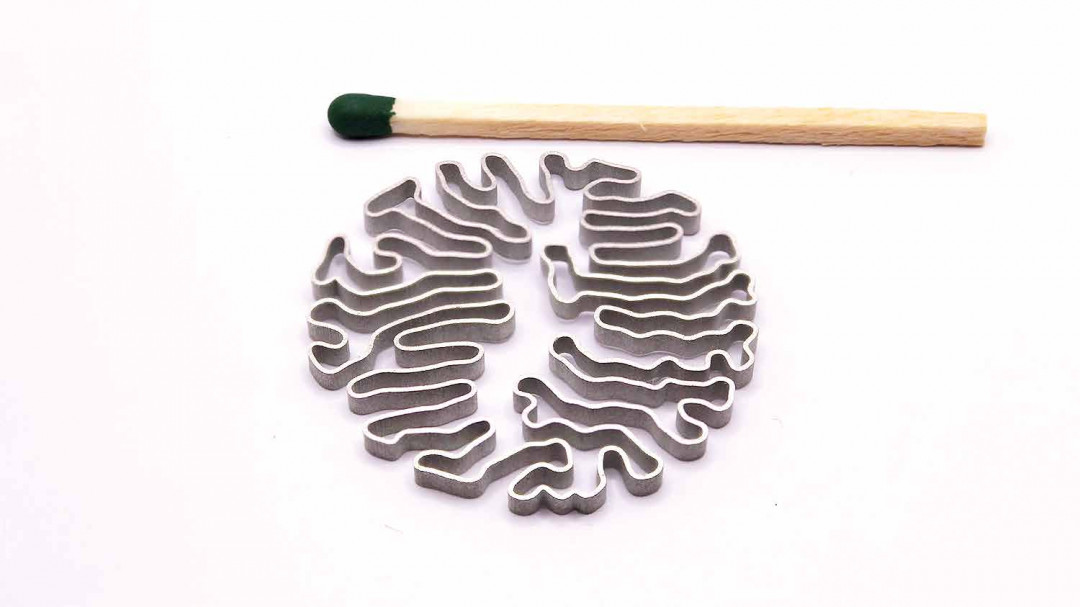
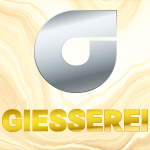
Die Additive Fertigung (AM) wird von den Anwendern klassischer Fertigungsverfahren, zu denen auch der Mikroguss (eine Form des Feingusses) zählt, häufig als Konkurrenz wahrgenommen. Während der Feinguss bereits seit vielen Jahren für komplexe metallische Bauteile etabliert ist, hat die AM-Technologie in den letzten Jahren einen beeindruckenden Aufschwung erlebt. Doch stehen diese Fertigungswege tatsächlich in Konkurrenz zueinander oder sind sie eher als komplementäre Technologien zu betrachten?
VON SONJA KAPPLER, CHIARA ARMBRUSTER, ANDREAS BAUM, KNUT HEITZMANN, CARLO BURKHARDT
Fertigungsverfahren für metallische Klein- und Mikrobauteile
Im Bereich der Additiven Fertigung existieren nur eine Handvoll Verfahren, die sich für die Fertigung von kleinen hochpräzisen Metallkomponenten eignen. Das direkte 3-D-Druckverfahren Mikro-Laserschmelzen (M-LPBF), bei dem Metallpulver schichtweise mit einem Laser aufgeschmolzen und verschweißt wird, hat die Einschränkung, dass bei Überhängen Stützstrukturen erforderlich sind, die aufwendig zu entfernen sind und der Prozess auch bei höheren Stückzahlen aufgrund des Energieverbrauchs und der punktuellen Bearbeitung weniger effizient und wirtschaftlich ist als die sinterbasierten, sogenannten indirekten Verfahren.
Zu den sinterbasierten AM-Technologien, die auch für kleine Bauteile im Größenspektrum des Feingusses relevant sind, zählen unter anderem das Metal Binder Jetting (MBJ) und das Lithographybased Metal Manufacturing (LMM), die einen zweistufigen Prozess nutzen. In der ersten Phase wird ein Grünteil mit einem hohen Anteil an Metallpulvermaterial gedruckt. Anschließend durchläuft das Grünteil einen Entbinderungs- und Sinterprozess, bei dem die im Druckprozess verwendeten Bindemittel durch thermische Behandlung entfernt werden.
