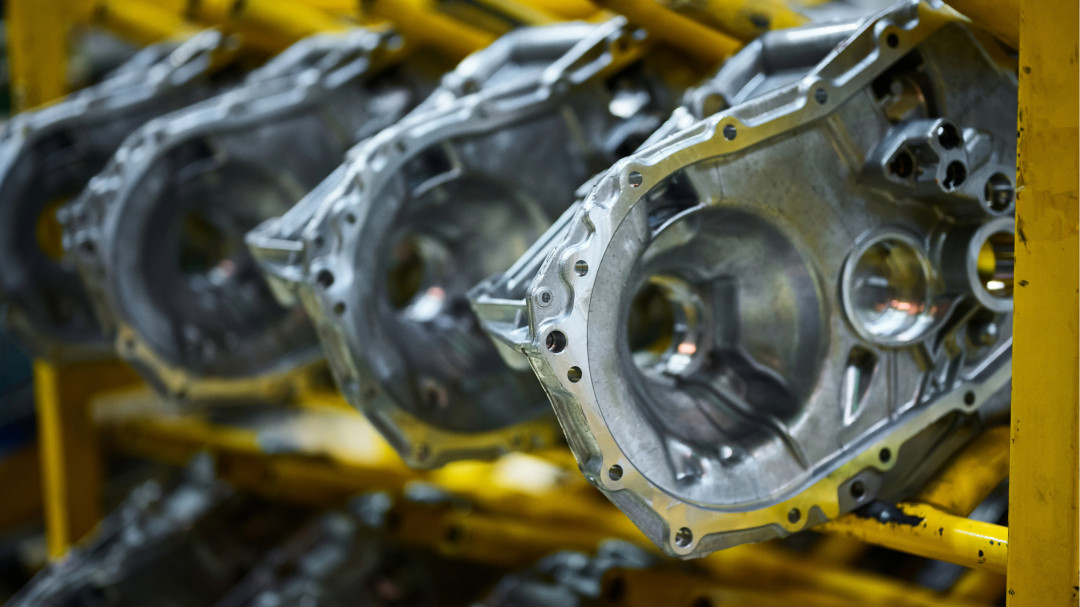
VON PROF. DR.-ING. KLAUS EIGENFELD
Die einzelnen Phasen der Entwicklung der Menschheit werden durch die jeweils genutzten hauptsächlichen Werkstoffe beschrieben. So entwickelte sich das menschliche Leben in der Steinzeit vor ungefähr 200.000 Jahren beginnend unter vornehmlicher Verwendung von Steinwerkzeugen und Holz hin zur Keramikzeit, in der bereits die künstlich hergestellten keramischen Massen in einem breiten Anwendungsgebiet zum Einsatz gelangten. Ein deutlicher Sprung gelang dann in der Kupfer- und Bronzezeit mit der Beherrschung metallischer Techniken und deren Nutzung im täglichen Leben. Die dritte große Periode in der einfachen zeitlichen Gliederung des Dreiperiodensystems ist die Eisenzeit. Sie reicht im südlichen Europa von etwa 800 v. Chr. bis um die Zeitenwende und im nördlichen Mitteleuropa von etwa 750 vor Christus bis ins 5. Jahrhundert nach Christus. Hieraus entwickelte sich dann die industrielle Revolution, eine umwälzende und bis heute andauernde Umgestaltung der wirtschaftlichen und sozialen Verhältnisse sowie der Arbeits- und Lebensbedingungen. Sie begann in der zweiten Hälfte des 18. Jahrhunderts und vor allem im 19. Jahrhundert, zunächst in England und breitete sich dann auf der gesamten Welt aus.
Dieser gewaltige Umschwung wurde neben den sozialen Veränderungen durch drei große Felder bestimmt:
- die Mechanisierung von händischer Arbeit durch Maschinen,
- die mechanische Energieerzeugung und Energieumwandlung vor allem durch die Dampfmaschine und den Einsatz von Elektrizität,
- die großtechnische Nutzung der Grundstoffe Kohle und Eisen.
Damit einhergehend folgte dann auch der Beginn einer neuen Mobilität. Der Ausbau des Eisenbahnnetzes, die Dampfschifffahrt, die beginnende individuelle Motorisierung und die Eroberung der dritten Dimension, der Luftfahrt, eröffneten neue weite Betätigungsfelder der Technik. Vorherrschend war dabei der Gedanke des Leichtbaues, da reduzierte Massen erheblich ökonomischer zu bewegen sind. Damit traten wir in ein „neues Zeitalter“ ein, in das Zeitalter der Leichtmetalle.
Leichtmetalle sind nun Elemente mit einer Dichte kleiner 5 Kg/dm3. Die vollständige Anzahl aller Leichtmetalle mit ihren Dichten in Kg/dm3 bei 20 °C zeigt die Tabelle 1.
Lithium 0,53 | Magnesium 1,74 | Aluminium 2,70 |
Kalium 0,86 | Beryllium 1,85 | Scandium 2,99 |
Natrium 0,97 | Francium 1,87 | Barium 3,65 |
Rubidium 1,53 | Caesium 1,90 | Yttrium 4,47 |
Calzium 1,54 | Strontium 2,63 | Titan 4,50 |
Tabelle 1: Dichte der Leichtmetalle in Kg/dm3
Von den gelisteten Elementen haben jedoch nur Magnesium, Aluminium, Titan und in geringem Maße Beryllium als eigenständige Konstruktionswerkstoffgruppen eine relevante Bedeutung. Betrachtet man die Entdeckungsgeschichten dieser Leichtmetalle, so fällt auf, dass alle in einem Zeitraum von 1754 bis 1798 entdeckt worden sind. Zur technischen Anwendung gelangten jedoch als Erste nur Aluminium und Magnesium, wobei durch politische und wirtschaftliche Gegebenheiten dem Werkstoff Magnesium – das deutsche Metall - in Deutschland eine besondere Rolle zukam.
