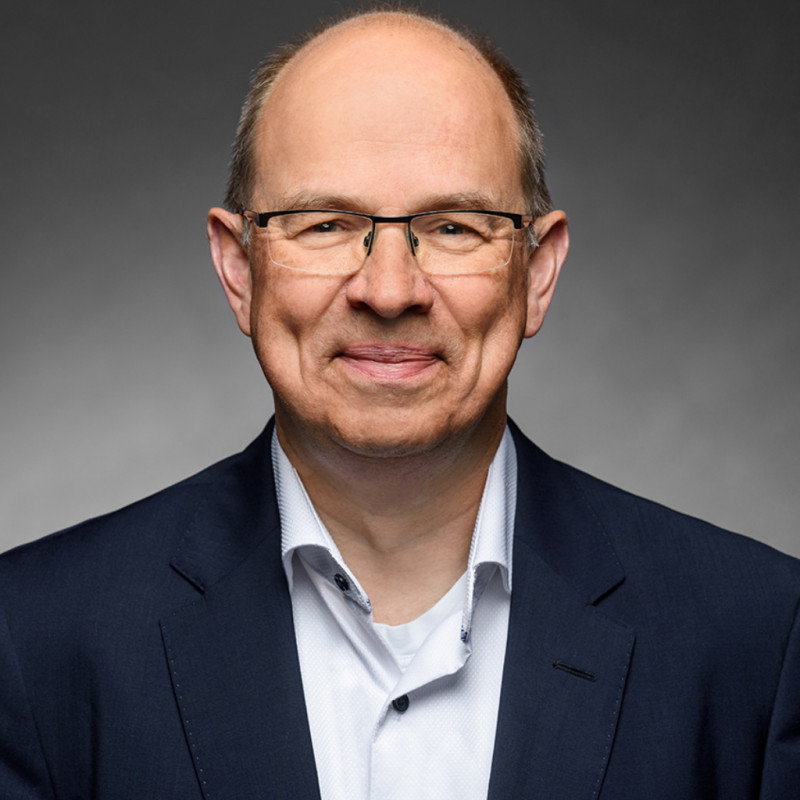
Industrie 4.0 hat eine Schlüsselrolle bei der systematischen Sicherung und Weitentwicklung der Wertschöpfung in Deutschland. Dabei lassen sich Potenziale zur Überwindung aktueller industrie- und gesellschaftspolitischer Herausforderungen heben. Im Interview spricht Dr. Marc Hüske über Nachhaltigkeit, technologische Souveränität, Interoperabilität und über die Rolle des Menschen. Hüske ist Mitglied im von acatech koordinierten Forschungsbeirat Industrie 4.0 und Leiter des Forum Manufacturing-X des VDMA.
Herr Hüske, die Klimakrise macht die Notwendigkeit von Innovationen im Kontext der ökologischen Nachhaltigkeit bei der Schaffung und Nutzung von Produkten und Dienstleistungen über den gesamten Lebenszyklus hinweg deutlich. Welche konkreten Schritte bzw. Ansätze sind dabei über die Erforschung und Implementierung von nachhaltigen Industrie 4.0-Lösungen zu verfolgen?
Die aktuellen Herausforderungen sind immens und angesichts der Klimakrise sollten wir uns die technologischen Möglichkeiten zunutze machen, die sich uns durch Digitalisierung und Automatisierung im Hinblick auf ökologische Nachhaltigkeit bieten – unterstützt durch das exponentiell anwachsende und uns zur Verfügung stehende Datenvolumen – auch eine Folge der EU-Datenverordnung. Entlang des gesamten Lebenszyklus von Produkten, also von der Rohstoffgewinnung bis zum Recycling, werden neue datenbasierte Geschäftsmodelle entstehen, was nachweislich die Resilienz, Nachhaltigkeit und Wettbewerbsfähigkeit der Industrie befördert. Die Folge sind eine höhere Transparenz, effiziente Ressourcennutzung und die Möglichkeit, schneller auf Störungen in den Lieferketten zu reagieren. Gerade bei wichtigen Themen wie Dekarbonisierung oder Kreislaufwirtschaft spielt eine nachhaltige Prozessoptimierung durch z. B. prozessübergreifende Regelketten eine große Rolle. Die Implementierung von Industrie 4.0-Technologien hilft beispielsweise auch dabei, durch präzisere Fertigungsmethoden den Materialverbrauch zu reduzieren. Durch Geschäftsmodelle, die auf der Bereitstellung von Dienstleistungen anstelle des Verkaufs von Produkten basieren, kann der Ressourcenverbrauch reduziert und der Lebenszyklus von Produkten verlängert werden, man denke nur an bestimmte Leasing- oder Sharing-Modelle. Auch im Bereich Energieeffizienz und Emissionsreduktion wirken sich beispielsweise intelligente Energiemanagementsysteme zur Überwachung und Optimierung des Energieverbrauchs in Echtzeit so aus, dass der Energieverbraucht minimiert und die Nutzung erneuerbarer Energiequellen maximiert werden kann.