Die sinterbasierten Verfahren bieten neue Möglichkeiten bei der Überwindung von geometrischen und qualitativen Einschränkungen, insbesondere im Bereich der Fertigung von kleinen Bauteilen mit herausragender Detailgenauigkeit und Oberflächengüte und können durch Skaleneffekte auch für Kleinserien und mittlere Stückzahlen eine interessante Alternative zur konventionellen werkzeuggebundenen Fertigung darstellen. Darüber hinaus erfordert das LMM-Verfahren beispielsweise keine Stützstrukturen und damit weniger manuelle Nacharbeit am Bauteil. Im Vergleich zum MBJ-Verfahren zeichnet sich das LMM-Verfahren durch eine höhere Auflösung und damit bessere Präzision und Oberflächengüte aus. Daher ist das LMM-Verfahren für Bauteile kleiner als ca. 40 mm Kantenlänge das bevorzugte Verfahren, während das MBJ für größere Bauteile wirtschaftlicher ist (Bild 1).
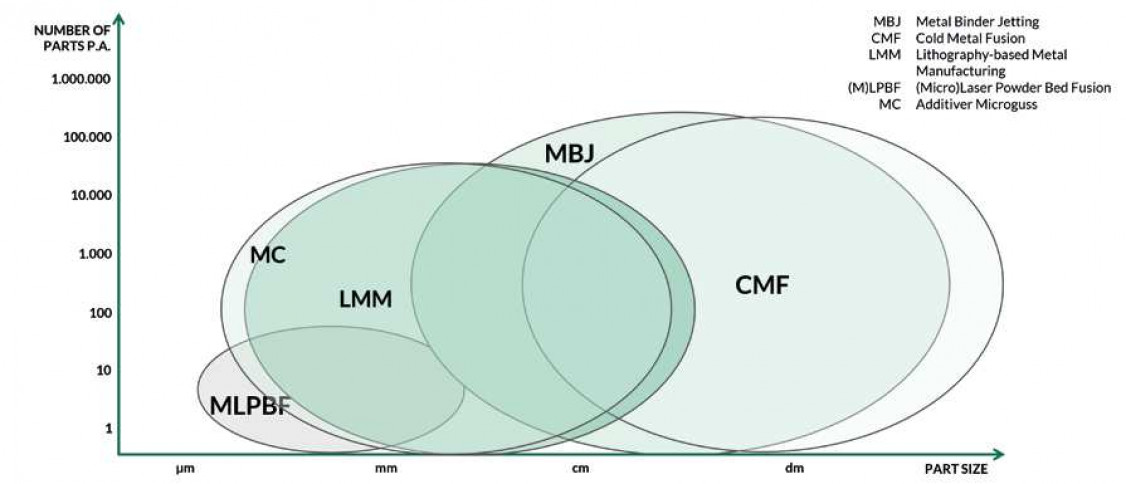
In der traditionellen Fertigung werden häufig Feingussverfahren oder Metallpulverspritzguss (MIM) für die Herstellung kleiner komplexer Bauteile eingesetzt. Da MIM aufgrund hoher Werkzeugkosten oft erst bei größeren Stückzahlen im vier- bis fünfstelligen Bereich wirtschaftlich ist, nutzen viele Anwender für kleinere Stückzahlen und Prototypen den additiven Microguss, ein abgewandeltes Feingussverfahren speziell für kleinste Bauteile.
Da sich sowohl LMM als auch additiver Microguss für kleine bis mittlere Jahresstückzahlen und komplexe Geometrien kleiner Metallbauteile eignen, ist ein Vergleich der Vorzüge und Einschränkungen der Verfahren notwendig, um die bestmögliche Entscheidung für die jeweilige Komponente treffen zu können (Bild 2).
