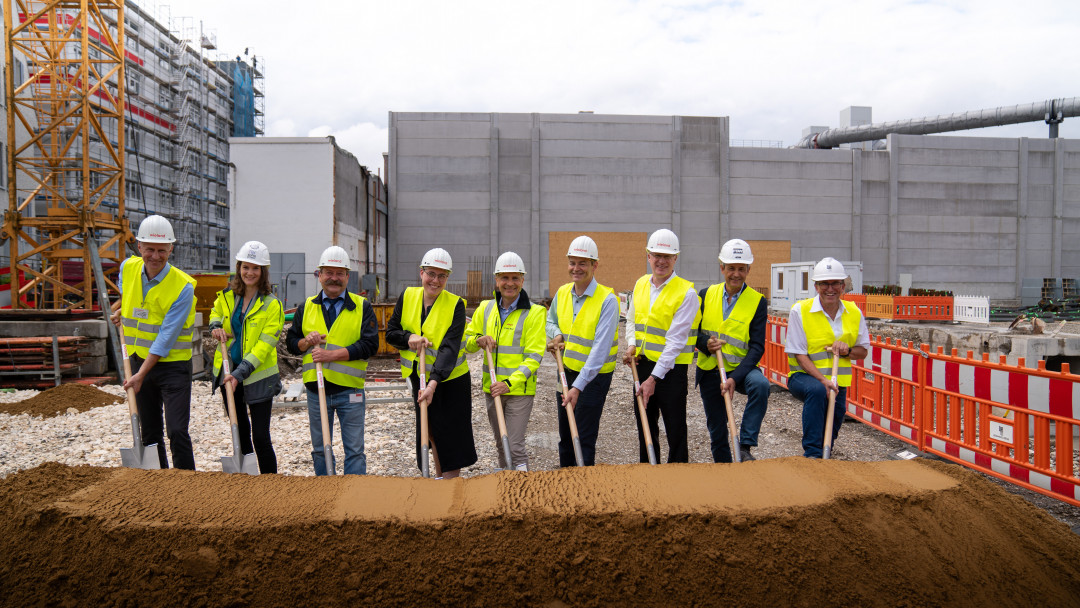
The official ground-breaking ceremony on 27 May 2024 marks the start of a project with a major impact at Wieland: the foundry at the Vöhringen site is being expanded to include a recycling centre that will enable the processing of copper scrap using the latest and most efficient technology, thus increasing the global recycling rate of Wieland products to over 80 per cent after commissioning.
‘If we look at the expansion of the foundry in Vöhringen with a recycling centre from a sustainability perspective, this is a global flagship project with a signalling effect,’ emphasises Dr Erwin Mayr, CEO of the Wieland Group. ‘The new plant is an important building block on our way to closing the material cycle sustainably and increasing our global recycling rate to 100 percent in the near future.’ This will bring Wieland a major step closer to its goal of greenhouse gas-neutral production by 2045 at the latest. Other cornerstones of the decarbonisation strategy are the electrification of all plants to phase out fossil fuels and the full use of renewable energies through green electricity supply contracts and in-house power generation using photovoltaic and wind power plants.
With this investment, Wieland is also establishing a strategic base for the supply of materials, as the plants throughout Europe and parts of Asia will be supplied with high-quality copper semi-finished products from Vöhringen. For Anton Zierhut, President of Extruded Products at the Wieland Group, the investment is a clear commitment to the Vöhringen site, where 25 new jobs will be created. ‘Our new recycling centre is a forward-looking investment for our main plant in Vöhringen and will play an important role in further differentiating us from the competition.’
In the future, the new plant on the site of the Wieland foundry will produce pure copper billets with a recycled content of 100 per cent. Copper scrap and granules as well as production scrap from the local production will be used for this purpose. This not only ensures the supply of material to various company sites, but also has a positive impact on the carbon footprint of Wieland products. The recycling process is based on a highly energy-efficient method known as fire refining. This step sets new standards for the company, which also benefits its customers. They receive input material with the lowest product carbon footprint (PCF) in the industry, enabling them to make their own process chains more sustainable and reduce emissions.