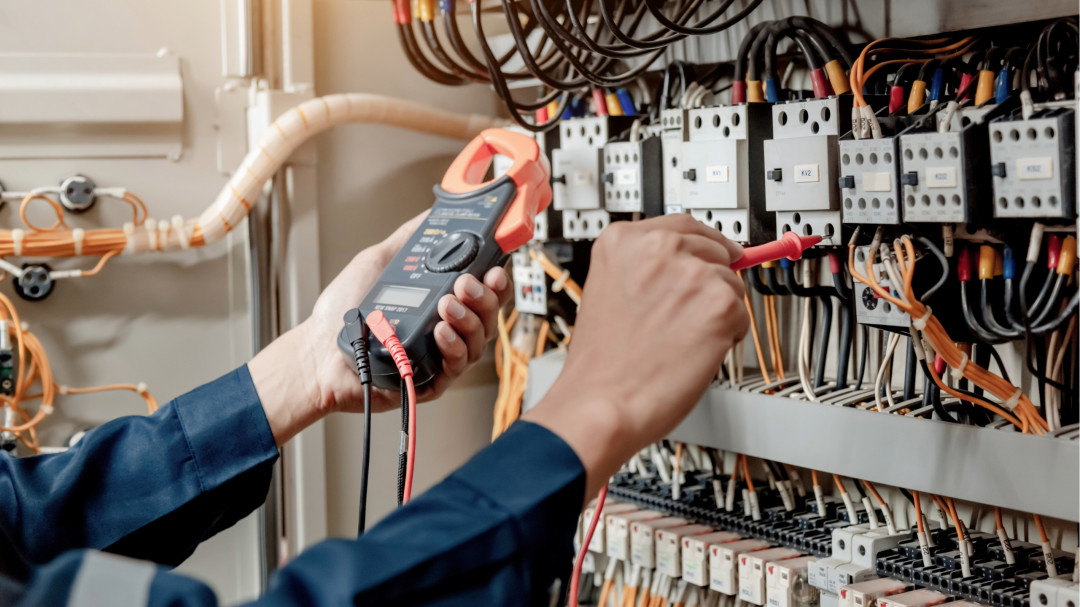
The Trimet aluminium smelter in Hamburg plans to replace parts of the busbar system of the electrolysis furnaces with superconductors. To this end, Vision Electric Superconductors GmbH (VESC) will install busbars made of superconducting material at the Trimet site, which will conduct electrical energy to the plants with almost no loss. This saves energy and reduces CO2 emissions.
Primary aluminium is produced using a process known as fused-salt electrolysis. This electrochemical process requires electricity as a raw material, which produces the light metal through a chemical reaction. However, some of the energy is lost when the electricity is transported to the electrolysis furnaces. This is because conventional busbars suffer losses due to electrical resistance. The new lines avoid these losses. The power rails developed by VESC are equipped with high-temperature superconductors, or HTSL for short. They are particularly suitable for applications with high DC currents and can transport electricity without loss. The technology has already been successfully tested in a pilot plant at the Trimet production plant in Voerde, where it set a world record: For the first time, HTSL was able to transmit electricity with a strength of 200,000 amperes. A superconductor line is now being built at Trimet Hamburg for the regular operation of the aluminium smelter.
‘As a system provider, we are very pleased to be installing the world's largest superconductor connection currently in use in industry for Trimet,’ says Dr. Wolfgang Reiser, managing partner of VESC. ’This flagship project will advance the industrial use of a technology that saves energy, contributes to climate protection and is also extremely material-efficient, since it requires only ten percent of the material of conventional lines.’
In the coming months, VESC will be installing a superconductor 600 metres in length in the Hamburg aluminium smelter that can transmit energy at a current strength of 200,000 amperes. Compared to conventional transmission systems, the HTSL saves more than 90 per cent of electrical power loss. This corresponds to the amount of energy consumed by 20,000 people in one year. Trimet is thus not only increasing the energy efficiency of its aluminium production, but also reducing carbon dioxide emissions. The new power transmission system saves around 8,000 tonnes of CO2 annually.
‘As an electricity-intensive materials producer, we take every opportunity to increase energy efficiency and minimise environmental impact. The innovative superconductor is a major step forward for us. It will enable us to further improve the ecological quality of our aluminium products,’ says Dr Andreas Lützerath, member of the Management Board of Trimet Aluminium SE.
The conversion of the power supply system in the Hamburg aluminium smelter is scheduled for completion by mid-2027. The project is being scientifically monitored by the Karlsruhe Institute of Technology and funded by the Federal Ministry for Economic Affairs and Climate Protection as a ‘real-life laboratory for the energy transition’.