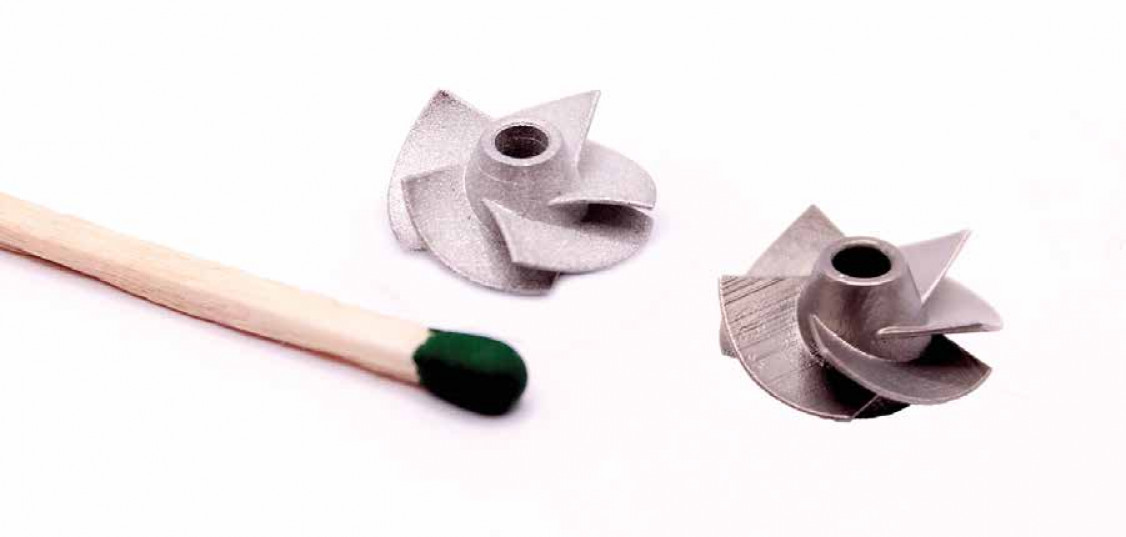
Oberflächenqualität
Die Oberflächenqualität ist für viele Anwendungen von entscheidender Bedeutung. Da beim sogenannten additiven Microguss im Prototypen- und Kleinserienbereich in der Regel auf 3-D-Druckmodelle aus Wachs als verlorene Modelle zurückgegriffen wird, ist häufig der Treppenstufeneffekt im gegossenen Endbauteil noch sichtbar. Außerdem kann es zur Lunkerbildung im Angussbereich kommen, sodass in diesem Bereich Oberflächenfehler auftreten können. Insgesamt wird beim additiven Microguss nach dem Abguss ein Ra von bis zu 6 μm erreicht. Durch anschließendes Gleitschleifen, Strahlen und Polieren können die Oberflächen auf einen Ra von bis zu 1 bis 2 μm verbessert werden.
Bei der LMM-Technologie liegt die Oberflächengüte ohne Nachbearbeitung bei einem Ra-Wert zwischen 2 und 3 μm. Mit vergleichbaren Oberflächenbearbeitungsmethoden wie beim additiven Microguss sind derzeit Oberflächen von bis zu 0,4 μm Ra erreichbar. Hinsichtlich der Oberflächenqualität hat die LMM-Technologie somit einen verfahrenstechnischen Vorteil gegenüber dem additiven Microguss, der jedoch stark von der gewählten Nachbearbeitungsmethode abhängt.
Toleranzen und Auflösung
Ein weiteres wichtiges Kriterium für die Auswahl der geeigneten Technologie ist die Präzision und welche Toleranzen eingehalten werden können. Das additive Microgussverfahren der Nonnenmacher GmbH erreicht je nach Bauteilgröße Toleranzen zwischen ±0,1 mm und ±0,03 mm. Da sowohl beim additiven Microguss als auch beim LMM-Verfahren mit einer Bauteilschrumpfung durch thermische Prozessschritte umgegangen werden muss, sind die Toleranzen immer in Abhängigkeit von der Bauteilgröße zu verstehen. Zur Einordnung eignet sich daher auch die Toleranzklassentabelle nach ISO 2768 bei der der additive Microguss die Klassen ISO 2768-m bis ISO 2768-f bedienen kann. Mit der LMM-Technologie von MetShape können Toleranzen von bis zu ±0,05 mm erreicht werden, allerdings ist auch dies abhängig von der Bauteilgröße und aufgrund der komplexen thermischen Prozessführung auch mit mehrfachen Iterationsstufen verbunden. Generell sind für erste Prototypen die Klassen ISO 2768-m oder ISO 2768-c zu erwarten. Bei Durchführung einer Kleinserie oder Serienanwendung mit LMM ermöglicht dann eine Aufmaßkorrektur eine Toleranz von ISO 2768-f. Im Bereich der Toleranzen glänzt der additive Microguss also bei ersten Prototypen mit einer höheren Genauigkeit, die mit LMM erst mit mehreren Iterationsstufen erreichbar ist. Durch die hohe Auflösung beider Verfahren zwischen 15 und 35 μm sind Bauteile mit sehr hohem Detaillierungsgrad realisierbar (Bild 3).
