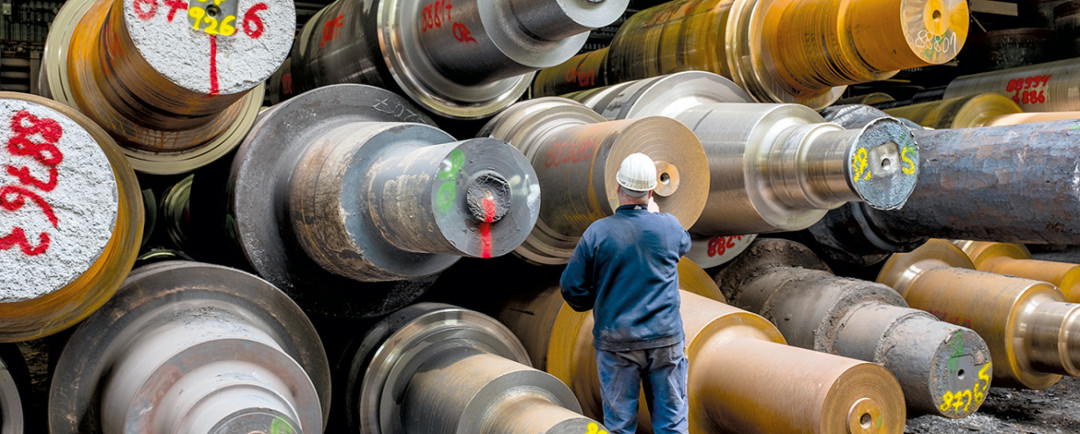
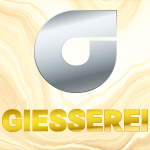
Gontermann-Peipers gießt die schwersten Walzen der Welt. Mit fast 200 Jahren Gießerei-Know-how, Ingenieurskunst und Innovationsgeist hat sich der Siegener Industriebetrieb bis heute zu einem der weltweit bedeutendsten Hersteller von Walzwerkswalzen und Hochleistungskomponenten für den Maschinenbau entwickelt.
Unter der rund fünf Meter durchmessenden Abdeckplatte in der Werkshalle vibriert es. Dann senkt sich eine zwei Meter hohe Gießpfanne langsam zum Eingusstrichter im Zentrum der Platte herab. Jetzt startet der Gießzyklus: ein Werker in Hitzeschutzmontur kippt die Pfanne per Handrad zügig, aber behutsam nach vorne. Die Stahlschmelze schwappt über die Gießschnauze und gleitet dann fast lautlos in einem breiten Strahl in die unterirdische rund 13 Meter tiefe Vertikalschleuder, die in vollem Betrieb ist.
Mit mehreren Hundert Umdrehungen in der Minute rotiert dort eine aufrecht stehende zylindrische Schleudergießkokille. Die Zentrifugalkräfte pressen die Schmelze vergleichbar einer riesigen Salatschleuder an den Rand der Form und sorgen so für eine kompakte Verdichtung des Gefüges. Rauch dringt jetzt aus dem Trichter und den Ritzen der mit riesigen Schrauben fixierten Abdeckplatte hervor. Im Vertikalschleudergießverfahren entsteht hier eine Arbeitswalze, die einmal im Vorgerüst einer Warmband- oder Grobblechstraße Brammen zu Blechen herunterwalzen wird. Der soeben gegossene Mantel aus extrem verschleißfestem Stahl wird im Verlaufe des Abgusses noch mit einem duktilen Kern gefüllt, der künftig die Kräfte aufnimmt, die auf die Walze einwirken. Für den aktuellen Arbeitsschritt wird die Schleuder einige Zeit brauchen – nach dem Abguss dauert es mehrere Tage, bis die Rohwalze so weit erkaltet ist, dass sie weiterverarbeitet werden kann.
