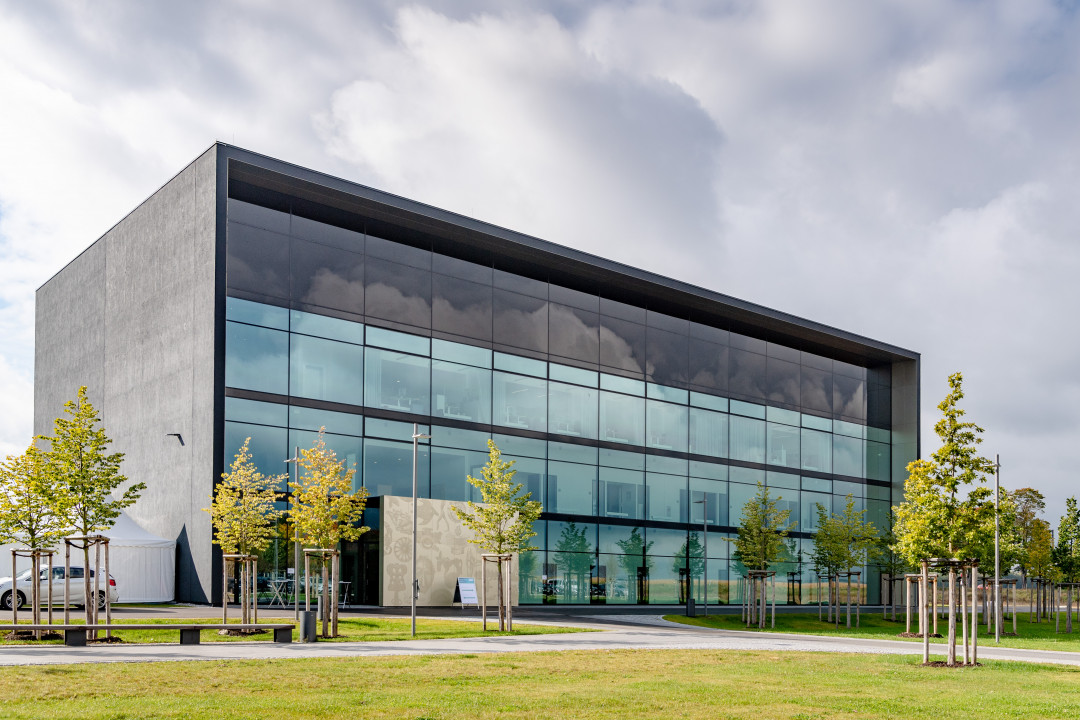
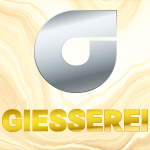
Aufbruch in die Zukunft: Das kürzlich eingeweihte Gießereitechnikum des Fraunhofer IGCV (Institut für Gießerei-, Composite- und Verarbeitungstechnik) bietet künftig der Forschung an jedem Schritt des Gießvorgangs eine neue Heimat – von der Formherstellung bis zum Veredelungsprozess. Im Fokus der Forscher stehen vor allem die Bereiche Digitalisierung von Produktionsprozessen sowie die Eigenschaftsoptimierung von Bauteilen. Prof. Dr.-Ing. Wolfram Volk, Institutsleiter des Fraunhofer IGCV und Verantwortlicher für den Wissenschaftsbereich Gießereitechnik, spricht im Interview über den neuen Standort, über Forschungsziele sowie aktuelle und künftige Herausforderungen an Forschung und Industrie.
Herr Prof. Volk, was waren die maßgeblichen Gründe für die Wahl des neuen Forschungsstandortes in Garching?
Das 2016 gegründete Fraunhofer IGCV hat den Hauptsitz in Augsburg, neu ist jetzt der Forschungsstandort für die Gießereitechnik in Garching, wo sich ja auch mein Lehrstuhl befindet. Das war eine wichtige Standortentscheidung, die neben politischen Aspekten – das Land Bayern wollte gerne ein produktionstechnisches Institut im Regierungsbezirk Schwaben – letztlich auch logistische Gründe hatte. Sowohl meine Kollegen Prof. Drechsler und Prof. Daub, mit denen ich gemeinsam das Institut leite, als auch ich haben ihre Lehrstühle am Garchinger Campus. Zudem ist ein Großteil unserer technischen Studierenden im Münchener Raum anwesend. Neben dem Fraunhofer IGCV befindet sich auf dem Gelände noch das Institut für angewandte und integrierte Sicherheit (AISEC), aktuell in der Konzeptphase ist das künftige Institut für Kognitive Systeme IKS. Unser Standort befindet sich in unmittelbarer Nähe zum Campus der TU München. Die bessere Anbindung und Vernetzung zur Nutzung bestehender Strategie- und Synergieeffekte spielte hierbei also auch eine entscheidende Rolle.
