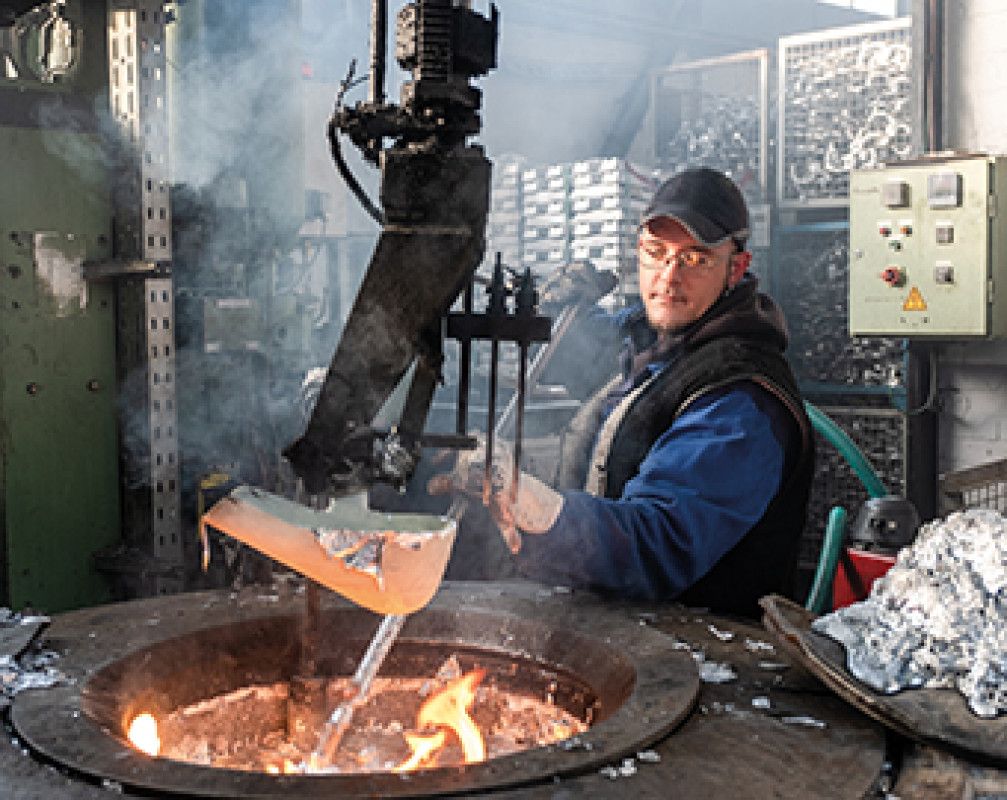
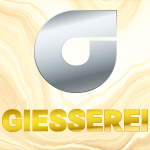
Vom Tüftler im eigenen Fahrradkeller bis zum erfolgreichen Unternehmer – so liest sich der Schöpfungsmythos von Matthies Druckguss und seinem schillernden Gründer Willy Matthies im Rückblick. Doch tatsächlich gründet sich der Erfolg der Druckgießerei auch auf den klassischen Tugenden des vielgepriesenen deutschen Mittelstands – zu denen sich auch Marco Matthies, Enkel des Gründers und neuer Geschäftsführer des Rendsburger Unternehmens bekennt.
Nach den Fabrikanten der Wirtschaftswunderjahre und ihren Nachfolgern tritt in den inhabergeführten deutschen Gießereien nun zunehmend eine neue Generation von Unternehmern in die Startlöcher. So auch bei Matthies Druckguss im schleswig-holsteinischen Rendsburg. Hier hat Marco Matthies Anfang des Jahres die Geschicke der familieneigenen Druckgießerei für Aluminium-, Zink- und Messinglegierungen von Vater Jörn übernommen. „Anders als in den großen Konzernen, in denen auch einmal rote Zahlen geschrieben werden können, gibt es für Familienunternehmer meist nur das Werk – und das muss überleben“, formuliert Marco Matthies die existenzielle Fallhöhe zwischen großen und mittelständischen Unternehmen.
