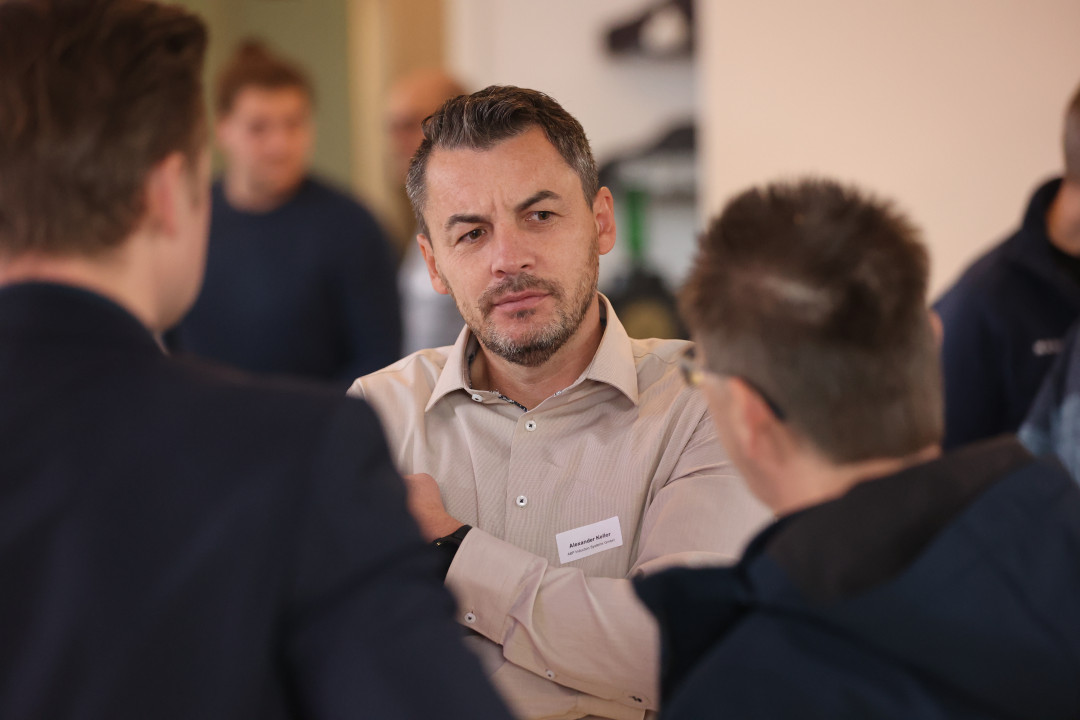
Die aktuellen Megatrends, insbesondere die Dekarbonisierung und die Digitalisierung, bewirken, dass grundlegende Prozesse in der metallverarbeitenden Industrie betrachtet und verändert werden müssen. In den Fokus ist dabei auch der Schmelzprozess des Druckgießens, Halbzeuge-Produktion und Recycling auf dem Aluminiumsektor geraten, da hier hohe
CO2-Emissionen entstehen, ein beträchtlicher Energieverbrauch zu registrieren und ein nicht geringer Materialverlust zu verzeichnen ist.
Hier sind innovative Lösungsansätze gefragt – die Alexander Keller, Head of System Sales bei ABP Induction, insbesondere in der Umstellung von traditionellen Erdgasöfen auf Induktionsschmelzöfen sieht, wie er im Interview erklärt.
Induktionsofentechnologie im Aluminium-Umfeld – wo sehen Sie die Vorteile?
Alexander Keller: Mit dem Einsatz der Induktionstechnologie in Verbindung mit regenerativen Energiequellen wird eine nahezu emissionsfreie Produktion ermöglicht. Im Vergleich zu Gasöfen bietet unsere Induktionstechnologie zahlreiche Vorteile: eine erhebliche Reduktion der CO2-Emissionen um bis zu 94%, eine signifikant höhere Energieeffizienz und wesentlich geringere Materialverluste. Die Energiebilanz der Induktionsschmelzöfen ist beispielsweise mit 440 kWh/t deutlich günstiger im Vergleich zu Gasöfen. Über eine Wärmerückgewinnung lässt sich der Einspareffekt nochmals um bis zu 20 Prozent erhöhen. Außerdem sind die Betriebskosten bei der Nutzung von Induktionstechnologie, insbesondere unter Berücksichtigung der Preise für CO2-Zertifikate und Energie, schon kurz- bis mittelfristig günstiger.