Nationale und globale Einflüsse auf das Wirtschaftssystem haben die Relevanz von Industrie 4.0 weiter verstärkt. So zeigten unter anderem die Corona-Pandemie sowie der russische Angriffskrieg gegen die Ukraine in Verbindung mit der Knappheit wichtiger Ressourcen die Verletzlichkeit bestehender Wertschöpfungsketten und -netzwerke auf. Gleichzeitig scheint in verschiedenen Bereichen die technologische Souveränität des deutschen Wirtschaftsstandorts zunehmend im internationalen Wettbewerb verloren zu gehen. Wie kann durch Industrie 4.0 die Resilienz der Wertschöpfung sowie die technologische bzw. strategische Souveränität von Deutschland und Europa gesteigert werden und welche Rolle spielen dabei interoperable, digitale Ökosysteme?
Gerade weil die technologische Souveränität ein so wichtiges Thema in der EU und Deutschland ist, um sich im internationalen Wettbewerb vor allem gegenüber den USA und China strategisch behaupten zu können, braucht es Initiativen wie Industrie 4.0 sowie den Aufbau einer europäischen Cloud-Infrastruktur wie GAIA-X und Datenrauminitiativen wie Manufacturing-X. Interoperable, digitale Ökosysteme spielen eine ganz zentrale Rolle, wenn es darum geht, durch Industrie 4.0 die Resilienz der Wertschöpfung und die Souveränität unseres Wirtschaftsstandortes zu stärken. Kommt es durch Pandemie, Krieg oder andere äußere Einflüsse zu plötzlichen Veränderungen bei der Nachfrage und der Ressourcenverfügbarkeit wird den Unternehmen ein hohes Maß an Flexibilität abverlangt. Durch den industriellen Datenraum, welcher eine vertrauenswürdige Infrastruktur für das Teilen von Daten bereitstellt, werden Unternehmen in die Lage versetzt, ihre Lieferketten und Produktionsprozesse datengetrieben flexibel und schnell anzupassen. Wertschöpfungsketten werden somit robuster und generell weniger anfällig für Unterbrechungen, wenn durch Echtzeit-Datenanalyse potenzielle Störungen frühzeitig erkannt und effizient bewältigt werden können. Mit Manufacturing-X wird die nahtlose Integration verschiedener industrieller Systeme über Unternehmens- und Ländergrenzen hinweg ermöglicht, was nicht nur die Zusammenarbeit, sondern auch neue Geschäftsmodelle und Wertschöpfungspotenziale fördert. Dies gilt gerade auch im Bereich von Schlüsseltechnologien wie KI und IoT. Die Datenhoheit bleibt beim Unternehmen, so dass jedes Unternehmen die vollen Vorteile aus seinen eigenen Daten schöpfen kann. Offene Standards und Interoperabilität sorgen dafür, dass die Zusammenarbeit insbesondere innerhalb Europas und mit internationalen Partnern funktioniert, was Abhängigkeiten reduziert und die europäische Position im globalen Wettbewerb stärkt, wie auch die technologische Souveränität.
Im Kontext von Industrie 4.0 wird von Beginn an die optimale Einbindung und Unterstützung von Menschen durch die entsprechende Gestaltung von Arbeits- und Produktionsprozessen adressiert. Wie kann auch in Zukunft konkret sichergestellt werden, dass der Mensch weiterhin im Zentrum dieser Entwicklung steht?
Das ist ein Blick in die Glaskugel, aber ich bin überzeugt davon, dass sich Arbeits- und Produktionsprozesse nicht völlig losgelöst vom Menschen entwickeln werden. Es wird ein wie auch immer gestaltetes Miteinander geben. Eine Rolle werden sicher Augmented Reality und Virtual Reality spielen, wenn es um die Interaktion zwischen Mensch und Maschine geht. Beide Technologien werden dabei helfen, komplexe Prozesse zu visualisieren und verständlicher zu machen. Ein Einsatz im Bereich von Schulungen oder bei Service-Mitarbeitern ist hier beispielsweise denkbar. Unerlässlich ist aber, dass die Beschäftigten über die notwendigen Kompetenzen verfügen, um mit neuen Technologien wie KI, Robotik und Datenanalytik umzugehen. Lebenslanges Lernen, Neugier und die Bereitschaft, sich immer wieder auf Neues einzulassen, gehören dabei zur Grundausstattung. Aufgabe von Führungskräften ist es, diesen Transformationsprozess konstruktiv zu begleiten. Produktionssysteme auf der anderen Seite sollten so flexibel und anpassungsfähig gestaltet sein, dass sie im Hinblick auf sich immer schneller ändernde Marktbedingungen und Kundenanforderungen entsprechend ausgerichtet werden können. Durch die Analyse von Daten aus Produktionsprozessen können Arbeitsabläufe nicht nur optimiert werden, sondern kann auch dafür gesorgt werden, dass auf die individuellen Stärken und Schwächen der Mitarbeiter eingegangen wird, was dem Miteinander von Mensch und Maschine entgegenkommt.
Schlagworte
AutomatisierungDigitalisierungEnergieeffizienzFertigungForschungGestaltungIndustrie 4.0LieferketteNachhaltigkeitProduktionProzessoptimierungRecyclingRobotik