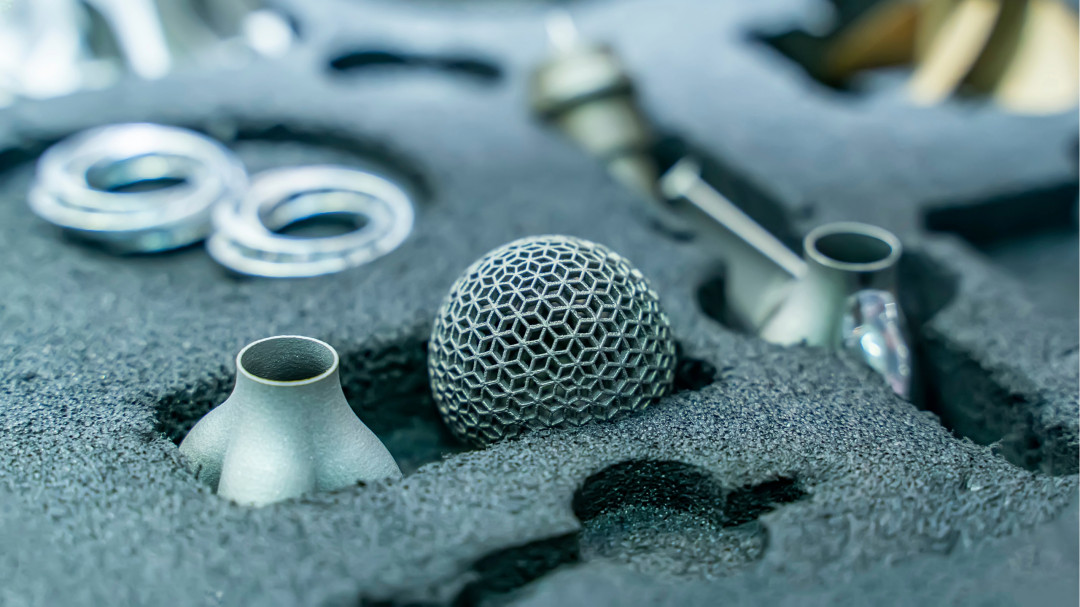
Werkzeuge für Umformprozesse werden in der Regel aus Werkzeugstahl hergestellt und benötigen ein bestimmtes Eigenschaftsprofil, um optimal und über einen möglichst langen Zeitraum eingesetzt werden zu können. Bislang werden sie vor allem durch konventionelle Fertigungsverfahren wie das Gießen oder die spanende Materialbearbeitung hergestellt, wobei Material verloren geht. Für die additive Verarbeitung sind Werkzeugstähle bisher nur eingeschränkt geeignet. Eine Legierung zu finden, die die geforderten Eigenschaften aufweist und additiv gefertigt werden kann, ist Ziel eines Projekts am Lehrstuhl Werkstofftechnik (LWT) der Ruhr-Universität Bochum.
Gefördert von der Firma Dörrenberg Edelstahl GmbH wird Doktorandin Julia Hahn danach auf die Suche gehen. Das Projekt wird für vier Jahre vom Industriepartner aus Engelskirchen im Oberbergischen Kreis finanziert. „Innovative Fertigungsverfahren wie die additive Fertigung benötigen spezifisch angepasste Werkstofflösungen, um ihr Potenzial vollständig auszuschöpfen“, erklärt Prof. Dr. Sebastian Weber vom LWT. „Wir freuen uns, durch die Kooperation für diese Herausforderung einen kompetenten Forschungspartner an unserer Seite zu haben“, ergänzt Prof. Dr. Christoph Escher von Dörrenberg.
Fertigen ohne Materialverlust
Werkzeugstähle für Umformwerkzeuge müssen unter anderem besonders hart und verschleißbeständig sein und eine möglichst hohe Wärmeleitfähigkeit aufweisen. „Solche Legierungen gibt es zwar, eine additive Verarbeitung ist jedoch nur bedingt möglich“, so Julia Hahn. Die Verfahren der additiven Fertigung besitzen allerdings Vorteile, die die Forschenden gerne ausnutzen wollen. So wird zum einen nur genauso viel Material benötigt, wie das Werkzeug am Ende ausmacht – es fallen nicht wie bei anderen Verfahren Späne an. Außerdem bieten additive Fertigungsverfahren die Möglichkeit, komplexe Strukturen wie etwa Kühlkanäle in Werkzeuge einzubauen. Sie können Umformprozesse optimieren und die Lebensdauer der Werkzeuge erhöhen. „Man kann auch durch bestimmte additive Fertigungsverfahren ein gegossenes Werkstück finalisieren und seine Oberfläche durch die Verwendung von Legierungen mit unterschiedlichen Eigenschaften beschichten. So kann man vorgegossene Umformwerkzeuge optimieren und mit lokal unterschiedlichen Eigenschaften versehen. Das wiederum verlängert die Werkzeugstandzeit und verbessert den Umformprozess“, erklärt Julia Hahn. „Auf diese Weise können belastbarere Werkzeuge bei einem gleichzeitigen Kostenvorteil gegenüber klassischen Produktionsverfahren hergestellt werden, und das bei stark verkürzten Vorlaufzeiten für Planung und Produktion“, so Christoph Escher.
Ihre Suche nach der optimalen Legierung wird Julia Hahn mit thermodynamischen Berechnungen beginnen und von erfolgreichen Legierungen ausgehen. Bei vielversprechenden Berechnungen geht es dann ans Experiment: Die berechneten Legierungen werden durch die lehrstuhleigene Verdüsungsanlage zu Pulver verdüst, welches dann mittels Pulverbettverfahren oder Direct Energy Deposition zu Probenkörpern verarbeitet wird. Beim Pulverbettverfahren verschmilzt ein Laser in einer Metallpulverschicht nur die Pulverpartikel, die das Werkstück später ausmachen sollen. Das übrige Pulver kann nach einer Wiederaufbereitung erneut verwendet werden. Direct Energy Deposition ähnelt dem Auftragsschweißen. Hierbei wird das Metallpulver durch eine Zufuhrdrüse zielgerichtet auf ein Werkstück aufgebracht und dort lokal durch Laserstrahlung aufgeschmolzen und mit dem Werkstück verbunden. Die Besonderheit bei diesem Verfahren stellt die gleichzeitige Verwendung von zwei unterschiedlichen Legierungen dar, wodurch Bauteile oder Beschichtungen mit lokal unterschiedlichen Eigenschaften gefertigt werden können.