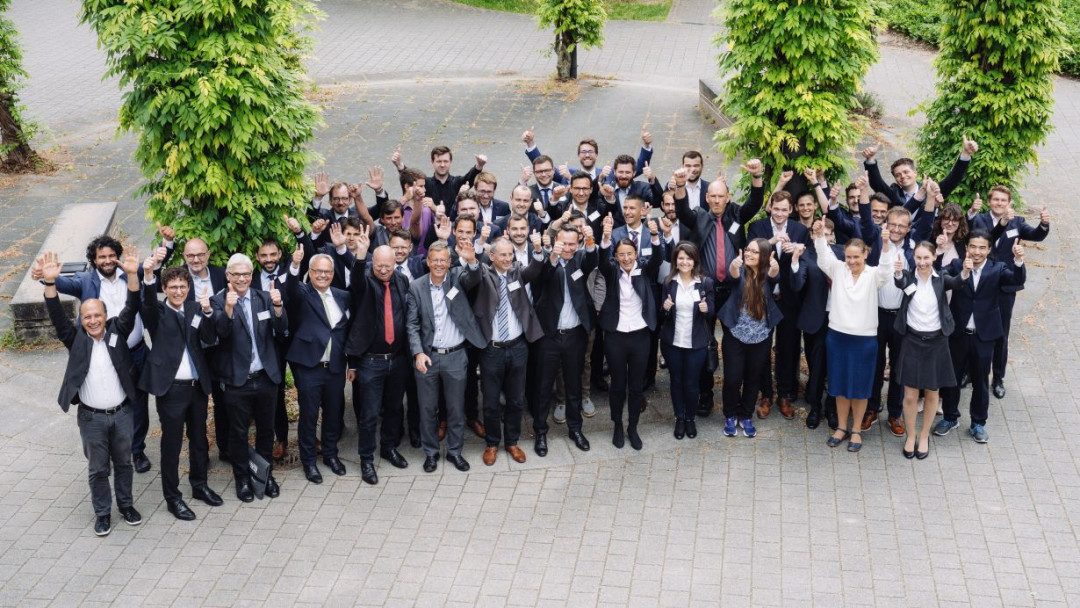
According to the Global Footprint Network, the rapid increase in global resource consumption means that around 1.75 Earths would have been needed to cover it in 2022. Researchers at the Karlsruhe Institute of Technology (KIT) want to fundamentally change the previous linear economic approach of "take, make, use, dispose". Their approach consists of circular processes in the circular economy: in the circular factory, used products are processed as automatically as possible so that they leave the factory as new products. This work is the focus of the new Collaborative Research Centre (CRC) 1574 "Circular Factory for the Perpetual Product" at KIT, which the German Research Foundation (DFG) is funding with around 11 million euros.
Manufacturing companies in particular are faced with the challenge of designing circular approaches economically in large-scale production. Today, these are still mostly carried out in small series with a high proportion of manual work steps at low-wage locations. For example, the proportion of materials recycled and fed back into the economy will only account for 7.2 per cent of all materials used in Europe in 2022 (see: www.circularity-gap.world/2023). "As a society, we cannot continue to simply dispose of the products we no longer need. In order to be able to utilise our resources in the long term, we need to consistently move towards a circular economy so that, in the best-case scenario, we can use products or their components forever. Corresponding circular economy approaches are the focus of the new CRC, which brings together the expertise of researchers from mechanical engineering, computer science, electrical engineering and information technology at KIT," says Professor Oliver Kraft, representing the President of KIT.
Vision of the eternal innovative product
Until now, remanufacturing, i.e. the refurbishment of used products, has been regarded as the process with the highest standard in terms of the quality and guarantee of the refurbished products. "It is the only circular process that can compete with a new product in these respects. However, the vision of the CRC 'Circular Factory' goes far beyond this. It is to make integrated linear and circular production of new products with individual refurbishment possible on an industrial scale," says Professor Gisela Lanza, Head of the wbk Institute for Production Technology at KIT and spokesperson for the CRC.
The circular factory is intended to transfer used products into current product generations in order to come closer to the vision of the eternal innovative product. Even if an "eternal" utilisation of used product substance does not appear to be practically feasible, the vision of the eternal innovative product is to be introduced. According to Lanza, this is comparable to the North Star, which represents the ideal state and towards which everything should be orientated.
"The Collaborative Research Centre 1574 marks a cornerstone in our research programme for the next decade at the wbk Institute of Production Engineering. Our fundamental research forms the basis for transforming the economy from linear to circular models and enabling a circular factory for the eternal, innovative product," explains Lanza. On this basis, she and her team want to launch numerous application-oriented collaborative projects with industry that will pave the way for a sustainable and innovative future.
Topics and project areas
In order to research the as yet unknown processes and mechanisms, the SFB team deals with scientific questions from production technology, product development and materials technology, ergonomics, robotics, computer science and knowledge modelling. The central questions are: How can new products be generated from unique used products? How can their functionality be guaranteed in the second life cycle? How can people learn complex problem-solving strategies and how can these strategies be transferred to automated production technology? How can this be implemented economically in a changeable, autonomous production system to enable circular production in large series at a high-wage location? How can data and information be utilised to further improve the process?
The SFB project is divided into three project areas: Project area A researches the planning and control of the circular factory in order to achieve maximum value retention of unique used products for the primary market, project area B designs measurement strategies for recording, modelling and evaluating the individual product condition as well as for recording and interpreting human process execution, and project area C creates a fully modular production system that enables continuous adaptation to ever new product instances. The construction of the circular factory on a laboratory scale is planned for the first funding period. The DFG is funding the project from 1 April 2024 to 31 December 2027 with around 11 million euros.