Flexibilität bei der Auswahl der Legierungen: Beim Druckgießen wird das Rohmaterial zuerst in einem eigens dafür konzipierten Schmelzofen geschmolzen. Dies ermöglicht den Einsatz von kundenspezifischen Legierungen und erleichtert das Recycling von Rücklaufmaterial aus dem Prozess. Pre-consumer Abfälle können somit vermieden werden.
- Aluminium mit geringem CO2e-Fußabruck: Der Elektrolyseprozess bei der Herstellung von Primäraluminium wird mit Elektrizität betrieben. Die Nutzung von Strom aus erneuerbaren Energien ist möglich, ohne Investitionen in die Anlagentechnik zu tätigen. Dies ermöglicht die Herstellung von Aluminiumlegierungen mit niedrigem CO2e-Fußsabdruck. Entsprechendes Aluminium ist heute schon in großen Mengen verfügbar.
- Sekundärlegierungen: Mit Megacasting lassen sich auch Sekundärlegierungen problemlos verarbeiten. Der limitierende Faktor ist nicht der Gießprozess, sondern die Anforderungen an Korrosionsschutz und unter Umständen mechanische Eigenschaften wie z.B. Bruchdehnung. Sekundärlegierungen mit möglichst wenig Eisen- und Kupfergehalt sind zu bevorzugen.
Aluminium gegen Stahl
Im Vergleich eines im Druckguss (Megacasting) hergestellten Unterbodens mit einem aus Stahlblech zusammengebauten Unterboden zeigte sich, dass unter den genannten Annahmen die Megacasting-Variante nachhaltiger ist als die Variante mit Stahlblech. Im Direktvergleich in Bild 1 ist zu erkennen, dass die Vorteile des Druckgießverfahrens sowohl in der Effizienz des Prozesses also auch in der Ausbeute des Rohmaterials liegen. So sind die Emissionen für das Rohmaterial vergleichbar, trotz höherem Emissionsfaktor für Aluminium.
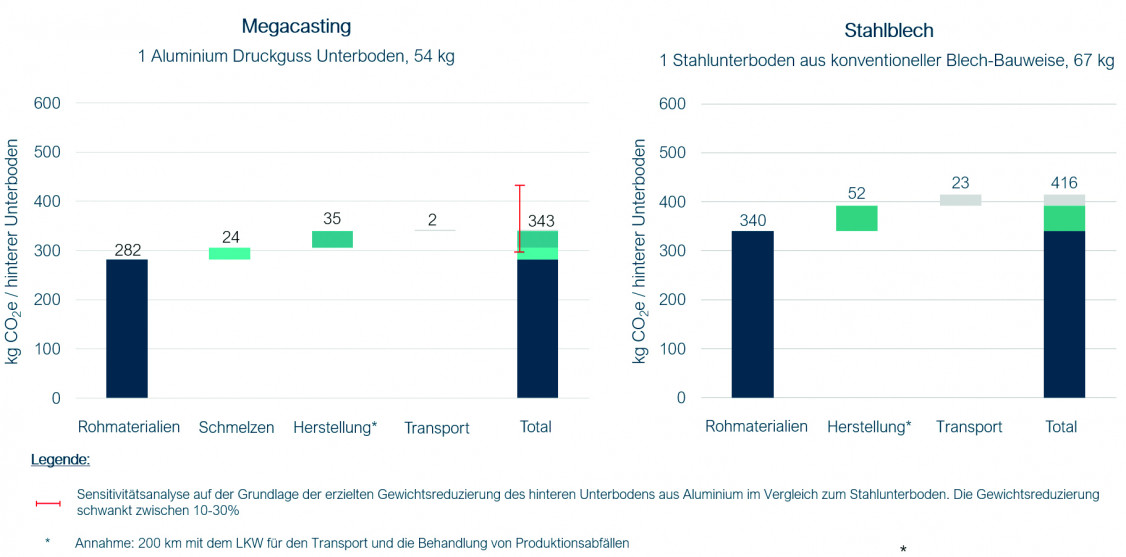
Ein weiterer Vorteil von Aluminium-Druckguss ist das Leichtbaupotential und die damit verbundene Emissionsreduktion auf Rohmaterialseite. Im aktuellen Beispiel wurden 20 % Gewichtseinsparung gegenüber der Stahlblech-Bauweise berücksichtigt. Selbst, wenn keine Gewichtsersparnis erzielt wird, sieht der CO2e-Fussabdruck des Aluminium-Gussbauteils im Vergleich gut aus. In Bild 1 ist der Einfluss der Gewichtsersparnis im Bereich von 0 bis 30 % mit einer roten Linie dargestellt.