Magnesium
Magnesium ist das leichteste Metall für technische konstruktive Anwendungen mit einer Dichte von 1,738 kg/dm³ bei 20 °C. Es ist ein chemisches Element mit dem Symbol Mg und der Ordnungszahl 12. Im Periodensystem der Elemente steht es in der zweiten Hauptgruppe und gehört damit zu den Erdalkalimetallen. Sein Masseanteil an der Erdhülle beträgt ungefähr 1,94 % und damit ist es eines der zehn häufigsten Elemente. Dies bedeutet, dass Magnesium in ausreichender Menge für die Zukunft zur Verfügung steht. Reines Magnesium hat nur eine sehr geringe Festigkeit und Härte. Daraus folgt, dass es für technische Anwendungen nur in Form von Legierungen nutzbar ist. Der Elastizitätsmodul beträgt ungefähr 45 Gigapascal, woraus folgt, dass bei auf Steifigkeit ausgelegten Bauteilen dies konstruktiv berücksichtigt werden muss. Eine Gewichtsreduktion gegenüber Aluminium im Verhältnis der Dichten ist nicht möglich; realistisch kann man von Gewichtseinsparungen in Höhe von ungefähr 20 % ausgehen. Magnesium besitzt eine hexagonale Kristallstruktur und hat demzufolge nur eine geringe Umformbarkeit bei Raumtemperatur wegen fehlender Gleitebenen. Bei technischen Umformprozessen müssen demzufolge die Werkstücke entsprechend vorgewärmt werden. Der Schmelzpunkt liegt bei 923 K (650 °C) und der Siedepunkt bei 1383 K (1110 °C). Der niedrige Schmelzpunkt sowie die nicht vorhandene Aggressivität gegenüber eisenbasierten Werkstoffen erlaubt es, Magnesium günstig in Eisentiegeln zu schmelzen und in Dauerformen zu vergießen. Die Wärmeleitfähigkeit liegt bei 160 W/mK und damit deutlich niedriger als die von Aluminium mit 235 W/mK. Dies bedeutet, dass Magnesiumlegierungen nicht für thermisch belastete Bauteile wie zum Beispiel Zylinderköpfe von Verbrennungsmotoren genutzt werden können. Analog verhält es sich mit der elektrischen Leitfähigkeit. Magnesium hat ein Normalpotenzial von -2,372 V; es ist also sehr elektronegativ (Mg2+ + 2e- Mg). An Luft überzieht sich Magnesium mit einer Oxidschicht, die im Gegensatz zum Aluminium nicht vollständig deckend ist. Eine hohe Korrosionsbeständigkeit ist also nicht gegeben. Für viele Anwendungsfälle, besonders in korrosiver Umgebung, ist demzufolge ein zusätzlicher Oberflächenschutz notwendig.
Entdeckung
Magnesium war in Form seiner Verbindungen bereits im Altertum bekannt. Der Name Magnesium kommt wahrscheinlich aus dem griechischen und bedeutet entweder Magnetstein oder Magnisia nach einem regionalen Gebiet in Griechenland oder Magnesia nach einer Stadt auf dem Gebiet der heutigen Türkei. Als Magnesia alba bezeichnete man üblicherweise Magnesiumcarbonat und mit Magnesia das Magnesiumoxid.
Es war dann der schottische Physiker und Chemiker namens Joseph Black (1728-1799), der diese Verbindungen grundlegend untersuchte. 1755 beschrieb er in seiner Dissertationsschrift „De humore acido a cibis orto et Magnesia alba“ den Unterschied zwischen Kalziumcarbonat und Magnesiumcarbonat, Magnesia alba. Er fasste dies als Carbonat eines bisher unbekannten Elementes auf. Aus diesem Grund können wir Black als den ersten Entdecker des Magnesiums bezeichnen, obwohl er es selber nie in metallischer Form hergestellt hatte. Ein halbes Jahrhundert später, 1808, erzeugte Sir Humphrey Davy (1778-1829), Magnesium durch Elektrolyse von Magnesiumhydroxid. Er stellte es jedoch nicht in reiner Form dar sondern als Amalgam, da er in seinem Prozess Quecksilber benutzte. Erst 1828 erhitzte der französische Apotheker und Chemiker Antoine Bussy (1794 – 1882), trockenes Magnesiumchlorid mit Kalium als Reduktionsmittel und stellte geringe Mengen von reinem Magnesium dar. In dem zeitlichen Ablauf erzeugte dann der englische Chemiker Michael Faraday (1791-1867), Magnesium durch Elektrolyse von geschmolzenem Magnesiumchlorid. Unter Zugrundelegung dieser Arbeiten entwickelte daraufhin der deutsche Chemiker Robert Wilhelm Bunsen (1811-1899), der vor allem durch die Entwicklung des Bunsenbrenners bekannt wurde, in den Jahren 1840-1860 Elektrolysezellen für die Darstellung neuer Elemente. Dies betraf neben dem Magnesium vor allem auch zahlreiche andere Metalle wie Chrom Aluminium, Mangan, Natrium, Barium, Kalzium und Lithium in Elementarform. Zusammen mit Gustav Robert Kirchhoff entdeckte er zusätzlich 1861 die beiden Leichtmetalle Cäsium und Rubidium. Auf diesen gesamthaften Arbeiten aufbauend begann dann die Entwicklung der deutschen Magnesium-Industrie, die im internationalen Vergleich über lange Jahre hin bis Ende des Zweiten Welt Krieges die absolut führende Stellung in der Welt einnehmen sollte.
Industrielle Produktion
Wie die meisten Metalle, außer den Edelmetallen, kommt Magnesium, besonders auch aufgrund seiner Elektronegativität, in der Natur nicht gediegen vor. Als Mineral tritt es bevorzugt in Form von Carbonaten, Silicaten, Chloriden und Sulfaten auf. In der Art von Dolomit bildet ein magnesiumhaltiges Mineral sogar ein ganzes Gebirge, die Dolomiten in Italien. Die wichtigsten Mineralien für die Magnesiumproduktion sind nun Dolomit CaMg(CO3)2, Magnesit (Bitterspat) MgCO3, Olivin (Mg, Fe)2 [SiO4], Enstatit MgSiO3 und Kieserit MgSO4 · H2O. Weitere Quellen sind zum Beispiel Serpentin Mg3[Si2O5] (OH)4, Spinell MgAl2O4 und Carnallit KMgCl3 · 6 H2O. Neben seinem Entdeckungsrevier Staßfurt in Sachsen-Anhalt fand man dieses Mineral in Deutschland unter anderem in den Kalisalzbergwerken von Heringen und Philippsthal und im hessischen Werratal. Einige von diesen Lagerstätten wurden dann Standorte von Magnesiumhütten, wie später erläutert wird.
Ein weiteres, fast unerschöpfliches Reservoir von Magnesium ist salzhaltiges Wasser, beispielsweise das klassische Meerwasser. In diesem ist Magnesium mit mehr als 1 Kg/m3 enthalten. Konkret wird diese Situation aber an anderer Stelle genutzt. Dead Sea Magnesium Ltd. am Toten Meer in Israel verwendete das hochsalzhaltige Wasser für die Gewinnung von Bromsalzen für fotographische und pharmazeutische Zwecke. Übrig blieben große Aufschüttungen magnesiumhaltiger Salze bzw. Mineralien wie Carnallit. Mit diesen begann dann die Magnesiumproduktion, die heute von hoch salzhaltigen Laugen gespeist wird. Prinzipiell werden zwei unterschiedliche Prozesstypen bei der Darstellung metallischen Magnesiums hauptsächlich genutzt:
- Schmelzflusselektrolyse
- thermische Reduktion
Durch Schmelzflusselektrolyse von geschmolzenem Magnesiumchlorid in Downs-Zellen: Downs-Zellen bestehen aus großen eisernen Trögen, die von unten beheizt werden. Als Anoden dienen von oben eingelassene Graphitstäbe, die an den Spitzen von einer ringförmigen Kathode umgeben sind. Das metallische Magnesium sammelt sich auf der Salzschmelze und wird abgeschöpft. Das entstehende Chlorgas sammelt sich im oberen Teil der Zelle und wird wieder verwendet zur Herstellung von Magnesiumchlorid aus Magnesiumoxid. Zur Schmelzpunkterniedrigung des Magnesiumchlorids wird der Salzschmelze Calcium- und Natriumchlorid zugesetzt.
