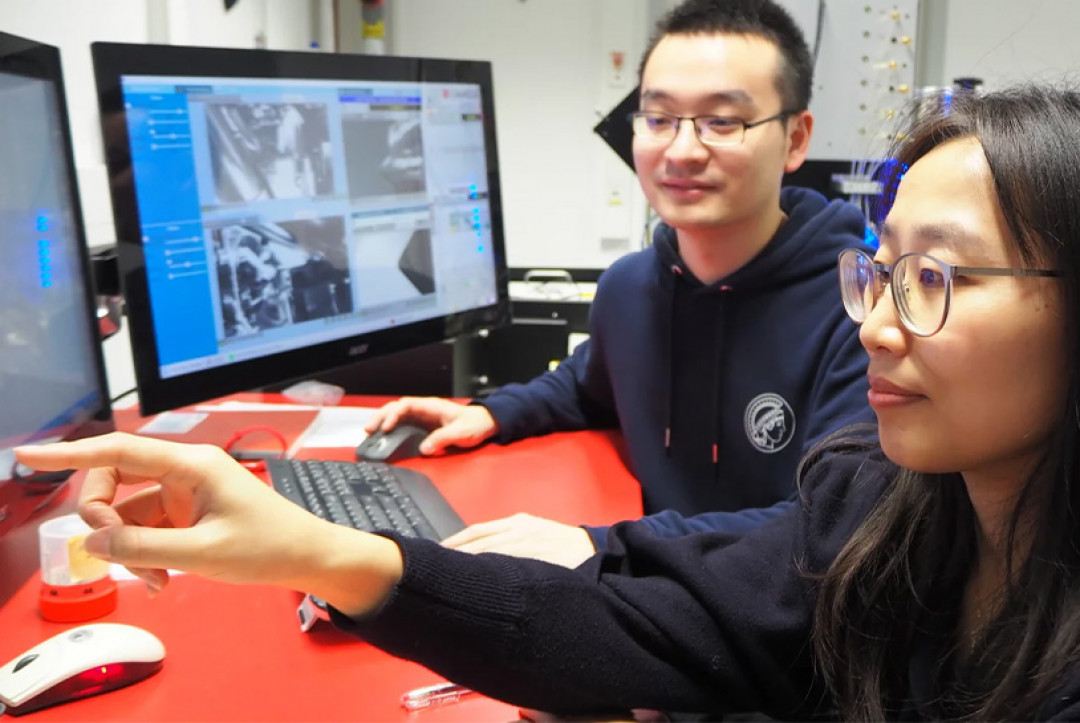
Ein Forschungsteam des Max-Planck-Instituts für Nachhaltige Materialien hat eine neue Designstrategie zur Metallproduktion entwickelt. Ihr Konzept vereint Gewinnung, Herstellung, Mischung und Verarbeitung in einem einzigen Prozessschritt.
Die Produktion von jährlich etwa zwei Milliarden Tonnen Metallen ist für 10 Prozent der globalen CO2-Emissionen verantwortlich. Allein um eine Tonne Eisen zu produzieren, werden zwei Tonnen CO2 ausgestoßen. Bei der Produktion von einer Tonne Nickel fallen sogar 14 Tonnen oder mehr CO2 an. Dabei sind Eisen und Nickel für die Luft- und Raumfahrt, den Transport von flüssigem Wasserstoff und für die Energiewende von entscheidender Bedeutung. Aus ihnen entstehen sogenannte Invarlegierungen, die aufgrund ihrer geringen thermischen Ausdehnung ideal für diese Anwendungsfelder sind.
Wie lassen sich solche Legierungen CO2-frei und mit geringem Energieverbrauch herstellen? Dazu haben Wissenschaftler des Max-Planck-Instituts für Nachhaltige Materialien (MPI-SusMat) eine radikal neue Strategie entwickelt. In einem einzigen Prozessschritt und Reaktor werden die Metallgewinnung, das Legieren, also das Mischen, und die thermomechanische Verarbeitung integriert, sodass am Ende das fertige Material entsteht. Diese Methode ermöglicht die direkte Umwandlung von Erzen in anwendungsfähige Produkte.
