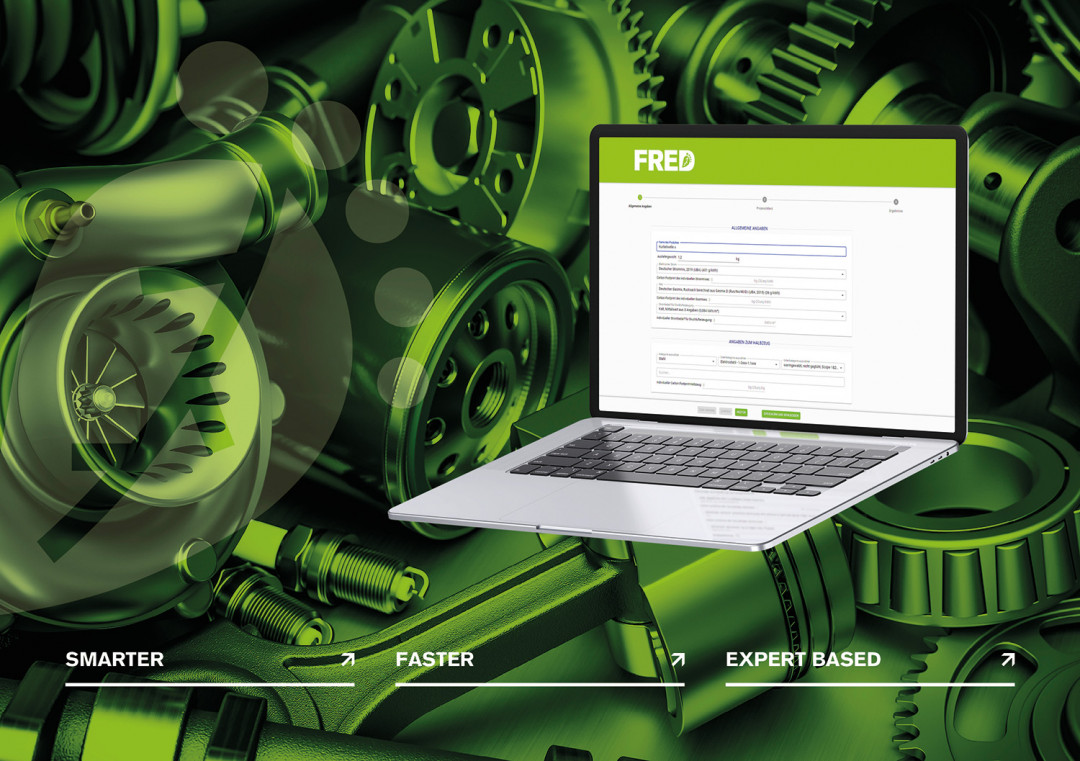
Europe wants to become climate-neutral; and the German foundry industry is transforming its processes to save CO2. As a founding member of FRED GmbH, the Federal Association of the German Foundry Industry has co-developed a CO2 calculation tool that is tailored to the processes in foundries. Companies can use it to calculate the CO2 footprint of products and companies and develop their individual decarbonisation strategy. FRED has now learnt to walk.
Innovation, flexibility and pragmatism have always been part of the foundry industry's DNA. With FRED, companies can now also prepare themselves for the future and the current challenges. The latest impetus for the launch was improved functions and increased user-friendliness of the CO2 calculation tool, as well as regular live demos, user consultation hours and user meetings - all of which can be booked on the FRED GmbH website. "With the August release, we have taken FRED to the next level," says FRED GmbH on LinkedIn. Foundries can find out more and order FRED at www.fred-footprint.de.
Expert knowledge as a basis
FRED is backed by the Federal Association of the German Foundry Industry (BDG), the German Steel and Metal Processing Association (WSM), the German Screw Association (DSV), the Iron Wire and Steel Wire Association (ESV), the Industrial Association for Massive Forming (IMU), the Association of Technical Plastic Products (TecPart) and the Association of the German Spring Industry (VDFI), which founded FRED GmbH in 2022. The German Surface Technology Association (ZVO) has been a new partner association since August. The Association of Metal Goods and Related Industries (FMI) has been a new cooperation partner since October. In this way, the supplier associations are setting the standards with a certified and generally recognised CO2 calculation tool instead of merely reacting to customer requirements or specifications from various service and IT groups.