Zu beachten ist, dass die Elektrolyse zur Erzeugung metallischen Magnesiums sehr energieintensiv ist. So müssen (heute) ca. 35 kWh für die Produktion von 1 Kg Magnesium aufgewendet werden. Bei der Substitution von Aluminiumteilen ist jedoch zu berücksichtigen, dass, bedingt durch die technologischen Eigenschaften, ca. 20% Gewicht eingespart werden können und so der Energieaufwand relativiert wird.
Die Produktion in kleinem Maßstab begann in Deutschland bei der Aluminium und Magnesiumfabrik A.G. in Hemelingen bei Bremen im Jahre 1886. 1893 errichteten die Elektro-Chemischen Werke GmbH, Berlin eine chemische Fabrik zur Herstellung von Ätznatron und Chlorkalk. Im selben Jahr beschloss die Chemische Fabrik Elektron AG, Frankfurt / a. M., eine Tochtergesellschaft der Chemischen Fabrik Griesheim, eine Niederlassung in Bitterfeld zu gründen; beide fusionierten dann 1894. Im Jahre 1925 entstand daraus der IG Farbenkonzern und damit nahm die Magnesiumproduktion einen rasanten Anstieg. Im Jahr 1944 betrug kriegsbedingt die Belegschaft ca. 16.000 Mitarbeiter.
Parallel dazu errichtete die Wintershall A.G. eine Magnesiumproduktion in Heringen an der Werra, die 1935 den Betrieb aufnahm. Markenname wurde MAGNEWIN: MAGNEsium aus WINtershall. Hier wurden auch weiterführende Bearbeitungen wie Schmieden und Strangpressen für Profile durchgeführt.
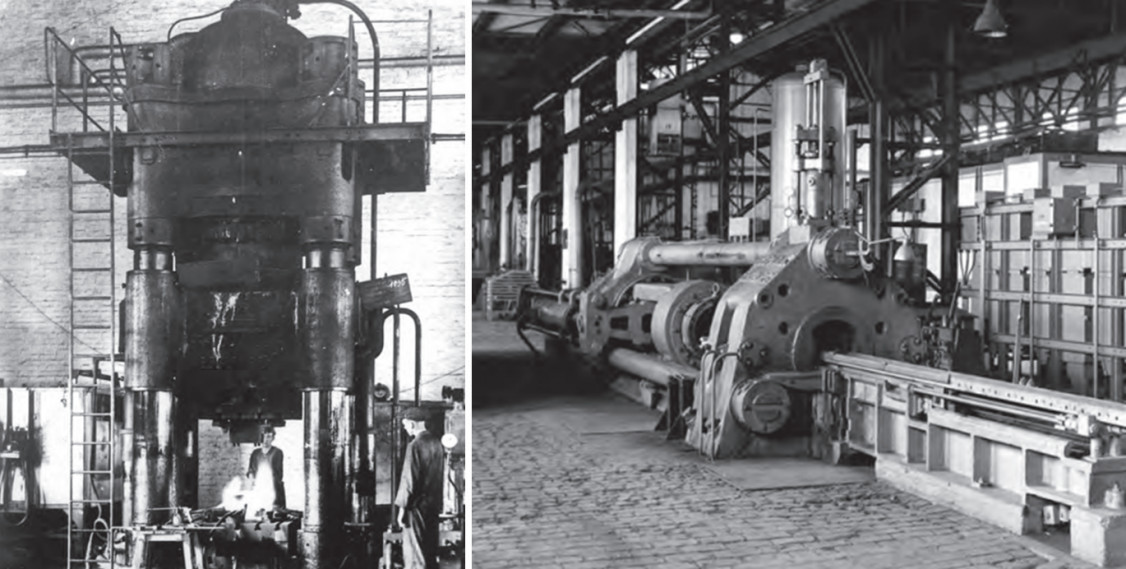
Bedingt durch die anlaufende Produktion des VW Käfers mit Magnesium Motor- und Getriebegehäuse entstand 1938 das damalig zweitgrößte Magnesiumwerk von Europa, die Societá anonima italiana magnesio SAIM in Bozen. Auf elektrolytischem Weg mit reichlich vorhandenem Strom von Montecatini wurden in Kriegszeiten 8000 Jahrestonnen und in den 1960er-Jahren 35.000 Jahrestonnen, vornehmlich für die VW AG, gefertigt. 1991 ging das Unternehmen in Insolvenz. Aber auch außerhalb Deutschlands wurden Magnesiumaktivitäten initiiert. So wurde 1938 Magnesium Electron Ltd. von der I.G. Farbenindustrie AG in Swinton bei Manchester gegründet. Heute werden hauptsächlich Sonderlegierungen, besonders auch hochfeste und hochwarmfeste, geliefert.
Kriegsbedingt stieg die Nachfrage nach Magnesium und nach weiteren Produktionsstätten. Ab 1940 entstand deshalb unter Leitung der I.G. Farbenindustrie A.G. ein bereits von Norsk Hydro begonnener Ausbau der Leichtmetallproduktion, insbesondere der von Magnesium aus Meerwasser (Gehalt ~ 1,30 – 1,35 Kg/dm3). Die Produktion in Porsgrunn kam jedoch nicht in Gang, da die fast fertigen Anlagen durch einen Luftangriff der Royal Airforce im Juli 1943 fast vollständig zerstört wurden und ein damaliger Wiederaufbau nicht erfolgte. Dieser fand erst nach dem Krieg durch Norsk Hydro statt.
Mit der zunehmenden Primärproduktion folgte aber auch der Ausbau der weiterführenden Produktionsschritten. Beispielhaft sei hier die Firma Edmund Becker & Co. A.G., Metallgussgesellschaft MEGU in Leipzig W 35 genannt, die ab ca. 1923 die größte Magnesiumgießerei weltweit mit einem breit aufgestellten Produktsortiment war und sich auch mit umfangreichen Magnesiumbroschüren sowie Veranstaltungs- und Messeauftritten darstellte. Doch auch die mechanische Fertigung stand dem Volumen der vorhergehenden Produktion nicht nach. Mahle, ab 1924 Elektronmetall GmbH, ab 1938 MAHLE KG, Werk Stuttgart Bad Cannstatt, widmete sich neben der Kolbenproduktion auch der Serienproduktion von Magnesium Luftfahrt-Komponenten, in der Kriegszeit auch unter Nutzung von Zwangsarbeitern.