Stichwort „Vernetzung“: Welche Kooperationen des Fraunhofer IGCV mit anderen Forschungsstandorten gibt es aktuell?
Betrachtet man die universitären Gießereiinstitute in Deutschland, so stellt man fest, dass deren Anzahl recht überschaubar ist. Wir haben zum einen die RWTH Aachen als größtes Institut, dazu kommen Freiberg, Clausthal, Kassel und der neue Lehrstuhl in Erlangen, wobei letzterer aber gerade erst mit der Forschungstätigkeit begonnen hat. Dazu kommen natürlich auch noch einige Fachhochschulen. 2013 haben wir die akaGuss (Akademische Interessensgemeinschaft Gießereitechnik) gegründet, um damit einen informellen Austausch zu ermöglichen. Ich sage hier bewusst „deutschsprachig“, weil in der Gemeinschaft auch der österreichische Standort Leoben und die DTU Kopenhagen mit einem ebenfalls Deutsch sprechenden Kollegen integriert sind. Wir pflegen hier einen regelmäßigen Austausch, und es gibt gemeinsame Veröffentlichungen. Wenn es sich ergibt, unterstützt man sich natürlich gegenseitig. Wir wissen immer, was die anderen tun und haben ein freundschaftliches Verhältnis.
Inwiefern ergänzen sich hierbei die Grundlagen- und die angewandte Forschung?
Da habe ich ein bisschen meine eigene Philosophie. Die Grundlagenforschung betreiben wir hauptsächlich am Lehrstuhl für Umform- und Gießereitechnik in München. Ich betreue hier auch derzeit zehn Doktoranden im Bereich der Gießereitechnik. Unser Schwerpunkt liegt hier auf durch die DFG (Deutsche Forschungsgemeinschaft) geförderte Projekte. Unser Anspruch ist es immer, Forschung von den Grundlagen bis zur industriellen Anwendung durchzuführen – sowohl am Lehrstuhl der TU, als auch beim Fraunhofer IGCV. Das ist für uns als Teil der Produktionstechnik ein zwingendes Muss: Nur, wenn wir den Spiegel vorgehalten bekommen, was auch wirklich in der Industrie ankommt und welche Bedarfe bestehen, können wir zielgerichtete Forschung betreiben. Anderenfalls ist immer der „akademische Elfenbeinturm“ recht nahe.
Wie beurteilen Sie den Forschungsstandort Deutschland im aktuellen internationalen Vergleich?
Es gibt derzeit drei führende Nationen auf dem Gebiet der produktionstechnischen Forschung: Deutschland, Japan und die USA. China ist stark im Kommen. Wir beobachten Letztere mit großem Interesse, allerdings ist das dortige Geschehen durch die große Masse der verschiedenen Angebote noch schwer durchschaubar. Es gibt in China schon einige sehr gute Universitäten, und wir in Deutschland sollten diese Entwicklung keinesfalls „vom hohen Ross“ beurteilen, denn entscheidend sind immer die dortigen Märkte, d. h. wie sieht die lokale Industrie aus? In Deutschland und Europa haben wir im Bereich der innovativen Produktionstechnik nach wie vor eine führende Rolle. Auf dem asiatischen Markt trifft dies eher auf Japan zu, zunehmend ergänzt durch China und Südkorea. Was die USA betrifft, da hängt die Situation immer stark von der jeweiligen politischen Lage ab. Dort wird die finanzielle Förderung mal gepusht, dann wieder ausgebremst. Unsere amerikanischen Kollegen vermissen eine Kontinuität, die wir in Deutschland in den vergangenen Jahrzehnten sowohl für die Grundlagen- als auch für die anwendungsbasierte Forschung nahezu durchgängig hatten. Dadurch konnten wir uns im internationalen Wettbewerb eine entsprechend starke Position erarbeiten.
Jetzt sind wir ja schon beim Thema Politik angekommen. Deutschland hat gerade gewählt, eine neue Koalition auf Bundesebene macht sich an die Arbeit. Wie bewerten Sie hier mögliche Chancen und Risiken aus der Sicht der Forschung?
