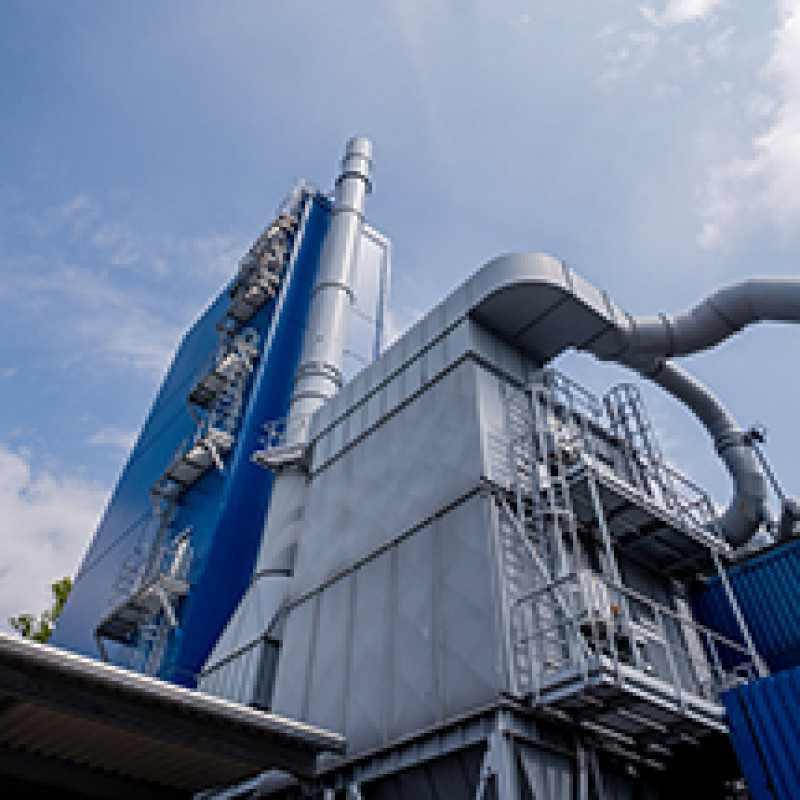
Der Zeitplan für die Gießerei-Industrie steht fest: Spätestens 2045 muss die Branche klimaneutral produzieren. Auch der BDG hat sich kürzlich auf dem Zukunftstag ausgiebig dem Thema gewidmet. Lohmann Guss in Witten-Annen ist dank eigenem Wasserkraftwerk und Bekenntnis zu Nachhaltigkeit sowie Kompensation schon heute klimaneutral und damit Vorreiter in der Branche. Geschäftsbereichsleiter Gießerei Thorsten Kutsch warnt davor, die erforderlichen Maßnahmen auf die leichte Schulter zu nehmen.
Das Lohmann-Stammwerk für Spezial- und Edelstähle liegt auf einer langgezogenen Insel – auf der einen Seite von der Ruhr, auf der anderen vom Mühlengraben gesäumt. Direkt vor dem Werksgelände im Wittener Stadtteil Herbede staut ein langes Wehr den Mühlengraben auf, darunter fließt dieser träge zum Kemnader Stausee weiter südlich. Am Geländer zum Fluss steht Thorsten Kutsch, Geschäftsbereichsleiter Gießerei bei Lohmann, graumeliert, Anfang 50 und Vollblutgießer. Kutschs Laufbahn begann als Modelltischlerlehrling und führte über das Fachabitur, ein Gießereitechnikstudium in Duisburg und eine erfolgreiche Karriere zunächst bei Lohmann und später bei GF Mettmann wieder zurück zu Lohmann, wo er seit 2012 die Gießerei leitet.
