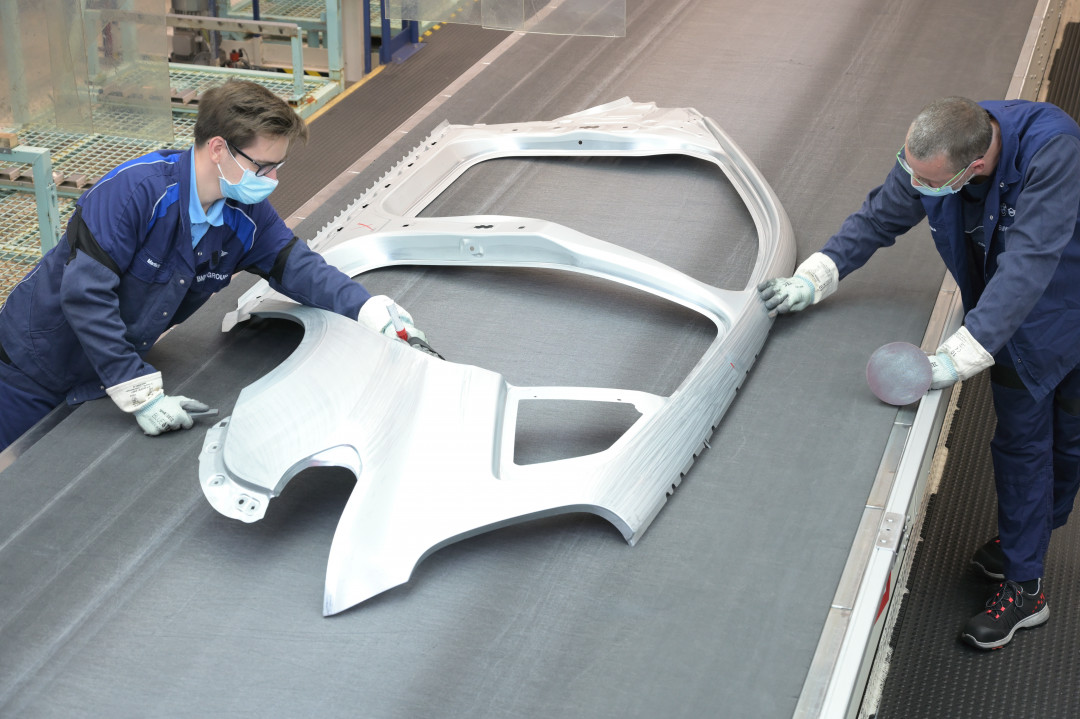
Trends beim Gießen in der Automobilindustrie bilden einen der wesentlichen Schwerpunkte der weltführenden Gießereifachmesse GIFA im Rahmen der Bright World of Metals vom 12. bis 16. Juni 2023 in Düsseldorf.
Dass mit der E-Mobilität die Karten im Automobilmarkt neu gemischt werden, dafür ist Elon Musk mit Tesla ein prominentes Beispiel. Doch dass Newcomer den etablierten Autoherstellern ihr Totenglöckchen läuten, wird von Fachleuten bezweifelt. „Die Chinesen und Tesla haben lange nicht die Steigerung hinlegen können, die sie versprochen haben. Etablierte Produzenten wie VW, BMW, Mercedes und GM konnten sich in den Märkten sehr gut behaupten“, wie Franz-Josef Wöstmann als Leiter der VDI-Konferenz „Gießtechnik und E-Mobilität“ im Oktober in Bremen mit Blick auf die aktuelle Verkaufsstatistik belegen konnte. Wöstmann, Abteilungsleiter Technologiefrüherkennung und Verwertung beim Fraunhofer Institut für Fertigungstechnik und Angewandte Materialforschung – IFAM in Bremen, erinnert daran, dass noch 2019 Tesla scheinbar unangefochten mit 245 000 E-Fahrzeugen auf Platz 1 stand. Seitdem konnte der E-Autopionier seinen Absatz zwar um den Faktor vier auf rund 936 200 Fahrzeuge 2021 steigern, doch in der Zeit hat VW einen Sprung vom Mittelfeld bis fast an die Spitze geschafft und den Verkauf von 41 000 Fahrzeugen 2019 auf 762 000 hochkatapultiert. „VW hat seinen Umsatz mit E-Fahrzeugen weltweit mehr als verzehnfacht, innerhalb von drei Jahren. Diesen Sprung hat auch ein Tesla nicht hinbekommen“, gibt Wöstmann zu bedenken. Auch weitere Etablierte wie BMW und Mercedes konnten die Produktion massiv erhöhen. Dabei müssen die alteingesessenen Unternehmen – anders als die Newcomer der E-Mobility – auch die etablierte Produktion im Auge behalten. Wie die Statistik der letzten Jahre aber zeigt, haben sie sehr gute Karten und holen bei den Absatzzahlen massiv auf oder überholen bereits.
