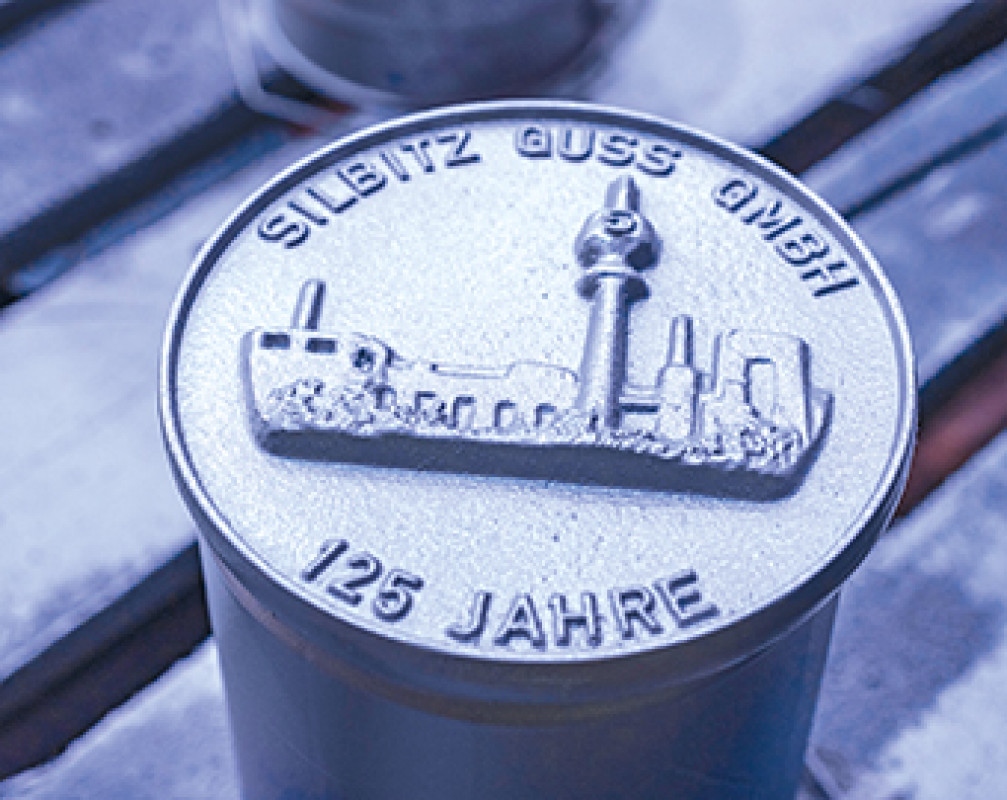
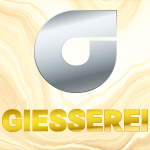
Einzigartiger Schmelzbetrieb
In der Gießhalle stehen Bauer und Eichler nun mit ihren Besuchern von der GIESSEREI gespannt vor einer runden mit Chromerzsand gefüllten Form mit rund drei Metern Durchmesser. Ein Kran hievt eine Acht-Tonnen-Pfanne mit glühendem, nickellegiertem Stahl über die Form. Wenig später strömt die Schmelze per Stopfenfüllung in nur anderthalb Minuten in die Sandform, begleitet von Gluckern und Funkensprühen. Flammen stieben aus der Form, ein Gießer mit silbernem Schutzanzug isoliert daraufhin die offenen Speiser rund um den Einguss mit Abdeckpulver, um eine gleichmäßige Erstarrung des Gussteils sicherzustellen. Hier entsteht ein Leitrad, das einmal Bestandteil einer Fahrwerkskomponente eines Baggers im Tagebau sein wird.
Etwas abseits von der Gruppe steht Schmelzbereichsleiter Stefan Fuchs. Er passt mit seinen 38 Jahren weniger zur alchemistischen Schablone früherer Schmelzer, aber umso besser in das junge Gesamtbild des Unternehmens. Mittels Gießereimechaniker-Lehre und parallelem Studium konnte auch Fuchs schon mit Ende zwanzig seine Führungsposition im Schmelzbetrieb übernehmen. Und der ist im deutschen Gießereikosmos alles andere als gewöhnlich, mit seinen zwei Lichtbogenöfen, seinen vier Mittelfrequenz-Induktionsöfen sowie der Detem-Anlage für die Sekundärmetallurgiebearbeitung. Voraussichtlich einzigartige Besonderheit seiner Abteilung ist jedoch, dass hier sowohl Stahlguss als auch Sphäroguss geschmolzen und drei Formlinien bedient werden – zwei davon kompatibel für Stahlguss.
