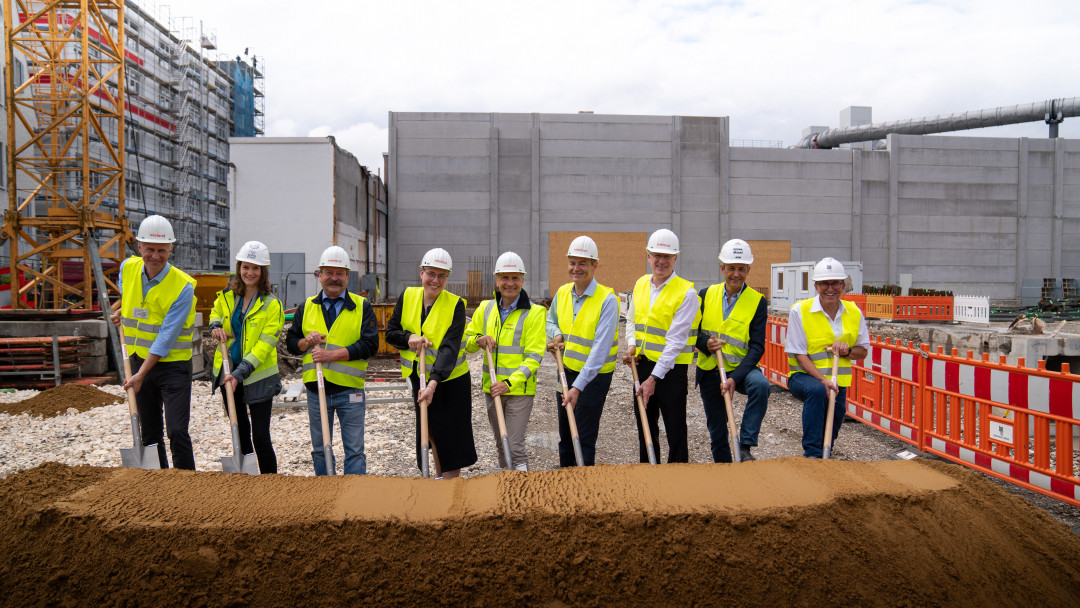
Mit dem offiziellen Spatenstich am 27. Mai 2024 fällt bei Wieland der Startschuss für ein Projekt mit großer Wirkung: Die Gießerei am Standort Vöhringen wird um ein Recyclingcenter erweitert, das dank modernster und effizienter Technik die Aufbereitung von Kupferschrotten ermöglicht und somit die weltweite Recyclingquote der Wieland-Produkte nach der Inbetriebnahme auf über 80 Prozent erhöht.
„Betrachten wir die Erweiterung der Gießerei in Vöhringen durch ein Recyclingcenter aus der Nachhaltigkeitsperspektive, handelt es sich hier um ein globales Leuchtturmprojekt mit Signalwirkung“, betont Dr. Erwin Mayr, CEO der Wieland Gruppe. „Denn die neue Anlage ist ein wichtiger Baustein auf unserem Weg, den Materialkreislauf nachhaltig zu schließen und unsere globale Recyclingquote in naher Zukunft auf 100 Prozent zu erhöhen.“ Dadurch kommt Wieland seinem Ziel der treibhausgasneutralen Produktion bis spätestens 2045 einen großen Schritt näher. Weitere Eckpfeiler der Dekarbonisierungsstrategie sind die Elektrifizierung aller Anlagen zum Ausstieg aus fossilen Brennstoffen sowie der vollständige Einsatz erneuerbarer Energien durch grüne Stromlieferverträge und der Eigenstromerzeugung mithilfe von Photovoltaik- und Windkraftanlagen.
Mit dieser Investition setzt Wieland darüber hinaus auf einen strategischen Stützpunkt in der Materialversorgung, da die Werke in ganz Europa und Teilen Asiens mit hochwertigen Kupferhalbzeugen aus Vöhringen beliefert werden. Für Anton Zierhut, President Extruded Products der Wieland Gruppe, ist die Investition ein klares Bekenntnis zum Standort Vöhringen, an dem auf diese Weise 25 neue Arbeitsplätze entstehen. „Unser neues Recyclingcenter ist eine zukunftsweisende Investition für unser Hauptwerk in Vöhringen und wird eine wichtige Rolle in der weiteren Differenzierung zum Wettbewerb spielen.“
In der neuen Anlage auf dem Gelände der Wieland-Gießerei werden künftig Reinkupfer-Bolzen mit einem Rezyklatanteil von 100 Prozent produziert. Hierfür kommen Kupferschrotte und -granulate sowie Produktionsschrotte aus der Fertigung vor Ort zum Einsatz. Auf diese Weise ist nicht nur die Versorgung verschiedener eigener Standorte mit Material gesichert, sondern die Anlage wirkt sich auch positiv auf den CO2-Fußabdruck der Wieland-Produkte aus. Der Recyclingprozess basiert auf einem sehr energieeffizienten Verfahren, der sogenannten Feuerraffination. Mit diesem Schritt setzt das Unternehmen neue Standards, von dem auch die Kunden profitieren. Sie erhalten Vormaterial mit dem branchenweit niedrigsten Product Carbon Footprint (PCF) und können dadurch ihre eigenen Prozessketten emissionsärmer und nachhaltiger gestalten.
Schlagworte
EisenFertigungHalbzeugeKupferNachhaltigkeitProduktionRecycling