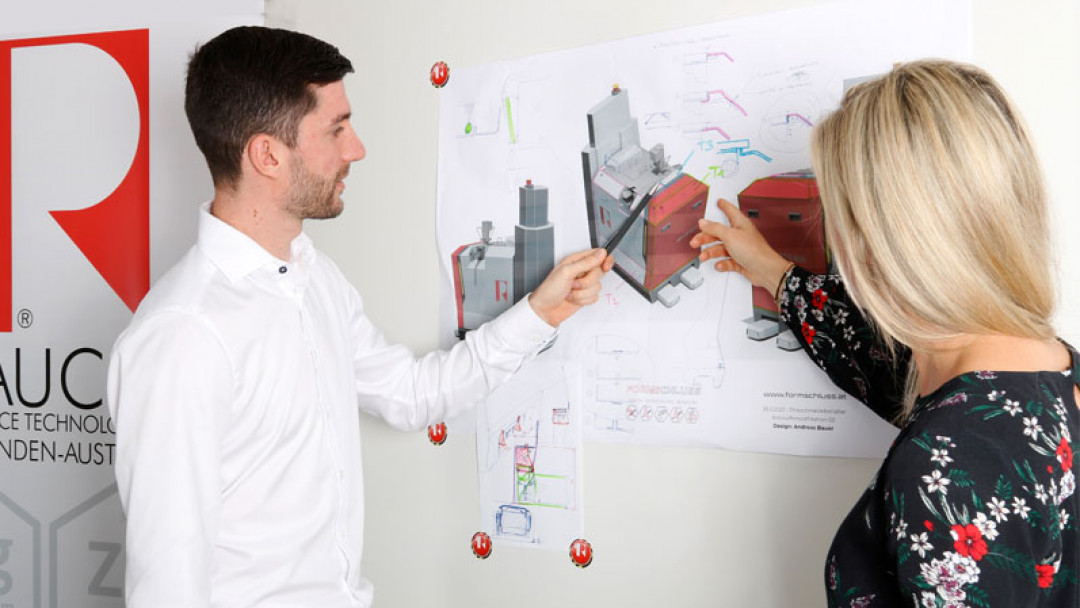
Magnesiumlegierungen werden in Schmelzöfen mit extremer Hitze und großen Temperaturschwankungen verarbeitet. Versagt ihr Herzstück, der Tiegel, steht die gesamte Gusszelle still. RAUCH Furnace Technology (FT) hat dieses Risiko drastisch gesenkt, indem ein Digitaler Zwilling den Tiegelzustand überwacht. Probleme werden so früh erkannt und Ausfallzeiten durch kontrollierte Maßnahmen minimiert.
Was verbindet Wasserkraft und Gießereitechnik? Es sind traditionsreiche Branchen, bei denen große Kräfte wirken. Sie gelten zudem als konservativ und werden bei Themen wie der digitalen Transformation gerne unterschätzt. Zu Unrecht, denn z.B. VERBUND, der Betreiber der großen österreichischen Wasserkraftwerke, sichert schon seit Jahren die Einsatzbereitschaft seiner Anlagen digital ab.
Dazu füttern echte Sensoren die digitalen Abbildungen kritischer Bauteile mit realen Lastdaten. Virtuelle Sensoren an kritischen Stellen erlauben die Auswertung der auftretenden Belastung und die Bewertung des Verschleißes. Werden definierte Grenzwerte erreicht, die einen Ausfall ankündigen, können sich die Techniker ohne Komplikationen um Wartung oder Austausch kümmern.
Viele reden noch von „Digitalen Zwillingen“ – VERBUND hat sie gemeinsam mit den Partnern ITficient und CADFEM bereits realisiert.
Ein weiterer Link zur Gießereitechnik entstand 2019 auf der CADFEM Conference in Linz. Die Vorstellung des VERBUND-Projektes beeindruckte Florian Sipek, Physiker beim österreichischen Spezialisten für Schmelztechnik RAUCH-FT so sehr, dass er es auf die eigenen Produkte übertrug und mit dieser Idee auch seine Kollegen begeisterte. Was nicht verwundert, denn Innovation und Mut zu neuen Wegen, gehören zur DNA von RAUCH-FT. Sie haben das hochspezialisierte Unternehmen an die Weltspitze in der Schmelztechnik geführt, bei Mg-Schmelzanlagen gilt es als Weltmarktführer. Das verpflichtet.