Der Vergleich zeigt deutlich, dass auf beiden Seiten das Rohmaterial den überwiegenden Anteil an den Emissionen ausmacht. Beim Aluminium-Gussteil sind dies über 80 %. Daher ist der alles entscheidende Faktor für die Gesamtemissionen der CO2e Fußabdruck des eingesetzten Rohmaterials.
Rohstoffemissionen und Reduktionsstrategien
Durch den dominanten Einfluss des Rohmaterials lohnt es sich, die verschiedenen Emissionsfaktoren von Aluminium genauer zu betrachten. Bild 2 zeigt, wie unterschiedlich die CO2e-Emissionen pro kg Rohmaterial sind. Während der weltweite Mittelwert, getrieben durch den hohen Anteil aus China, bei über 16kg CO2e pro kg Primäraluminium liegt, ist der europäische Mittelwert unter 7 kg CO2e pro kg Aluminium. Heutiger Benchmark ist jedoch Aluminium mit 4 kg CO2e pro kg Rohmaterial oder weniger. Diese Art Primäraluminium ist heute schon in großen Mengen bei verschiedenen Herstellern verfügbar und wird mit Strom aus erneuerbaren Ressourcen hergestellt. Will man die Emissionen noch weiter reduzieren, muss man entweder den Elektrolyseprozess verbessern oder Sekundäraluminium beimischen.
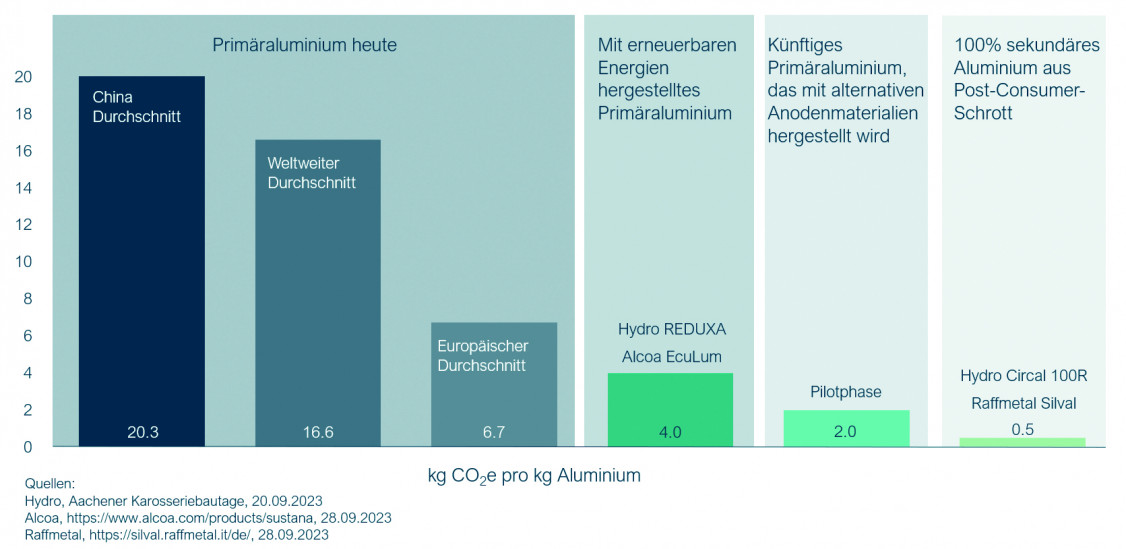
ELYSIS-Elektrolyse-Prozess
Bei der klassischen Aluminium-Primärproduktion werden Anoden aus Graphit eingesetzt. Im Elektrolyseprozess wird Aluminiumoxid zu Aluminium reduziert. Der dabei freiwerdende Sauerstoff verbindet sich mit dem Kohlenstoff der Anode und bildet CO2. Um diese prozessbedingten CO2-Emissionen durch die Graphitanoden zu verhindern, hat ELYSIS ein inertes Anodenmaterial entwickelt. Der ELYSIS-Prozess, entwickelt von einem Joint Venture zwischen Alcoa und Rio Tinto, eliminiert damit direkte Treibhausgasemissionen während der Aluminium-Primärproduktion. Bei gleichzeitiger Verwendung von Strom aus erneuerbaren Energien sind Emissionsfaktoren von weniger als 2kg CO2e pro kg Primäraluminium möglich. Noch befindet sich die Produktion mit dem ELYSIS-Prozess in der Pilotphase. Trotz den noch kleinen verfügbaren Mengen gibt es aber bereits Produkte im Handel, welche mit ELYSIS-Aluminium hergestellt werden.
