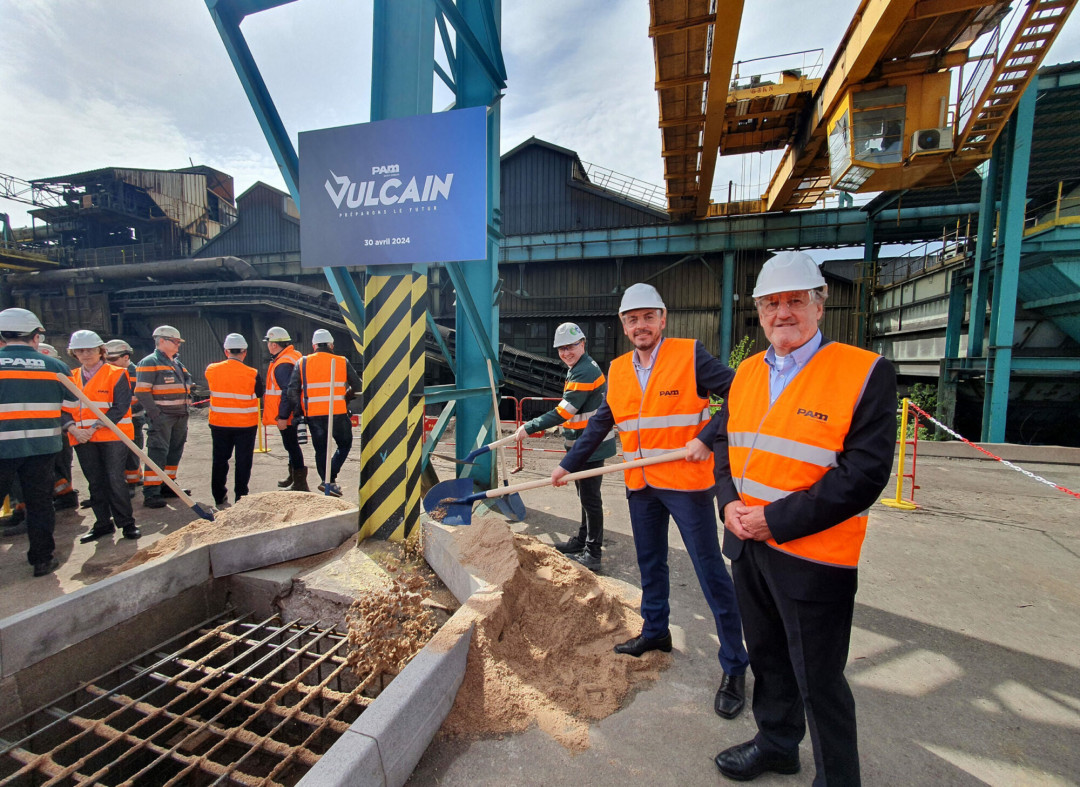
It is a milestone for Saint Gobain PAM, a beacon project for French industry, and a showcase for ABP Induction: In the French town of Foug, an old cupola furnace is being decommissioned and replaced by a more climate-friendly induction furnace from ABP Induction. The aim is to massively reduce CO2 emissions and water consumption. After the ABP induction system has been set up and installed, production will be converted without any interruption to production.
The history between Saint Gobain PAM and ABP Induction is long: ‘We have been working together on various projects for many years, most recently on projects in China, the Czech Republic and Brazil,’ explains Alexander Keller, Head of System Sales at ABP. Saint Gobain PAM's objectives are in line with ABP's strategy, which focuses in particular on the four megatrends of decarbonisation, digitalisation, deglobalisation and demographic change. ‘In France in particular, the issue of decarbonisation is being pushed much harder,’ explains Alexander Keller. On the surface, a cupola furnace is being replaced by induction furnaces – in this case by two 30-tonne IFM furnaces with a capacity of 18 MW, built using TWINPOWER® technology; incidentally, one of the largest induction furnace systems ever installed in a foundry in Europe. But the changes at the Foug site are much more far-reaching: ‘A lot more is happening here – the entire foundry is being modernised. It's about environmental aspects, digitalisation, a significant improvement in working conditions – we at ABP identify with this 100 per cent.’