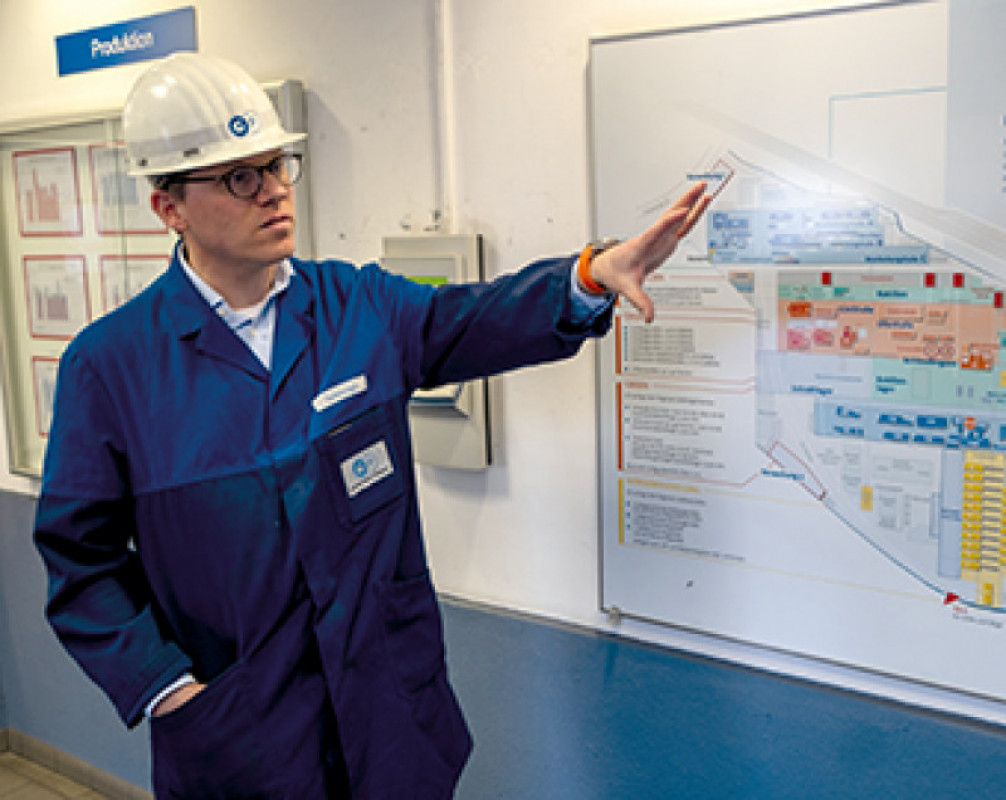
Mittelständisches Paradebeispiel
Ort des Geschehens ist das Werk Marienborn der Siegener Traditionsgießerei Gontermann-Peipers, die neben anderen Hochleistungskomponenten rund 800 Walzen in der Gewichtsklasse ab etwa acht Tonnen im Jahr gießt und fertig bearbeitet. An den beiden Standorten des Unternehmens, den Werken Hain und Marienborn, arbeiten 570 Mitarbeiterinnen und Mitarbeiter. Rund 100 Mio. Euro Umsatz erwirtschaftet der Betrieb Jahr für Jahr. Der große Mittelständler ist weiterhin in Familienhand. Die Nachkommen der Firmengründer leiten den Traditionsbetrieb bereits in der siebten Generation.
Auf das Jahr 1825 geht die Grundsteinlegung zurück – in sechs Jahren wird das Unternehmen 200 Jahre alt. Gontermann-Peipers ist damit ein Paradebeispiel für mittelständische Wirtschaftskraft, die seit jeher Rückgrat der deutschen Gesellschaft ist Auch im Walzengießen hat das Unternehmen schon jahrhundertealtes Know-how: 1855 wurden hier die ersten Walzen abgegossen. Kein Wunder, dass es weltweit nur wenige Firmen gibt, die dem Unternehmen in seinem Marktsegment das Wasser reichen können. Einen Weltrekord stellte Gontermann-Peipers 1985 mit dem Abguss einer Walze für die Dillinger Hüttenwerke auf: Sie hatte ein Fertiggewicht von 265 Tonnen und war 11,5 Meter lang. Um die benötigten 500 bis 600 Tonnen Flüssigeisen für den Abguss einer Walze in dieser Größenordnung zusammenzubekommen kooperierte Gontermann-Peipers mit weiteren Gießereien und Stahlwerken in der Region. Eine Mammutaufgabe, an die allenfalls die Fertigung der größten Walze für Aluminiumbleche heranreichte: Mit einem Gewicht von 236 Tonnen und einer Länge von 13,55 Metern wurde hier auch die längste Schwerstwalze der Welt gegossen. Kunde ist das Arconic-Werk im US-amerikanischen Davenport, das u. a. für den Flugzeugbauer Boeing produziert.