Kompakt-Metallurgie spart bis zu 40 Prozent Energie
Die konventionelle Legierungsproduktion ist seit mehr als 6000 Jahren in der Regel ein dreistufiger Prozess: Zuerst wird Sauerstoff aus den Erzen entfernt, um das reine Metall zu erhalten. Dieser Schritt heißt Reduktion: Eisen- oder Nickelerz werden somit zu Metall reduziert. Danach werden mehrere Metalle oder andere Elemente erhitzt und verflüssigt, um sie miteinander zu vermischen, das sogenannte Legieren. Zum Schluss wird die Legierung thermomechanisch bearbeitet, also geschmiedet, gewalzt, erhitzt, um die gewünschten Eigenschaften zu erzielen. Jeder dieser Schritte ist energieintensiv, vor allem da die Erze und Metalle mehrmals erhitzt, verflüssigt und wieder abgekühlt werden. Zudem wird bisher Kohlenstoff als Energieträger und Reduktionsmittel genutzt, was zu erheblichen CO2-Emissionen führt.
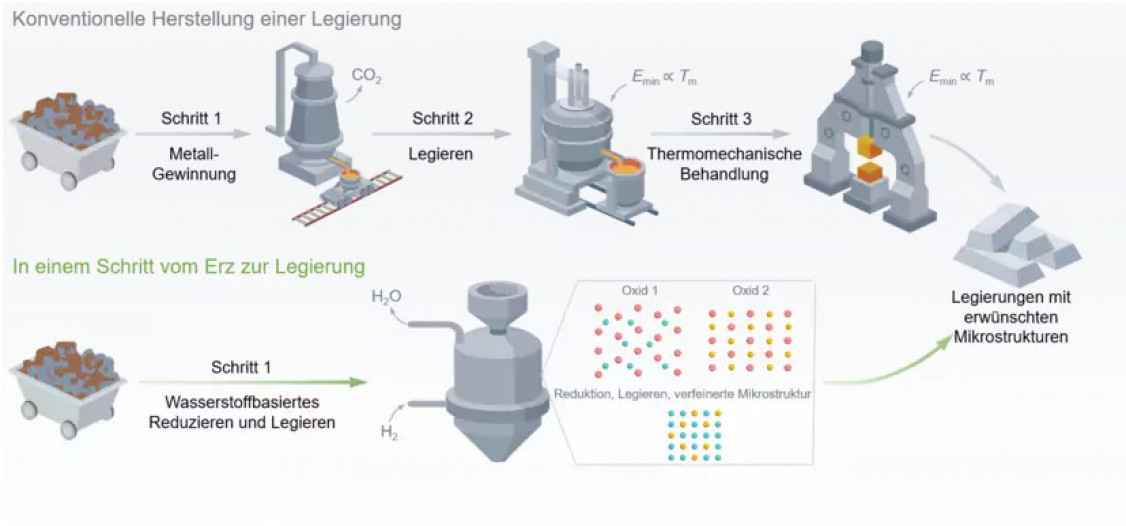
"Der Schlüsselgedanke besteht darin, die Thermodynamik und Kinetik jedes beteiligten Elements zu verstehen und Elemente mit ähnlichem Reduktions- und Mischverhalten bei etwa 700°C zu verwenden", erklärt Shaolou Wei, Humboldt-Forschungsstipendiat am MPI-SusMat . "Bei 700°C können wir den Sauerstoff aus den Erzen entfernen und die so entstehenden Metalle in einem einzigen Schritt legieren, und zwar ohne das Material verflüssigen zu müssen. Dies spart enorme Mengen Energie."