Produkte
Die Eigenschaften der Magnesiumlegierungen sind für eine große Anzahl von Anwendungen optimal geeignet. Die geringe Dichte bietet sich für bewegte Massen hervorragend an. So sind handgeführte Werkzeugmaschinen, die Verkehrstechnik und besonders der Flugzeugbau Hauptanwendungsgebiete. Die gute Dämpfungseigenschaft, besonders bei grobkörnigem Sandguss, ähnlich Gusseisen mit Lamellengraphit, eröffnete Anwendungsgebiete bei Werkzeugmaschinenbetten. Das exzellente Verhalten im Druckguss gepaart mit einer gegenüber Aluminium deutlich höheren Standzeit der Form eröffnete dem Werkstoff dann breite Anwendungsfelder.
Maschinenbau
Beispiele für handgeführte Maschinen sind Bohrmaschinen, Winkelschleifer, Handkreissägen, Nibbler und viele mehr. Da es früher die Robotertechnik noch nicht gab. mussten auch Serienabläufe wie das Punktschweißen händisch durchgeführt werden. Auch hier war jedes Gramm eingespartes Gewicht hilfreich und deshalb wurde der Elektronarm für eine Punktschweißzange eingesetzt. Aber auch bei großen Werkzeugmaschinen wurde Magnesiumguss eingesetzt. Die Hettner Radialbohrmaschine besaß ein Getriebegehäuse mit Spindellagerung aus diesem Material. Ein weiteres herausragendes Beispiel ist das Maschinenbett und der Spindelstock einer Boehringer Drehmaschine, bei der unter anderem das hohe Dämpfungsvermögen von Magnesium eine Rolle spielte. Darüber hinaus sprach das geringere Gewicht der Maschine auch für eine einfachere Transportmöglichkeit und somit für den Einsatz in mobilen Werkstätten im militärischen Bereich. Bei der Bodenverdichtung, besonders für den Straßenbau kamen Explosionsrammen, sogenannte „Delmag Frösche“, mit 100, 250 und 500 Kg Gewicht zum Einsatz. Bei diesen Geräten waren Kühlmäntel und Zylinderköpfe aus Magnesium Sandguss. Komponenten für Hollerithmaschinen und Spinnereimaschinen bestanden ebenfalls aus Magnesiumguss. Die Körper der Hollerith-Maschinen besaßen Grundplatte und Maschinenfüße aus Elektron Sandguss, während die Versteifungsstützen aus gepresstem Elektronblech bestanden. Da gerade Spinnereimaschinen hohe Arbeitsgeschwindigkeiten besitzen, ist die Reduzierung des Gewichtes bewegter Massen dringend geboten. Bei Gillspinnmaschinen (Trockenspinnstühlen) der Firma Haas u. Kellhofer in Singen kamen zum Beispiel 1938 Haubenflügel aus Elektron Kokillenguss zum Einsatz. Ein nicht ganz bekanntes Einsatzgebiet von Elektronguss waren Umformgesenke. Diese kamen beim Umformen von Stahlblech, besonders aber von Aluminiumblech zum Einsatz. Oftmals waren dabei die Gegenstücke aus Hartgummi. Hauptabnehmer war die Flugzeugindustrie, da hier die Stückzahlen überschaubar waren. Nach Einstellung des Produktionsmusters wurden die Gesenke eingeschmolzen und zu einem Neuen gegossen.
Verkehrstechnik
Die rasch zunehmende Mobilität in Deutschland fragte nach seriengeeigneten Fortbewegungsmitteln, die außerdem kostengünstig und mit vorhandenen Ressourcen gefertigt werden konnten. Hier bot sich naturgemäß der Magnesiumguss mit den Möglichkeiten der Funktionsintegration gut an. Dazu kam, dass Magnesium im eigenen Land hergestellt wurde. Mit diesen Voraussetzungen wurden dann die unterschiedlichsten Projekte, teilweise mit hinterfragenswerten Konzeptideen, angegangen. Ein derartiges Projekt war das „Einguss-Zweiradauto“ der MOTAG, Leipzig 1923/24. Das mit Zweizylinder-ohv-Motoren von 500 – 800 ccm Hubraum auf der Auto- und Motorradaustellung in Berlin 1923 vorgestellte Fahrzeug wurde wahlweise luft- oder wassergekühlt angeboten. Motor- und Getriebegehäuse, der mehrteilige Rahmen mit integriertem Benzintank, Kotflügel und diverse andere Teile waren aus Magnesiumguss mit einem Gewicht von ungefähr 43 Kg. Über Verkaufserfolge ist nichts bekannt. Wenige Jahre später, 1926, produzierten die ADLER - Werke vorm. H. Kleyer A.G., Frankfurt am Main, dann die Automodelle Standard 6 und 1928 Standard 8 mit sehr hohem Magnesium Gussanteil.
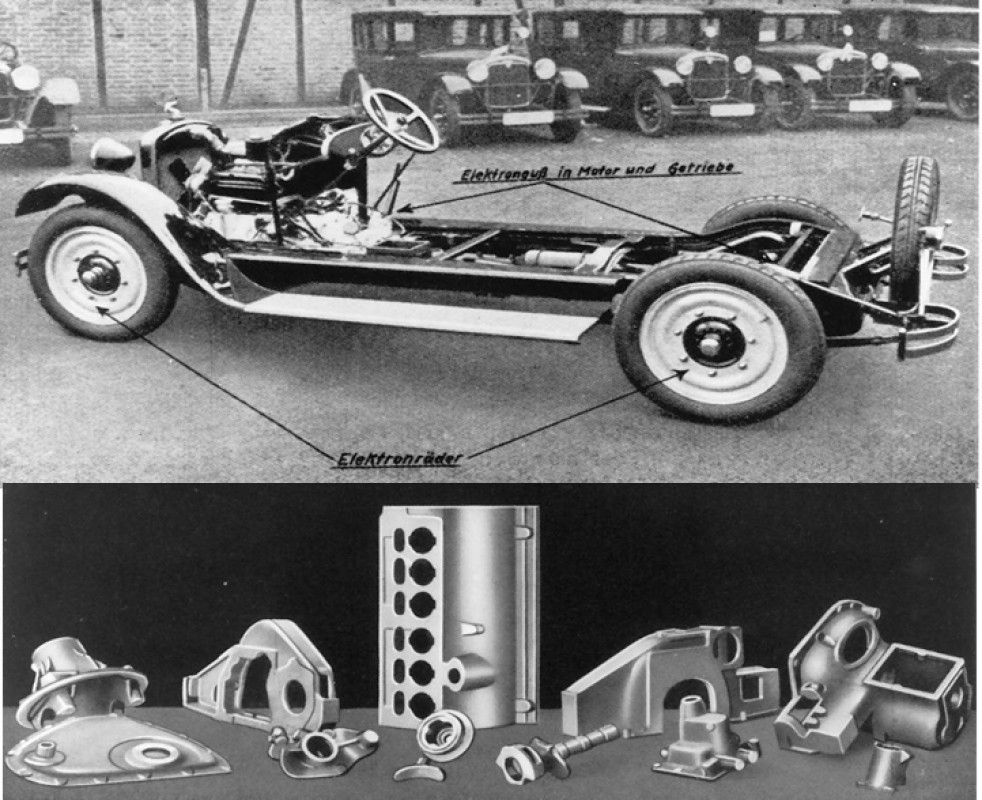
Dabei konnte sich ADLER auf Erfahrungen im Luftfahrtbereich stützen, wie wir später noch sehen werden. Die beiden Fahrzeugtypen wiesen als Sandgussteile die Scheibenräder, Kurbelgehäuse, Kettenkasten und Kettenkastendeckel, Schwungradgehäuse, Getriebegehäuse mit diversen Deckeln sowie das Hinterachsgetriebegehäuse und im Druckguss, damals Spritzguss genannt, Lager, Stösselführungen und Deckel auf. Dabei betrug das Gewicht der Magnesiumteile beim 6-Zylinder 73,8 Kg und beim 8-Zylinder 86,8 Kg. Vom 6-Zylinder wurden insgesamt knapp 30.000 Stück verkauft. Einen neuen Weg ging auch ein anderer Motorenhersteller, der 1927 einen wassergekühlten Motorblock aus Magnesiumguss vorstellte.
