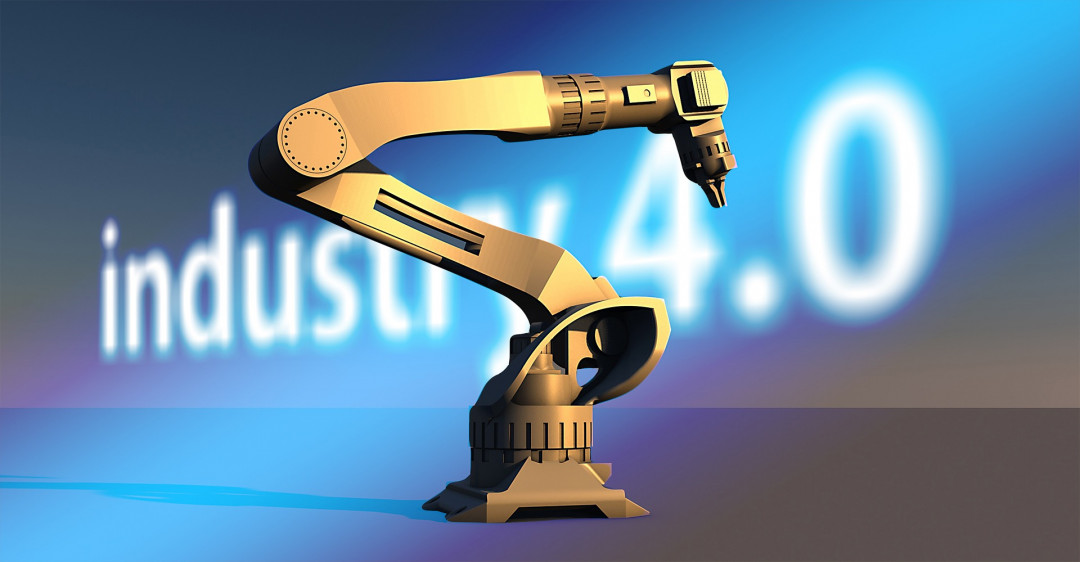
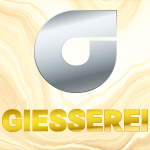
Die Fraunhofer IFAM-Forschungseinrichtung in Bremen arbeitet derzeit an der Verknüpfung der Gießereitechnik mit Elementen von Industrie 4.0 – genauer an der Gussteilkennzeichnung und der Sensorintegration. Zugleich steht die Ausgründung eines neuen Unternehmens zur Vermarktung der sogenannten Casttronics-Technologie unmittelbar bevor. Christoph Pille, Stellv. Abteilungsleiter, Thomas Rahn, Projektleiter, und Franz- Josef Wöstmann, Abteilungsleiter Gießereitechnologie und Leichtbau, beantworteten der GIESSEREI hierzu einige Fragen.
Herr Pille, Herr Rahn, Herr Wöstmann, die an Ihrem Institut entwickelte sogenannte Casttronics-Technologie zum direkten Eingießen von RFID-Transpondern im Aluminium- Druckgießverfahren wollen Sie in einer Ausgründung vermarkten. Was genau wird das Unternehmen machen?
Wöstmann: Die Ausgründung verfolgt die wirtschaftliche Serienproduktion des Halbzeugs, also des eingießbaren RFID-Transponders mitsamt der thermischen Schutzkapselung, ergänzt um eine Softwarelösung (vgl. GIESSEREI 7/2017, Anm. d. Red.). Dazu zählt Daten auslesen, Daten verwalten, Daten analysieren und Daten-Management. Wo das direkte Eingießen des RFID-Transponders aus thermischen oder geometrischen Gründen derzeit nicht möglich ist, wird es eine Lösung geben, den Transponder auch nachträglich mit dem Bauteil zu verheiraten. Damit wird auch eine Lösung für Bauteile mit Wärmebehandlung sowie Bauteile aus Gusseisen oder Stahlguss und auch für nicht gießtechnisch hergestellte Bauteile angeboten. Für Druckgussteile wie z.B. Strukturguss gibt es bereits fertige Lösungen, den RFID in die Struktur des Bauteils passend einzugießen.
Welche Anfragen kommen aus dem Markt?