Interessant auch die Entwicklung beim chinesischen Wettbewerb. So konnte BYD den Absatz zwar verdoppeln, fiel aber von Platz 2 auf Platz 3 zurück. BAIC ist gar auf einen der hinteren Plätze gefallen. „Die Chinesen konnten, obwohl sie in dem Hauptmarkt der E-Mobilität sitzen, ihre Poolposition nicht nutzen“, sagt Wöstmann. Der amerikanische Traditionalist GM hingegen, der in der Statistik von 2019 noch gar nicht auftaucht, hat es in der kurzen Zeit ins Mittelfeld geschafft.
Wachstum außerhalb Europas
In den gesättigten Märkten Deutschland, Europa und USA vollzieht sich der Wandel vom Verbrenner zur E-Mobilität ohne nennenswerte Veränderung des Gesamtvolumens zugelassener Fahrzeuge. Wachstum findet überwiegend in Asien und vor allem in China statt. Experten sind sich einig, wie auf der Bremer Gießtechnik-Konferenz deutlich wurde, dass bis 2030 rund die Hälfte aller weltweit verkauften Autos E-Fahrzeuge sein werden. Dennoch werden auch 2050 jede Menge Verbrenner unterwegs sein, aus den unterschiedlichsten Gründen, wie Fraunhofer-Forscher Wöstmann vorhersagt. Denn auch dann werden noch viele Regionen in Asien, Afrika und Lateinamerika nicht über die für flächendeckende E-Mobilität erforderliche Infrastruktur verfügen. Hinzu kommt, dass im Bereich der Nutzfahrzeuge, Schifffahrt und Luftfahrt E-Mobilität nicht die alleinige Lösung sein kann, weshalb auch E-Fuels und Wasserstoff eine wesentliche Rolle im Antriebsmix zukünftiger Mobilität spielen werden.
Ab 2035, so haben die Mitglieder der Europäischen Union beschlossen, soll in der EU kein Verbrenner mehr verkauft werden. Die Entwicklung zur E-Mobilität sehen vor allem die Leichtmetallgießer im Bereich Aluminium und Aluminium-Druckguss für Karosserie und Antriebsstrang durchaus optimistisch, wenngleich der Guss großvolumiger Verbrennungsmotoren auf dem Rückzug ist. „E-Mobilität bedeutet eine Vielzahl neuer Gussteile“, erläutert Wöstmann. Gehäuse für E-Maschinen, Getriebegehäuse, Batteriekästen, Kühlungssysteme, Gehäuse und Kühlung für Leistungselektronik sowie in Zukunft vielleicht gegossene Al-Spulen als Alternative zu gewickelten Cu-Spulen. Wenig Veränderung und garantiert keinen Zuwachs erwartet der Fraunhofer-Forscher im Gusseisenbereich. Was kommen könnte, im Bereich Motorgehäuse, sei dünnwandiger Stahlguss, insbesondere für Hochdrehmomentmotoren mit integrierter Kühlung. Momentan entwickelt allerdings keiner der OEM in diese Richtung. Dann ist da noch das Thema Leichtbau, eine klare Domäne von Aluminium und Aluminiumguss gerade in der E-Mobilität.
Bei den zukünftigen Gussteilen im Druckguss gehen die Philosophien insbesondere zwischen den etablierten Herstellern und den neuen Angreifern auseinander. Während Tesla und verschiedene chinesische Hersteller auf Giga- und Megacasting mit Maschinen über 12 000 Tonnen Schließkraft den Markt erobern wollen, sind die Etablierten eher zurückhaltend. Wöstmann sieht den Ansatz durchaus positiv, insbesondere, weil dadurch gezeigt werde, wozu Guss fähig sei. Allerdings dürfte es nur wenige Zulieferer geben, die in diesen Markt vordringen würden. Vielmehr sei noch eine Menge technologisches Potential in Schließkräften unterhalb von 6 000 Tonnen zu heben, das wirtschaftliche Fertigung bei geringeren Anforderungen an Logistik, Qualitätssicherung und Produktionssicherheit stellt. „Am Ende wird technologisches Verständnis und Know-how vor Gigantomanie für variantenreiche Produkte stehen“, ist sich Wöstmann sicher.