Wenn man sich die Wahlprogramme anschaut, hat man bei der FDP ein klares Bekenntnis zum Industriestandort Deutschland gefunden. Bei den Grünen stehen natürlich die Themen Nachhaltigkeit und Klimafreundlichkeit weit oben auf der Agenda. Die SPD betont traditionell auch die sozialen Aspekte der Industriearbeiterschaft. Ich persönlich denke nicht, dass wir durch den politischen Wechsel eine disruptive Veränderung zum Guten oder zum Schlechten zu erwarten haben. Wir haben genug Weitsicht, um die erfolgreichen Dinge weiterführen zu können. Man muss jetzt natürlich abwarten, bei welchen Parteien und Personen die einzelnen Ministerien landen und wie dort die Schwerpunkte gesetzt werden. Das ist momentan natürlich noch etwas Kaffeesatzleserei. Dennoch vertraue ich darauf, dass wir auch in Zukunft auf die nötige Kompetenz in den entscheidenden Positionen setzen können. Insofern: Ein Neuanfang bedeutet immer gewisse Chancen und gleichzeitig auch Unwägbarkeiten, die noch nicht absehbar sind. Für übertriebene Euphorie besteht kein Anlass, aber auch nicht für Pessimismus. Ich gehe davon aus, dass wir hier weiterhin mit Kontinuität rechnen können.
Sprechen wir über Ihre aktuellen Forschungsinhalte. Was ist Ihnen besonders wichtig, in welche Richtung soll es perspektivisch gehen?
Hier wäre als erster Punkt das Thema Digitalisierung zu nennen, also der digitale Wandel und die zunehmende Automatisierung der Produktion. Hier haben wir im Gießereiwesen noch einen recht großen Nachholbedarf. Das liegt unter anderem auch an den oftmals eher mittelständisch geprägten Industriebetrieben. Wir brauchen hier Lösungen, um von den eingehenden Rohstoffen bis zum fertigen Produkt eine durchgehende Prozessmodellierung und -optimierung sowie Informationsweitergabe zu erreichen. Wir arbeiten intensiv daran, die Gießerei systematisch in das 21. Jahrhundert zu führen.
Könnte man hier ein konkretes Beispiel für ein entsprechendes Projekt nennen?
Beim Kokillengießverfahren arbeiten wir derzeit an einem so genannten intelligenten Kernregal, mit dem kontinuierlich Umgebungstemperaturen registriert werden. Über den Zeitstempel des Kerns können wir eine direkte Zuordnung von der Herstellung des Kerns bis zum Gießverfahren erreichen, um dadurch Ursache-Wirkungsketten bei eventuell auftretenden Qualitätsproblemen zu identifizieren. Weiterhin beschäftigen wir uns mit den Themen Softsensorik und Temperaturmanagement beim Kokillen- und Druckgießen. Die Problematik besteht aktuell darin, dass es schwierig ist, den Temperaturübergang, die Kornfeinung und damit die Gefügeeigenschaften prognostizierbar zu machen. Mittels verbesserter Sensorik können wir bessere Eigenschaftsprognosen hinsichtlich der Schwankungen im Produktionsprozess liefern. In diesem Zusammenhang ist auch der weitläufig bekannte Begriff künstliche Intelligenz (KI) zu nennen. Das Gießverfahren ist ein sehr sensibler Prozess, der nicht robust auf Störungen reagiert. Bis man diese erkannt hat, entsteht viel Ausschuss. Mit den neuen Methoden der KI kann man rechtzeitig Handlungsanweisungen generieren, um den Produktionsprozess insgesamt wesentlich effizienter zu machen. Durch entsprechende Datenkorrelationen kann man Ursache-Wirkungsketten aufbauen und viel schneller auf Störgrößen reagieren. Diese Erkenntnisse sind in der Praxis sehr weiträumig anwendbar: Maschinen- und Anlagenbau, Automobilbau, Medizintechnik, Luft- und Raumfahrt – da gibt es eigentlich keine Grenzen.
Ein weiterer Forschungsbereich sind eigenschaftsoptimierte Gussbauteile, oder auch: maßgeschneiderte lokale Eigenschaften. Wie schaffe ich es, bestimmte Eigenschaften eines Gussteils an den korrekten Stellen zu beeinflussen, um damit eine höhere Qualität des Produkts zu erreichen?
Der dritte Forschungsblock betrifft die Realisierung topologieoptimierter Bauteile. Es geht dabei um lastgerechte geometrische Strukturen für die Großserie. Wir haben hier bereits Einiges an Aufwand investiert. Als Beispiel für die Anwendung in der Praxis könnte man lange Traggerüste mit großem Hebelarm nennen, wie sie in der Bau- oder Verpackungsindustrie zum Einsatz kommen. Ein derart optimiertes, einteiliges Bauteil könnte dann über eine an den jeweiligen Lastfall angepasste Tragstruktur verfügen.
