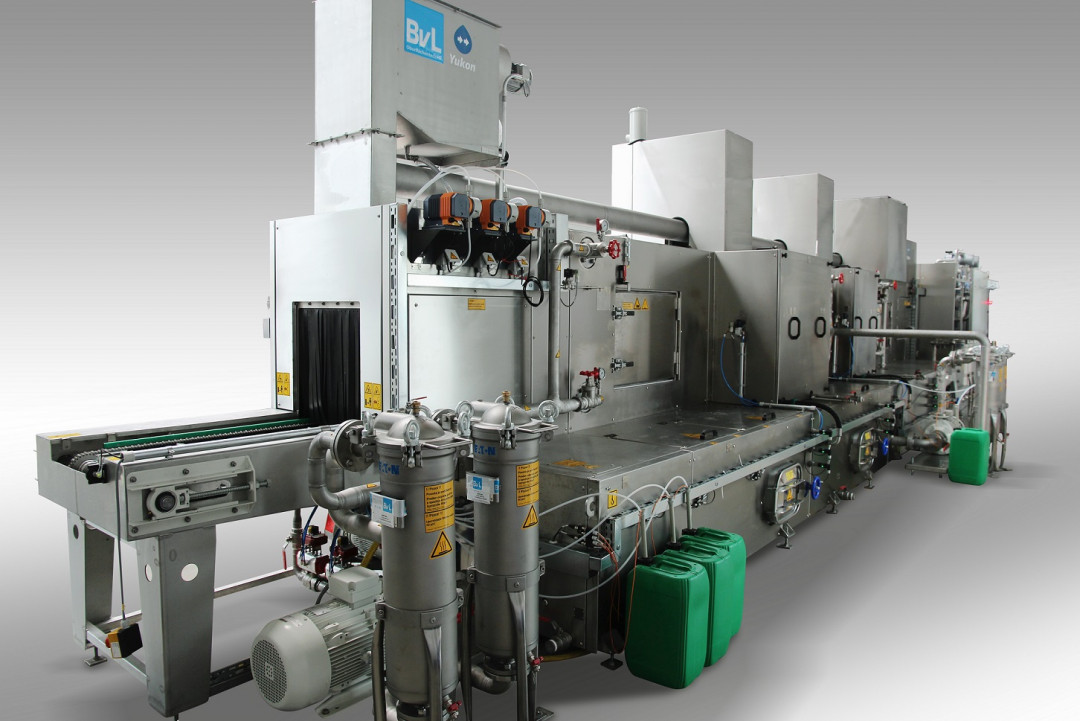
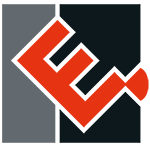
Even cast parts are not unaffected by the trend towards greater component cleanliness. The functionality of cast parts depends heavily on their cleanliness after machining. Cast parts must be thoroughly cleaned of chips, small burrs, oils and emulsions. Only then can they be used in the next processing steps without any problems or disruptions. Thoroughly cleaned castings reduce the risk of unforeseen failures and are an essential part of quality management.
At Euroguss, BvL Oberflächentechnik GmbH will be showcasing effective cleaning solutions that not only fulfil the highest cleanliness requirements, but also enable an economical process with fast throughput times. The diverse spectrum of cleaning systems from BvL ranges from small, compact washing systems to customised special solutions.
Continuous cleaning system for continuous material flow and high throughput
BvL Yukon continuous flow systems are ideal for foundries with a continuous material flow in the series production of components. Depending on the cleanliness requirements and the degree of soiling, washing, rinsing and drying processes are designed in one or more stages and are therefore customised. The nozzle arrangement in the cleaning zone is specifically adapted to the cast parts. This ensures thorough cleaning on all sides, even in the oil channels. The cleaning system can also be supplemented with a high-pressure zone for deburring cast parts. The individual treatment zones can be run through in cycles or continuously. The Yukon cleaning system is ideal for use as an inline solution. This enables an efficient cleaning process.
Space-saving basket washer for thorough cleaning of multiple castings in just one washing chamber
The BvL Niagara basket washer is suitable for thorough cleaning of several components in a basket or on product carriers in just one washing chamber. Cleaning is carried out using the spray/flood method. Depending on customer requirements, the system is supplemented by a swivelling or rotating pick-up system or a nozzle frame that rotates around the components. This ensures all-round cleaning of the cast parts and reliable cleaning results. The nozzles and nozzle frames of this type of cleaning system can also be customised to the component. Integrated vacuum drying in the cleaning chamber enables ideal further processing of the cast parts after the cleaning process.
Supplementary automation systems depending on customer requirements
The Niagara basket washer can be loaded and unloaded using a simple cross transfer table or automatically. In the case of automatic loading and unloading, e.g. by robot systems, the Niagara is supplemented with a roller conveyor, for example. This significantly reduces non-productive times. The use of a gantry loader or a shuttle system also further increases productivity and enables operation with fewer personnel. A double chamber version of the Niagara is also suitable for higher room capacities and for a particularly high throughput.
Process monitoring and quality control
Smart Cleaning gives BvL cleaning systems "intelligence". Changes in the cleaning process are immediately visible on the control panel. The intelligent system reacts autonomously in some cases when system statuses change, so that processes are optimised and operators no longer need to intervene. Predictive maintenance is also possible on the basis of real-time data. This enables efficient production planning and coordination and ensures a longer service life and higher machine availability.
Personalised advice at Euroguss
At Euroguss in Nuremberg from 16 to 18 January 2024, BvL will be providing information on innovative cleaning systems specifically for foundry requirements at stand 7-219 in hall 7 and offering detailed advice on customised solutions.