Aluminiumverarbeitung bleibt eine energieintensive Industrie – wie agieren Sie mit Blick auf Energiekosten und -verfügbarkeit?
Alexander Keller: Induktionsöfen von ABP können nicht nur durch niedrigen Energieverbrauch glänzen sondern auch als Energiespeicher genutzt werden – es ist also ein Ofenbetrieb möglich, der auf den jeweiligen Strompreis abgestimmt werden kann. Das heißt, wenn Strom günstig ist, nutzt man den großen Puffer im Ofen, der bis zu vier Stunden Produktion abdecken kann. Seine Vorteile ausspielen kann diese Produktionsweise nicht nur aus wirtschaftlicher Sicht, sondern auch mit dem Blick auf den „Global Footprint of Product“.
Es geht also um den CO2-Fußabdruck des jeweiligen Produkts?
Alexander Keller: Genau, wenn man Aluminium als Schrott einschmelzt, verbessert sich der globale CO2-Fußabdruck des Produkts. Bei der Herstellung von Primäraluminium wird sehr viel Energie benötigt. Aber wenn man Schrott in einer Induktionsanlage einschmilzt, reduziert sich der CO2-Footprint erheblich. Ein signifikantes Beispiel kommt aus der Automobilindustrie, wenn Teile aus recyceltem Aluminium mit einem Induktionsofen als Schmelzaggregat verarbeitet werden. Die Richtung stimmt, wenn sich der Carbon Footprint nahe null bewegt.
Wie groß sind die notwendigen Umstrukturierungen in Gießereien, vor allem, wenn eine Umstellung vom Gasofen zu Induktionsofen ansteht?
Alexander Keller: Da stehen wir im direkten Dialog mit unseren Kunden: Der Betrieb der ABP-Induktionsrinnenöfen in Aluminium-Gießereien wird gemeinsam mit dem Kunden logistisch optimiert und an bestehende Abläufe angepasst. In der Praxis kann man sich das so vorstellen: Behälter mit dem zu verwertenden Metall werden einfach per Stapler zum Ofen gebracht und dieser direkt beladen. Es sind also keine großen Änderungen im Materialfluss, der Anlagenbedienung oder Wartung erforderlich, was für den ABP-Kunden einen wichtigen Vorteil darstellt. Wir unterstützen Kunden dabei auf der gesamten Reise beim Umstieg von einer Technologie auf die andere intensiv – sei es durch Prozessberatung, Schulungen oder technische Unterstützung.
Wie verändern sich denn die Prozesse? Die Technologie hat sich ja bewährt…
Alexander Keller: Das ist richtig, wir sprechen bei unseren Induktionsrinnenöfen von „proven technology“. Die Erfahrung mit dieser Technik reicht über unsere Vorgänger-Unternehmen wie ASEA bis ins Jahr 1903 zurück. Und obwohl in den letzten 30 Jahren kaum neue Induktionsöfen für Aluminium installiert worden sind, sind die bestehenden Anlagen weiterhin in Betrieb. In dieser Zeit wurden viele Optimierungen gemeinsam mit den Kunden durchgeführt und die Entwicklung kontinuierlich fortgesetzt. Uns ist dabei eine enge Zusammenarbeit mit anderen Branchenteilnehmern wie Druckgießmaschinenherstellern und Lieferanten wichtig, gerade auch mit großen Kunden, die viele Aluminiumgießereien betreiben, um deren Anforderungen und Prozesse zu verstehen. Das Ergebnis ist eine Kombination aus jahrzehntelanger Erfahrung, bewährter Technologie und neuen Innovationen.
Können Sie Beispiele aus der Praxis liefern?