Die Geschichte seines Werks prägt das Rendsburger Wirtschaftsleben nun schon seit über 60 Jahren. Und es waren seit jeher Eigenverantwortung und Weitsicht, aber auch die kurzen Entscheidungswege, die den Erfolg des Unternehmens sicherstellten – ob bei Großvater Willy Matthies oder Vater Jörn. Für dieses Modell erfolgreichen Unternehmertums – eigentlich exemplarisch für die ganze mittelständische deutsche Unternehmenslandschaft – steht nun auch der 38-jährige Wirtschaftsingenieur Marco Matthies, der bereits seit 2008 Betriebsleiter im Unternehmen ist.
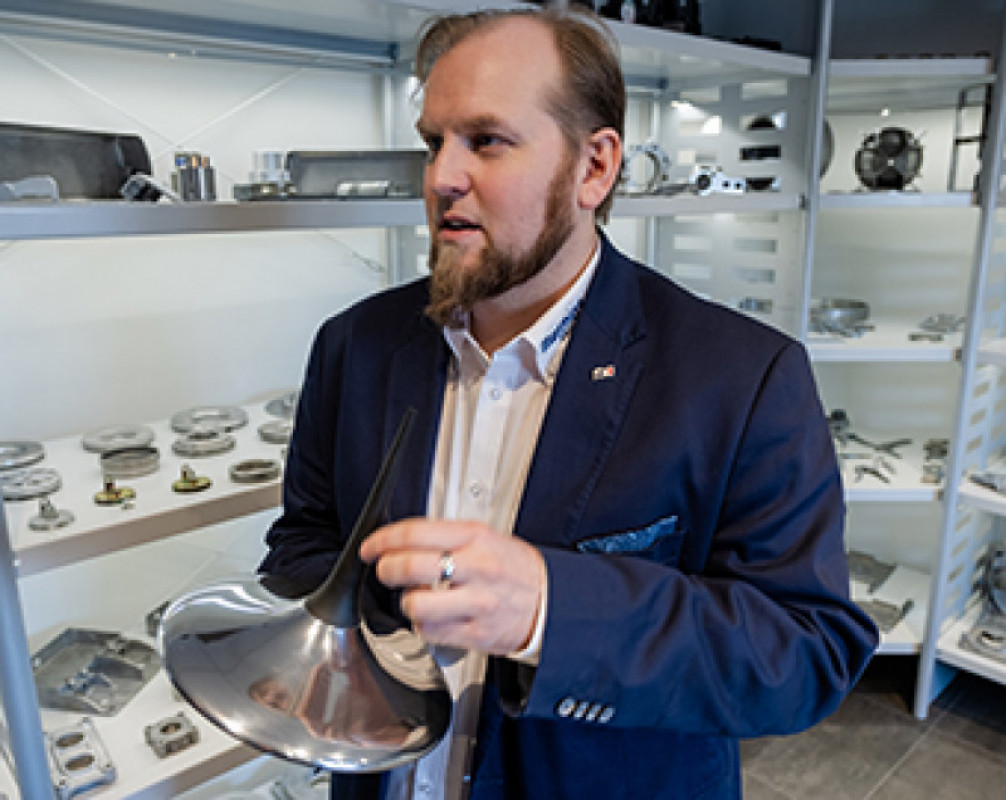
Druckguss aus dem Fahrradkeller
Was Marco Matthies für die Zukunft will und warum ist auch das Ergebnis einer bewegten Unternehmenshistorie: Und die hat, wie auch bei Apple-Gründer Steve Jobs, in der Garage begonnen, genauer im Fahrradkeller der Familie Matthies, wo Unternehmensgründer Willy bereits in den 1950er-Jahren gemeinsam mit Söhnen und Töchtern mit einer frühen Druckgießmaschine Gussteile fertigte und entgratete. Willy Matthies war ein Macher-Typ erster Güte, der sich zahlreiche Male neu erfand. Zu seinen Firmengründungen gehörten u. a. eine Marmeladenfabrik und die Weiterführung einer Firma für das Trockenhaarwaschmittel Curelljo.