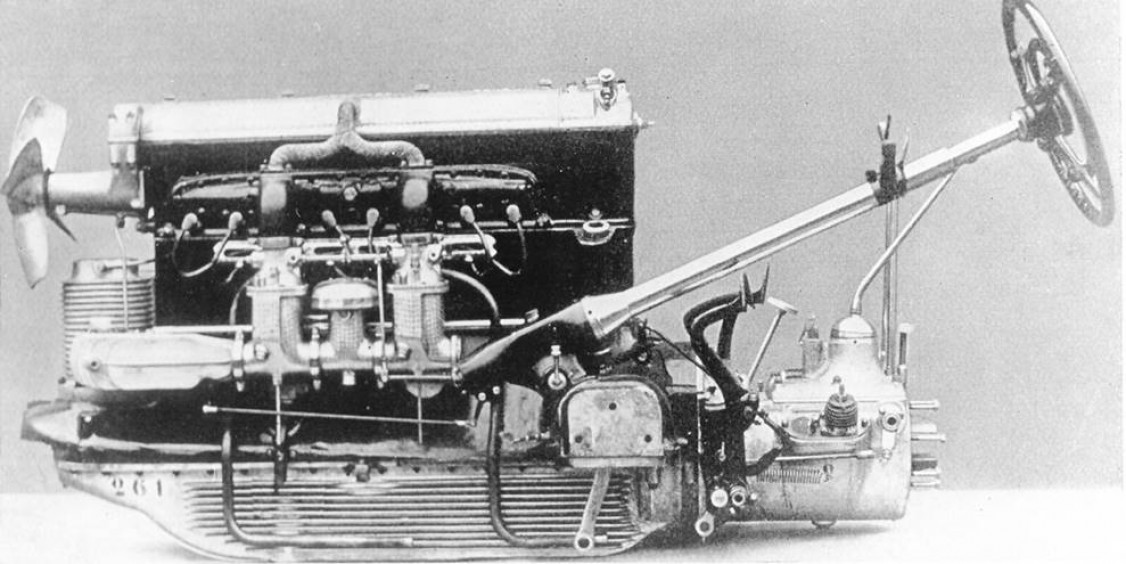
Um Korrosionserscheinungen zu vermeiden, wurde dem Kühlwasser Natriumbichromat zugesetzt. Aber auch mechanisch und thermisch höchstbelastete Motorenkomponenten wurden in Magnesium ausgeführt. Die Mahle GmbH, 1924 in Elektronmetall GmbH umbenannt, warb auf dem Plakat ebenfalls aus diesem Jahr für Magnesiumkolben im Serienmotorenbau. Bereits früher, 1921, stellten Magnesiumkolben ihre Leistungsfähigkeit unter Beweis, indem sie bei den 500 Meilen von Indianapolis die Plätze 1, 3 und 9 mit Dowmetal-Kolben (USA) belegten. Ein weiteres Magnesium Highlight war der Versuchswagen Bugatti Typ 57 Aerolithe auf dem Pariser Autosalon 1935, dessen Karosserie komplett aus Magnesiumblech bestand. Da es damals keine geeigneten Schweißverfahren für verzugsfreie Schweißnähte an dünnen Blechen gab, wurden die Trennstellen gefalzt und genietet, was gut an Kotflügeln und auf dem Dach zu erkennen ist. In Serie produziert wurden dagegen die Omnibusanhänger der Deutschen Reichspost, deren Struktur komplett aus Magnesium bestand. Dabei wurden gepresste Magnesiumprofile durch tiefgezogene Magnesium-Blechknoten verbunden und stellten so eine frühe Art von „Spaceframe“ dar. Dieser wurde mit unter Vorwärmtemperatur tiefgezogenem Magnesiumblech beplankt und dies übernahm gleichzeitig einen Teil der Strukturfestigkeit. Vier Personen konnten die gesamte Struktur bequem heben.
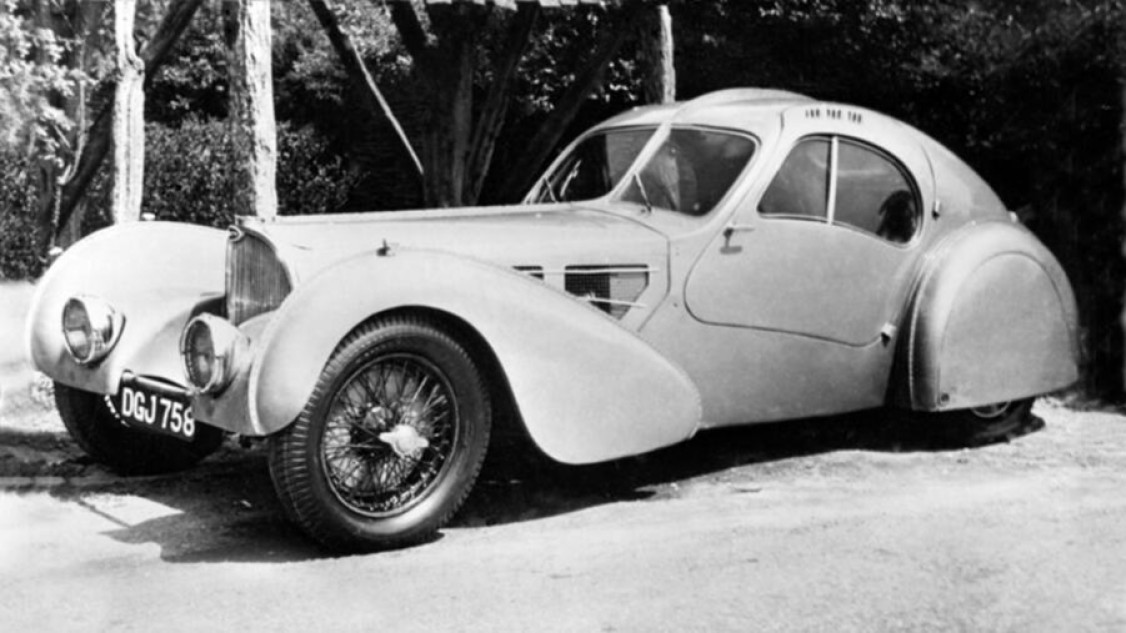
Im Hochleistungsbereich gab es ebenso zahlreiche Beispiele von Magnesiumguss. So besaß das DKW Ladepumpen Rennmotorrad von 1939 mit 350 ccm 2-Zylinder 2-Takt Doppelkolbenmotor Kurbelgehäuse, Zylinder und Zylinderkopf diverse Deckel sowie Radnaben aus Elektronguss. Der Motor leistete 32 PS bei 6250 U/min. und gewann 1939 die Europameisterschaft. Ebenfalls extrem erfolgreich war die BMW Kompressor Rennmaschine mit 500 ccm von 1939. Hier waren Motorgehäuse, Getriebegehäuse, Kompressorgehäuse, Zylinderkopfdeckel, Radnaben und etliche kleinere Teile aus Magnesiumguss. Der Motor leistete bei Straßenrennen ca. 60 PS bei 7000 U/min, während er bei Rekordversuchen 108 PS bei 8000 U/min lieferte. Mit diesem Motorrad gelang der Gewinn des 500 ccm Rennens 1939 auf der Isle of Man durch Schorsch Meier als erstem Nichtbriten. BMW setzte auch im Automobilsport auf Magnesium. Der BMW 328 „Mille Miglia“ von 1940 hatte Magnesiumkolben und Magnesium Bremsankerplatten.