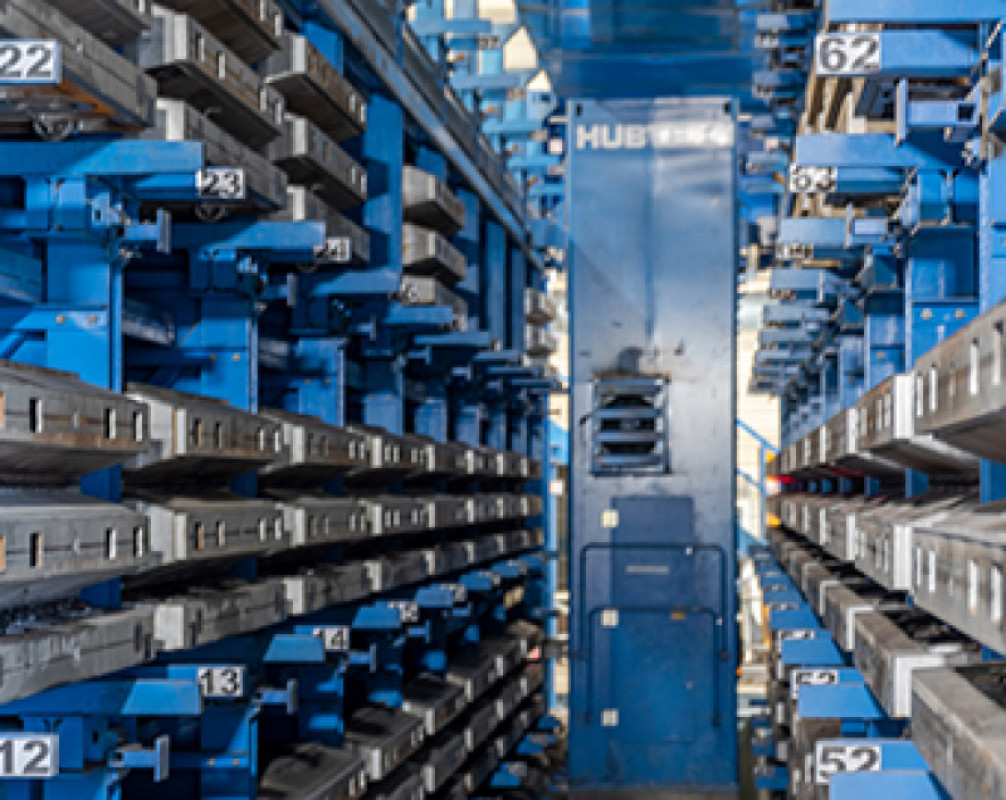
Klimaneutraler Strom aus Solar- und Wasserkraft
Kutsch weist auf den aufgestauten Mühlengraben und ein altes Fachwerkhaus neben dem Wehr und erklärt, dass hier vier Turbinen erneuerbare Wasserkraft abschöpfen, die jährlich 4,5 Millionen Kilowattstunden Strom liefern. Das entspricht dem Energiebedarf von rund 1100 Haushalten. „Die Wasserkraft ist für Lohmann eigentlich ein alter Hut“, sagt er. Denn das Unternehmen nutzt schon seit 1859 die Strömungskraft des Flusses. Damals stand hier nur ein Stahlwerk, später kam eine Gießerei dazu, die 1973 in den Wittener Stadtteil Annen umzog. Der „alte Hut“ hat heute neue Brisanz gewonnen. Denn nicht zuletzt durch die Beschlüsse der Regierung zur Klimaneutralität bis 2045 ist erneuerbare Energie ein wertvolles Gut geworden, das Lohmann nun die Gelegenheit gibt, bei der erforderlichen Transformation der Industrie voranzupreschen. Mithilfe der hier gewonnenen Energie ist die von Kutsch geleitete Gießerei im 15 Kilometer entfernten Annen nun 24 Jahre vor dem Stichtag klimaneutral.
Das Wasserkraftwerk ist aber nicht nur ein glücklicher Zufall für die Wittener Edelstahlspezialisten. Lohmann setzt schon lange auf Nachhaltigkeit. Kutsch führt die Besucher nun tiefer ins Stahlwerk hinein. Es geht vorbei an Werkshallen, vor denen Stahlteile, sogenannte Platinenstücke, in großen Kisten liegen, die erhitzt und später zu Tafelblechen gewalzt werden. Hier fertigen 272 Werker vorkonfektioniertes Halbzeug und Werkzeugstähle in relativ kleinen spezialisierten Chargen. Mit einer Hubbühne geht es nun hoch über die Dächer des Stahlwerks. Soweit das Auge reicht, sind die Werksdächer der umliegenden Hallen mit Solarpaneelen bestückt, die weitere 200 000 Kilowattstunden Strom jährlich ins Netz speisen. Installiert wurden sie im Jahre 2010, als Klimaneutralität für viele Menschen in Deutschland noch ein Fremdwort war.
