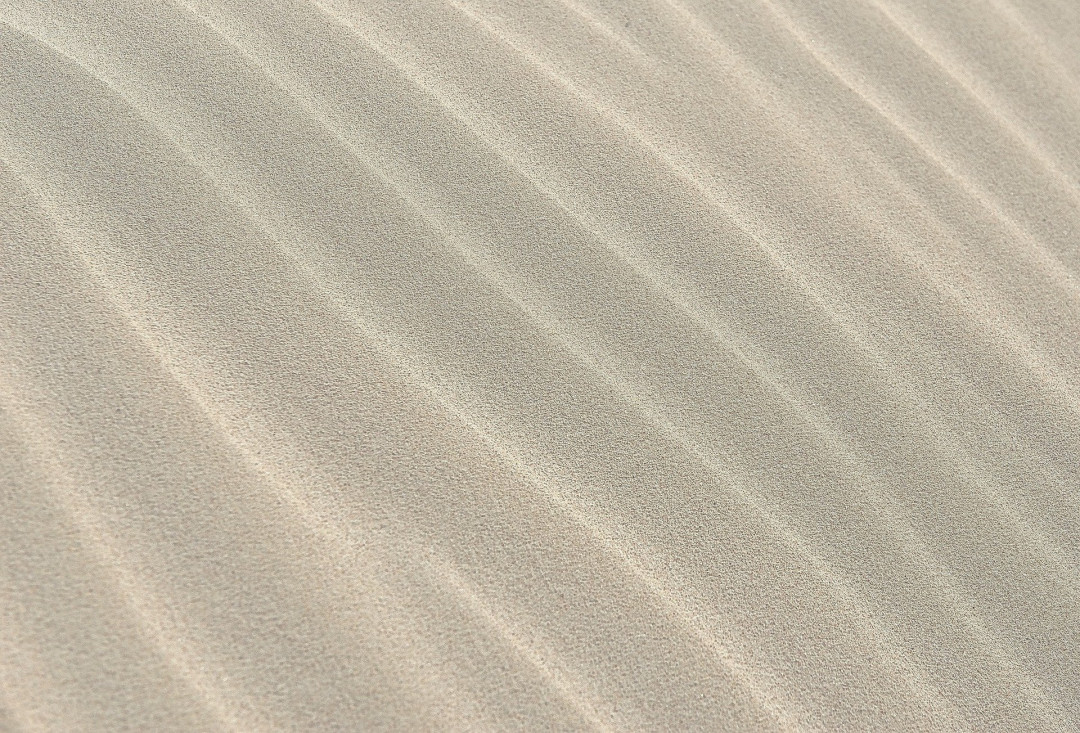
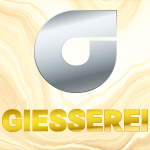
Altsand macht den größten Teil des Abfallaufkommens in Sandgussbetrieben aus; bei Grünsandbetrieben sind es sogar mehr als 50 % aller Produktionsabfälle. Aufgrund immer knapper werdender Deponiekapazitäten hat Gemco Engineers, Eindhoven, für die Sandaufregenerierung den SandCleaner in Zusammenarbeit mit verschiedenen führenden europäischen Gießereien weiter entwickelt.
Gießereisand wird in der Regel auf Deponien entsorgt, aber diese Praxis wird zunehmend als umweltschädlich eingestuft und stößt vermehrt auf Widerstand, weshalb sie immer häufiger verboten wird. In einigen Fällen – z. B. bei einem hohen Aufkommen an Bauschutt aufgrund des derzeitigen Baubooms – werden die Deponiemöglichkeiten für Gießereisand stark abnehmen oder sogar ganz ausgeschöpft sein.