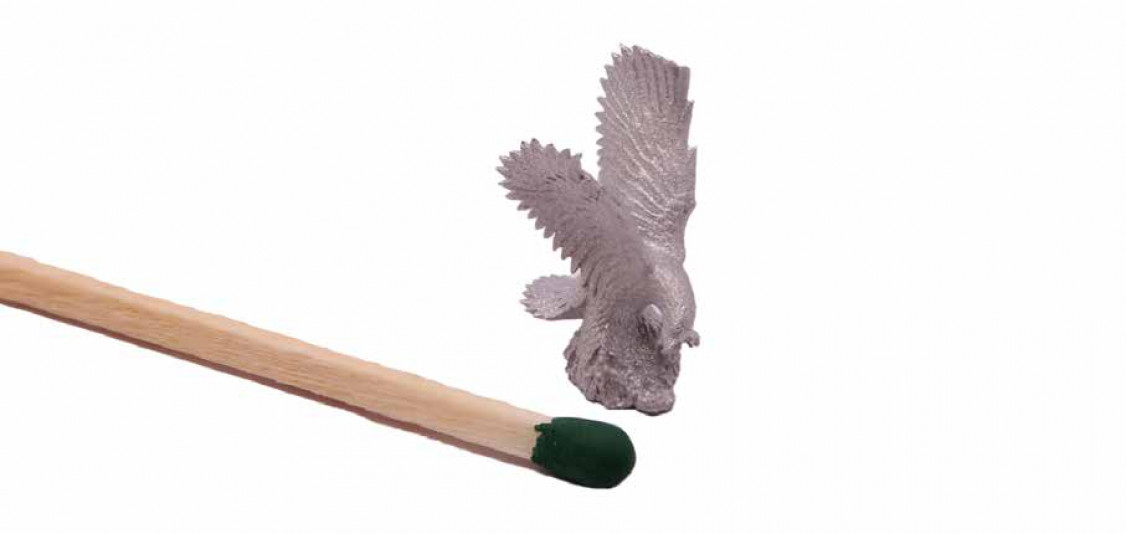
Feine Strukturen und dünne Wandstärken
Mit beiden Verfahren können Wanddicken ab 0,1 mm hergestellt werden. Die Machbarkeit hängt jedoch stark von der Länge und Höhe dieser Wandstärken ab. Beim additiven Microguss kann es beim Einbetten des 3-D-gedruckten Modells zu Werkzeugbrüchen kommen, während beim LMM-Verfahren sehr dünne Wandstärken beim Reinigen brechen können. Bei der Verwendung sehr filigraner Strukturen ist daher die Stabilität und Anbindung an den Bauteilkörper entscheidend für eine erfolgreiche Umsetzung (Bild 7).