Hoher Exportanteil
Aktueller Vertreter der Familie bei Gontermann-Peipers ist Frieder Spannagel. Gemeinsam mit Dr. Bernd Hofmann und Dr. Hartmut Jacke bildet er die dreiköpfige Geschäftsführung des Familienunternehmens. Der 44-Jährige hat die Leitung des Unternehmens 2015 von Vater Fritz Spannagel übernommen, der das Unternehmen heute als Aufsichtsratsvorsitzender beratend begleitet. Frieder Spannagel hat BWL studiert und sechs Jahre lang bei der SMS-Group gearbeitet, bevor er ins elterliche Unternehmen eingestiegen ist. Von Einträgen im Guinness Buch für die Rekord-Schwerstwalzen hält Spannagel ebenso wenig wie von der kürzlich erfolgten Aufnahme in das Weltmarktführer-Ranking der Wirtschaftswoche.
Denn bei der Leitung des Unternehmens zählen für ihn eher realistische Geschäftseinschätzungen als Titel. „Um im weltweiten Wettbewerb ganz oben mitzuschwimmen, müssen unsere Produkte mindestens so viel besser sein, wie wir teurer sind als andere“, betont er. Der weltweite Wettbewerb spielt für Gontermann-Peipers bei einem Exportanteil von 70 Prozent bei den Walzen ebenso eine Rolle, wie die Entwicklungen auf dem Stahlmarkt. Denn hier sind Kunden der Siegener wie die Dillinger Hütte, Dillinger France, Salzgitter Grobblech, thyssenkrupp, Severstahl und MMK Magnetogorsk aktiv.
Die Stahlbranche ist spätestens seit 2009 von gewaltigen Überkapazitäten, ausgelöst durch chinesische Stahlwerke, geprägt. Aktuell zieht das Walzengeschäft jedoch wieder an. Abnehmerländer sind Indien, Lateinamerika, Mexiko und Russland. Rückläufig sind Aufträge aus China. Die Nachfrage nach Schwerstwalzen ist allerdings überschaubar, da es nur eine begrenzte Anzahl von Anlagen gibt, die sie einsetzen. Zudem halten Schwerstwalzen sehr lange bis sie ausgetauscht werden müssen.
Innovative Walzenzusammensetzung
Neben Arbeitswalzen fertigt das Werk Marienborn auch noch Stützwalzen und Profilwalzen, die ebenfalls in Walzwerken zum Einsatz kommen. Die Stützwalzen, zu denen auch Schwerstwalzen gehören, entstehen im Stahlverbundgießverfahren, einem selbst entwickelten Prozess, in dem ähnlich wie beim Vertikalschleudergießverfahren, verschiedene Werkstoffe für Walzenmantel und -kern zu äußerst leistungsfähigen Walzen verbunden werden. Eingesetzte Walzenwerkstoffe sind Warmarbeitsstähle, Chromstähle mit bis zu 18 Prozent Chrom und HS-Stähle mit einem hohen Vanadium-Anteil.Nachteil hier ist der kürzlich massiv gestiegene Preis des Elements, das die Zähigkeit und damit die Widerstandsfähigkeit des Stahls erhöht.
Weiteres prominentes Produkt von Gontermann-Peipers sind Nuklearbehälter-Körper, gegossene und mechanisch bearbeitete dickwandige Gusskörper für die Castor®-Behälter der GNS Gesellschaft für Nuklear Service. Der Castor® ist ein Sicherheitsbehälter für den Transport und die Lagerung von hoch radioaktiven Abfällen und Brennelementen von Kernkraftwerken. Die 100 Tonnen schweren Behälterkörper aus Sphäroguss gehören zu den anspruchsvollsten Gussteilen überhaupt. Gontermann-Peipers zählt zu einem sehr kleinen Kreis von Unternehmen, die Castor-Körper gießen und bearbeiten können. Das Unternehmen unterhält hierfür ein staatlich akkreditiertes Prüflabor.