Die Digitalisierung der Extreme
Schmelzöfen haben es „in sich“: Wenn darin Metalle geschmolzen, recycelt und auflegiert werden, ist es bis zu 2000°C heiß, Gasströme haben Geschwindigkeiten von 1.000 km/h, Belastungswechsel sind die Regel.
Mehr Ausfallsicherheit der Schmelzanlagen ist für die Betreiber viel wert. Denn steht eine Anlage plötzlich still, drohen neben den Schäden am Ofen empfindliche Produktionsverzögerungen oder -ausfälle. Schlimmstenfalls kommt es zur Gefährdung der Mitarbeitenden.
Die Idee: Digitale Zwillinge sollen solche Gefahren erheblich reduzieren, indem sie Probleme früh sichtbar machen. Darüber hinaus will RAUCH-FT den Kunden im laufenden Betrieb wertvolle Erkenntnisse liefern, d.h. sie auf Wartungs- oder Reinigungsbedarfe hinweisen.
Daten und Simulationswissen perfekt orchestriert
In der Gießereitechnik gibt es noch keine vergleichbaren Ansätze. RAUCH-FT ist die Herausforderung – wie schon die Impulsgeber von VERBUND - mit ITficient und CADFEM angegangen. ITficient für Datenmanagement, Geschäftsmodell- und IT-Architektur, CADFEM für die Simulation, von Strömung über verschiedene transiente und nichtlineare strukturmechanische Anwendungen und Sensitivitätsstudien bis hin zu Systemsimulationen inklusive Zustandsüberwachung.
RAUCH-FT war gerüstet für den Digitalen Zwilling. Zum einen werden bereits viele Anlagen und Komponenten simuliert. Meist geht es um Strömungsmechanik, das Spektrum reicht von transienten Abkühl- und Aufheizprozessen über Vorgänge in Dosier- oder Strömungspumpen bis hin zu chemischen Reaktionen.
Zum anderen ist neben einer leistungsfähigen IT-Infrastruktur über die Fernwartung schon ein großer Datenpool zur Anlage vorhanden. Dessen Auswertung liefert wertvolle Erkenntnisse zum Betrieb der Öfen, die ebenfalls in den Digitalen Zwilling einfließen.
Wie lange hält der Tiegel durch?
Das ideale Bauteil für die erste praktische Umsetzung ist der Tiegel. Die Schweißkonstruktion aus Stahl ist hoch belastet: „2000°C heißes Rauchgas außen, korrosives Schutzgas und hydrostatischer Druck von bis zu 4t schwerer Schmelze innen“, erklärt Florian Sipek. „Hinzu kommen extreme Temperaturgradienten, die Strahlungsleistung der Flamme und hohe Geschwindigkeiten bei einer inhomogen verteilten Strahlungsenergie“.
Versagt der Tiegel, steht das System still. Die Wartung basiert üblicherweise auf Erfahrungswerten, was funktionieren kann - in einer idealen Welt. Sobald aber Unregelmäßigkeiten in den Prozessen oder bei der Handhabung auftreten, droht ein Versagen und damit Folgeschäden. „Genau dann zeigt sich der Wert der prädiktiven Wartung“, fasst Florian Sipek zusammen.
Beispiel
Die Idee der digitalen Zustandsüberwachung des Tiegels ist ein Zusammenspiel aus realen Messwerten und virtueller Sensorik. Durch die in der Schmelze auftretende Segregation, d.h. Absetzung bestimmter Verbindungen, bildet sich ein Sumpf am Tiegelboden. Er führt lokal zu einer Änderung der Strömungsbedingungen und der Materialparameter Wärmeleitung und Wärmekapazität, was den Wärmetransport am Tiegelboden von Ofenraum zu Schmelze stört. In Verbindung mit der inhomogenen Temperaturverteilung an der Außenwand entstehen hohe Spannungen im Tiegel.