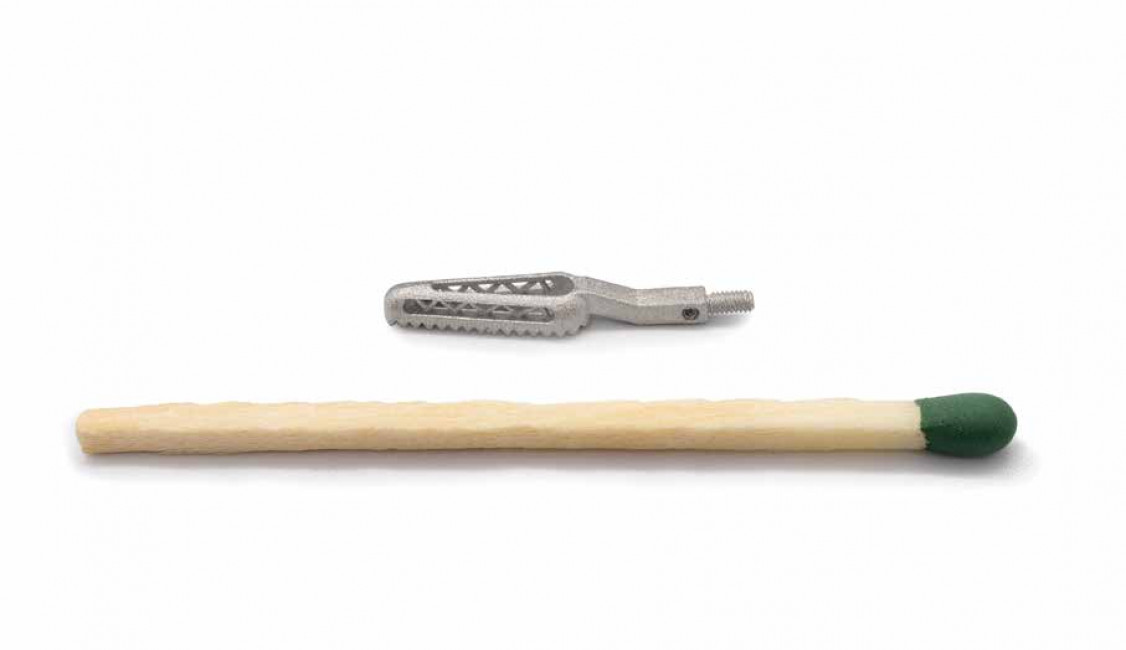
Eine der größten Herausforderungen der LMM-Technologie ist der Verzug beim Sintern, der insbesondere bei sehr dünnen Stegen auftreten kann. Bauteile wie in Bild 4 können durch additiven Microguss mit geringen Verformungen hergestellt werden, mit der LMM-Technologie wäre dies nur mit anschließendem Richten des Bauteils möglich. Dagegen sind Bauteile mit feinen Wandstrukturen wie im Aufmacherbild bevorzugt mit der LMM-Technologie herzustellen, da hier die Anbringung von Angüssen und der Materialfluss im additiven Microguss nur sehr schwer realisierbar sind.
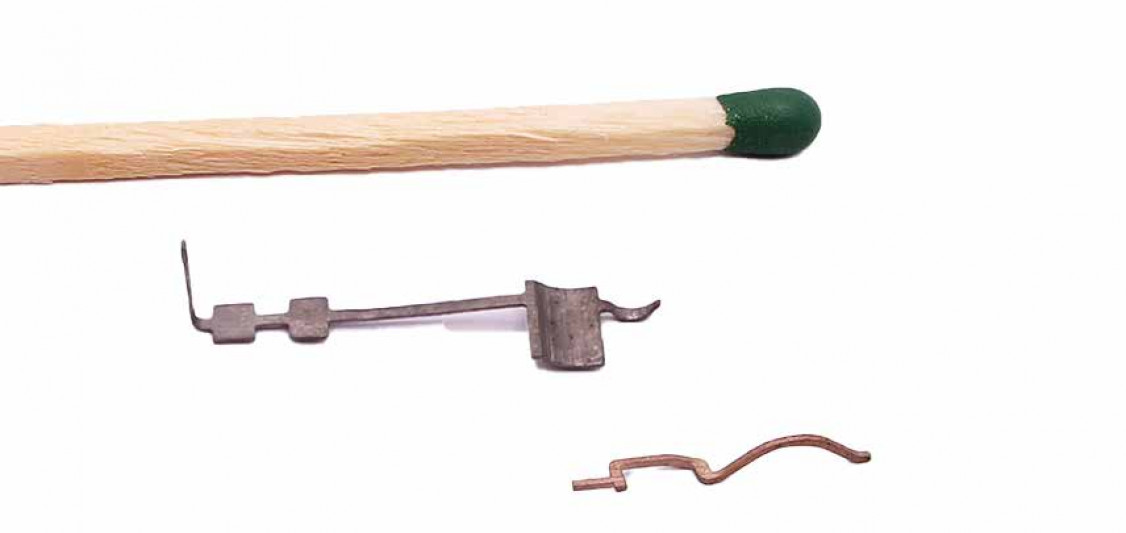
Materialvielfalt
Hinsichtlich der Materialvielfalt bietet das Feingießen eine Vielzahl von Werkstoffen von kupferbasierten Legierungen über Aluminium bis hin zu austenitischen, rostfreien Stählen. Generell können alle Metalle und Legierungen mit einer Schmelztemperatur unter 1500 °C verarbeitet werden. Im Bereich der indirekten Additiven Fertigung gibt es stärkere Einschränkungen. Da die Verfahren noch sehr jung sind und sich eines Binders, also Zusatzstoffen aus Wachs und Polymeren bedienen, die in einem Entbinderungs- und Sinterprozess entfernt werden müssen, ist der Aufwand zur Materialentwicklung sehr hoch. Bisher können mit dem neuen LMM-Verfahren die Edelstähle 316L und 17-4 PH angeboten werden. MetShape nimmt mit seiner Expertise im thermischen Prozessschritt der