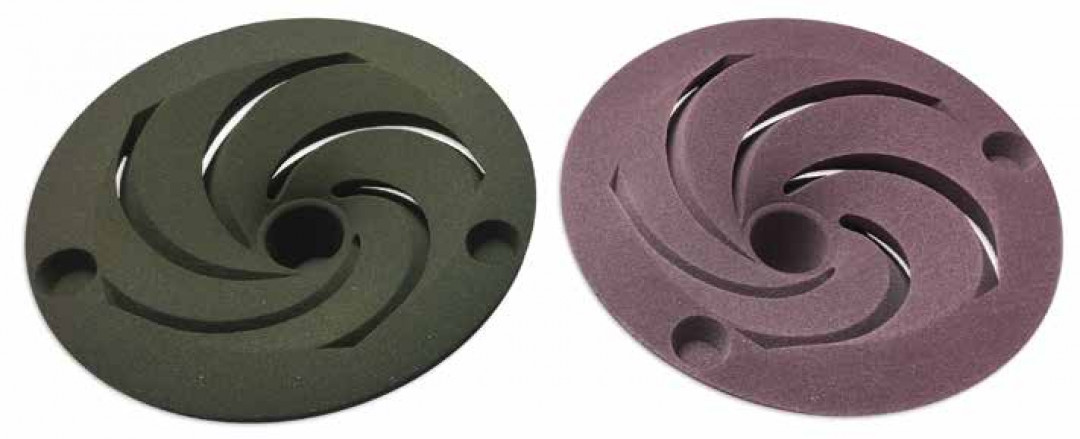
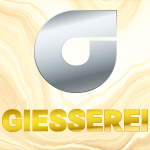
Fachlicher Rückblick. Lesen Sie einen Fachartikel aus der GIESSEREI 03/2018.
VON THOMAS FRANK, TOBIAS TUFFENTSAMMER, GERSTHOFEN
Wie überall bestimmen auch im Pumpenmarkt Preis und Qualität einer Pumpe die Nachfrage. Selbst bei einer guten Marktposition ist für den Verkauf jeder einzelnen Pumpe immer noch die Wirtschaftlichkeit entscheidend. Dabei ist es kein leichtes Unterfangen, ein produktionsaufwendiges und komplexes Produkt wie eine Pumpe in seiner Leistungsfähigkeit einerseits und seinen Produktionskosten andererseits ständig weiter zu optimieren.
Für gegossene Bauteile einer Pumpe, insbesondere für das Herzstück, den Impeller, entfällt mit dem 3-D-Druck für die Sandgussformen jetzt ein kompletter Arbeitsschritt in der Nachbereitung, der zuvor viel Zeit und Arbeitsaufwand in Anspruch genommen hat. In der Branche sind pro Impeller Nachbereitungszeiten von durchschnittlich 10 bis 15 min üblich, was einen vergleichsweise hohen Zeitaufwand in der Serienproduktion darstellt. Der industrielle 3-D-Druck erschließt also Pumpenherstellern und ihren Gießereien ganz neue Einsparpotenziale bei den Herstellungskosten.
Die aufwendige Nacharbeit an den Schaufellamellen und vor allem an der Blattspitze, die aus dem traditionellen Gussverfahren resultiert, entfällt mit dem 3-D-Druck komplett. Das fertige Gussteil kann ohne Zwischenschritt umgehend von der Gießerei in die Abteilung für Laufruhe überführt werden. Dort können die Spezialisten in der Qualitätssicherung noch mögliche Feinanpassungen durchführen. Hinzu kommen weitere Vorteile, auf die später noch eingegangen wird.
3-D-Druck braucht keinen Kernkasten
Bei einem traditionell geschossenen Kern setzen komplexe Geometrien voraus, dass Kerne als einzelne Losteile oder ohne Hinterschneidung konstruiert sind. Wäre dies nicht der Fall, würde sich beim Versuch der Entnahme aus dem Kernkasten der Kern verkanten und selbst blockieren (Bild 1). Denn im Kernschießverfahren wird der Sand in den Kernkasten eingeschossen und dann ausgehärtet. Beide Bestandteile bilden also unausweichlich eine starre Einheit, aus der die Entnahme eines Kerns mit Hinterschneidung, wie im Fall des Impellers, nicht ohne weiteres durchführbar ist.