Kein Wunder also, dass Silbitz Guss auf gutes Know-how und studierte Fachkräfte setzt – optimalerweise ausgebildet im eigenen Haus. Kürzlich erst sind zehn weitere Auszubildende unbefristet eingestellt worden, die auch parallel studieren können. Von den 430 Mitarbeitern am Standort Silbitz absolvieren aktuell 27 eine Ausbildung.
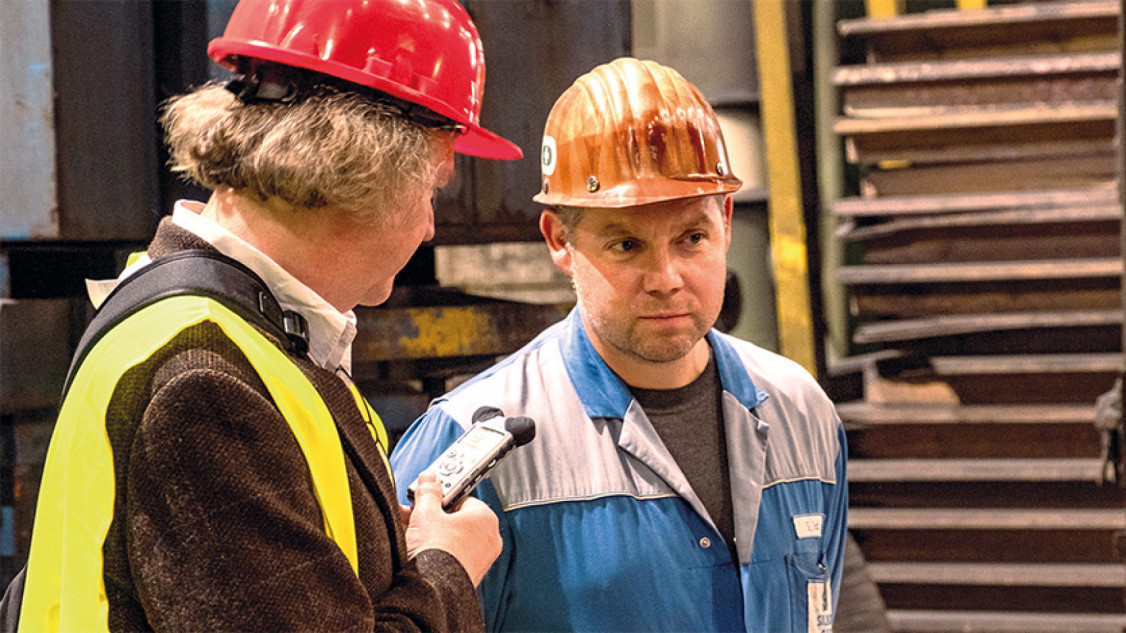
Europäische Marktführung bei Schiffskolben
Die gut ausgebildeten Kräfte zahlen sich auch bei der Werkstoffentwicklung aus. In den letzten Jahren entwickelten die Silbitzer im eigenen Haus mischkristallverfestigtes Gusseisen sowie NiResist, ein hochbeanspruchbares austenitisches Gusseisen mit Kugelgrafit, das mit mehr als 30 Prozent Nickel legiert ist. „Das kann nicht jeder herstellen“, sagt Daniel Bauer stolz.
Die Gießer aus Silbitz reagieren damit auch auf Substitutionsdruck aus dem Schmiedebereich. Denn eines ihrer Hauptprodukte sind große Gusskolben und Zylinderdeckel für Großdiesel- und Gasmotoren im Gewichtsbereich von 30 bis zu mehreren Hundert Kilogramm, bei denen Silbitz Guss Marktführer in Europa ist. Allerdings setzen sich bei neueren Schiffsmotoren bereits Schmiedeteile durch, die den Verdichtungsdruck in den Motoren besser aushalten können. Zeit zum Handeln also, um nicht Teile der Kolbenproduktion aus der Hand zu geben. Kolben mit dem Gewicht von jeweils knapp 200 Kilogramm tun auch in der britischen Queen Mary II, einem Transatlantikliner und Kreuzfahrtschiff ihren Dienst. „Der 25 000 PS-Motor der Queen Mary II ist so gewaltig, dass ein weiterer Antrieb erforderlich ist, um ihn anzulassen“, weiß Bauer.