indirekten Prozesskette bei der Materialentwicklung in Kooperation mit dem Institut für strategische Technologie- und Edelmetalle der Hochschule Pforzheim (STI) und der Incus GmbH, dem 3-D-Drucker-Hersteller, eine zentrale Rolle ein. Teil dieser kooperativen Arbeit ist unter anderem die Qualifizierung von Titan Grade 5 und Edelmetallen wie Gold, aber auch der Formgedächtnislegierung Nitinol.
Innenliegende Kanäle
Beim additiven Microguss besteht die Herausforderung bei Bauteilen mit innenliegenden Kanälen darin, dass die Kanäle des Modells beim Einbetten in die Form leicht abbrechen können. Die Möglichkeit innenliegende Kanäle beispielsweise für die Kühlung von Werkzeugen umzusetzen, ist einer der Aspekte, bei der die neuen additiven Fertigungsverfahren punkten (Bild 5). Da das LMM-Verfahren auf Stützstrukturen beim Druck komplett verzichten kann, ist es im Gegensatz zu anderen additiven Fertigungsverfahren möglich, die Kanäle funktionsgetreu zu fertigen. Allerdings hängt die Machbarkeit entsprechender Kühlstrukturen stark von Durchmesser, Länge und Winkel des Kanals ab, da bei der LMM-Technologie die Reste des Binder-Pulver-Gemischs in einem Spülvorgang entfernt werden.
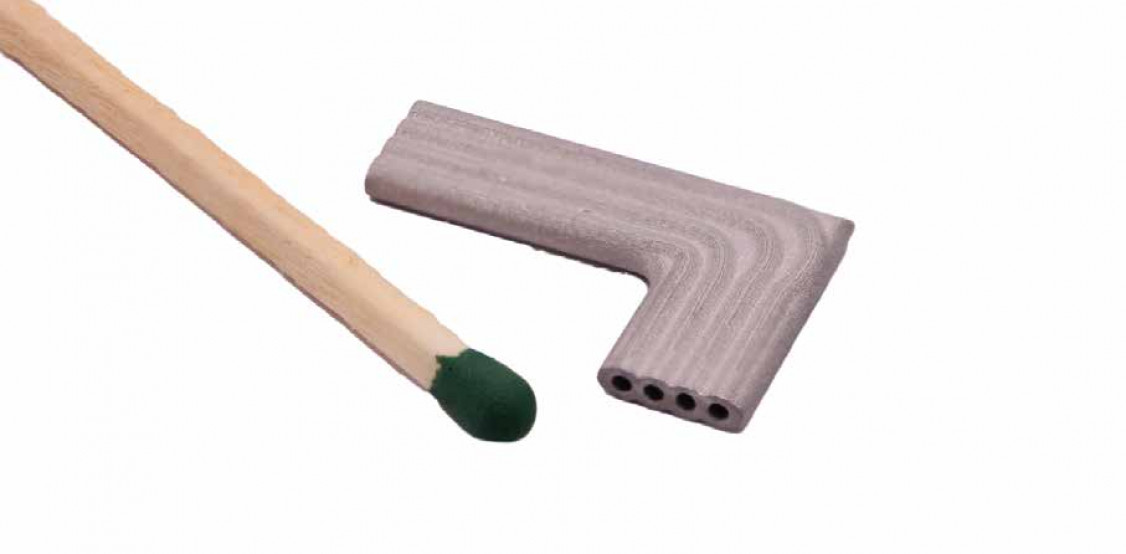
Funktionsintegration und Baugruppensubstitution
Eines der Hauptmerkmale beider Technologien ist die Ermöglichung von Funktionsintegration und Baugruppensubstitution bei komplexen Bauteilen (Bild 6).