Fokus auf Nachhaltigkeit und Klimaschutz
Zur Fußball-Europameisterschaft ist das Hauptgebäude mit vielen bunten Flaggen geschmückt. Spielt die Heimat eines Mitarbeiters bei der EM, hängt hier auch die Fahne. „Scheidet eine Nation aus, wird die Flagge eingeholt“, erklärt Thomas Wagner, Stellvertretender Instandhaltungsleiter in Herbede. Er steht neben einer riesigen Platane, die rund 25 Meter hoch ist und gut und gerne aus der Anfangszeit des Familienunternehmens stammen könnte, das bereits 1790 gegründet wurde. Ursprünglicher Standort war jedoch das sogenannte Haus Berge im Zentrum von Witten, wo heute noch ein kleines Museum alte Schmelzgefäße zeigt.
Heute leiten Friedrich Lohmann-Voß sowie Gunnar und Katja Lohmann-Hütte das Unternehmen als Geschäftsführende Gesellschafter in siebter Generation. Sie investieren überdurchschnittlich viel und setzen auf grundsolides vorausschauendes Wirtschaften. Energie- und Ressourceneffizienz sowie Umweltschutz spielen für die Unternehmer schon lange eine wichtige Rolle.
Raffinierte und energieeffiziente Formtechnik
Szenenwechsel in die Stahlgießerei. In der 15 Meter hohen Werkshalle ertönt eine Sirene, die den Produktionsanlauf ankündigt. Entfernt erinnert sie an das Martinshorn eines Rettungswagens. Gefertigt werden hier zum einen hitzebeständiger Guss, wie Gestelle, die Härtereien für die Wärmebehandlung brauchen sowie verschleißfeste Gussteile wie Wurfschaufeln für Schleuderradstrahlanlagen. In den Produktionshallen des Standorts arbeiten 92 Mitarbeiter in sechs Arbeitsbereichen: in der kleinen Handformerei, an der Rüttelpress- und einer kleinen automatischen Formanlage, in der Sandaufbereitung, im Croning-Bereich sowie an der hochmodernen Modulcast-Formanlage von 2016.
Letztere ist ein beachtliches Meisterwerk deutscher Gießereitechnik, gebaut von den Anlagenbauern Künkel-Wagner und Hubtex. Statt in die Breite geht die Anlage in die Höhe. Wie in einem Amazon-Warenlager stapeln sich fertig bestückte Formkästen in mehreren Lagen übereinander. Ein Hubtex-Regalbediengerät transportiert die rund vier Tonnen schweren Kästen mit drei Metern pro Sekunde an chaotisch festgelegte Plätze, wo nach dem Abguss auch die Verbrennungsgase abgesaugt werden. Die kompakte, rund zehn Meter breite, zwanzig Meter lange und rund fünf Meter hohe Anlage entspricht acht Reihen nebeneinander angeordneter Formkästen einer normalen Linie. Platz, der in Annen nicht zur Verfügung stand.
Die Reihenfolge beim Abgießen und Ausleeren erfolgt automatisch, ebenso die komplette Prozessdokumentation. Zudem ist Modulcast in Sachen Ergonomie, Sicherheit, Energieeffizienz und Ressourcenschonung auf dem neuesten Stand der Technik. 11 Millionen Euro betrug die Investitionssumme für die Anlage und die angeschlossene Sandaufbereitung.