Sekundäraluminium
Der Druckgießprozess ist sehr tolerant, was verschiedene Legierungszusammensetzungen anbelangt. Klassische Druckgussbauteile im Antriebsstrang sind typischerweise reine Sekundärlegierungen. Die Herausforderungen bei Karosserie-Bauteilen sind grösser, bedingt durch die hohen Anforderungen an Korrosionsschutz und Bruchdehnung. Verunreinigungen durch Kupfer, Eisen und Zink sind nur bis zu einem gewissen Grad toleriert. Firmen wie Raffmetal oder Hydro bieten jedoch heute schon Sekundärlegierungen für Strukturbauteile an. Die Emissionsfaktoren von ca. 0,5 kg CO2e pro kg Aluminium erlauben eine sehr nachhaltige Produktion von Karosseriebauteilen.
Ergänzend ist bei diesem Punkt zu erwähnen, dass große Gussteile für die Kreislaufwirtschaft ideal sind. Am Ende des Lebenszyklus des Fahrzeugs ist eine Sortierung entsprechend einfach, da ein großes Gussteil aus demselben Material hergestellt ist und nicht wie andere Bauweisen aus bis zu 100 Einzelteilen mit diversen unterschiedlichen Materialien und Materialgüten.
Emissionsreduzierung in der Fertigung
Bedingt durch das verwendete Rohmaterial werden auch im Herstellungsprozess gewichtige Mengen CO2e-Emissionen verursacht. Ein großer Teil davon entfällt auf den Schmelzprozess, der typischerweise mit Erdgas betrieben wird. Ein von ABP in Zusammenarbeit mit Bühler konzipierter elektrischer Induktionsschmelzofen bietet eine umweltfreundlichere Alternative zu klassischen, gasbefeuerten Schmelzöfen und reduziert die CO2e-Emissionen in der Gießerei um mehr als 90 %.
Neben dem Schmelzprozess, der ca. 60 % des Energiebedarfs eines Bauteils ausmacht, ist der Druckgießprozess selbst für die restlichen 40 % verantwortlich. In den meisten Fällen handelt es sich dabei um Energie in Form von elektrischem Strom. Das heißt, die Emissionen, die beim Druckgießprozess entstehen, sind eins zu eins abhängig vom Emissionsfaktor des verwendeten Stroms. Im vorliegenden Beispiel sind die Prozessemissionen sogar höher als die des Schmelzprozesses. Dies erklärt sich durch den Europäischen Strommix, der pro kWh deutlich mehr CO2e mit sich bringt als die Wärmeerzeugung durch die Verbrennung von Erdgas.
Um den Energieverbrauch in der Gießzelle zu reduzieren, ist es vor allem sinnvoll auf Servoantriebe bei der Druckgießmaschine zu setzen. Dies spart im Falle von Bühler Carat Maschinen ca. 40 % Energie pro Zyklus. Zudem soll der Temperaturhaushalt der Form optimiert werden, was zwei Effekte haben kann: Erstens wird dadurch der Energieverbrauch der Formtemperiergeräte minimiert und zweites erlaubt eine ausgeglichene Wärmebilanz den Einsatz von Mikrosprühen – die effizienteste und kostengünstigste Variante, den Trennstoff auf die Form aufzutragen.
Schlussfolgerungen
- Die Reduktion der Emissionen sollte sowohl in der Nutzungsphase als auch in der Produktionsphase der Fahrzeuge erfolgen.
- Megacasting ermöglicht nachhaltige Leichtbaulösungen.
- Bei der Kombination sämtlicher Optimierungsschritte (nachhaltiges Rohmaterial, gewichtsoptimiertes Bauteildesign, elektrischer Schmelzprozess und optimierter Giessprozess) können gegenüber dem heutigen Stand weitere 70 % Emissionen auf Bauteilebene reduziert werden.
- Gewichtsersparnisse tragen zu weiteren Emissionsreduzierungen durch sekundäre Effekte bei, z.B. kleinere Motoren und Batterien.
- Der Einsatz von Sekundärlegierungen oder primärem Aluminium mit geringem CO2-Fußabdruck ist unerlässlich.
- Maßnahmen zur Emissionsreduktion senken gleichzeitig die Produktionskosten.
Bühler unterstützt Automobilhersteller durch Beratung bei der Gestaltung von Bauteilen und der Auswahl geeigneter Materialien. Das Portfolio an Druckgießanlagen und Dienstleistungen ermöglicht Lösungen für unterschiedliche Bedürfnisse und Anwendungen – vom Produktionsstart bis über den gesamten Lebenszyklus der Anlagen.
Martin Lagler ist Director Global Application Technology bei der Bühler AG in Uzwil, Schweiz.
Beitragsbild: Bühler
Schlagworte
AluminiumCastingDruckgussFertigungGussGussteileLeichtbauNachhaltigkeitProduktion