Pille: Das Unternehmen wird in einigen Wochen an den Start gehen. Wir bekommen heute schon jeden Tag Anfragen von Gießereien, von Zulieferern und von OEMs. Die Unternehmen wollen wissen, wie sie ihre Gussteile digitalisieren können, welche Vorteile ihnen das Verfahren bietet und was das Fraunhofer IFAM hierzu an Technologie anbieten kann
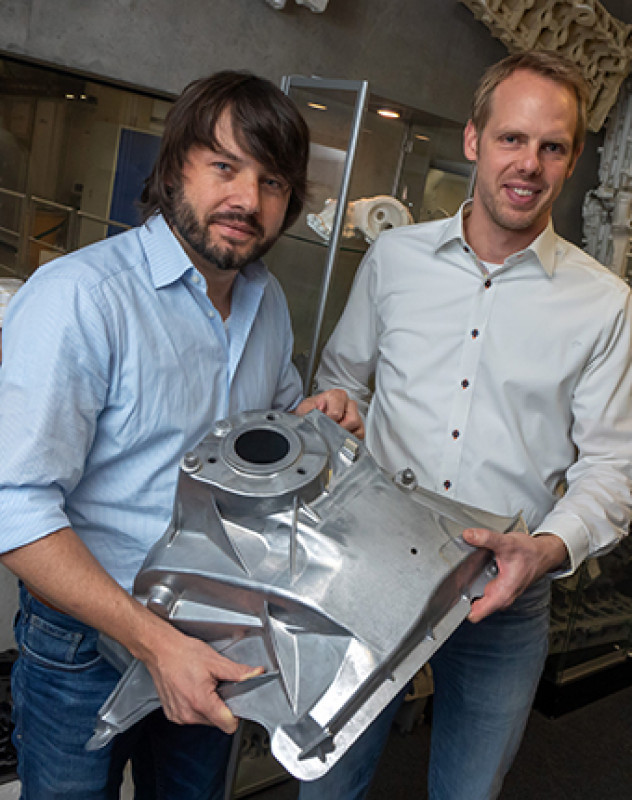
Welche konkreten Anwendungen sehen Sie?
Wöstmann: Zunächst einmal Plagiatsschutz, eine robustere Bauteilkennzeichnung bei Bauteilen mit einer hohen Marge und bei sicherheitsrelevanten Bauteilen. Das ist der Anwendungsfall, der von den Kunden aktuell am stärksten nachgefragt und auch am leichtesten verstanden wird. Aber im Weiteren geht es um den Plagiatsschutz und Verfolgung über die gesamte Supply Chain, vom Herstellungsprozess bis hin zum Recycling inkl. Datenauswertung zur Qualitätssicherung und Entwicklung neuer Geschäftsmodelle.
Was ist das Innovative an Ihrer Lösung?
Rahn: Der integrierte RFID bedeutet zuerst mal Langlebigkeit. Eine derzeit übliche, optische Kennzeichnung wird über kurz oder lang verloren gehen, wird überlackiert, korrodiert oder beschädigt. Der eingegossene Transponder begleitet das Gussteil sein ganzes Leben lang. Damit lassen sich auch die nachgelagerten Prozesse aktiv abfragen, beispielsweise um zu verfolgen wie das Bauteil gewartet wird, was genau mit ihm passiert. Das geht mit den aktuellen optischen Markierungssystemen wie Barcode oder DataMatrix-Code nicht immer sicher.
Wöstmann: Das Entscheidende ist die dahinterstehende Software und damit das Potenzial an zusätzlicher Wertschöpfung auf Basis der Schnittstelle zwischen Hardware und Software. Das Ziel sind neue Industrie 4.0 Lösungen.
Können Sie das näher ausführen?
Wöstmann: Der Anwender bekommt die Hardware und Software- Lösungen für die Datenbank für Bauteilverfolgung, die Qualitätssicherung sowie das Auswerten von Daten. An der Stelle wird es wirklich interessant, da ich aus den Daten zusätzliche Möglichkeiten generieren kann. Gießereien haben eine Vielzahl von Daten in der Produktion, die sie gar nicht nutzen. Ein aktuelles Thema ist, diese Daten so zu verwenden, dass ich meinen Prozess verbessern kann: Qualitätsüberwachung für das Bauteil und für die Produktionsaggregate, bedarfsgerechte Wartung umsetzen und eine rückwirkende Qualitätssicherung, was heute so nicht möglich ist. Und ich kann auf meine Prozesse zurückschließen und diese verbessern. Wenn man das weiterverfolgt, dann gibt es noch eine ganze Reihe weiterer Anwendungen, die man aus den Daten generieren kann, wie zum Beispiel das Erkennen einer Drift in einzelnen Prozessparametern und dem automatischen Anpassen der Prozessparameter. Das ist für mich Industrie 4.0, vernetzte, selbststeuernde und adaptive Prozesse über die gesamte Wertschöpfungskette. Damit lässt sich die Effizienz in den Gießereien weiter steigern.