Zukunftsfähige Ideen für die Produktion
Kutsch macht beim Rundgang auf zahlreiche clevere Ingenieurtricks aufmerksam, die Energie und Ressourcen einsparen. Dabei ist der Einsatz sensorgesteuerter LED im gesamten Werk, die sich selbsttätig aus- und anschalten, noch das Unspektakulärste. Die abgesaugten Abgase aus den Formkästen werden etwa in den Auspackturm geleitet und führen dort zu einem hohen Luftwechsel. Ergebnis: Das Einspeisen von 20 000 Kubikmetern Luft wird eingespart und es bildet sich darüber hinaus kein Kondenswasser, das die Anlage schädigen könnte.
Im Croning-Bereich, wo unter anderem die verschleißfesten Wurfschaufeln abgegossen werden, weist Kutsch auf eine Mittelschiene mit Absaugschlitzen zwischen den Gießplätzen hin. Beim Abguss erzeugt sie eine Querströmung über dem Teil, wodurch der umweltbelastende Qualm des verbrennenden Novolak-Binders abgesaugt wird. Entweicht dennoch zu viel Qualm in die Halle, registriert das ein Verschmutzungssensor, der dann die Hallenabsaugung auslöst. Noch raffinierter ist aber die anschließende Entschärfung dieser Schadstoffe in der Filteranlage, wo die abgesaugten Abgase der unterschiedlichen Gießverfahren zusammenkommen. Denn die bentonithaltigen Stäube der grünsandgebundenen Modulcast-Formen nehmen die Croning-Schad- und Geruchsstoffe auf. Auf ähnliche Art und Weise entfernt auch Katzenstreu Geruchsstoffe. Auch er enthält Bentonit.
„Wenn wir etwas bauen, überlegen wir uns, was in zehn Jahren sein könnte“, erklärt Kutsch den Erfindungsreichtum in der Stahlgießerei. Dieses vorausschauende und auf Nachhaltigkeit ausgelegte Denken findet sich auch in der Sandaufbereitung. Ähnlich wie eine Rolltreppe, die sich selbstständig abschaltet, wenn sie nicht benutzt wird, ruhen auch die Förderbänder für den Formstoff, wenn ein Modell gewechselt wird oder die Produktion aus anderen Gründen steht. „Ich wette darauf, dass in vielen Gießereien die Sandaufbereitung auch in der Pause im Standby-Modus weiterläuft“, glaubt Kutsch.
Kernstück des Abluftsystems ist die Filteranlage, ein grauer Blechturm, dessen gewaltige Absaugrohre sich über die Dächer des Werks wie Arme eines riesigen Kraken erstrecken. 800 000 Euro hat die Anlage gekostet und auch in ihr ist das langfristige Denken verankert, das Lohmann ausmacht. Für den Bedarf des Werks hätte eigentlich eine Anlage mit zwei Filterkammern ausgereicht. Doch Kutsch nahm lieber 80 000 Euro mehr in die Hand, damit das Filtersystem die doppelte Filterfläche hat. Hintergrund: Wird die Filterfläche vergrößert, nimmt die Verschmutzung ab. Dadurch braucht der Ventilator weniger Kraft, um die Luft durch die Anlage zu saugen. Folge: Zusammen mit einer bedarfsgerechten Steuerung wird 50 Prozent weniger Energie gegenüber dem herkömmlichen Einsatz verbraucht. Die Zu- und Abluftanlagen des Werks sind für jeweils 140 000 Kubikmeter Luft ausgelegt.
Klimabilanz und Kompensation
Nun könnte man meinen, dass angesichts des klimaneutralen Stroms die vielen weiteren Maßnahmen in der Stahlgießerei in Annen nicht notwendig sind. Doch weit gefehlt. Eine klimaneutrale Gießerei muss jede Emission und sogar den CO2-Footprint eingekaufter Einsatzstoffe angeben und möglichst vermeiden. Gelingt das nicht, bleibt nur noch die Kompensation. Darüber hinaus schafft der klimaneutrale Strom bei Lohmann zwar eine gute Ausgangsposition für das Familienunternehmen, er reicht aber nicht für beide Werke aus.