Vorbei an einer Strahlanlage für Zylinderköpfe, die an Haken davorhängen, und Anlagen mit überdimensionalen Ausschlagrosten für die Trennung von Guss und Formsand, geht es weiter zur mechanischen Bearbeitung. Auch die leitet mit Nico Schmidt ein Mann von Anfang 30. Schmidt hat mit einem Bachelor in Maschinenbau und Produktionstechnik sowie einem weiterführenden Masterstudium in Maschinenbau und Management gleich zwei Abschlüsse in der Tasche. Er delegiert hier 25 Mitarbeiter und überwacht einen Maschinenpark mit zahlreichen Karusselldrehmaschinen, Schrägbrettdrehmaschinen, Plandrehmaschinen sowie einem Bohrwerk und einem 5-Achs-Bearbeitungszentrum. Aktuell wird gerade eines der abgegossenen Leiträder auf einer Karusselldrehmaschine bearbeitet. Späne und ganze Metallstreifen dreht die Maschine von dem überdimensionalen Bauteil ab, das für einen Bergbaumaschinenhersteller gefertigt wird. Auch Kolben werden hier vorbearbeitet. Einige Bauteile der Gruppe bekommen ihren letzten Schliff auch in der mechanischen Bearbeitung im anderthalb Autostunden entfernten Staßfurt in Sachsen-Anhalt, die auch zum Gießereiverbund gehört.
Geschäftsführer Torsten Tiefel empfängt zum Gespräch über das Unternehmen und die lange Historie der ehemals größten Stahlgießerei der DDR. Das niedrige Durchschnittsalter von 42 Jahren im Werk hat System. „Eine gute Mischung aus alten Haudegen und jungen Kräften ist eines unserer Erfolgsrezepte“, sagt der 49-jährige Manager, der seit 2010 im Unternehmen ist. „Wir denken, dass das Team immer stärker ist als der Einzelne. Nicht nur Erfahrung bestimmt bei uns die Aufstiegschancen“, ergänzt er. Der jugendliche Charme des Produktionsbetriebs hat Strahlkraft: Mit einer vorbildlichen Ausbildung und frühen Aufstiegschancen ist der Nachwuchs gesichert. Der Betrieb beschäftigt die bundesweit beste Modellbau-Auszubildende und wurde von der IHK als Top-Ausbilder der Region ausgezeichnet.
Historie: Industrialisierung, DDR-Leitbetrieb, Neuanfang
Während heute in Silbitz Gussteile für die Motorentechnik, Baumaschinen und den Bergbau hergestellt werden, war der Zweck für die Gründung noch ein anderer. Die erste Gießerei der heutigen Silbitz Gruppe wurde 1896 in Zeitz-Rasberg als Zulieferbetrieb für den Maschinenbau zur Industrialisierung der Zückerrübenproduktion errichtet. Das 2009 neu an diesem Standort errichtete Werk, das heute Windkraftguss fertigt, zeugt mit der benachbarten größten Zuckerrübenmühle Europas noch von dieser Vergangenheit.
Silbitz Guss selbst wurde zu Zeiten der Weimarer Republik gebaut. Die Wende überstanden von ehemals 22 Stahlgießereien in der DDR nur zwei – eine davon war Silbitz Guss, die nach der Einführung der D-Mark und dem daraus folgenden Verlust des osteuropäischen Kundenstamms noch einmal bei Null anfangen musste, aber damals mit Kunden wie dem Getriebehersteller ZF, Bosch Rexroth, Knorr-Bremse und der Bahn wieder auf die Beine kam. Entscheidend für das Überleben von Silbitz Guss war dabei die Erweiterung der Werkstoffpalette um Eisenguss, das erst seit Anfang der 1990er-Jahre gefertigt wird.
2013 dann der Schock: Die Weiße Elster stieg über ihre Ufer und überflutete weite Teile der Produktion (die GIESSEREI berichtete). „Wenn ich heute die Bilder aus Ahrweiler sehe, bekomme ich immer noch eine Gänsehaut“, gesteht Tiefel. In einem gemeinsamen Kraftakt von Mitarbeitern und Gießereigruppe sowie der Deckung der knapp 15 Millionen Euro Flutschäden durch die Versicherung überstand Silbitz Guss die damalige Krise. Auch Corona scheint nach zwischenzeitlichen pandemiebedingten Einbrüchen von rund einem Drittel der Produktion überwunden zu sein. Tiefel hofft in diesem Jahr bei Umsätzen von 155-160 Millionen Euro wieder auf erste Gewinne.