Dadurch kann der Aufwand für die Fertigung einzelner Komponenten und anschließender Montage reduziert werden, indem ein komplexes Bauteil gefertigt wird. Ein Beispiel hierfür ist die Anwendung in Bild 8.
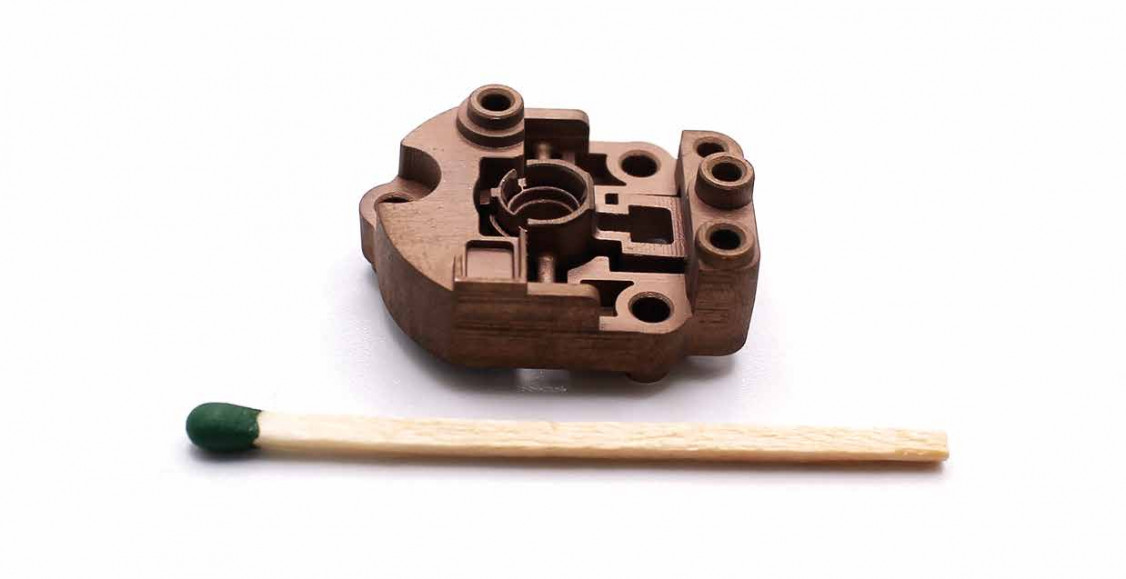
Die Entwicklung dieser Aufnahme für ein Lasermessgerät wurde, bis sämtliche Funktionalitäten gegeben waren, mit additiv gefertigten Bauteilen abgedeckt. Unter anderem sind zur Aufnahme des Lasers zwei Clipfunktionen und zu dessen Justierung eine Torsionsfeder integriert. Nach Validierung dieser Bauteile wurde für die Großserienfertigung ein Werkzeug angefertigt.
Insgesamt ermöglichen sowohl die sinterbasierte Additive Fertigung mit der LMM-Technologie als auch der additive Microguss die Herstellung von komplexen metallischen Klein- und Mikrobauteilen bereits in geringen Stückzahlen. Beide Verfahren haben dabei Stärken und Schwächen, weshalb jeweils anwendungsspezifisch zu entscheiden ist, welches Verfahren besser geeignet ist. Sind die Faktoren Toleranz oder Materialvielfalt bereits bei ersten Prototypen ausschlaggebend, ist der additive Microguss vorzuziehen. Ist die Oberflächenqualität entscheidend oder liegen sehr komplexe Strukturen vor, wird das LMM-Verfahren empfohlen.
Schlagworte
3-D-DruckAdditive FertigungAluminiumBinderFertigungFertigungsverfahrenGussKupferMesseSchleifenSchmelzenStrahlenWerkstoffe