Damit die Klimabilanz in Annen stimmt, muss Gießereimanager Kutsch die Emissionen kompensieren, die er unter dem Strich nicht vermeiden kann. Lohmann arbeitet dafür mit einem zertifizierten Verein mit dem passenden Namen „Prima Klima“ zusammen. Aktuell wird ein Projekt in Uganda unterstützt, bei dem ein zerstörter Regenwald wieder aufgeforstet wird. Und wer es ernst meint, sollte es nicht dabei belassen, lediglich Kompensationzertifikate zu erwerben. Denn die Emissionstonnagen, die kompensiert werden, gehen von einer 50-jährigen Einbindungszeit von CO2 in den Baum aus. „Dann muss der Baum aber auch wirklich 50 Jahre stehen bleiben“, gibt Kutsch zu bedenken und ergänzt: „Es gibt bei Kompensationen keinerlei gesetzliche Regelungen, damit ist Tür und Tor für Missbrauch geöffnet.“
Schafft die Branche die Klimawende?
In 24 Jahren muss die deutsche Industrie klimaneutral sein. Schon deutlich vorher müssen die Emissionen stark reduziert werden. Die Transformation in dieser Zeit erscheint beherrschbar, aber wird die Branche die erforderlichen Maßnahmen auch finanzieren und umsetzen können? „Um Klimaneutralität zu erreichen, müssen sie investieren und neue Prozesse und Technologien einführen. Das erfordert Jahrzehnte. Mir macht Sorgen, dass die Gießerei-Industrie die Wende vielleicht erst in Jahren angeht und sie dann nicht mehr stemmen kann“, betont Kutsch.
Zwar ist durchaus wahrscheinlich, dass die Einsatzstoffe über kurz oder lang bereits klimaneutral eingekauft werden können, sodass die Klimabilanz vereinfacht und die Kosten für Klimaneutralität vielleicht gesenkt werden. Die deutschen Gießereien müssen Kutsch zufolge aber bald mit dem Weg in die Klimaneutralität starten: nicht zu schnell, um sich nicht finanziell zu überfordern, aber schnell genug, um rechtzeitig klimaneutral sein zu können. Mit regulatorischen Daumenschrauben rechnet er schon bald: „Ich bin sicher, dass die Klimabilanz, die wir erstellt haben, in zehn Jahren Pflicht ist“, so seine Überzeugung.
Bei Lohmann sieht man die Zukunft gelassen. Nach dem Einbruch durch die Coronakrise geht es jetzt im Stahlmarkt allmählich wieder aufwärts. Lohmann Guss hängt mit seinen Produkten der Erholung noch etwas hinterher, bald dürften Hauptprodukte wie Härtereigestelle und Wurfschaufeln aber wieder geordert werden. Kutsch verfolgt zahlreiche Pläne wie den Bau einer neuen Versandhalle und die Optimierung von Putzerei und Nachbearbeitung. Ein automatischer Pfannentransport ist angedacht, eine Robotertrennzelle soll bald in der Putzerei zum Einsatz kommen.
Nachdem das Thema Klimaneutralität in der Stahlgießerei nun klar umrissen ist, kann sich Kutsch, der nebenher auch noch Wirtschaftsingenieurwesen studiert hat, nun mit einem anderen wichtigen Problemgebiet in der Branche auseinandersetzen: der E-Mobilität, die in einigen Jahren dazu führen wird, dass ein wichtiges Marktsegment zusammenschmilzt. Schließlich sind auch alle großen Automobilbauer mit ihren werkseigenen Härtereien Kunden der Wittener Stahlgießer.
Mit einigen Jahren Vorlauf konzentriert sich Kutsch daher schon heute darauf, alternative Produktsegmente mit Marktpotenzial auszubauen. Auch das Stahlwerk in Herbede ist noch nicht klimaneutral. Die Crux dabei ist Scope 3, die eingekauften Einsatzstoffe und Leistungen. „Das wird ein richtig dickes Brett“, befürchtet Thorsten Kutsch. „Dafür sollten wir uns nicht zu viel Zeit lassen.“
VON ROBERT PITEREK, DÜSSELDORF
Schlagworte
AbsaugungAnlagenbauEnergieeffizienzGießereiGießerei-IndustrieGussteileInstandhaltungNachhaltigkeitProduktionPutzereiSicherheit