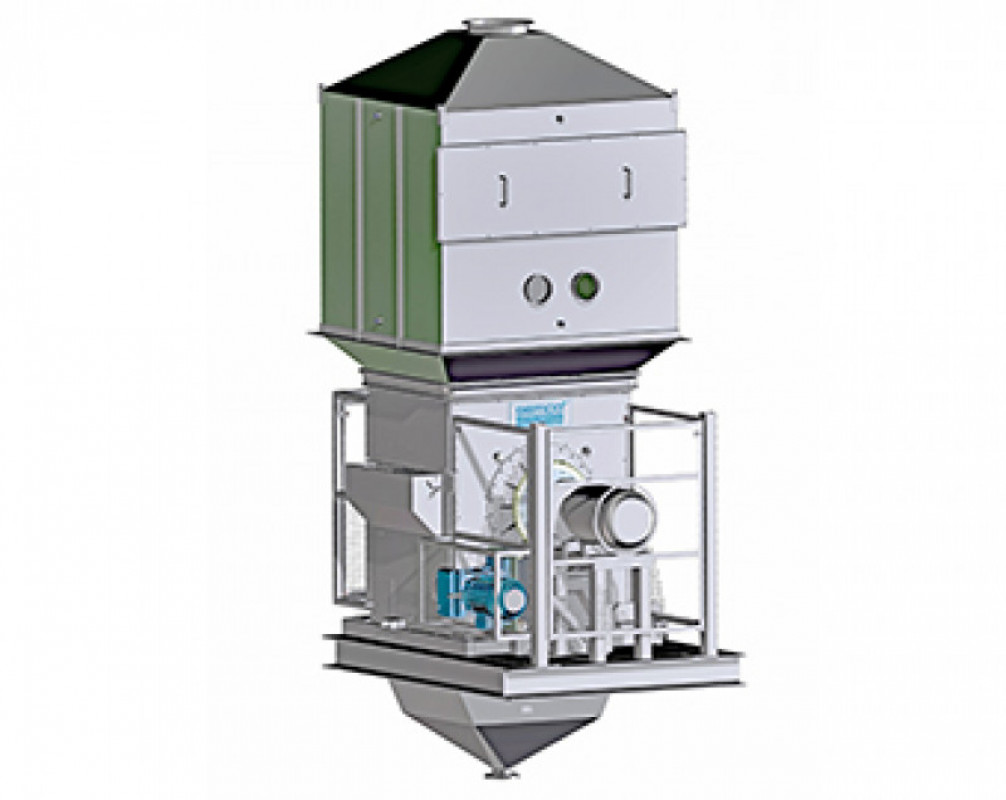
Sandregenerierung schont die Umwelt
Die Sandregenerierung hingegen ist ein umweltfreundliches, sehr nachhaltiges Verfahren. Viele Gießereien scheinen aber immer noch unschlüssig bezüglich dieser Abfall- und Umweltfragen zu sein. Dabei hat die Sandregeneration ihren verfahrenstechnischen und wirtschaftlichen Nutzen längst unter Beweis gestellt. Sie spart nicht nur die Kosten für Neusand, sondern auch für dessen Transport und verringert die Anzahl der erforderlichen Lkw-Bewegungen und entlastet damit den Verkehr.
Letzteres ist besonders wichtig, da der Lkw-Verkehr vielerorts durch die Gesetzgebung immer weiter beschränkt wird. Daher sollten Transportkapazitäten lieber für die Auslieferung von Gussteilen genutzt werden. Doch trotz dieser vielen Vorteile regenerieren bisher nur wenige Gießereien den eigenen Sand. Die Regenerierung von Altsand verfolgt das Ziel, möglichst viel qualitativ hochwertigen Sand – vergleichbar mit Neusand oder sogar besser – zu gewinnen. Dazu werden Stoffe entfernt, die während eines Form- und Gießzyklus zugesetzt oder gebildet worden sind. Der regenerierte Sand ist dann anstelle von Neusand als Kernsand wiederverwendbar.
Der SandCleaner
Um dies zu erreichen, hat Gemco den SandCleaner in Zusammenarbeit mit verschiedenen führenden europäischen Gießereien entwickelt (Bild 1). Seit Mitte der 90er-Jahre sind mehrere SandCleaner in Betrieb, darunter in Werken und Gießereien in Mannheim, Stadtallendorf und Weert (NL), die seit ihrer Einführung erfolgreich ihren Dienst verrichten. Das Prinzip des SandCleaners basiert auf einem trockenen mechanischen Verfahren, bei dem einzelne Sandkörner gemahlen und ständig durch Schleifen entstaubt werden. Durch das Schleifen werden die Körner von anhaftenden Bindemitteln und anderen Schmutzpartikeln gereinigt, die Form des Korns wird abgerundet, schwache Körner brechen und werden als Staub ausgetragen (Bild 2 a, b, c). Der gewonnene Sand kann mit einem Wirkungsgrad von mehr als 97 % bei Quarzsand als Kernsand wiederverwendet werden. Darüber hinaus erfordert das Schleifen des Sandes keine zusätzliche Kühlung und hat daher den geringsten Energieverbrauch aller Gewinnungsverfahren. Das hält die CO2-Emissionen auf einem niedrigen Niveau. Ein weiterer Vorteil der mechanischen Aufbereitung im Batch-Verfahren gegenüber der Aufbereitung im kontinuierlichen/sequenziellen Verfahren ist die Tatsache, dass sich SandCleaner je nach benötigter Kapazität unabhängig voneinander betreiben lassen. Ein SandCleaner-System kann zudem modular aufgebaut werden (Bild 3).
