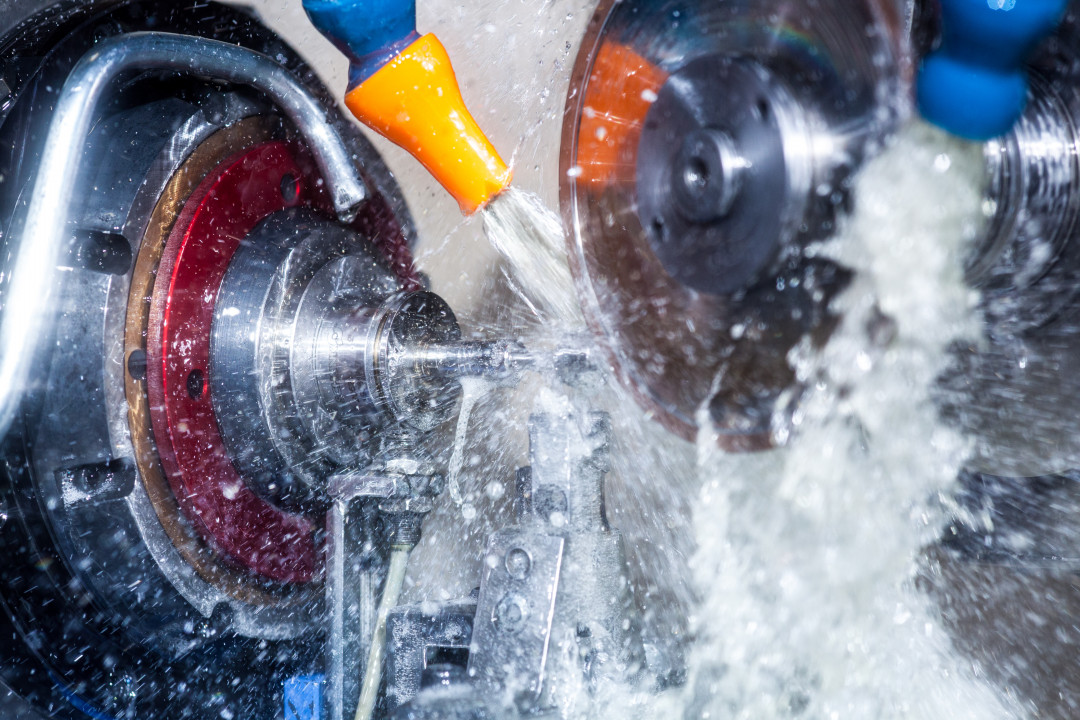
The changes in the automotive industry are confronting parts manufacturers with new tasks and requirements in the area of component cleaning as well. A holistic view of the process chain is required to meet these requirements in the best possible way, both technically and economically, as well as sustainably.
The transformation of mobility is having an impact on industrial component cleaning. Among other things, modified and new components are placing higher demands on particle cleanliness. ‘Depending on the component, this includes not only stricter specifications regarding particle number and size, but also, for example, specifications for fibres in the case of workpieces for traction batteries, since these can cause short circuits when wet,’ reports Kerstin Zübert, application engineer at Hermann Bantleon GmbH. ’The use of other manufacturing technologies, for example adhesive bonding and modern welding processes, also places higher demands on surface cleanliness. In this area, residual contamination in the form of films plays an important role,’ adds her colleague Julian Fischer. Another aspect that makes it necessary to adapt cleaning processes is changes in the materials. Examples of this are that parts that were previously made of cast steel can now be cast from lighter aluminium materials, or that components for injection systems for hydrogen propulsion have to be changed from cast to stainless steel. ‘Furthermore, we are seeing more and more companies expanding their value chain in order to be able to supply completely assembled and sometimes coated modules instead of individual components. This means that the technical cleanliness of production and assembly lines and of production equipment is becoming more important, i.e. topics that are dealt with in VDA 19, Part 2,’ explains Kerstin Zübert.
In most cases, it is not enough to see component cleaning as the only solution to this problem – at least not in terms of cost-effectiveness and resource conservation. This is because upstream processes have a significant influence on the cleaning effort and result. It is therefore advisable to look at the entire process chain. As a globally active system partner to the metalworking industry, Hermann Bantleon GmbH supports this holistic approach in close cooperation with customers and, if necessary, cleaning system and filter manufacturers. The Ulm-based company develops, produces and sells lubricants for the metal-cutting and metal-forming industry as well as cleaning and corrosion protection media worldwide. This product portfolio is complemented by a wide range of services, which always take sustainability aspects into account.
Regardless of the cleaning task, the aim is to avoid or minimise contamination. After all, if it is not applied to a component, it does not have to be removed. This insight is not new, but it is often neglected. ‘If you go through the production process with this process concept together with the customer, there are often starting points in the upstream processes to improve the cleaning result,’ says Julian Fischer from experience. It is often the case that relatively simple measures can be implemented to reduce the cleaning effort or to ensure that the required cleanliness specification is achieved with the existing cleaning equipment. In this way, customers often benefit from the company's good connections with other suppliers of industrial cleaning technology. ‘If, for example, the cleanliness standard is insufficient in terms of particulate cleanliness, we may go to the customer together with a filter manufacturer to find a solution that would allow the particles to be retained during the manufacturing process itself, rather than being applied to the component,’ explains Kerstin Zübert.
Another approach enabled a large automotive supplier to eliminate a particulate cleanliness problem when cleaning with an existing solvent system. Instead of placing the components in the cleaning system after production, they are rinsed with a dewatering corrosion protection product during the production process. This is sufficient to meet the particle requirements for this component. The previous cleaning process can be dispensed with, as can the effort involved in collecting, loading and unloading the parts. In addition, the thin corrosion protection layer allows the parts to be stored for a certain period of time without affecting the subsequent joining process. Previous corrosion problems have also been eliminated and scrap reduced to zero.
Whether the deciding factor for optimising a process is higher cleanliness requirements, modified materials or the demand for reduced production costs, the solution can also be an adapted cleaning medium. In doing so, conflicting requirements often have to be reconciled. This is demonstrated by an application in which bulk quantities of formed parts with particulate cleanliness specifications have to be cleaned. ‘Due to the type of contamination to be removed, this would actually be a job for aqueous cleaning. However, since this method cannot ensure that all parts come out of the system dry, we have developed a new solvent formulation that meets both requirements – particulate cleanliness and drying,’ reports Kerstin Zübert. When it comes to water-based cleaning, lower cleaning temperatures are one of the current topics for reasons of economic efficiency and sustainability. For example, an identically good result must be achieved at 45 °C instead of the classic 65 °C for the same process. ‘To ensure this, it is essential to take a close look at the customer's existing cleaning technology and test the possibilities together. This is the only way to avoid negative effects such as increased energy consumption during drying,’ notes Julian Fischer.
For both the redesign and the optimisation of cleaning processes, it is ideal for an efficient and sustainable solution if the media manufacturer and, if necessary, the cleaning system manufacturer are involved in the planning at an early stage.