This is because OEMs - particularly in vehicle, machine and plant construction - are increasingly making the product carbon footprint (PCF) of supplied products a delivery condition as part of their corporate strategies to reduce CO2 emissions. Foundries are therefore increasingly being asked to provide specific PCFs for the cast products they supply. "If you are asked by your customers and other stakeholders for a product-specific carbon footprint - with FRED, this can be determined in a process-specific and certified manner," says Elke Radtke, BDG Environmental and Occupational Safety Officer. She supported the development of FRED for the BDG.
Strategic corporate planning beyond the product
Elke Radtke is convinced by FRED, above all because the tool allows companies to go one step further than just the product. Foundries can also use FRED to determine their corporate carbon footprint (CCF). Companies can then build their entire decarbonisation strategy on the basis of the individually determined CCF. This is because the CCF visualises where most of the CO2 is generated during production. "The carbon footprint for the site forms the essential basis for designing a transformation strategy," explains the BDG consultant, adding: "FRED can be used to run through various scenarios for reducing greenhouse gas emissions in order to identify the most effective levers for this." One example of this is the calculation of the fictitious use of green electricity instead of the usual electricity mix in Germany.
What is special about FRED
The fact that FRED can also identify process- and site-specific CO2 reduction potential and can be used as the basis for a company's decarbonisation strategies is a key advantage over other footprint calculators. Another absolutely unique feature of the CO2 calculation tool is a reference database with real industrial data on energy and material consumption. Companies can access this secondary database if they do not yet have their own data for certain processes. It provides the benchmarks for their own primary data and temporarily bridges data gaps until their own data is available.
Potential standard for the supply industry - certified
Several supplier industry associations have joined forces for FRED in order to support their companies in providing reliable information on the CO2 footprint of their products, which is increasingly being demanded by OEMs. In this context, the BDG has promoted the foundry-specific solution for determining the PCFs of cast products. The focus is on the goal of establishing FRED as a certified PCF calculator for automotive OEMs. From the outset, the data was therefore recorded in accordance with the rulebook of the OEM data platform Catena-X, of which FRED has been a member since April 2023. Discussions are held on an ongoing basis with associations from the automotive, mechanical and plant engineering sectors, as well as with the companies themselves, in order to communicate the benefits of FRED. The methodology for PCF calculation has been confirmed by BMW and ZF and is certified by GUTcert in accordance with DIN EN ISO 14067. The methodology for calculating the CCF is currently also being validated in accordance with DIN EN ISO 14064.
FRED is being continuously developed and monitored by the advisory board
The update, which went live at the end of August, included additional or improved functions: the calculation of emissions by area, time or unit, the input of several primary materials at several points, the merging of PCFs, the differentiation of scopes for electricity, gas and other inputs (upstream chain statement), the specification of biogenic emissions, the calculation of the overall quality, the display of the mass of the individual process steps and materials in the results view. However, the associations continue to support FRED. It was not until mid-September that further opportunities for improvement were identified at the advisory board meeting. Elke Radtke's advice: "Don't wait - get started. FRED has the potential to make foundries fit for the future."
The advantages of FRED at a glance
> Reference database with primary data from foundries
> Modular, expandable structure
> Mapping of individual process chains and all influencing parameters of casting production with calculation of the resulting CO2 emissions
> PCF shown by process step (hotspot analysis) and by Scope 1 to 3
> Simulation of CO2-relevant effects from material, process, design or energy source adjustments
> System-independent (web-based) IT solution
> In- and out-interfaces to ERP systems possible
> Customised to foundry-specific processes
> Calculation based on real data from foundries
> Further development supported by experts from the Federal Association of the German Foundry Industry
All information and contact options at www.fred-footprint.de