Transformation in Foug – holistic and sustainable
That is why it is too narrow a view to reduce the project in the arrondissement of Toul to the process of technology transformation. ‘Behind it is a complete project planning and implementation that has a holistic and sustainable impact on the organisation and the region,’ explains Alexander Keller.
ABP Induction supports its customers throughout the transformation process: ‘We accompany all process steps and develop the project together with the customer. This starts with the concept creation, continues with the project planning and leads to the construction and commissioning of the plant, including the implementation of the melting process,’ says Alexander Keller. Throughout the entire process, the teams from ABP and the customer work together intensively to identify what is important for the customer. ‘We have to understand where the focus lies and what role aspects such as environmental impact, occupational safety or productivity play."
The human factor also plays a major role: ABP Induction provides training for customer employees at the site or at the Virtual Academy so that they can operate the new induction furnace system effectively and efficiently under optimal and safe conditions. ABP also offers products for activities on the furnace platform to reduce the need for human intervention: Our modern digital products and safety equipment help to make the foundry a more attractive workplace.’ The concept creation takes about three to four months: “A new, individual concept is created for each project because the starting situation and conditions can vary greatly depending on the location and customer. But our project experience and the expertise of our team in converting from cupola furnace to induction furnace are of course extremely helpful,” he explains. The approach was similar for a previous project with Saint Gobain PAM. In 2022, the Pont-à-Mousson plant in the Meurthe-et-Moselle department was equipped with a new 30-tonne ABP induction furnace for the production of spheroidal graphite cast iron.
Vulcain project: conversion to induction without production downtime
Saint Gobain has summarised the complete modernisation of the foundry plant under the project name Vulcain. ‘Many ancillary units and systems will also be modernised, and we will be able to implement all of this without interrupting production,’ predicts Alexander Keller.
Saint-Gobain PAM, a specialist in ductile cast iron pipes, produces 60,000 tonnes of pipes and fittings annually, mainly for water and sanitary pipes. In April 2024, the Foug plant laid the foundation stone for the Vulcain project. The foundry, which specialises in the production of ductile cast iron, will be able to dispense with the cupola furnace in about a year's time, once all the buildings for the induction furnace plant and the plant itself are in place. 7,800 tonnes of coal were consumed here every year. After the conversion, this requirement will be eliminated completely – less energy will be consumed and less CO2 will be emitted. The overall aim is to reduce the factory's CO2 emissions by 62 per cent – that's 22,000 tonnes of emissions saved per year. With around 330 employees, Foug is set to become the group's factory with the lowest CO2 footprint in Europe. Foug is also aiming to reduce its water consumption by 80 per cent. This would save the equivalent of the annual water consumption of the city of Toul, with its population of around 15,000.
Jérôme Lionet, CEO of Saint-Gobain PAM, explains the responsibility that the company is aware of and that it is actively communicating: ‘We have to anchor the industry in a more sustainable world, that is part of our conviction.’ At the groundbreaking ceremony in Foug, Jérôme Lionet went a step further: ‘For us, it is a new industrial revolution, because we will leave the age of coal behind us – it is entering an age of electricity with much less impact on the environment.’
The Vulcain project represents a major investment for Saint Gobain. Although 25 per cent of the planned investment of 20 million euros will be financed by the Agence de la transition écologique (ADEME), it is still a major undertaking – which should pay off, as Claire Pedini, Deputy General Manager at Saint-Gobain, explained: ‘It is part of what we want to achieve at Saint-Gobain – to be a responsible company that reduces its carbon footprint and offers its customers decarbonisation solutions.’
Although potential risk factors such as the development of electricity prices are being monitored, this is a risk that the company is willing to take because the project's focus and message are part of the company's sustainable, environmentally conscious strategy – just like ABP Induction.