Leichtbau: Intelligenter Materialmix mit Stahl und Aluminium
Doch auch Stahl, für die Karosserie im Volumenmarkt ohnehin der Werkstoff Nr. 1, kann seine Stellung behaupten. Und das nicht nur beim Elektroband, dem ohnehin unverzichtbaren Kernwerkstoff für E-Maschinen. Auch Premiumhersteller wissen um die Stärken neuer höchstfester Stähle, wie Porsche mit der Mischbauweise seines batterieelektrischen Sportwagens Taycan zeigt.
Warmumgeformte Stähle schützen die Fahrgastzelle mit A-Säule, B-Säule, Dachrahmen und Sitzquerträger. Als besonderes Highlight gilt der Stirnwandquerträger aus Mangan-Bohr-Stahl. Durch spezielle Fertigungsverfahren sind innerhalb des rohrförmigen Bauteils verschiedene Querschnitte realisiert. So wird höchste Festigkeit bei optimiertem Gewicht erreicht. Aus Aluminium-Druckguss gefertigt sind Federbeinaufnahme, Achsaufnahme und der hintere Längsträger. Das alles sind komplexe Bauteile mit Funktionsintegration, die also mehrere Bauteile bzw. Bauteilfunktionen zu einem einzigen zusammenfassen. Die besonders hoch belasteten Aufnahmen der Pralldämpfer sind aus Aluminium geschmiedet. Der vordere Längsträger kombiniert eine Aluminiumblech-Schalenbauweise mit Strangpressprofilen. Die knapp 2 m langen Schweller sind als Siebenkammer-Strangpressprofil ausgeführt. Mit der Siebenkammer-Geometrie erfüllt das Aluminiumbauteil alle Anforderungen an die Steifigkeit beim Seitencrash oder gegen ein Verdrehen der Karosserie. Gegenüber einem Stahlschweller reduziert die Konstruktion die Zahl der Bauteile pro Seite von fünfzehn auf drei und das Gewicht um rund 3,4 kg, wie der Hersteller mitteilt. Die komplette Außenhaut ist bis auf die Front- und Heck-Endteile aus Aluminium gefertigt. Insgesamt beträgt der Aluminium-Anteil beim Taycan rund 37 %. Gefertigt wird die Karosserie von Thyssenkrupp Automotive Body Solutions, der Karosseriebautochter des Essener Industriekonzerns.
Die Wirtschaftlichkeit von Leichtbau wird wesentlich vom Fahrzeugtyp definiert. Hinsichtlich gegenüber Stahl teurerer Leichtbaumaterialen wie Aluminium und CFK ist der Spielraum bei Premiumfahrzeugen wie von Audi, BMW oder Mercedes ungleich größer als im Volumenmarkt der Volkswagen und Co.. Die selbsttragende Schalenbauweise aus Stahl ist daher die weltweit am häufigsten vertretene Karosseriebauweise, sie gerät jedoch seit einigen Jahren durch Aluminium unter Druck. Aus mehreren Stahlblechteilen zusammengeschweißte Blechkonstruktionen weichen zunehmend Aluminium-Druckgussteilen aus einem Guss. Die Vorteile liegen klar im Verfahren. Im Druckguss lassen sich auch große Gussteile mit komplexer Geometrie wie Federbeindome wirtschaftlich in hoher Stückzahl fertigen.
Trend zu größeren Druckgießmaschinen
Wirtschaftlich und technologisch geht der Trend bei Fahrwerk- und Strukturteilen sowie E-Mobilität im Druckguss grundsätzlich zu größeren Schließkräften, also größeren Druckgießmaschinen, wie Johannes Messer von der gleichnamigen Consulting GmbH mitteilt. Leistungsfähigere Druckgießmaschinen erlauben eine wirtschaftlichere Fertigung größerer und komplexerer Autoteile.