Im Gegensatz zu herkömmlichen Methoden, bei denen Erze mit Kohlenstoff reduziert werden, verwenden die Max-Planck-Wissenschaftler Wasserstoff als Reduktionsmittel. "Die Verwendung von Wasserstoff anstelle von Kohlenstoff bringt vier entscheidende Vorteile mit sich", so Dierk Raabe, geschäftsführender Direktor des Instituts. Erstens entstehe bei der wasserstoffbasierten Reduktion nur Wasser als Nebenprodukt und kein CO2. Zweitens würden direkt reine Metalle beziehungsweise sogar gleich deren fertige Legierungen gewonnen. "Man muss also keinen verbliebenen Kohlenstoff aus dem Endprodukt entfernen. Dies spart Zeit und Energie", sagt Raabe. Drittens führen die Forscher den Prozess bei vergleichsweise niedrigen Temperaturen und in der festen Phase, also nicht in flüssigen Schmelzen, durch und sparen damit erneut Energie. Viertens vermeiden sie das häufige Abkühlen und Wiedererhitzen, das für herkömmliche metallurgische Prozesse charakteristisch ist - und können auch in diesem Bereich Energie sparen.
Insgesamt werde der Energieverbrauch im Vergleich zur konventionellen Metallurgie um bis zu 40 Prozent gesenkt, resümiert das MPI-SusMat. Dem Institut zufolge haben die mit dieser Methode hergestellten Invar-Legierungen dieselbe geringe Wärmeausdehnung wie die konventionell hergestellten Invar-Legierungen. Zudem böten sie aufgrund der verfeinerten Mikrostruktur, die aus diesem Verfahren resultiert, sogar eine bessere mechanische Festigkeit.
Vom Labor in die Industrie
Die Max-Planck-Wissenschaftler konnten zeigen, dass die Herstellung von Invar-Legierungen durch ein schnelles, CO2-freies und energieeffizientes Verfahren vielversprechend ist. Um diese Methode vom jetzigen Labormaßstab zur industriellen Anwendung zu bringen, müssen die Wissenschaftler drei zentrale Herausforderungen überwinden.
Erstens: in der jetzigen Forschungsarbeit verwendeten die Wissenschaftler reine Oxide. In der Industrie hingegen werden günstigere, verunreinigte Oxide verwendet. Das heißt für das Max-Planck-Team, dass sie ihren Prozess anpassen müssen, um weiterhin dieselbe Qualität der Legierungen zu erhalten. Zweitens: Die Verwendung von reinem Wasserstoff im Reduktionsprozess ist zwar effektiv, aber für industrielle Anwendungen kostspielig. Das Team führt nun Experimente mit niedrigeren Wasserstoffkonzentrationen bei höheren Temperaturen durch, um ein optimales Gleichgewicht zwischen Wasserstoffverbrauch und Energiekosten zu finden und den Prozess für die Industrie wirtschaftlicher zu machen. Drittens: Für industrielle Zwecke werden sehr fein porige Metalle gebraucht, die mit der neuen Methode der Max-Planck-Wissenschaftler nicht direkt, sondern mit einem zusätzlichen Schritt - dem Sintering - hergestellt werden müssten.
Das neue Verfahren ist nicht nur für Invar-Legierungen interessant, sondern für alle Legierungen auf der Basis von Eisen, Nickel, Kupfer oder Kobalt. Im Fokus des Düsseldorfer Max-Planck-Teams stehen jetzt auch komplexe Legierungen, die aus mehr als fünf verschiedenen Elementen bestehen, sogenannte Hoch-Entropie-Legierungen. Diese werden zum Beispiel in Flugzeugturbinen und Elektromotoren eingesetzt. Eine weitere vielversprechende Richtung könnte die Verwendung von metallurgischen Abfällen anstatt reiner Oxide sein.
Die Forschung wurde durch ein Stipendium der Alexander von Humboldt-Stiftung für Shaolou Wei und einen European Advanced Research Grant von Dierk Raabe finanziert. Ihre Ergebnisse haben die Forscher unter dem Titel "One step from oxides to sustainable bulk alloys" in der Fachzeitschrift Nature veröffentlicht.
Beitragsbild: Yasmin Ahmed Salem, Max-Planck-Institut für Nachhaltige Materialien GmbH