Die Sumpfmenge ist demnach eine wichtige Kenngröße für eine korrekte Aussage zur Echtzeit-Belastung des Tiegels und damit auch für die Verlässlichkeit der prädiktiven Wartung. Aufgrund der Umgebungsbedingungen im Tiegel und im Ofen ist die Nutzung realer Sensorik für die Temperaturmessung kaum möglich. Daher sah das Konzept von CADFEM virtuelle Sensoren für die Simulationen vor. Zusammen mit einer aus den Temperaturen berechneten Sumpfmenge und den Prozessparametern kann so mit wenigen Messstellen und Eingangsgrößen auf eine lokale Belastung am Tiegel geschlossen werden.
Für die Vorhersage der verbleibenden Standzeit des Tiegels sind die präzise Modellierung der Temperaturverteilung im Ofenraum durch Computational Fluid Mechanics (CFD) und der Spannungen an den Schweißnähten (Strukturmechanik, FEM) essenziell. CFD-seitig wird für eine korrekte Vorhersage der Flammentemperatur, der Wärmestrahlung und des Impulseintrags eine Verbrennungssimulation des Brenners und des Ofenraums durchgeführt. Auf Basis der CFD-Ergebnisse werden eine Temperaturfeld- und eine Spannungsanalyse durchgeführt, mit der Schmelze als variable Wärmesenke, um das Aufschmelzen eingeworfener Barren abzubilden.
In jeder Infrastruktur
Der Digitale Zwilling muss die individuellen Voraussetzungen beim Endkunden adaptieren – bei den abzubildenden Prozessen genauso wie bei der genutzten IT-Infrastruktur. Ein Konzept zur IT-Integration ist ein wichtiger Baustein bei der Umsetzung, es geht u.a. um den Umgang mit Sensordaten, den Betrieb des Zwillings, Security- und Netzwerk-Themen. ITficient konnte bei RAUCH-FT auf einen Datenpool und eine IoT-Plattform aufsetzen.
Die notwendigen Microservices – Entgegennahme der Sensor- und Maschinendaten, Berechnung der virtuellen Sensoren, Modelle und Prozesse, Datenhaltung und -auswertung sowie Visualisierung von Ergebnissen – wurden dort so integriert, dass IT-Ressourcen optimal ausgeschöpft wurden, keine Insellösungen entstanden sind und RAUCH-FT die volle Kontrolle über alle Vorgänge in der Hand behalten hat, d.h. auch, sie eigenständig weiterentwickeln kann.
ITFICIENT und CADFEM
Ein leistungsfähiger Digitaler Zwilling hat zwei wesentliche Ebenen: Akkurate Simulationen und eine zuverlässige IT-Infrastruktur. Erfolgreich wird das Projekt dann, wenn beide Seiten ineinandergreifen. Dies ist bei RAUCH-FT auch deshalb gelungen, weil mit CADFEM und ITficient zwei Partner eingebunden wurden, die in ihrem jeweiligen Bereich viel Erfahrung mitbringen. Gleichzeitig stehen sie in engem und vertrauensvollem Austausch, sind sie doch beide als Unternehmen der CADFEM Group auch organisatorisch eng miteinander verbunden.
Denn der Tiegel war erst der Startpunkt – RAUCH-FT will die erworbenen Fähigkeiten zu Planung, Aufbau und Management eines Digitalen Zwillings skalieren und künftig alle relevanten Bauteile wie Dosierpumpen, Beheizungssysteme oder Umwälzpumpen und ganze Anlagen mit digitalen Lösungen zur prädiktiven Wartung zur Verfügung stellen und damit in der Gießereitechnik und bei Kunden wie Georg Fischer Maßstäbe setzen.
Diese Vision endet nicht bei den eigenen Produkten. Eine klassische Druckgusszelle besteht nicht nur aus dem Schmelzofen, sondern aus weiteren Komponenten verschiedener Hersteller. Seien es Roboter, Presse, Heiz-/Kühlgerät oder die Druckgussmaschine selbst - in der Gießerei hat beinahe jedes Bauteil das Potenzial für einen Digitalen Zwilling.
Schlagworte
CADDatenmanagementDigitalisierungDruckgussEisenGussKonstruktionMagnesiumModellierungProduktionSchmelzanlagenSchmelzenSicherheitSimulationStahl