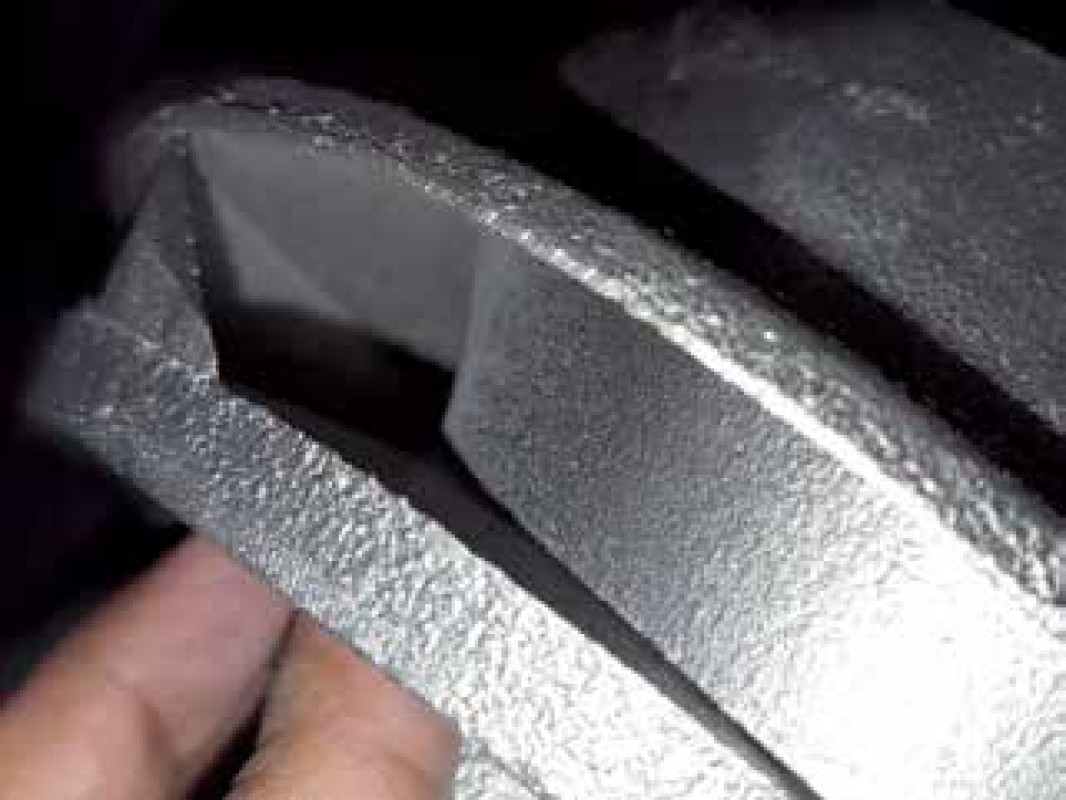
Das bedeutet, dass bei der konventionellen Produktion des Impeller-Kerns nur eine grobe Kontur des eigentlichen Gussteils herstellbar ist. Diese muss dann in einem gesonderten Arbeitsschritt durch Nacharbeit zur geforderten Perfektion gebracht werden. Genau diese Vorgehensweise ist heute immer noch weit verbreitete Realität in der Gießereibranche. Die Lösung: Im 3-D-Sanddruck wird genau das gedruckt, was der Konstruktion entspricht. Fließender Produktionsprozess mit 3-D-Kern- und Formdruck. Bei Kernen und Formen, die im 3-D-Druck hergestellt werden, laufen die CAD-Daten direkt ohne Umwege und ohne teure Werkzeuge in den 3-D-Drucker. Das Binder-Jetting-Verfahren von ExOne baut im 3-D-Druck Schicht für Schicht, mit einer Schichthöhe von 0,28 mm bis 0,38 mm, den Kern des Impellers mit so präziser Genauigkeit auf, dass die vollendete Form des Propellers bereits in der gedruckten Negativform erkennbar ist (Bild 2). Die Negativform des Impellers ist also an den Blattenden schon exakt so, wie es beim gegossenen Endprodukt aussehen soll. Der Produktionsprozess verkürzt sich damit erheblich im Vergleich zum Kernschießverfahren.
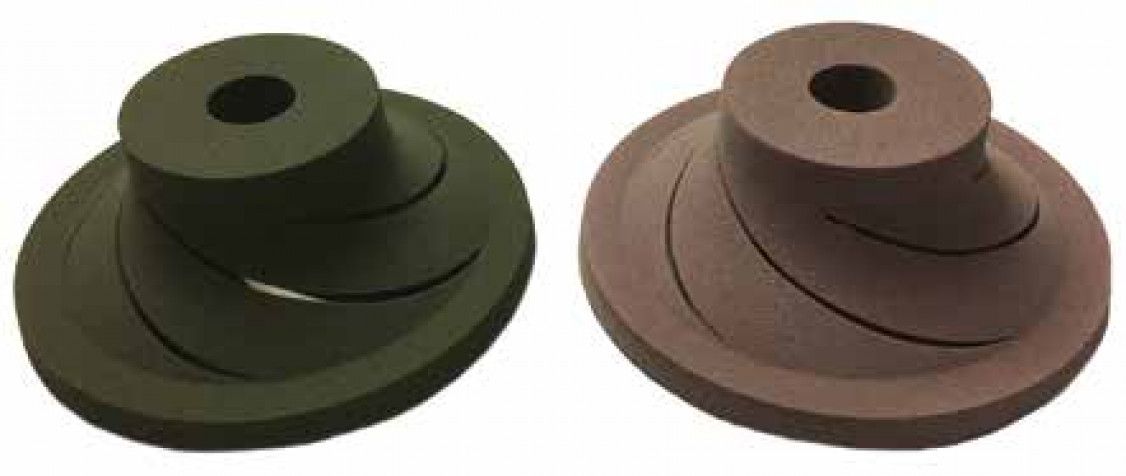
Der zweite große Unterschied ist, und dies ist der ausschlaggebende Dreh- und Angelpunkt für die Einsparung eines kompletten Produktionsprozesses, dass beim 3-D-gedruckten Kern und der Außenform einfach alles aus einem Sand-Binder-Gemisch besteht.