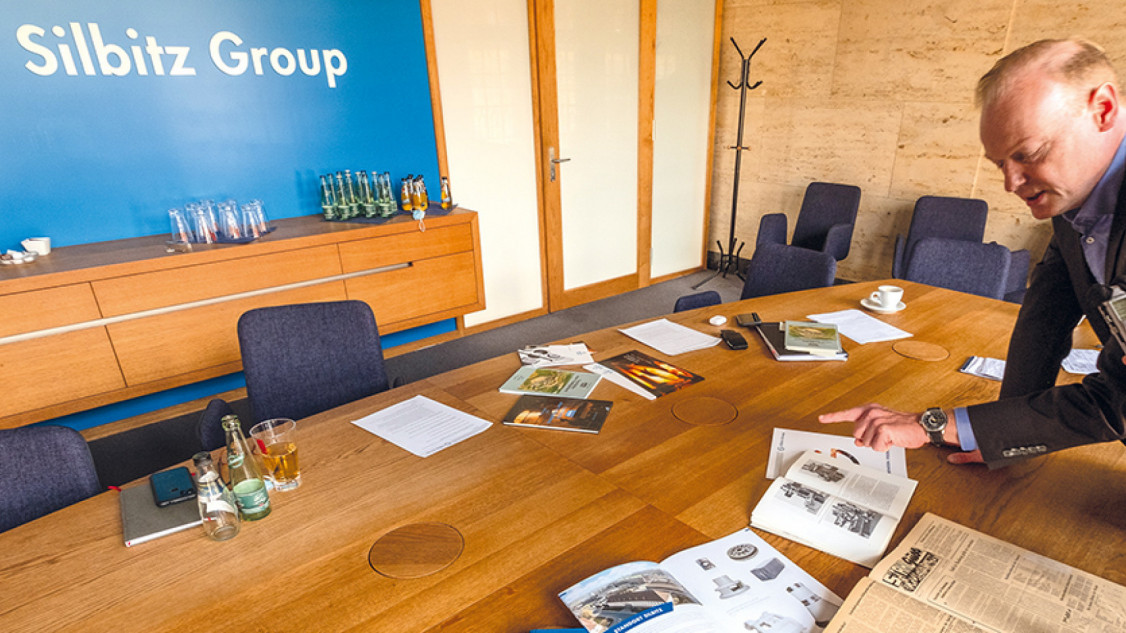
Der Verband als Hüter nachhaltiger Lieferketten?
Auch künftigen Herausforderungen blickt man in Silbitz zuversichtlich entgegen. Ein Klimaschutzplan mit Umsetzung vor 2050 liegt vor. Kernstück soll der mit Grünstrom betriebene Schmelzbetrieb sein, aber auch die Deckung der Materialversorgung durch 80 Prozent recyceltes Metall. Nähere Details zur genauen Umsetzung will Tiefel bald liefern. Elisa Eichler wird die ambitionierten Pläne dann im Rahmen ihrer Öffentlichkeitsarbeit publik machen.
Damit die Rechnung für klimabewusste Gießereien aufgeht, gilt es Tiefel zufolge allerdings, nachhaltige Lieferketten zu schaffen: „Wir sehen, dass einige Unternehmen ein Green-Label betreiben, aber auf der Einkaufsseite sagen, es ist uns egal, wo die Teile herkommen.“ In der Pflicht sieht er hier auch den Verband als starke Stimme für nachhaltiges Wirtschaften auf dem Weg in die Klimaneutralität. Tiefel selbst engagiert sich im BDG-Beirat Stahl- und Eisenguss.
Die „Old Economy“ ist für ihn ein überkommenes Klischee. Und die Klimawende, an der die Silbitz Group im Windkraftbereich und bei der Realisierung des ersten Wasserstoff-Personenzugs Coradia-Ilint gemeinsam mit dem Railway-Bereich der ZF Group aktiv mitarbeitet, sieht er als Chance, den verkrusteten Blick auf die Branche aufzubrechen – von einer neuen Gießergeneration mit dem Anspruch einer nachhaltigen und modernen Produktion.
(Autor: Robert Piterek, Düsseldorf)
Schlagworte
EisengussFertigungGießereiGusseisenGussteileKommunikationLieferketteMarketingMaschinenbauMesseMetallurgieProduktionStahlgussWerkstoffe