Als in der aufstrebenden Industrie der 1950er-Jahre klar wurde, dass sich mit Druckguss Geld verdienen ließ, stieg Willy Matthies um und erwarb 1961 das heutige Firmenareal, wo er in einer Fertigungshalle mit rund zehn bis zwölf Maschinen den Betrieb aufnahm. Nach Willy Matthies‘ frühem Tod folgte ihm Sohn Jörn 1974 direkt nach dem Studium auf den Chefsessel. Bald ging es stetig bergauf: geschultes Personal wurde eingestellt, bessere Maschinen sowie die CNC-Bearbeitung ersetzten den alten Maschinenpark. So entstand in dem Unternehmen an der Bredstedter Straße eine moderne Fertigung, die heute an den benachbarten Netto-Markt und eine Autowerkstatt grenzt. Aktuell erwirtschaften hier 23 Mitarbeiter einen Umsatz von 2,5 Millionen Euro im Jahr.
Erfolgsgarant Kundenservice
Im Fokus aller Unternehmer vom Schlage Matthies standen immer der Kunde mit seinen Bedürfnissen und die Überlegung, wie ihm zum beiderseitigen Vorteil weitere Aufgaben abgenommen werden können. Den Kundenwunsch in den Vordergrund zu stellen, ist auch für Marco Matthies daher ein Erfolgsgarant, den er weiterhin fest im Blick hat. Schließlich sind die Stückkosten bei kleineren Losgrößen naturgemäß teurer – da können Zusatzleistungen für den Kunden, etwa das Vorhalten von Lagerbeständen für kurzfristige Bestellungen, die Kundenbindung entscheidend beeinflussen.
Und um die noch weiter zu intensivieren und zugleich das eigene Geschäft auszubauen, denkt der Enddreißiger, der in seiner Freizeit gerne reist und Gitarre in einer Rockband spielt, unter anderem an die additive Entwicklung und Fertigung von Dauerformen. Ihn faszinieren dabei besonders die Möglichkeiten des neuen Verfahrens, mit dem es über kurz oder lang grundsätzlich möglich sein dürfte bessere Formen mit längerer Standzeit, raffinierten Kühlkanälen und größerer Gestaltungsfreiheit zu drucken.
Denkbar sei auch, künftig mit Kunden zusammenzuarbeiten, die ein Gussteil übernommen haben, für das es keine Konstruktionszeichnungen gibt. „Von dem Teil können wir dann einen 3-D-Scan machen, es vermessen und mit Hilfe dieser Daten fertigen“, zählt er auf. Wenn sich die Technologie weiter erfolgversprechend entwickelt und z. B. das Lunkerverhalten vorhergesehen werden kann, will Marco Matthies in die Fertigung per Metall-3-D-Druck einsteigen.
Gussteile mit Manufaktur-Charakter
An erster Stelle wird aber auch zukünftig die Produktion für die 150 aktiven Kunden stehen. Das Produktportfolio des Rendsburger Unternehmens umfasst sage und schreibe 1050 verschiedene Gussteile. Um einen Eindruck von der Produktionsvielfalt zu bekommen, führt Matthies in einen Ausstellungsraum im Verwaltungstrakt der Gießerei. Sphärische Musik empfängt den Besucher, die Wände sind von robusten Aluminiumregalen verdeckt. Die Auswahl der hier präsentierten Gussteile reicht von einer zwei Gramm leichten Aluminiumhalterung bis zum acht Kilogramm schweren Kabeldeckel aus Messing. Mal sind die Teile rund, mal rechteckig, mal einfach, mal komplex und mal strahlen sie im Schein der Lampen silbern oder golden – je nach Legierung.