Einen großen Sprung bei der Verbreitung von Magnesiumguss brachte der Druckguss. Hier spielte das gute Fließvermögen, der gegenüber von Aluminium-Gusslegierungen geringere Wärmeinhalt und die Resistenz des Formstahles gegen den Magnesiumangriff eine überzeugende Rolle. Darüber hinaus unterstützte natürlich die fortschreitende Technik der Druckgießmaschinen deren weiten Einsatz. Das Bild zeigt eine Warmkammer-Druckgießmaschine Bauart Mahle und deren Prinzipaufbau. Magnesium-Druckgussteile für den Automobilbau der Jahre 1934 – 1940 wie die Lenkrad-Innenstruktur, Lenkspindelgehäuse, Getriebedeckel, Stößelführungen und sogar Wasserpumpenräder wurden in großen Stückzahlen gefertigt. Weitere Druckgusserzeugnisse sind im Kapitel Magnesium im täglichen Leben aufgeführt.
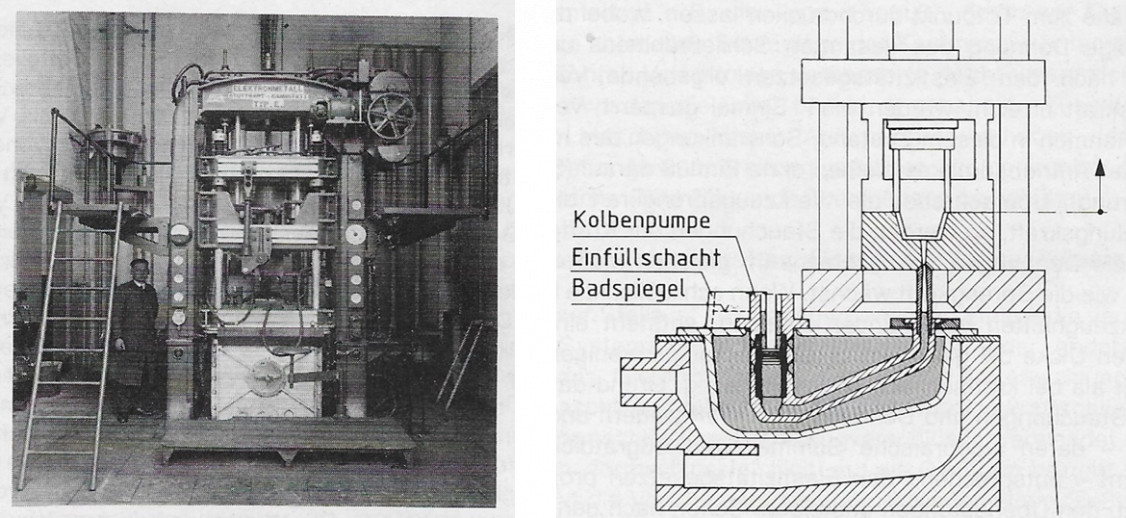
Luftfahrt
Die beginnende Luftfahrt hatte naturgemäß hohe Anforderungen an leichte leistungsfähige Antriebsquellen und leichte hochfeste Konstruktionselemente. Da es anfangs des 19. Jahrhunderts noch keine dafür geeigneten Aluminiumlegierungen gab, eröffneten sich für Magnesium- Knet- und Gusslegierungen breite Anwendungsfelder. Die Verfügbarkeit des Werkstoffes und die intensive Forschungs- und Entwicklungstätigkeiten in Deutschland führten dann dazu, dass militärische Flugzeuge bei Beginn des zweiten Weltkrieges durch ihr geringeres Gewicht bei identischer Motorleistung den Alliierten überlegen waren.
Die erste Entwicklung im Bereich der Luftfahrt ging von den ADLER Werken vorm. Heinrich Kleyer A.G. in Frankfurt/Main aus. Im Jahre 1909 präsentierten sie einen 6-Zylinder Luftschiffmotor mit 75 PS Leistung und einem Kurbelgehäuse aus Magnesiumguss auf der Internationalen Luftfahrtausstellung ILA in Berlin.