Den neuesten Trend bei großformatigen Druckgussbauteilen will Tesla-Chef Elon Musk mit dem Mega- oder Giga-Casting eingeläutet haben. Die von Tesla erstmals eingesetzten Druckgießmaschinen vom Typ Giga-Press des italienischen Herstellers Idra bringen mit einer Presskraft von 6 000 bis 9 000 Tonnen das geschmolzene Aluminium in die Form kompletter Hinter- und Vorderwagenteile. Musk will sogar über ein Patent für die gesamte Karosserie aus einem Stück Druckguss ohne Wärmebehandlung verfügen. Sein Mega-Casting erspart laut Musk heute bereits 300 Roboter am Fließband und reduziert drastisch die Montagezeit. In der Teslafabrik Grünheide rollt alle 45 Minuten eine Rohkarosse vom Band. Mit der Herstellung eines kompletten Fahrzeugs in nur zehn Stunden liegt Tesla klar vor der Konkurrenz wie VW, wo ein Fahrzeug rund 30 Stunden bis zur Fertigstellung benötigt. Idra war das erste Unternehmen mit Produktionsaufträgen für 9 000-Tonnen-Maschinen, die für SUV- und Kleinlastwagenmärkte eingesetzt werden können. Weltweit will das Unternehmen bereits 24 seiner Giga-Press Druckgussmaschinen verkauft haben, überwiegend nach China und nicht nur in die Automobilbranche.
Nio und Xpeng, zwei chinesische Elektroauto-Start-ups, sind dem Beispiel von Tesla bereits gefolgt und haben bei der Idra-Muttergesellschaft, der chinesischen LK Group, Druckgießmaschinen mit einer Kraft von 12 000 Tonnen bestellt, wie die US-Marktforschungsgesellschaft Ducker berichtet. Die „12000 T Super Large Intelligent Die Casting Unit“ von LK Technology wurde erstmals Ende September in Shanghai der Öffentlichkeit vorgestellt, gemeinsam mit der chinesischen Gießerei Guangdong Hongtu.
Ducker sieht im Großguss einen ernstzunehmenden Trend zur Verbesserung der Rentabilität von E-Fahrzeugen. Volvo hat bereits bekanntgegeben, im Werk Torslanda in Schweden in Mega-Casting für Aluminium-Karosserieteile für die nächste Generation reiner Elektrofahrzeuge zu investieren. „Mega-Casting bietet eine Reihe von Vorteilen in Bezug auf Nachhaltigkeit, Kosten und Leistung während der Lebensdauer des Fahrzeugs“, heißt es bei Volvo. Das Gießen großer Teile der Bodenstruktur des Fahrzeugs als ein einziges Aluminiumteil reduziere das Gewicht, was wiederum die Energieeffizienz und damit die elektrische Reichweite des Fahrzeugs verbessere. Zudem könnten die Volvo-Designer so den verfügbaren Platz in der Kabine und im Gepäckraum optimal nutzen, was die Vielseitigkeit des Fahrzeugs insgesamt erhöhe, begründet Volvo die Investition. Zu den weiteren Vorteilen des Mega-Casting gehöre die geringere Komplexität des Fertigungsprozesses. Dies wiederum führe zu Kosteneinsparungen beim Materialeinsatz und in der Logistik, wodurch der gesamte ökologische Fußabdruck in den Produktions- und Lieferkettennetzwerken verringert werde.
Auch Volkswagen hat im Hinblick auf sein neu zu bauendes Werk für das E-Modell Trinity Interesse an den Produktionsmethoden von Tesla bekundet, eine Investitionsentscheidung zugunsten von Mega-Casting bislang aber nicht bekannt gegeben.
Mega-Casting: Entwicklung mit Fragezeichen
Ducker räumt bei allem Optimismus ein, dass Mega-Casting noch einige Fragen aufwerfe. Was beispielsweise die Reparaturfähigkeit angeht, so ist ein Tesla nicht so beschaffen, dass das Großgussteil gerichtet oder einfach ersetzt werden kann. Ist nach einem Crash die Struktur verzogen oder gebrochen, ist das Fahrzeug mit hoher Wahrscheinlichkeit ein Totalschaden. Dass Mega-Casting a la Tesla der große Gamechanger im Automobilbau wird, darf zumindest bezweifelt werden. Gießerei-Experte Wöstmann kann von der Bremer Gießereikonferenz jedenfalls berichten: „Klare Aussage etwa von BMW: Unsere Maschinen sind ausreichend, wir gehen nicht in den 6 000 oder 8 000-Tonnen-Bereich“.
