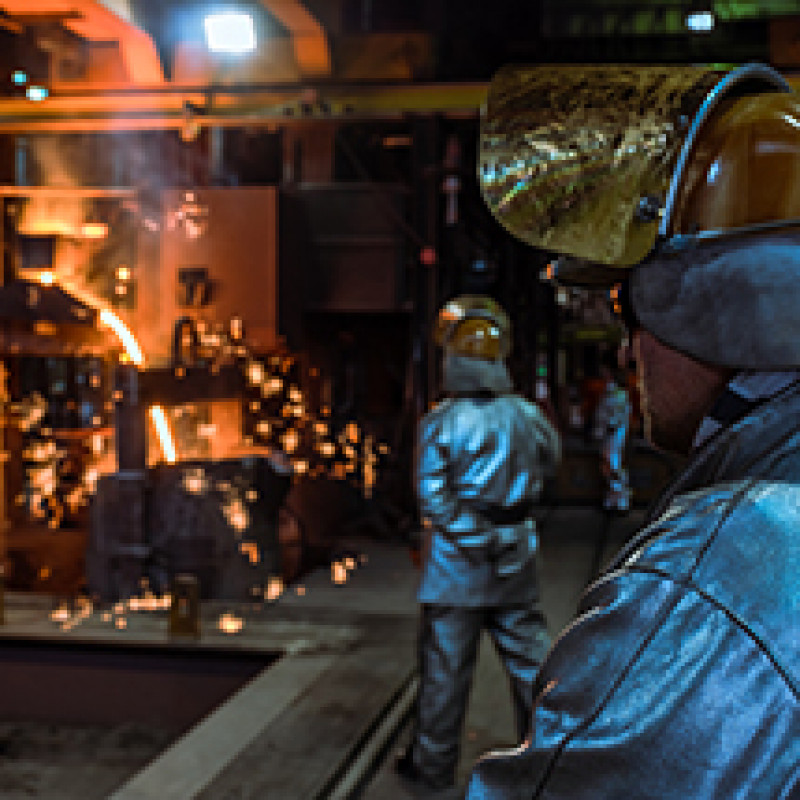
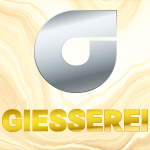
Die Bonner Gießerei Stolle ist erfolgreich im Sondermaschinenbau tätig – das Angebotsspektrum umfasst nicht nur das Gießen und die Bearbeitung, sondern die komplette Projektierung.
Es ist Freitagmorgen um kurz nach halb sieben, als in der Gießerei Stolle an der Broichstraße in Bonn-Beuel die letzten Vorbereitungen für den Abguss eines 25 Tonnen schweren Maschinenbetts getroffen werden. Ein stämmiger Mann mit silbernem Schutzanzug und geöffnetem goldenen Blendschutzvisier winkt die am Hallenkran befestigte mannshohe Pfanne langsam an den Eingusstrichter heran. Konzentriert verfolgt er jede Bewegung des gewaltigen Gefäßes, das Gesicht erhellt vom Schein der gleißenden Schmelze. Etwa fünf bis sechs Meter entfernt, am anderen Ende der mit Gewichten beschwerten Gitterstruktur über der Bodenform, spielt sich der gleiche Prozess ab. Am Drehkreuz der Pfannen warten derweil weitere Gießer auf ihren Einsatzbefehl, um die Pfannen zum Abgießen zu kippen. Es folgt eine letzte Messung mit der Temperaturmesslanze – dann ergießt sich die goldglänzende Schmelze funkensprühend in breiten Strahlen an beiden Enden der Form in die Öffnungen. Zwischen den Gewichten steigen kurz Flammen auf, dann erlöschen sie und machen einer Rauchsäule Platz. Mehrere weitere Formen warten noch auf ihren Abguss – 98 Tonnen Graugussschmelze wird der Tageskupolofen mit Obergichtabsaugung heute insgesamt für die Abgüsse bereitstellen.