Besonders durch die Möglichkeit des Hohldruckens und der verbesserten Entkernungseigenschaften lassen sich beim 3-D-Druck die gedruckte Außenform und der innere Kern einfach vom fertigen Gussprodukt entfernen. Die Blattspitze des Impellers muss für den Guss weder in den CAD-Daten zuvor geometrisch beeinflusst werden noch gibt es bei der Entnahme irgendwelche Blockaden.
Weitere Kostenvorteile
Für Gießereien spielen noch weitere Einsparungspotenziale durch den 3-D-Druck eine wichtige Rolle. Um nur einige zu nennen, beginnen die Vorteile schon in der Prototypenphase mit einer optimierten Entwicklungszeit. Bis das Bauteil vom Pumpenunternehmen endgültig zur Produktion freigegeben ist, lassen sich jegliche Änderungen in den CAD-Daten einfach in den 3-D-Druckprozess überführen und auf Knopfdruck sofort realisieren. Der gesamte Aufwand für den traditionellen Formherstellungsprozess entfällt einfach. Das steigert nicht nur die Produktivität, sondern spart auch Verbrauchsmaterialien, Werkzeugkosten, Personalaufwand, Lagerkosten, etc. und beschleunigt die Bearbeitungszeit von Kundenaufträgen signifikant. Lagerkosten sind ja nicht nur ein Thema für Gießereien. Bei der Vielzahl von Pumpenmodellen sind diese Kosten auch den Pumpenherstellern „ein Dorn im Auge“. Durch eine schnellere Produktion im 3-D-Binder-Jetting-Verfahren lassen sich solche Kosten deutlich senken. Zusätzlich ist die Generierung von Neugeschäft möglich: Pumpengussteile sind wichtige Umsatzposten im Ersatzteilgeschäft und in der Nachproduktion von industriellen Unikaten (Reverse Engineering).
Auch die Qualitätsverbesserung beim Gießen und beim gegossenen Endprodukt ist ein wirtschaftlicher Faktor. Beim 3-D-Druck gibt es einfach keine einzelnen Kernbaugruppen, die miteinander verklebt werden und möglicherweise Miss-Matches und dadurch Personalkosten oder im schlechtesten Fall Ausschusskosten für die Nacharbeit verursachen. Bezüglich hoher Anforderungen an die Komplexität gibt es zudem kaum noch Grenzen, die eine 3-D-gedruckte Form nicht überwinden kann. Der 3-D-Druck ist für hohe Komplexität wie geschaffen und sichert eine hohe Reproduzierbarkeit ohne aufwendigen Formenbau. Das erfüllt nicht nur die wirtschaftlichen Erwartungen der Industrie, sondern schafft auch Wettbewerbsfähigkeit in Sachen Ergonomie, Effizienz und Zuverlässigkeit der industriellen Produktion.
Selbst, wenn Pumpenunternehmen und beauftragte Gießereien schon seit vielen Jahren gut zusammenarbeiten und sämtliche Produktionsabläufe perfekt aufeinander abgestimmt sind, es führt, mit Blick auf die weitere rasante Entwicklung, kein Weg an der additiven industriellen Fertigung vorbei. Der 3-D-Druck erzeugt auf dem Markt der Pumpenhersteller schon heute einen starken Sog und gleichzeitig hohen Druck. Die bei Innovationen führenden Unternehmen müssen hier an „vorderster Stelle“ schon aufgrund ihres Führungsanspruchs dabei sein, wodurch automatisch der Druck auf traditionelle Unternehmen weiter zunimmt. Daher können sich auch lokale Größen der Gießerei-Industrie mit regionaler Vorherrschaft weder dem steigenden Wettbewerbsdruck entziehen noch die Erwartungen der Pumpenindustrie ignorieren. 3-D-Druck ist für alle Beteiligten von Vorteil.
Schlagworte
3-D-DruckBinderCADFertigungFormenbauGussGussformenGussteileKonstruktionProduktion