Prof. Dr.-Ing. Martin Fehlbier, Leiter Gießereitechnik am Institut für Produktionstechnik und Logistik an der Universität Kassel kann einen internationalen Trend zur Fertigung von Großgussteilen auf großen Gießzellen erkennen, nicht nur in Asien. „Die Substitution von bis zu 100 einzelnen Stahlblechteilen zu einem einzigen Gussteil und der Entfall von vielen Fügeprozessen bietet einen großen Anreiz sich intensiv mit dieser neuen Fertigungstechnologie zu befassen“, sagt Fehlbier. Hinzu komme ein Gewinn von Produktionsfläche bis 30 Prozent, zudem spare der Einkauf die Beschaffung von bis zu 100 Einzelformen (Gesenke) und anderes mehr.
Dagegen zu halten sei grundsätzlich die ungelöste Frage der Reparierbarkeit eines Großgussteils im Crashfall. In den Griff zu kriegen seien zudem logistische Themen wie Transport und Wechsel der großen Gießformen, zudem wichtige Fragen, wie die korrekte Auslegung und Gewährleistung der optimalen Formtemperierung und damit der Formstandzeiten der bis zu 2 Millionen € teuren Werkzeuge mit teilweise deutlich mehr als 40 Temperiergeräten. Zu klären seien auch das optimale Formsprühen von großen Flächen, das ideale Anschnittsystem bei langen Fließwegen, benötigte Mindestwandstärken, ideale Gusslegierungen und vieles andere mehr. „Grundsätzlich aber alles machbar“, wie Fehlbier sagt.
Grünstahl für nachhaltige E-Mobilität
Mit dem Weg der Stahlerzeuger in die Klimaneutralität erwirbt sich Stahl ein zunehmend grünes Image. Unterstützt wird der Trend von Autoherstellern wie BMW und Mercedes, die verstärkt nach einem klimaneutralen Stahl verlangen. So haben denn auch alle führenden Stahlhersteller von ArcelorMittal über Salzgitter, Tata Steel und Thyssenkrupp bis Voestalpine nicht nur erste CO2-reduzierte bis hin zu ersten CO2-neutralen Produkte im Portfolio. Für elektromobilen Leichtbau mit Stahl bieten die Schwergewichte komplette Werkstoffsortimente mit den dafür passenden Materialkonzepten, sowohl für die Warm- als auch für die Kaltumformung. Beispiel Batteriekasten: Als Bestandteil der Bodenstruktur ist der Batteriekasten eine der wichtigsten Komponenten eines E-Fahrzeugs überhaupt und bislang eine Domäne von Aluminium, in Druckguss, Blech und Profil.
Mit dem Hochlauf im Volumenmarkt der E-Mobilität sind aber zunehmend wirtschaftliche Lösungen für das Batteriegehäuse gefragt. So hat beispielsweise Thyssenkrupp Steel eine crash- und brandsichere Leichtbaulösung für Batteriegehäuse aus hoch- und höchstfestem Stahl im Angebot. Gegenüber einer Aluminiumreferenz verursache das Stahl-Batteriegehäuse 50 Prozent geringere Produktionskosten und über den gesamten Lebenszyklus um 50 Prozent geringere CO2-Emissionen, wie der Stahlhersteller versichert. Das Batteriegehäuse mit Unterfahrschutz und Deckel hat dank Stahl höchstmöglichen Brandschutz und kann laut Thyssenkrupp alle Anforderungen annähernd gewichtsneutral gegenüber Aluminium erfüllen. Der sicherheitsrelevante Rahmen des Batteriekastens ist aus kostengünstig hergestellten Rollprofilen beliebiger Länge zusammengesetzt, wodurch kein aufwendiges Tiefziehwerkzeug für die Fertigung des skalierbaren Batteriegehäuses erforderlich ist.
Autorenhinweis: Gerd Krause, Mediakonzept Düsseldorf
Schlagworte
AluminiumAutomobilindustrieCastingDesignDruckgussDruckgussmaschinenEisenEnergieeffizienzFertigungFertigungsverfahrenForschungGIFAGussGusseisenGussteileIndustrie 4.0KonstruktionLeichtbauLieferketteLogistikMesseNachhaltigkeitProduktionSicherheitStahlStahlgussSteel