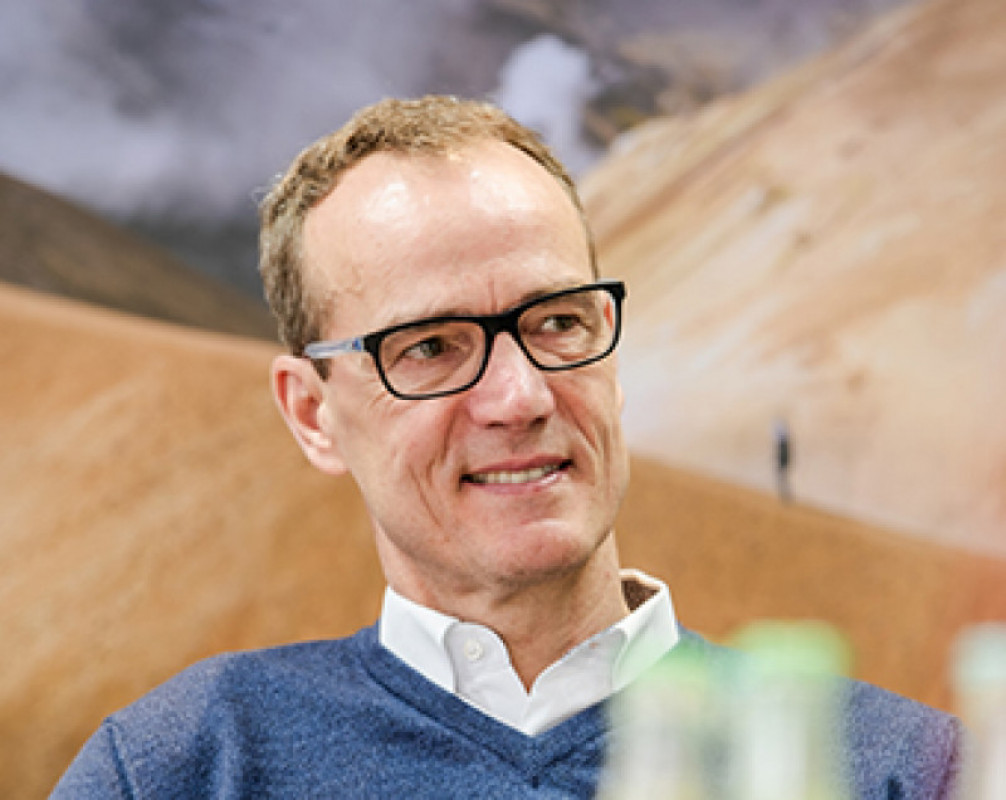
Massive Expansion infolge der Globalisierung
Schauplatz des eindrucksvollen Schauspiels ist die Gießerei Stolle mit Standorten in Bonn Bad-Godesberg und -Beuel. Sie liefert Teile für den Sondermaschinenbau, die in der Automobilindustrie, dem klassischen Maschinenbau und der Mess- und Prüftechnik eingesetzt werden. Trotz 120-jähriger Geschichte ist das Unternehmen mit etwa 180 Mitarbeitern/-innen in seiner heutigen Form erst mit der Globalisierung auf die heutige Größe angewachsen. Dieser Ausbau begann mit dem Kauf einer Gießerei in Bonn-Beuel im Jahr 1997, nach fast 100 Jahren überschaubarer Fertigung am Stammsitz in Bonn-Bad Godesberg. „Wir haben das Werk in Beuel im Verlaufe von zehn Jahren massiv ausgebaut und die Belegschaft unserer Firma in dieser Zeit insgesamt verdreifacht. Es wurden Hallen gebaut, zusätzliche Bearbeitungskapazitäten und Montagebereiche geschaffen, weitere Finish-Prozesse an unseren Produkten auf den Weg gebracht und eine den neuen Erfordernissen angepasste Verwaltung aufgebaut,“ erinnert sich Geschäftsführer Martin Stolle an die Anfänge der Expansion.
Angebotsspektrum umfasst Guss, Bearbeitung und Projektierung
Heute sind Lieferungen für weltweite Investitionsprojekte ein nicht unerheblicher Bestandteil des jährlichen Umsatzes von etwa 25 Millionen Euro. Diese Projekte können die Bonner Spezialisten zu Montageeinsätzen zu Werften, die Hallen mit Platten auslegen, neuen Automobilfabriken, die Montageplätze einrichten, oder auch zu Unternehmen der Kraftwerkbranche führen, die ebenfalls große Plattenfelder brauchen. Plattenfelder? Das sind beispielsweise Aufspannplatten mit Nuten und Bohrungen zur Befestigung von Vorrichtungen, Maschinen, Messstationen oder einfach Montageflächen. Zum allgemeinen Portfolio des Unternehmens gehören insbesondere Platten für den Werkzeugmaschinenbau, Prüfplatten, Messplatten, ebenso wie die soeben in der Gießhalle abgegossenen tonnenschweren Maschinenbetten – jeweils „maßgeschneidert und nicht von der Stange“, wie Stolle betont.
