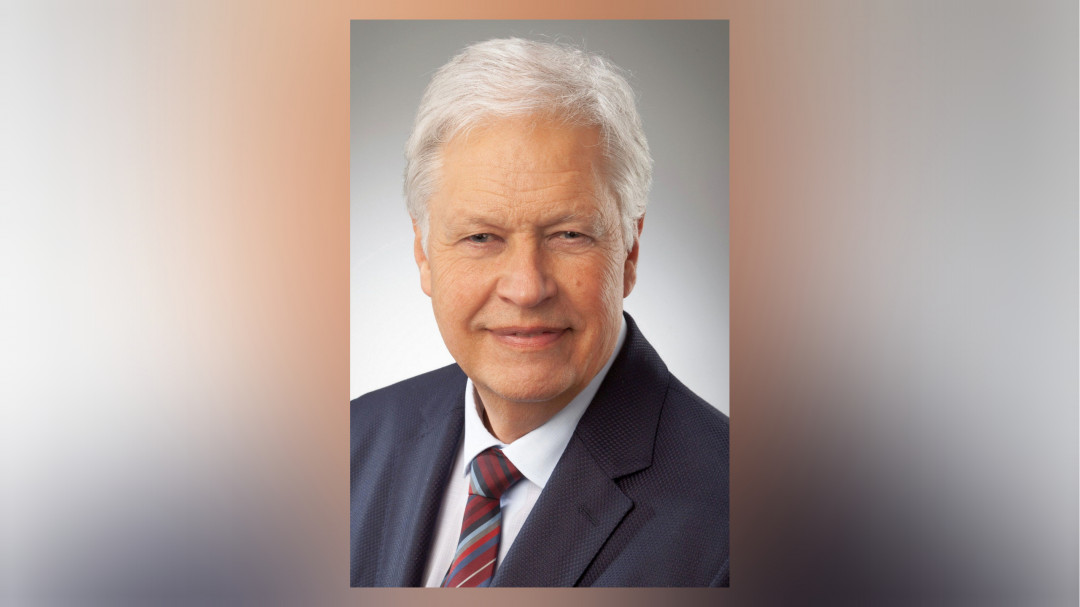
A robot-supported 3D sand printer, a large CNC milling machine for the production of polystyrene models, optimised machining processes and a wealth of experience in the production of moulded-in temperature control systems - innovative machine technology and craftsmanship form a highly efficient combination in the Blöcher foundry's range of services.
This is of particular benefit to manufacturers of large-format plastic parts who require sophisticated series tools made of aluminium for use in their thermoforming, vacuum casting, blow moulding or foaming systems. The Blöcher foundry is an attractive partner, especially when they frequently have to produce new moulded parts with modified geometries due to their customers' diversified component requirements - for example in automotive or container construction. "Thanks to our modern equipment, we are currently able to provide our customers with aluminium tool castings including cast-in temperature control systems for the production of large plastic parts with dimensions of up to 3,000 x 2,000 mm in less than three weeks," says company founder and Managing Director Jürgen Blöcher.
Flawless data sets as the basis
In the field of plastics technology, manufacturers of bodywork components for agricultural and construction machinery, producers of large transport containers and manufacturers of car roof boxes are among those currently utilising the services of the Blöcher foundry. "Word has got around among plastics processors that we can realise even demanding cavities with complex, near-contour tempering for the production of large blow-moulded, deep-drawn or foamed components at short notice," reports Jürgen Blöcher. An important basis for the rapid provision of aluminium tools is, of course, that the customer's designers supply complete 3D data sets in good quality.
If this requirement is met, Blöcher can fully utilise its expertise as a modern on-demand caster. In concrete terms, this means that the models for the large plastic parts are produced from expanded polystyrene (EPS) within a few hours in a recently modernised large five-axis CNC milling machine, while geometrically complex moulds made from modified quartz sand take shape fully automatically and robotically in the additive layer building process of a 3D sand printer. According to Jürgen Blöcher, "the use of these innovative technologies alone reduces the entire manufacturing process for a large mould by several weeks". The company achieves further time savings through the work of its in-house 3D CAD department, which can quickly implement design optimisations, as well as a 3D scanner, which ensures the geometric quality of the EPS models. This already results in process efficiency in the foundry's preliminary stages, which significantly reduces costs.
Casting instead of machining
In the past, the Blöcher foundry has also proven to be a competent partner for those customers who were looking for alternatives to machining from the block in mould making. Jürgen Blöcher reports: "Aluminium casting, as we practise it, has made many plastics processors realise how quickly tool casting is available today and how cost-effective it can be. Last but not least, the advantages that stainless steel temperature control integrated into the cavities offers in practice also speak in favour of casting." The tempering channels drilled directly into the solid block material using the deep-hole drilling method sometimes have acute-angled dead spots in which sludge pockets can form. As a result, they make it difficult to cool the mould in a controlled manner. In addition, some cooling water additives attack the aluminium surfaces of the drilled tempering channels, which can cause further process-related problems. These disadvantages do not usually occur with the stainless steel tube tempering of the aluminium mould castings cast into the cavities.