Aus den gewonnenen Daten lassen sich neue Geschäftsmodelle entwickeln. Welche Industrie-4.0-Lösungen sind denkbar, worin bestehen die Herausforderungen?
Wöstmann: Die meisten Gießer haben zu sehr die Produktion im Fokus. Wenn man Industrie 4.0 als Basis für weitere, neue Aktivitäten nutzen will, dann muss man von diesem Grundgedanken wegkommen. Industrie 4.0 heißt Digitalisierung. Die Franzosen sprechen, was es noch besser ausdrückt, auch von „Dematerialisation“. Sehr treffend. Mit der Digitalisierung eröffnet sich die Chance mit den Daten zu den Bauteilen Geld zu verdienen und die Wertschöpfungskette zu verlängern.
Die Wertschöpfung steckt nicht mehr im Bauteil, sondern in seinen Daten, mit denen ich zu neuen Dienstleistungen komme?
Wöstmann: Das ist der wesentliche Punkt. Ich muss die Daten verstehen und für neue Geschäftsmodelle einsetzen. Und das ist leider der Trugschluss der meisten Gießer, sie denken immer noch in der Materie, im Gussteil. Erfolg wird in den nächsten Jahren aber nicht mehr über die Kilos erzielt, sondern über die Funktion.
Gießer beschränken sich beim Thema Industrie 4.0 zu sehr auf Prozessoptimierung? Wöstmann: Eindeutig ja. Solange ich mich aber nur im Bereich der Verbesserung der Prozessabläufe bewege, habe ich vielleicht ein oder zwei Jahre Luft gewonnen, weil ich aus der höheren Qualität und dem geringeren Ausschuss noch das letzte kleine Quäntchen an höherer Marge für mich selbst rausziehe. Aber auch hier wird die Konkurrenz nachziehen. Nur wenn ich aus den Daten auch weitere der Produktion nachgelagerte Funktionen/ Nutzervorteile einbringen kann, kann ich mich vom Markt absetzen.
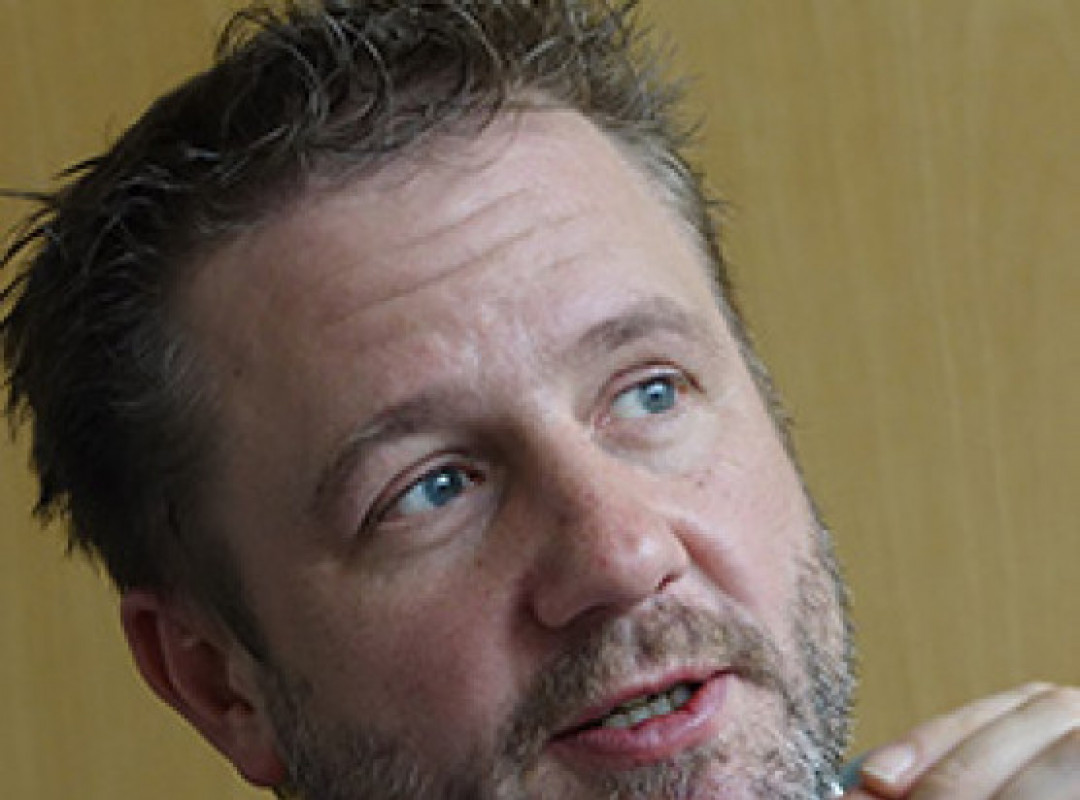
Unter Industrie 4.0 verstehen Sie neue Dienstleistungen?