Die Sandrückgewinnung
In einer Gießerei mit Sandrückgewinnung besteht der zur Herstellung von Kernformen verwendete Sand aus einer Mischung von Regeneratsand und Neusand. Dieser kann zu 100 % aus Regeneratsand bestehen oder mit einem beliebigen Prozentsatz an Neusand gemischt werden. In diesem Grünsand-/Kernsandkreislauf wird also ein bestimmter Prozentsatz wiederholt zurückgewonnen und als Sand zur Herstellung von Kernen wiederverwendet. Allgemeinen gilt, dass von einer 50/50-%-Mischung aus Rücklaufsand und Kernsand 14 % an Zusätzen (Bentonit, Bindemittel, Kohlenstoff usw.) gereinigt werden müssen, um wieder die Eigenschaften von Neusand zu erreichen; durch Schleifen werden weitere 3 % als zusätzlicher Staub entfernt.
Von diesen 17 % sind 10 % Staub, der so viel aktives Bentonit und Kohlenstoff enthält, dass er dem Mischer zugegeben werden kann. Außerdem verbleiben durch diese mehrfachen Regenerationszyklen nur mehr die starken Sandkörner, was zu einem stabileren Sand führt. Die abgerundeten Körner verbessern die Formfüllung des Kernkastens und die Oberflächenqualität. Die Grate am Gussteil werden dadurch um >30 % reduziert, was die Entgratungskosten verringert.
Die Sandreinigungsanlage in Mannheim, die seit 1996 in Betrieb ist, umfasste ursprünglich vier SandCleaner, deren Leistung je nach Verhältnis zwischen 130 und 170 t/Tag variierte. Inzwischen wurden die bestehenden SandCleaner optimiert und die gesamte Anlage um zwei weitere SandCleaner ergänzt, um den Einsatz von Regenerat erhöhen zu können. In der Mannheimer Anlage schwankt das Verhältnis von Kernsand zu Grünsand zwischen 60 % und 40 %. Die bestehenden SandCleaner wurden in den letzten beiden Jahren modernisiert. Dadurch erhöhten sich Kapazität und Laufzeit der Anlage.
Die Leistung des SandCleaner 2.0 stieg um 100 kg auf ein Chargengewicht von bis zu 850 kg. In Kombination mit einer höheren Betriebsleistung der Anlage blieben die Zykluszeiten unverändert. Der SandCleaner 2.0 ist unempfindlicher gegenüber Temperaturschwankungen im Sand und ermöglicht die Verarbeitung von heißerem Sand, wodurch die erforderliche Kühlung des Sandes vor der Rückgewinnung reduziert wird. Die verbesserte Konstruktion und die Verwendung von leichter austauschbaren und verschleißfesteren Materialien ermöglichen längere Wartungsintervalle. Eine vollständige Wartung ist nur noch einmal jährlich erforderlich, was die Wartungskosten senkt. Die kombinierten Modernisierungen erzielen eine Steigerung der Anlagenleistung um 15 %.
Testanlage
Seit 2019 verfügt die TU Freiberg über eine SandCleaner-Anlage von Gemco mit einem Chargengewicht von 150 kg. Damit werden Tests durchgeführt, um die Produktionsprozesse von Kunden zu simulieren. Tests mit dieser Anlage haben gezeigt, dass die Messwerte in der Produktionspraxis exakt mit diesen übereinstimmen. Versuche mit Altsand aus dem Kernpaketverfahren zeigen, dass die mechanische Regenerierung allein bessere Ergebnisse erzielt als die alleinige thermische Regenerierung.
Auch zeigen alle Resultate, dass die Grenzwerte für die Herstellung eines guten Kerns ausreichend eingehalten werden. Zudem sind die Produktionskosten mit dem SandCleaner am niedrigsten und ohne CO2-Ausstoß. Bild 4 zeigt, dass die Werte von regeneriertem Kernsand innerhalb der Festigkeitsgrenzen liegen um wieder sehr gute Kerne zu fertigen – auch für Kernpaketguss.
Fazit
Die Kostenreduzierung für Sand, Entsorgung und Transport mag bei den Überlegungen zur Sandregenerierung an erster Stelle stehen, ebenso wie eine bessere Oberflächenqualität der Gussstücke aufgrund der besseren Sandqualität.
Doch in einer Zeit, in der auch unsere Branche Verantwortung für die Umwelt übernehmen muss, lohnt es umso mehr, den Einsatz der Sandregenerierung im Gießereiprozess ernsthaft in Betracht zu ziehen. Und zwar so, dass die geringsten Umweltauswirkungen entstehen.
VON HUUB VAN DER WEIDEN, EINDHOVEN