Am Zielort werden die Platten dann vielfach auf Betonfundamenten verankert oder schwingisoliert aufgestellt – Konstruktion, Guss, Bearbeitung und Projektierung, ebenso wie die Montage vor Ort kommen hier also, wenn gewünscht, aus einer Hand. „Wir haben uns auf das Geschäft mit Platten, Maschinenbetten, -Ständern und -Winkeln sowie die Montage von Führungssystemen bzw. Einbauteilen spezialisiert und konzentrieren uns darauf, unsere Produkte in Gänze, also inklusive Konstruktion, Logistik und Montage bereitzustellen. Sie können bei uns üblicherweise keinen Rohguss kaufen und wir bearbeiten auch eigentlich keinen fremden Guss. Wir sehen uns bei der Konstruktion und Entwicklung der Produkte als Partner der Kunden und nicht als Zulieferant“, formuliert Martin Stolle das Angebotsspektrum und fügt hinzu „wir wollen mit und für unsere Kunden geeignete Produkte entwickeln – das ist seit jeher unsere Unternehmensphilosophie“.
Individuelle Fertigung und Montage
Der Großteil des Geschäfts wird innerhalb der Grenzen des Kontinents abgewickelt, denn hier sitzen die großen Maschinenbauunternehmen. „Eine große Werkzeugmaschine, die beispielsweise einen Schiffsdiesel oder große Teile für die Aeronautik bearbeitet, können Sie nicht in Asien kaufen und auch nicht in den USA. Die Hersteller hierfür sitzen in Europa. Wenn Sie über die Fertigungstechnik-Messe IMTS in Chicago gehen, stehen da auch überwiegend die europäischen Werkzeugmaschinenhersteller“, macht Martin Stolle die Gewichtung auf dem internationalen Maschinenbaumarkt deutlich. Die Stolle-Kunden sind in allen Bereichen des Werkzeugmaschinenbaus, der Prüf- und Energietechnik, ebenso wie in der industriellen Messtechnik vertreten. Und deren Ansprüche sind hoch, wie die Anforderungen an die Aufspannplatten zeigen.
Denn Platte ist nicht gleich Platte, da sich Aufspannplatten mit den gleichen Ausmaßen in Gewicht und Beschaffenheit stark unterscheiden können – je nachdem, wie der Anwendungsfall ist. „Wir haben Kunden, die eine Plattenbelastung von 150 Tonnen pro Quadratmeter wünschen – für uns nicht ungewöhnlich – und andere, die nur eine sehr niedrige Gesamtbelastbarkeit auf der Oberfläche benötigen. Die Konstruktion der niedriger belasteten Platte wird deutlich filigraner und leichter sein, aber äußerlich möglicherweise gleich aussehen“, erklärt Martin Stolle, der die Geschicke der Eisengießerei gemeinsam mit seinem Cousin Wolfgang lenkt und seit 1990 im Unternehmen tätig ist. Insgesamt produzieren die eigenen Gießereien Gussteile mit einer Tonnage von bis zu 14 000 Tonnen im Jahr.
Als Systemlieferant sorgt das Unternehmen bei der Montage je nach Wunsch auch für schwingungsisolierte Aufstellung – zum Beispiel bei Prüfständen für den Automobilbau oder den Getriebebau. „Diese Prüfstände, die mitunter sehr beachtliche Ausmaße haben können, stehen dann auf Stahlfedern, auf Elastomerfedern oder auch auf Luftfedern“, beschreibt Martin Stolle und zeigt die Dimensionen eines Windradgetriebeprüfstands beispielhaft mit ausladenden Armen. Auch bei Fahrsimulatoren auf einem Automobilprüfstand ist die Basis häufig ein Stolle-Produkt. „Damit tragen wir zur Flexibilität in der Automobilindustrie bei, denn der Kunde muss lediglich seine Anforderungen formulieren – alles Weitere übernehmen wir“, sagt der Wirtschaftsingenieur stolz. Das Geschäft mit Automobilprüfständen läuft auch angesichts der Dieselkrise und dem Wandel der Mobilität derzeit allerdings schleppend.
Herausforderungen sind Industrieakzeptanz und Fachkräftenachwuchs
Zurück im Werk führt Gießereileiter Florian Lorenz durch einen Teil der 13 Hallen, in denen sich alle Prozessschritte einer Gießerei vom Modellbau über die Kernmacherei und Gießerei bis hin zu Fertigbearbeitung, Finish und Logistik widerspiegeln. Hinzu kommen die Konstruktions- und Entwicklungsabteilung sowie die Verwaltung. Beschäftigt sind sowohl Vertriebs- und Gießerei-Ingenieure als auch Gießerei-, Industrie- und Zerspanungsmechaniker, Modellbauer, Produktdesigner, Mechatroniker sowie Vertreter vieler weiterer Berufsgruppen.