Besonders stolz ist Marco Matthies auf eine LED-Lampe, die aussieht wie ein plattgedrückter Tropfen. Erdacht hat sie ein renommierter Industriedesigner. Warum die Gießer aus Rendsburg hier zum Zug kamen, hat zwei Gründe: Zum einen führen Gussteile die abgestrahlte Wärmeenergie der Lampe effizient ab und zum anderen sorgt das sogenannte Matthies Cast Design für ein formschönes Aussehen des Teils. „Gussteile können auch einen edlen Manufaktur-Charakter haben. Sie haben eine gewisse Schönheit – Schade eigentlich, dass sie oft nur eingebaut werden“, erklärt Marco Matthies, den Blick versonnen auf die spiegelglatte Oberfläche des Lampenschirms gerichtet.
Doch wie kann das sein? Im Designbereich brillieren überwiegend Teile aus Zinkdruckguss, Aluminium gilt als eigenwilliges, nicht dekoratives Material. „Zusammen mit einem Lieferanten haben wir das Matthies Cast Design entwickelt, bei dem das Material auf eine bestimmte Weise mit einer speziellen Polierpaste bearbeitet wird. Das Verfahren ist viel nachhaltiger als ein galvanisches Verfahren“, klärt Matthies auf und ergänzt: „Dafür muss die Oberfläche aber absolut glatt sein – das stellt einen hohen Anspruch an den Druckgießprozess.“
Vom Wassersprinkler über Markisengelenke bis zu Lampengehäusen
Matthies Druckguss gießt derzeit auch zentrale Teile der Midgard-Maschinenleuchte, deren Design auf den Ingenieur Curt Fischer zurückgeht, der vor genau 100 Jahren das lenkbare Licht erfand. Seine Bürotischlampen mit den langen, schwenkbaren Gelenkarmen sind seither weitverbreitet. Matthies Druckguss stellt die Lampe nun wieder exakt so her wie früher – mit Erfolg, wie die Verkaufszahlen zeigen. Der Anbieter der Lampen, die Hamburger Midgard Licht GmbH, drehte bei Matthies Druckguss kürzlich einen Image-Film über die Lampenfertigung, der mittlerweile auch auf YouTube abgerufen werden kann.
Die größten Umsatzbringer für die Druckgießerei sind aber Wassersprinkler-Elemente aus Messing für die Firma Minimax, einen Stammkunden, der bereits seit 35 Jahren beliefert wird. Gut laufen auch Verbindungsteile für den Kabelfernsehempfang oder selbstschlagende Handschellen, die dem Delinquenten von einem einzelnen Beamten angelegt werden können. Matthies: „Was Automobilzulieferer nicht abdecken möchten, nehme ich.“ So war es auch bei den Handschellen, die seit nunmehr drei Jahren in Rendsburg gefertigt werden. Besonders gefragt sind aktuell auch Gelenke für Markisen aus Aluminium, die Matthies Druckguss für die Firma Lewens Sonnenschutzsysteme gießt.
Geschäftsbeziehungen existieren aber auch über die deutschen Grenzen hinaus. Etwa nach Indien, wo die Firma Honeywell Landeleuchten und Beschilderungen für die Anflugbahnen von Flughäfen benötigt. „Bei der Landung eines A380 auf einem indischen Airport brachen alle dort angebrachten Beschilderungen“, verrät Matthies. Damit die starren Elemente nicht zu Flugunfällen beitragen, wurden die Beschilderungen anschließend neu entwickelt. Die optimierten Schilder enthalten nun eine Sollbruchstelle, die bei einer bestimmten Kraft bricht.