Das Werk Hain versteht sich als Spezialitäten-Gießerei. Hier kommen unterschiedlichste Gießverfahren zum Einsatz. Gefertigt werden anspruchsvolle Werkstoffe und Komponenten für den allgemeinen Maschinenbau. Neben dem Kokillen- und dem Horizontalschleudergießen wird im Strang- und Handformgießverfahren produziert. Typische Produkte sind z.B. Zylinderlaufbüchsen, große Gussteile für Werkzeugmaschinen, gut zu zerspanender Strangguss und im Verbund gegossene Hochleistungsmahlbandagen für Zementwerke und andere Zerkleinerungsanwendungen – Bauteile, die in den letzten Jahren recht gut liefen, wie Spannagel berichtet.
Korsett aus Kokillen und Ringen
Ab den 1970er-Jahren kam das Geschäft mit großen Walzen im Werk Marienborn in Schwung. Damals wurde auch der Schmelzbetrieb vergrößert, der heute vier Lichtbogenöfen mit 20, 30, 40 und 60 Tonnen Kapazität umfasst. Gerade schwebt ein großer Chargierkorb am Hallenkran heran, der seine Fracht klirrend in den Ofen chargiert. Ein Werker mit wuchtigem Schutzanzug spült die Schmelze mit Sauerstoff. Danach wird das Schlacketor geöffnet; der Blick ins Innere zeigt drei grellglühende Grafitelektroden – das mehrere Tausend Grad heiße Herz des Lichtbogenofens.
Entlang an gestapelten Formringen und Kokillenelementen – die in Hain für den Einsatz in der Schwestergießerei gegossen werden – geht es weiter zur 13 Meter tiefen Gießgrube. Hier steht, eingezwängt in ein Korsett eben jener Kokillenelemente, eine Stützwalze. Der Abguss kann noch nicht allzu lange zurückliegen, denn die Konstruktion qualmt und glimmt noch. Stützwalzen haben in Walzwerken die Aufgabe, das Durchbiegen der Arbeitswalze zu verhindern. „Damit stärkt die Stützwalze der Arbeitswalze quasi den Rücken bei der Umformarbeit“, nennt Spannagel einen Vergleich. Der Stützwalze kommt so eine zentrale Funktion zu, die für die Leistung des gesamten Walzwerks wichtig ist. Dass die Nachfrage nach Walzen derzeit gut läuft, zeigt der anschließende Weg hin zur Fertigbearbeitung. Auf der einen Seite begrenzt eine rote Ziegelmauer den Durchgang, die mit den abschließenden Schindeln und türmchenförmigen Aufbauten unverkennbar aus der Kaiserzeit stammt, auf der anderen ist die zum Durchgang hin offene Halle übermannshoch mit Walzen unterschiedlicher Größen ausgefüllt, die allerdings statt chromglänzendem Schein hier noch eine rauhe und stachelige Oberfläche aufweisen.
Für die Fertigbearbeitung steht eine rund einhundert Meter lange Halle bereit, die von Anfang bis Ende mit Schleifmaschinen, Vor- und Fertigdrehmaschinen sowie Bohr- und Fräswerken besetzt ist. Darauf eingespannt sind Walzen unterschiedlichster Größen. Soeben schabt eine Drehmaschine dreifingerbreite geringelte Späne von der Oberfläche einer Rohwalze. Das schabende Geräusch erfüllt, gemischt mit kurzen hydraulischen Stößen und scheppernden Lauten, die Halle. An Displays stehen Mitarbeiter und überwachen die Prozesse. Spannagel macht darauf aufmerksam, dass Gontermann-Peipers über die größte Walzendrehmaschine der Welt verfügt, dann tritt ihm Christian Balling, Betriebsleiter in der mechanischen Bearbeitung, entgegen und schüttelt ihm die Hand. Er ist verantwortlich für das Vor- und Fertigdrehen der Walzen, das Schleifen, die Fräs- und Bohrbearbeitung sowie die Verpackung. Er nennt die jährliche Walzenproduktion und weitere Aufgaben seiner Abteilung wie Lohnbearbeitung und Reparaturen. „Wir sind hier gut ausgelastet“, sagt er selbstbewusst und Spannagel konkretisiert mit dem Auslastungsgrad der Werke von 80 Prozent. Zurzeit produziert das Werk Marienborn 20 000 Tonnen im Jahr, im Werk Hain sind es 23 000 Tonnen. Es wird nichts dem Zufall überlassen. Ist die Walze versandbereit, glänzt sie wie eine Weihnachtskugel am Baum - neben den inneren Werten der Produkte zählt auch immer der äußere Eindruck.