Die Entwicklung der Flugmotoren ging rasant voran. Bedeutenden Anteil daran hatten auch die Bayerischen Motoren Werke A.G. in München, deren Logo einen stilisierten rotierenden Propeller darstellt. 1926 entwickelten sie einen 24,4 Liter 6-zylinder Reihenmotor mit 4 Ventilen pro Zylinder, einem durchgehenden Zylinderkopf und Zylinderblock in Aluminiumguss; Kurbelgehäuse und Nockenwellengehäuse waren auch in Elektronguss erhältlich. Der Motor entwickelte über 320 PS und wurde neben Flugzeugen auch versuchsweise in Panzerfahrzeuge eingebaut. Weitere Beispiele für die fortschreitende Entwicklung sind Motoren der Hersteller Argus Motoren Gesellschaft mbH in Berlin-Reinickendorf. Der Argus As 410 (1933) ist ein luftgekühlter hängender (Kurbelwelle oben) 90° V-8 Motor mit Kurbelgehäuse und Anbauteilen aus Elektronguss. Er leistete bei 12,7 Liter Hubraum als Startleistung 240 PS bei 2000 U/min. Vom Typ AS 410 wurden insgesamt 28.000 Stück hergestellt. Er wurde unter anderen in der Schweizer Pilatus P2 eingesetzt. Ein kleinerer Motor mit Elektron Kurbelgehäuse ist der HM 504 4-Zylinder hängend luftgekühlt der Hirth Motoren GmbH Stuttgart-Zuffenhausen 1934 mit 4 Liter Hubraum und Startleistung 105 PS bei 2350 U/min. Er kam bei kleineren Sportflugzeugen zum Einsatz und wurde ca. 6.000 mal gebaut. Ein Highlight das Magnesiumeinsatzes im Flugmotorenbau ist das Kommandogerät zur Einhebel-Steuerung des BMW 801 14-Zylinder Doppelsternmotores von 1940. Das Kommandogerät stellte automatisch als „mechanischer Analogrechner“ alle motorrelevanten Parameter wie z. B. Zündzeitpunkt, Drosselklappenöffnung, Einspritzmenge und Luftschraubenstellung, Flughöhe und Motortemperatur korrelierend zu dem vom Piloten mit dem „Leistungswählhebel“ vorgegebenen Ladedruck oder Drehzahl ein und entlastete damit den Piloten. Das Gehäuse bestand aus Magnesiumguss mit dünnen (6 mm) vorgegossenen Druckölkanälen in der Gehäusekontur, gefertigt durch geschlichtete mehrlagige Federkerne. Aber nicht nur im Motorenbau wurde Magnesium verwendet. Ein exzellentes Beispiel für Magnesium Blech und Profilen in der Struktur ist das Experimentalflugzeug L 81 „Electra“ der Albatros Flugzeugwerke GmbH Berlin Johannistal von 1932. Mit Anleihen des Konstruktionsprinzipes des Zeppelin wurde die Struktur aus Magnesiumrohren und -Profilen und, größtenteils gelochten, Magnesiumblech gefertigt. Beispielhaft ist die Flügelstruktur der L 81 Electra in Abbildung 39 gezeigt. Höhen- und Seitenruder folgten dem gleichen Konstruktionsprinzip. Die Außenhaut war eine lackierte Stoffbespannung. Weitere Magnesiumkomponenten waren Motorträger, Fahrwerk, Federbeine, Treibstofftank und Sitzgestell. Als Motor kam der bereits vorgestellte BMW Va zum Einsatz. Im zivilen Flugzeugbau wurden dann in den folgenden Jahren viele Komponenten in Elektron in Serie gefertigt wie beispielsweise Räder und Bremsen für diverse Flugzeugtypen. Im Gegensatz zu heute wurden damals Werkstoffnutzungen auch werbewirksam präsentiert, wie die Werbung für Magnesiumteile der Focke-Wulf „Condor“ durch Wintershall „Magnewin“ beweist. Mit der abgebildeten Focke Wulf Condor wurden regelmäßige Passagierflüge Berlin – New York absolviert.
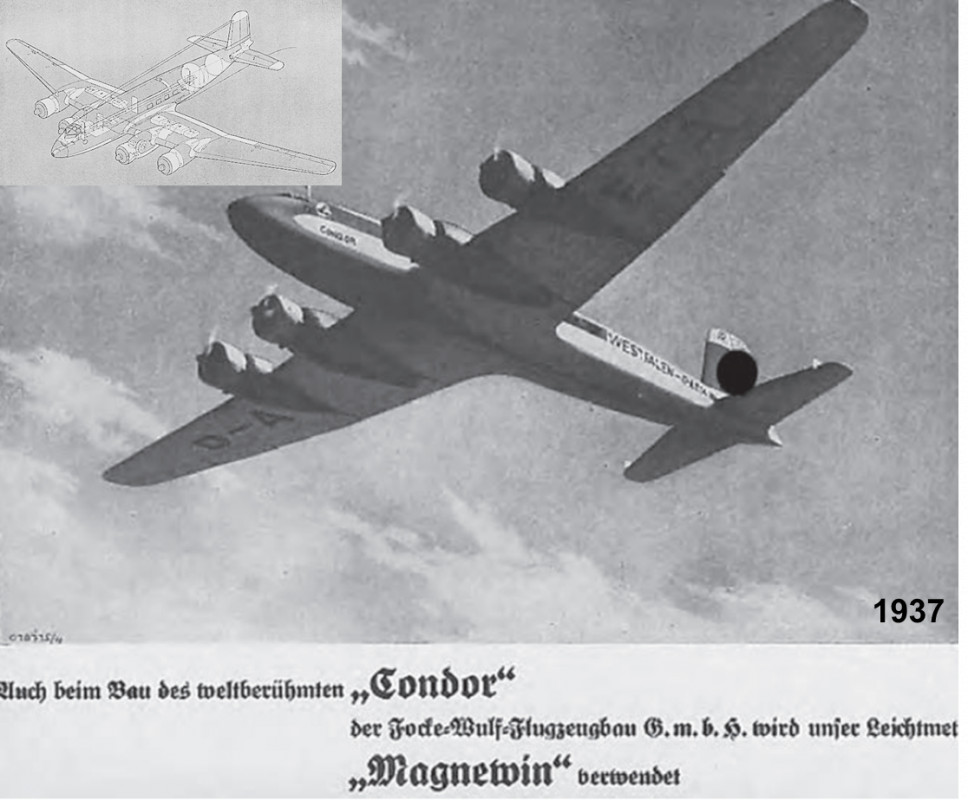
Alltag
Doch nicht nur in der Mobilität bewährten sich Magnesiumteile. Auch im täglichen Leben fand sich eine große Anzahl gegossener oder geformter Elektron-Komponenten. Als Beispiel sei die Medizintechnik genannt. Die Firma Electr.-Ges. „Sanitas“ in Berlin N 24, Friedrichstr. 131 d fertigte medizinische Apparate unter Zuhilfenahme von Magnesiumguss. Das Bild zeigt ein Röntgengerät mit dem Gestell und Armen aus Guss. Darüber hinaus wurden Komponenten für Zahnarztstühle, Zahnarztarbeitsplätze, Verstellbetten und etliche weitere medizinische Teile gegossen. Ebenfalls aus Magnesium Sandguss ist der Buchdeckel aus England für eine Loseblattsammlung. Im Gegensatz dazu eroberten die in hohen Stückzahlen kostengünstig gefertigten Druckgussteile ab Mitte der 1930er Jahre das ganz alltägliche Leben. Ein Beispiel hierzu ist der Zeiss Feldstecher mit seiner Magnesium-Gussstruktur. Weitere Teile seien hier beispielhaft aufgezählt: Fahrkartendrucker, Radiogehäuse, Kameragehäuse, Walze und Klischee für Fahrscheindrucker, Elektromotorgehäuse für Haushaltsmaschinen, Schreibmaschinengestelle.