Messingdruckguss für den Schiffbau
Das Know-how beim Messingdruckgießen kommt den Rendsburgern besonders bei der Fertigung von Schiffsbauteilen zugute. Nach Norwegen gehen beispielsweise Messingteile für die Backbord- und Steuerbordbeleuchtung von Schiffen. Der Grund für die Werkstoffwahl ist simpel: Messing ist seewasserbeständig. Daher verwundert es auch nicht, dass der norddeutsche Druckgießer Matthies mit seinem Standort zwischen Nord- und Ostsee eine Lanze für das goldglänzende Metall bricht. „Messing ist beliebt, wird im Druckguss aber oft unterschätzt, obwohl es zu den ersten Metallen gehörte, die im Druckgießverfahren eingesetzt wurden. Leider wird häufig übersehen, dass auch einbaufertige Teile aus Messing möglich sind“, gibt er zu bedenken. Apropos einbaufertige Teile. Matthies Druckguss liefert Bauteile in jeder Fertigungsstufe – bis zur einbaufertigen Komponente. „Bei manchen Teilen möchte ich auf eine Wertschöpfung von fast 100 Prozent kommen“, kündigt Matthies an. Hierfür müssen aber noch weitere CNC-Fräsen angeschafft werden – eine Investition, die zurzeit noch geprüft wird.
Flexibilität sichert Produktvielfalt
Nur ein Treppenhaus, ein Gang und einige Türen trennen den Ausstellungsraum von der Fertigungshalle. Hier zischen und surren die Druckgießmaschinen, dazwischen manövrieren Gabelstapler und aus den benachbarten Hallen dringen Stanz- und Bohrgeräusche ans Ohr. Der Maschinenpark besteht ausschließlich aus italienischen Colosio-Druckgießmaschinen mit Schließkräften zwischen 140 und 500 Tonnen.
Wie gelingt es einer Druckgießerei mit überschaubarer Größe wie Matthies Druckguss über Tausend verschiedene Gussteile aus zahlreichen Legierungen dreier völlig unterschiedlicher Werkstoffgruppen zu fertigen? „Wir haben keinen großen zentralisierten Schmelzbetrieb, das macht uns flexibler“, klärt Marco Matthies auf und weist zu einem ölbefeuerten Öfen, an dem ein Mitarbeiter gerade Schlacke abschöpft. „An jeder Gießzelle betreiben wir dezentral einen Schmelz- und Warmhalteofen. Per automatisiertem Dosierlöffel wird die Schmelze dann für jeden Schuss in die Zelle transportiert.“ Und tatsächlich: Gerade schwebt ein mit Schmelze gefüllter Dosierlöffel entlang einer langen Schiene zur Gießzelle, wo er in die Gießkammer entleert wird. Es folgt ein dumpfer Schlag – der Schuss der Anlage. Dann folgt die Entnahme der Druckgussteile aus der Form. 100 bis 180 Stück kann die Maschine so pro Stunde produzieren. In diesem Fall sind es Verschraubungen für Solarpaneele.
Die vergleichsweise geringe Stückzahl der einzelnen Anlagen täuscht aber über die doch recht beachtliche Gesamtmenge hinweg, die das Werk Tag für Tag verlässt: Es sind 50 Gitterboxen oder ein vollbepackter Lkw. Im Jahr kommen so fünf Millionen Gussteile aus Rendsburger Produktion zusammen. Wie das Beispiel Matthies Druckguss zeigt, sind Pragmatismus, Flexibilität, Kundennähe und Innovationskraft die Zutaten für ein erfolgreiches mittelständisches Unternehmen. Die norddeutschen Druckgießer scheuen sich auch nicht davor, ihre Qualitäten unter Beweis zu stellen. Allerdings nicht auf der bevorstehenden NEWCAST im Rahmen der „Bright World of Metals“ in Düsseldorf, sondern auf der EUROGUSS in Nürnberg im kommenden Jahr. Auf der Hausmesse der Rendsburger wird Marco Matthies sein Unternehmen dann auch erstmals als neuer Geschäftsführer vertreten.
VON ROBERT PITEREK, DÜSSELDORF
Schlagworte
3-D-DruckAluminiumDruckgussFertigungGestaltungGießereiGussteileKonstruktionMesseProduktion