Know-how-Pflege für das 3. Jahrhundert
Beim Blick auf die vielfältigen Arbeitsschritte stellt sich die Frage, wie das breite Spezialisten-Know-how des Unternehmens den Übergang ins dritte Jahrhundert des Familienbetriebs überdauern kann? Die Antwort ist: mit zunehmender Automatisierung und Digitalisierung sowie einem gut durchdachten Nachwuchsprogramm, das aktuell 30 Auszubildende und rund 15 Nachwuchsführungskräfte mit Meister- oder Technikerabschluss umfasst.
Die frisch gebackenen Fachkräfte sollen die Belegschaft mit ihrem aktuellen Durchschnittsalter von etwa Mitte Vierzig nach und nach ablösen. Beim Anwerben von Nachwuchs helfen der gute Name von Gontermann-Peipers in der Region, die abwechslungsreiche Ausbildung im Betrieb sowie die fruchtbare Zusammenarbeit mit den regionalen Bildungsinstitutionen und Partnerunternehmen. Hinzu kommt der konsequente Fokus auf Innovationen mit zwei hauptamtlichen F&E-Ingenieuren, deren Aufgabe es ist, die Produktion immer leistungsfähiger zu machen und dabei auch die Chancen durch die Digitalisierung zu berücksichtigen – etwa bei der Optimierung der Prozess- und Logistiksysteme.
Nachschub an Ingenieuren erhält das Unternehmen von den Universitäten und Hochschulen in Freiberg, Aachen, Clausthal, Friedberg, Duisburg und Siegen. „Einer unserer Ingenieure promoviert gerade an der Universität Siegen“, berichtet Spannagel stolz. „Es geht um Veränderungen der Walzenoberfläche während des Walzprozesses“, ergänzt der Geschäftsführer. Wichtig für die Zukunft sind auch regelmäßige Investitionen in die technische Substanz und Infrastruktur des Unternehmens: jeweils sechs bis sieben Millionen Euro fließen hier jedes Jahr.
Belohnt wird dieser Kurs von dem Vertrauen der Kunden in aller Welt. Ein prestige- und finanzkräftiger Auftrag kam in den letzten Jahren etwa von Big River Steel, einem von der Düsseldorfer SMS Group neugebauten Stahlwerk am Ufer des Mississippi im US-Bundesstaat Arkansas. Hier ging es um über 100 Walzen mit Anschlussaufträgen – ein ähnlich großer Auftrag ist kürzlich aus Mexiko eingegangen.
Die großen Walzen werden dabei üblicherweise mit Schiffen und der Eisenbahn befördert. Hier steht ein eigener Gleisanschluss auf dem Gelände des Werks zur Verfügung. Die Waggons, die sich für den Transport von Schwerstwalzen eignen, sind ein begehrtes Gut bei Industriebetrieben mit Produkten in dieser Größenordnung. „Es gibt jedoch nur zwei Waggons dieser Art in ganz Deutschland“, gibt Spannagel zu bedenken. Das führt gelegentlich zu Gerangel mit Siemens und anderen Herstellern von Großkomponenten. Von Bremerhaven gehen die Walzen dann auf die Reise ins Zielland – und verbreiten so den guten Ruf von Ingenieurskunst „Made in Germany“ in aller Welt.
VON ROBERT PITEREK, DÜSSELDORF