Wöstmann: Nichts anderes. Die neuen Digitaltechniken für mehr als die klassische Prozessoptimierung nutzen. Das, was wir heute nicht machen, ist mit Industrie 4.0 auch wirklich umzusetzen. Industrie 4.0 und Digitalisierung beginnt bei der Zusammenarbeit mit dem Kunden. Mit dem Kunden muss ich sehr viel enger zusammenkommen, und zwar schon vor der eigentlichen Produktion.
Als Erstes muss also ein digitaler Kanal zum Kunden aufgebaut werden?
Wöstmann: Ja, es geht nicht nur darum, die Produktion des eigentlichen Bauteils zu optimieren, sondern die Schnittstelle zum Kunden zu entwickeln. Wenn ich die habe, dann habe ich eine Plattform für neue Dienstleistungen und alle, die produzieren, sind davon abhängig. Wenn ich den Input vom Kunden habe, dann kann ich ganz andere Leistungen anbieten in Richtung Flexibilität, Variantenvielfalt, kundenindividuelle Massenproduktion. Weitergedacht kann ich jetzt anfangen Systeme anzubieten und nicht nur Kilos zu verkaufen. An der Stelle wird es auch mit dem RFID-Transponder interessant. Der Transponder kann mit anderen Bauteilen kommunizieren und lässt sich auslesen, ich weiß jederzeit, wo er wann ist. Das Bauteil kann beispielsweise beim aktiven Plagiatschutz selbst entscheiden, gehe ich in Dienst oder gehe ich nicht in Dienst, weil z. B. ein Ersatzteil kein Originalteil ist. Das ist zum Beispiel die Sicherung des Aftersalesgeschäftes.
Was können Sie sich konkret vorstellen?
Wöstmann: Beispielsweise komplette digitalisierte Logistikketten mit dem Entfall von Positionen, wie ich sie heute habe. Bei der Ersatzteilversorgung etwa die Reduktion von Lagerkapazitäten. Wenn ich an die Gießer im Automotive-Bereich denke, dann lässt sich dort direkt aus dem Markt ablesen, wann welche Bauteile irgendwo in der Werkstatt sind. Ich bekomme im Prinzip sogar mit, wenn das Auto in die Werkstatt einfährt und kann auslesen, wann welche Bauteile ausgetauscht werden und welche Komponenten bearbeitet werden müssen. Da kann ich dem Kunden, dem Autohersteller, einen Mehrwert mitgeben, denn der braucht sich um die Ersatzteillieferung nicht mehr zu kümmern.
Wer kann die Plattform betreiben, auch der Gießer selbst?
Wöstmann: Definitiv ja.
Wenn wir jetzt wieder einen Schritt zurückgehen, dann wird der erste Schritt des neuen Unternehmens sein, den eingießbaren Transponder mit dem zugehörigen Prozesswissen zu vermarkten. Haben Sie darüber hinaus auch weitere Elektronikbauteile als Eingießlösung im Köcher?
Pille: Kommunikation und die Kennzeichnung mit Datenspeicher ist das eine. Das zweite ist, wie verpasse ich einem Bauteil „Nerven“. Die nächsten Anwendungen werden integrierte Sensorlösungen sein. Das Bauteil selbst soll merken, in welchem Zustand es aktuell ist. Ein dominierendes Thema ist hier das autonome Fahren. Wenn ich selbst nicht mehr am Steuer sitze, ich selbst also nicht mehr Herr bin über mein eigenes Fahrzeug, bekomme ich auch kein Feedback mehr von meinem Auto. Hat das Fahrwerk beispielsweise einen Schaden erlitten, weil der Wagen zu schnell über einen Bordstein gefahren ist oder sonstigen Missbrauchslasten unterlag, dann merke ich das nicht mehr. Das ist ein Problem. Das Fahrzeug muss das zukünftig selbst merken können, d. h., die Anforderung nach mehr Sensorierung im Fahrzeug wird in Zukunft mit Sicherheit deutlich steigen. Insbesondere wenn das Fahrzeug einen Schaden hat, der die Fahrsicherheit gefährdet und daher maximal in der Notlaufeigenschaft betrieben werden darf, damit es den Weg zur nächsten Werkstatt schafft, dann muss das mindestens das eigene Fahrzeug wissen. Im Zeitalter des kollektiv autonomen Fahrens aber auch die Fahrzeuge, die hinter diesem Wagen fahren.