Was tut sich gerade auf dem Gebiet der additiven Technologien?
Wir unterscheiden ja zwischen dem direkten und indirekten Verfahren. Es wird also entweder durch direkten Druck das jeweilige Bauteil hergestellt oder nur die Form dafür, in die dann konventionell die Schmelze eingelassen wird, d. h. die additive Herstellung von Formen ohne Modelle direkt vom Computer. Bei diesem indirekten Verfahren verfolgen wir nun zwei Ansätze: Zum einen die Produktion von Formen mittels sehr großer Drucker. Wir arbeiten hier gemeinsam mit dem Hersteller Voxeljet an der Entwicklung eines Druckers, der Formen für bis zu 80 t schwere Bauteile – etwa Komponenten für Windenergieanlagen – produzieren kann. Der zweite Ansatz bezeichnet das so genannte Stapel- oder Voxelgießverfahren. Hierbei wird nicht eine große Form gedruckt, sondern einzelne Segmente, die dann per 3-D-Puzzle wieder zusammengefügt werden. Das steigert die Effizienz, weil man den Schritt des 3-D-Druckens auf mehrere kleine Drucker parallelisieren kann. Dadurch lassen sich auch extrem große Bauteile schnell produzieren. Ein weiterer Vorteil sind die geringen Produktionskosten – wir können hier, bezogen auf das Bauteilgewicht und verglichen mit dem direkten Druckverfahren, etwa 50 Mal günstiger produzieren. Beide Ansätze sehen aus meiner Sicht sehr viel versprechend aus.
Ein Hauptabnehmer dieser additiven Verfahren ist die Automobilindustrie. Wo genau sehen Sie hier die Bedarfe?
Dort gibt es in jedem Fall Bedarf in den Bereichen der Karosseriefertigung, Speichertechnologie, Batteriewannen und der Fertigung von E-Motoren. Insgesamt werden durch die schrittweise Umstellung auf Elektroantriebe natürlich weniger Gussteile am Fahrzeug benötigt. Sie werden aber auch in Zukunft immer noch signifikant sein: Auch ein E-Motor braucht schließlich ein Gehäuse. Dann haben wir ja noch das klassische Fahrwerk mit seinen Achsschenkeln, das werden auch künftig Gussteile sein. Aber die bereits erwähnten topologieoptimierten Gussteile und Teile mit optimierten lokalen Eigenschaften können in der Autoindustrie zum Einsatz kommen. Wie man sieht: Die Möglichkeiten sind vielfältig – aber wir müssen immer am Ball bleiben, Angebote machen, die auch im Rahmen der Mobilitätswende dazu führen, dass wir künftig eine hinreichende Anzahl an Gussteilen am Fahrzeug haben.
Auch das Thema Klimaschutz und Nachhaltigkeit gewinnt massiv an Bedeutung. Welche Herausforderungen bestehen hier auf dem Gebiet der Forschung?
Hier ist ganz klar der schonende Umgang mit Ressourcen zu nennen. Wir müssen zusehen, dass wir so viel Kreislaufmaterial wie möglich nutzen und Verschwendung minimieren. Der zweite große Punkt ist das Thema Energie. Natürlich ist das Gießen ein energieintensiver Prozess. Hier haben wir aber auch spannende Ansätze, wie wir durch eine gewisse Flexibilität des Schmelzbetriebes Wege finden können, um auch mit nicht mehr stabiler Energiegrundlast umgehen zu können. Ich sehe hier auch den Ausbau der erneuerbaren Energien als eine gewisse Chance für die Gießereitechnik, weil wir mit entsprechendem Aufwand durchaus flexibel auf Angebotsspitzen und -senken reagieren können – etwa durch vorausschauende Produktionsplanung. Vereinfacht gesagt, wir müssen Energie für intensive Prozesse nutzen, wenn sie günstig ist, und mittels weniger intensiver Verfahren überbrücken, wenn sie knapp ist. Diese Möglichkeiten, flexibel auf Netzüber- und unterlastungen reagieren zu können, sehe ich als große Chance für Gießereien. Damit können wir, trotz des prinzipiell energieaufwändigen Verfahrens, ein sehr nachhaltiges produzierendes Gewerbe sein.
Herr Prof. Volk, vielen Dank für das Gespräch!
VON JAN KRETZMANN