Dass bei Stolle vieles selber gemacht wird, ist auch ideal für die eigene Ausbildung: Mit 8 -10 Azubis im Jahr stemmt sich das Unternehmen auf eigene Faust erfolgreich gegen den Fachkräftemangel. Und auch mit der Nachbarschaft ist die Gießerei so gut es geht im Reinen, obwohl an der Industrieakzeptanz kontinuierlich etwa mit der Beteiligung am Tag der Industrie oder der Installation von umfangreicher Filtertechnologie gearbeitet werden muss. In Kühl-, Entstaubungs- und Filtertechnologie wird deshalb auch viel investiert. Das Ergebnis kann sich sehen lassen: Am Kupolofen und an der Sandanlage werden jeweils 40 000 Kubikmeter Emissionen und Stäube pro Stunde abgesaugt. Das entspricht stündlich etwa einem Viertel des Volumens des Oberhausener Gasometers.
Abgüsse mit bis zu 140 Kernen
„Wir formen zuerst ein Formbett im Boden, bauen dann unsere Modelleinrichtung auf, und formen dann hintereinander weg erst den Unterkasten und dann den Oberkasten. Schließlich werden die Kerne eingebaut und das Ganze gießfertig vorbereitet. Das dauert zwei bis drei Tage“, beschreibt Lorenz die Vorarbeit für den Abguss einer Aufspannplatte in der Gießhalle. Lorenz ist 33 Jahre alt, stammt aus der Gegend von Freiberg in Sachsen und hat im ostsächsischen Bautzen Wirtschaftsingenieurwesen mit Vertiefungsrichtung Gießereitechnik studiert. Der Studiengang fand in Kooperation mit der TU Bergakademie Freiberg statt. Nach Stationen bei AC Tech in Freiberg und der Walzengießerei in Quedlinburg ist der junge Ingenieur nun seit fünf Jahre bei Stolle in Bonn.
Auf dem Weg durch die Kernmacherei, in der drei Mitarbeiter arbeiten, erklärt er die Komplexität von Form- und Kernkonstruktionen, die bis zu 140 Kerne umfassen können und alle im Handformverfahren vor Ort selbst gefertigt werden. Gerade lässt das Brummen der Vibrationstische zur Verdichtung des Kernsands die Luft vibrieren. Die Gewichte der eingesetzten Kerne reichen von 2 - 3 Kilogramm bis zu 1,3 Tonnen. Wichtig für Stolle ist aber auch der eigene Modellbau, der laut Martin Stolle ohne entsprechende Spezialisierung und Flexibilität eine „enorme Summe“ an den Gesamtkosten der Produkte verschlingen kann. In Bonn werden Kernkästen und Modelle komplett nach Zeichnung gefertigt. Langweilig wird es dabei nicht, denn Routine ist die Ausnahme, da „jedes Mal kundenspezifisch“ konstruiert wird.
XXL-Bearbeitung im µ-Bereich
Einen Verkaufsraum für Gussprodukte im Großformat könnte man die Putzerei nennen, wo rund ein Dutzend größere und kleinere Werkstücke in den Abmessungen von 2 x 3 bis 9 x 3 Metern aufgebockt sind. Die Oberfläche eines Maschinenbetts mutet an wie eine Szene in einem Science-Fiction-Film. Lorenz: „Das ist eines unserer typischen Produkte – ein Kompaktmaschinenbett. Auf ihm werden anschließend Frästeile bearbeitet. Rundherum verlaufen später bereits vorgegossene Ablaufrinnen für das Kühlmedium, das während der Bearbeitung aufgefangen und wieder hoch zum Fräskopf gepumpt wird.“
Der Höhepunkt der Betriebsbesichtigung folgt am Ende, denn jetzt finden alle Puzzlestücke zusammen und bilden ein großes Ganzes. Die Fertigbearbeitungsmaschine für Bauteile mit Abmessungen von 20 x 5 Metern ist der Anlass für die Erkenntnis, denn mit ihr wird der Sinn der Produkte aus dem Hause Stolle deutlich. Die gewaltige Maschine hat einen von Stolle selbst gefertigten Maschinentisch, der fest im Fundament verankert ist – so können Maschinenkonstruktionen also aussehen, bei denen Platten oder Maschinenbetten von Stolle für Stabilität sorgen! Das Portal der Anlage vom Typ Powertech des Coburger Maschinenbauers Waldrich Coburg fährt fast wie eine Autowaschanlage über das eingelegte Maschinenbett hinweg und fräst dabei die gewünschten Umrisse µ-genau per Fünf-Achs-CNC-Bearbeitung nach. Die Arbeiten in der Putzerei, der späteren Vor- und Fertigbearbeitung, sowie der aufwendigen Montage- und Finishingprozesse verschlingen pro Bauteil noch viele Wochen – insgesamt ein hoher Aufwand, der mit mehreren zehntausend Euro pro Platte auch seinen Preis hat.
VON ROBERT PITEREK, DÜSSELDORF
Schlagworte
AbsaugungAutomobilindustrieFertigungFormverfahrenGießenGießereiGussteileKonstruktionLogistikMaschinenbauMessePutzereiVertrieb