Wo sind die Grenzen der Technologie? Könnten Sie auch Mikroprozessoren eingießen? Pille: Erst kürzlich wurden wir darauf angesprochen, ob das technologisch geht. Aktuell beherrschen wir es noch nicht. Daran müssen wir noch arbeiten, ein Mikroprozessor ist ein elektronisch aufwendigeres System als ein RFID-Transponder. Aber da stellt sich auch die Frage, ob das wirklich sinnvoll ist.
Also keine Bauteile mit möglichst viel Intelligenz?
Wöstmann: Soviel Intelligenz wie notwendig, aber immer noch so günstig und vor allem zuverlässig wie möglich. Je mehr ich an komplexen Systemen integriere, desto fehleranfälliger wird das System. Die Frage ist immer auch: Wie sieht es mit Reparaturkonzepten und der Wirtschaftlichkeit aus? Integration machen wir nur vor dem Hintergrund, dass sie möglichst einfach und möglichst robust erfolgen soll, auf das notwendigste im Endeffekt beschränkt. Das gilt auch für den Transponder. Der Transponder dient für die individuelle Kennzeichnung und Identifizierung. Wenn das gegeben ist, dann kann ich über ein separates Softwaresystem im Prinzip alle Daten damit ablegen und automatisch zuordnen. Und diese Schnittstelle ist eben das eigentlich interessante. Ich kann auch einen Transponder nehmen, auf dem ich die Daten speichern kann. Wir haben auch schon Kunden gehabt, die alle Prozessparameter auf dem Bauteil speichern wollten. Nur, was habe ich damit gewonnen, wenn die Daten nur auf dem Bauteil liegen, nicht aber in meiner zentralen Datenbank? Dann habe ich die Daten erhoben, und kann sie doch nicht auswerten. Das Ergebnis wäre ein teurerer Transponder und im schlimmsten Fall keinerlei Redundanz, wenn ich die Daten nicht anderswo abspeichere. Damit wäre die Technologie ad absurdum geführt.
Das Bauteil kommuniziert mit der IT, die eigentliche Intelligenz aber steckt in der Software der Datenbank bzw. der Cloud?
Pille: Genau. Plakativ dargestellt, wir werden wohl kaum jede Schraube in einem Pkw mit Sensorfunktionen ausstatten, das wird der Nutzen nicht hergeben. Bei einem E-Motorengehäuse kann ich mir das sehr gut vorstellen. Da sind die Daten relevant und wichtig. Unter welchen Betriebsbedingungen befindet sich das Gehäuse, welchen Verformungen unterliegt es. Da wird es interessant. Wo es aus meiner Sicht geradezu kriegsentscheidend wird, ist das ganze Thema Fahrwerk bei Leichtbau und zukünftigen Fahrzeugkonzepten. Wenn ich über ein Achssystem im Pkw nachdenke mit den verschiedenen Lenkern, dann sind das alles sicherheitsrelevante Bauteile. Sind diese Bauteile geschädigt, dann sollte man darüber in Kenntnis sein.
Der Sensor im Fahrwerk würde an den Bordcomputer melden und der an das übergeordnete IT-System in der Cloud, von wo aus der Bordcomputer dann die Information erhalten würde: stehen bleiben oder in die Werkstatt?
Wöstmann: Entsprechend der Eskalationsstufe. Das Zweite dabei ist, ich muss dann nicht mehr mit mehrfacher Sicherheit konstruieren. Ich kann das Bauteil bedarfsgerecht auslegen und einen eventuellen Überlastfall sofort detektieren. Damit wird für den Leichtbau eine neue Option eröffnet.
Wer liefert das IT-System?
Wöstmann: Das könnte der Gießer sein, der Automobilhersteller, ein Zulieferer oder ein neuer Dienstleister wie unsere Ausgründung.
Das Interview führte Gerd Krause, Mediakonzept, Düsseldorf
Dipl.-Wi.-Ing. Christoph Pille, Stellv. Abteilungsleiter, Dipl.-Wi.-Ing. Thomas Rahn, Projektleiter, Dipl.-Ing. Franz-Josef Wöstmann MBA, Abteilungsleiter Gießereitechnologie und Leichtbau, Fraunhofer IFAM, Bremen
Schlagworte
AluminiumDigitalisierungDruckgussForschungGießereiGießereitechnikGusseisenGussteileIndustrie 4.0KommunikationLeichtbauLogistikProduktionProzessoptimierungRecyclingSicherheitSoftwareStahlguss