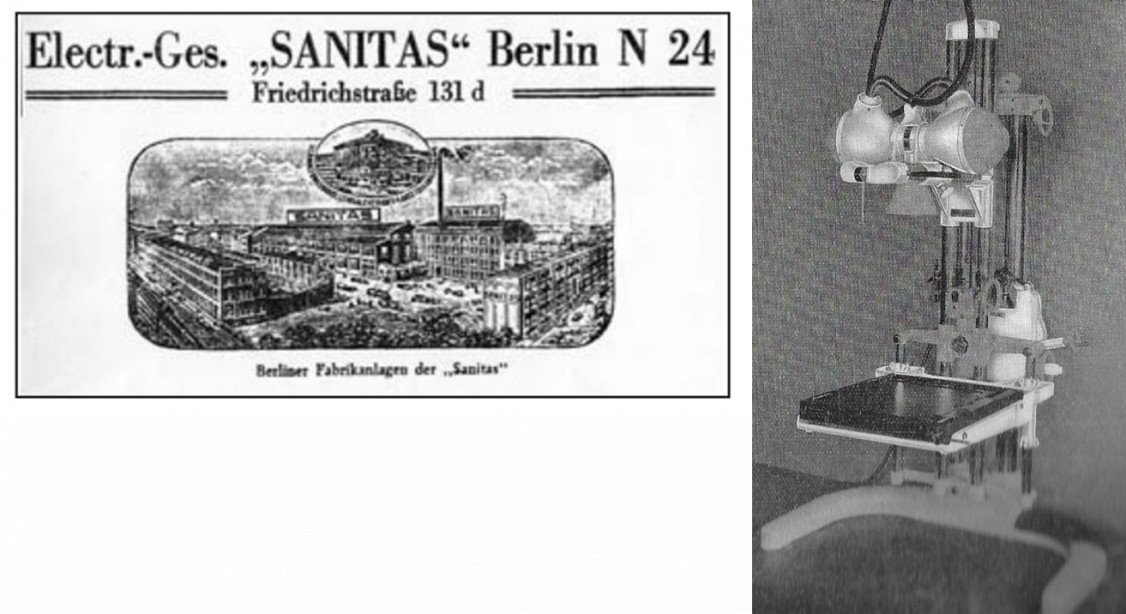
Literatur
[1] WISSENSCHAFTLICH-TECHNISCHE MITTEILUNGSBLÄTTER der Firmen EDMUND BECKER & CO. A. G. und METALLGUSSGESELLSCHAFT mbH Leipzig W 35.
[2] ELEKTRON: I. G. FARBENINDUSTRIE AKTIENGESELLSCHAFT ABTEILUNG ELEKTRONMETALL, Bitterfeld
ELEKTRON – NACHRICHTEN: I.G. Farbenindustrie Aktiengesellschaft, Abteilung Elektronmetall, EN 1 – EN 21, 1935 – 1944. In dieser Schriftenreihe, die den Magnesiumabnehmern zur Verfügung gestellt wurde, gab es Anweisungen und Ratschläge für die Bereiche Schmelzen und Gießen, Legierungen, Wärmebehandlung, Formstoff und Formherstellung, Betriebsvorschriften und Unfallverhütungsvorschriften für Elektron-Gießereien
[3] Werkstoff MAGNESIUM, nach Vorträgen der Magnesiumtagungen Berlin und Frankfurt a. M. 1938 und 1939, VDI-Verlag GmbH, Berlin NW 7
[4] Von Anton Doppelfeld wurde im Herbst 1939 das Buch „DER REICHSVERBAND DER DEUTSCHEN LUFTFAHRT-INDUSTRIE“ bearbeitet und im WIKING VERLAG GMBH BERLIN W 35 aufgelegt. In diesem Band werden Flugzeugfirmen, Motorenhersteller und Zulieferbetriebe vorgestellt, von denen etliche Fertigungen im Bereich der Magnesiumguss -Knet- und -Walzfertigung betrieben.
[5] Adolf Beck: Magnesium und seine Legierungen, Verlag von Julius Springer, 1939 Berlin. Adolf Beck war der Leiter des Zentrallabors der I.G. Farben A.G. Bitterfeld. Mit seinem Buch schrieb er das Standardwerk für Magnesium, das noch viele Jahrzehnte seine Berechtigung hatte. Es umfasste auf 520 Seiten ausführlichst die Kapitel Rohstoffe und Herstellung, physikalische Eigenschaften, Festigkeiten, chemisches Verhalten, Korrosion und Oberflächenschutz, Schmelzen und Gießen, Umformen, spangebende Bearbeitung, Konstruktionsrichtlinien und Magnesium als Legierungselement.
Übrigens wurde ein ähnlich aufgebautes Buch in Ungarn von Emöd Gyula und Solti Màrton: MAGNÉZIUMÖNTÉSZET, Nehézipari Könyv és Folyóiratkiadó Vállalat, Budapest 1953 (MAGNESIUMGUSS, Buch- und Zeitschriftenverlag für die Schwerindustrie) mit Bezug auf Adolf Beck aufgelegt.
Von Walter Bulian und Eberhard Fahrenhorst wurde 1943 das Buch „Metallographie des Magnesiums und seiner technischen Legierungen“ im Springer Verlag Berlin aufgelegt. Dr. phil. W. Bulian war Leiter des Metall-Laboratoriums der Wintershall A.G. und Dr. phil. E. Fahrenhorst Assistent daselbst.
Von André Caillon wurde in Frankreich das Buch „LA FUSION INDUSTRIELLE DU MAGNESIUM ET SES MOULAGES EN SABLE“ von Publications scientifiques et techniques du Ministère de l’Air N° 130, 1938, aufgelegt. Das Buch beschäftigt sich ausführlich mit der Gießtechnologie bis hin zur Fehlervermeidung.
[6] Joseph Black painted by David Martin 1787, National Galleries of Scotland
[7] Sir Humphry Davy auf einem Gemälde von Thomas Phillips aus dem Jahr 1821
[8] Antoine Bussy von Pierson, photographer, National Library of Medicine
[9] Michael Faraday, Ölgemälde von Thomas Phillips, etwa 1841/42
[10] Robert Wilhelm Bunsen, Photogravure von J. B. Obernetter um 1885
[11] Dirk Hackenholz: Die elektrochemischen Werke in Bitterfeld 1914-1945, Verlag LIT, 2004
[12] Kali und Steinsalz, herausgegeben vom VKS e.V., Heft 3/2013
[13] Museodellatecnica tecneum, SAIM Gesellschaft - Magnesiumwerk, (Societá anonima italiana magnesio, Bozen
[14] Norsk Hydro: Company history 1929 - 1945
[15] Mahle Innovation - der Motor der Geschichte, Mahle GmbH, 2014
[16] Bugatti Revue 36, Editor Jaap Horst, Volume 13, Issue 5
[17] Dr.-Ing. Karlheinz Lange, BMW Mobile Tradition: The History of Engines – Engines that Made History
[18] VDI-Zeitschrift 54 (1910) Nr. 10
[19] www.luftarchiv.de
Schlagworte
AluminiumDruckgussEisenFertigungForschungFotoGestaltungGIFAGussGusseisenGussteileKonstruktionKupferLeichtbauMaschinenbauMesseMetallographieProduktionSchmelzenStahlVerlagWerkstoffe