Alexander Keller: Natürlich, das zeigt sich zum Beispiel in der täglichen Produktionsweise: Normalerweise hat man bei Aluminium einen Abbrand von über 2 %, was die Recyclingzyklen auf ungefähr 50 begrenzt. Der Abbrand bei effizienten ABP-Anlagen liegt jedoch weit unter 1 %, wodurch sich die Anzahl der Recyclingzyklen mindestens verdoppelt. Das unterstreicht, dass ABP mit der Induktionsofen-Technologie auch auf dem Aluminium-Sektor extrem vertraut ist – mit Vorteilen gerade auch für die Anwender.
Aber in der Anschaffung sind Induktionsofenanlagen teurer als beispielsweise gasbetriebene Anlagen…
Alexander Keller: Auf den ersten Blick – ja. Aber es zeigt sich, dass die Induktionsschmelztechnik nicht nur umweltfreundlicher, sondern auch kosteneffizienter ist. Einsparungen durch geringere Betriebskosten und eine unabhängige Energieversorgung, die durch erneuerbare Energiequellen gesichert wird, positionieren die von unseren Ingenieuren stets weiterentwickelte und perfektionierte Induktionstechnologie als eine überlegene Alternative im modernen Druckguss und anderen Aluminium-Gießereien. Die angesprochenen Mehrkosten in der Anschaffung für eine Induktionsofenanlage amortisieren sich dank der beschriebenen Effizienzeigenschaften innerhalb von etwa zwei Jahren durch den niedrigeren Energieverbrauch, die Wärmerückgewinnung, den geringeren Abbrand und die Tatsache, dass keine CO2-Zertifikate benötigt werden. Induktionsöfen können zudem wie gesagt als Energiespeicher genutzt werden – eine wertvolle Eigenschaft gerade auch mit Blick in die Zukunft der energieintensiven Industrie. Das unterstreicht, wie die Umstellung auf innovative Technologien sowohl ökologische als auch ökonomische Vorteile bieten kann, was sie zu einer wichtigen Überlegung für die Zukunft der Fertigungsindustrie macht.
Wollen Sie denn auch wieder neue Öfen installieren?
Alexander Keller: Definitiv! Die Induktionsofentechnologie ist unter den heutigen Gegebenheiten perfekt für die Aluminiumverarbeitung. Und aktuell entwickeln unsere Ingenieure und Konstrukteure einen neuen Ofen für große Maschinen, Stichwort GiGA Casting, die mit einem einzigen Druck quasi halbe Autos produzieren. Dieses Entwicklungsprojekt ist weit fortgeschritten, und der Ofen wird voraussichtlich im Sommer 2025 verfügbar sein. Auch das zeigt, dass ABP die eigenen Anlagen konsequent an neue Trends und Bedürfnisse der Industrie anpassen kann.
ABP Induction Systems GmbH
Kanalstr. 25
44147 Dortmund
www.abpinduction.com
(Hinweis: Alle Fotos von ABP Induction Systems GmbH)
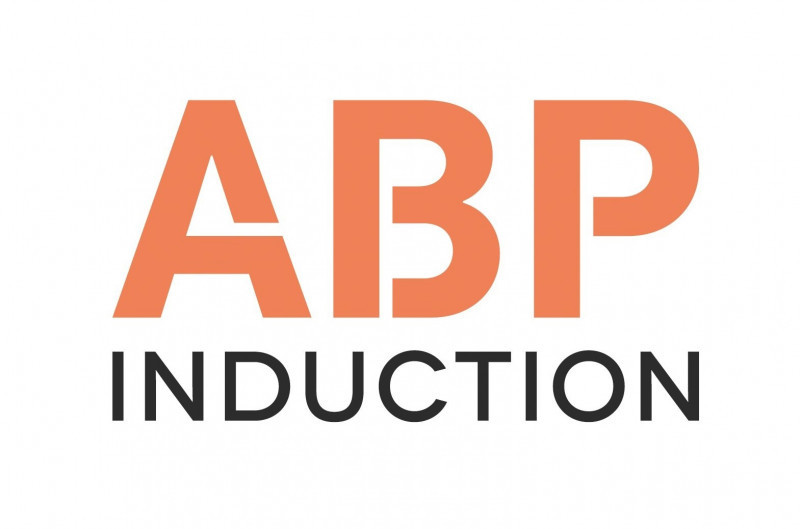
Schlagworte
AluminiumDigitalisierungDruckgussRecycling