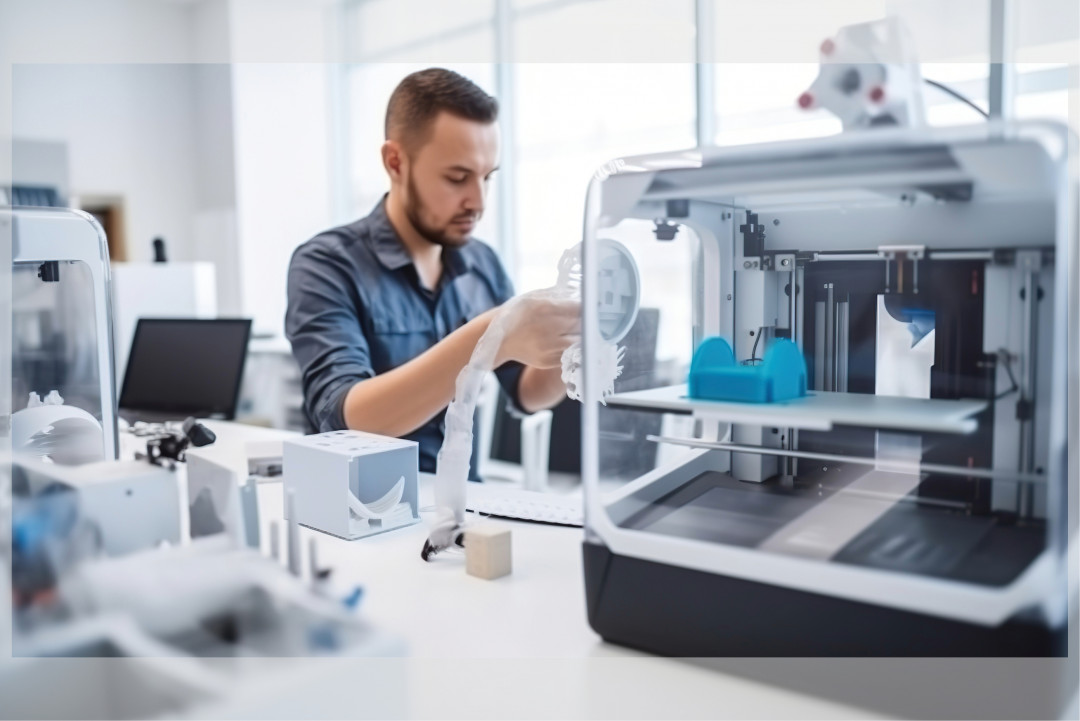
Additive manufacturing is increasingly becoming an everyday technology. However, as with any comparatively new process, there is still a lot of room for improvement. The Rostock scientist and engineer Erik Westphal is getting to the bottom of the process errors. He is using machine learning, a branch of artificial intelligence (AI).
Hardly any sector of business and industry today can do without three-dimensional printing. "But there are still significant obstacles. The quality of the printed components and the reproducibility of the printing process are not yet where they should be," says Erik Westphal. The 32-year-old mechanical engineer is currently conducting research at the Chair of Microfluidics at the University of Rostock under Professor Hermann Seitz to find ways to bring this future technology to a safe level and has already achieved considerable success.
He is using machine learning (ML), a sub-area of AI, for this purpose. "AI is not yet perfect in this area. We still have to train the computers for our purposes." AI actually means that the PC is as intelligent as a human being. "But that doesn't exist yet."
In 3D printing, for example, a workpiece is built up layer by layer from a meltable material (usually plastic) using the FDM process (fused deposition modelling). A powdery starting material is first melted or sintered in layers with a laser according to the desired component shape and then moulded. A new layer of powder is then applied and the process is repeated. This "selective laser sintering" process creates new 3D components from up to thousands of layers.
In the quality assurance process developed by Westphal, for which he had the initial idea back in 2019, the printing process is closely monitored by several cameras, documented by video and image and analysed directly by an ML algorithm. "Each image shows the layer that is currently being processed. Defects or impurities are recognised immediately by the algorithm." The algorithm developed by Westphal searches huge amounts of data for patterns that a human would not be able to see or find directly - for example, whether there is a defect in the current component layer, where it is located and what effects it has on the further printing process. "The aim is to use these patterns to automatically trigger human decisions."
"This method makes it possible to make the production process more stable," says Westphal. Previously, errors could not be recognised at all or, if they were, then only after the printing process. "Now you can decide during the printing process to optimise the print settings or cancel printing if the errors are too serious." This saves time and money - a tantalising prospect for business and industry. In addition, image data acquisition also provides detailed monitoring of the entire 3D printing process.
3D printing is used in the aerospace and medical technology sectors, for example, and enables new design freedoms and customisation options in particular. "It is very much on the rise in mechanical engineering," says Westphal. The new technology is also being used in pharmacology and even in the food sector. This makes it clear that a multi-billion market is growing here. The issue of quality control is therefore of considerable importance.