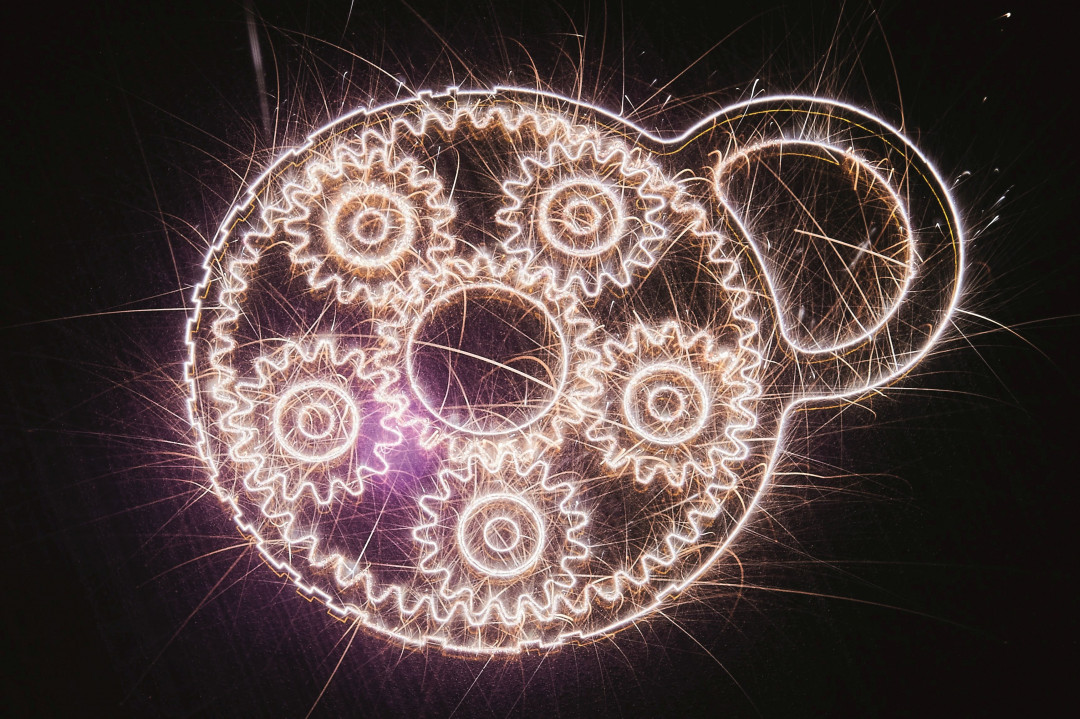
There are many different methods for 3D printing of metals. The most common is Laser Powder Bed Fusion (LPBF), in which lasers build up a workpiece by exposing metal powder layer by layer. The design data has to be converted several times along the process chain. This sometimes results in data volumes in the double-digit gigabyte range. Processing them not only takes time, but also pushes even modern IT systems to their limits.
A research team from the Departments of Laser Technology LLT and Digital Additive Production DAP at RWTH Aachen University and the Fraunhofer Institute for Laser Technology ILT in Aachen has developed a more practical solution. The new open vector format accelerates 3D printing, enables distributed data processing and simplifies the control of larger plant parks in addition to plant scaling. This is Industry 4.0 in practice.
Why a new data format?
The need for a new data format becomes clear when looking at the processes in the LPBF process chain. After design with a CAD program, the component contours must be converted into the smallest geometric structures in the second step. As a rule, these are triangles ("tessellation"). This is followed by the virtual fitting of the component into the installation space, whereby it is rotated and, if necessary, arranged with other parts in the virtual installation space in order to make optimum use of its volume ("nesting and orientation"). In this step, the design is also secured by any support structures. Up to this point, the data in the process is managed as three-dimensional coordinates.
This is followed by "slicing", which translates the 3D structure into thousands of 2D layers for the LPBF process. This is because LPBF systems spread out a fresh powder bed after each laser exposure, fix the intended component structure in it by laser and then move on to the next layer. In addition to the 2D contours of the respective layer, this process requires precise instructions for machine control.
This is where the need arises: while there are sufficient formats for 3D design data, the data after slicing is mainly processed using proprietary solutions from the respective LPBF system manufacturers. This is also due to the fact that standardized solutions from other areas, such as the "G-Code" format for CNC machines or the CLI format (Common layer interface), can only be used to a limited extent for 3D printing. For example, G-code is based on the storage of coordinates in text format (ASCII), which means that data volumes quickly swell to several tens of GB. Processing these data volumes is correspondingly time-consuming.
What can the new format do?
The new "Open Vector Format OVF" solution initially offers open structures so that users have full access to the geometry data. These are saved in a vector format based on the manufacturing process, which drastically reduces the size of the files compared to the text format. In addition, production information such as laser power or delay times during the scanning process can be saved in the new OVF. For multi-beam systems, the so-called scan feed allocation is also defined, i.e. the allocation to several beam sources. In detail, the format is based on the open source technology "Protocol Buffers", which Google also uses for structured data. Protocol Buffers defines an Interface Description Language (IDL), which was used to define the OVF data.
The format can be read by six programming languages supported by Google, and 30 other languages can also work with it. It is based on binary data. The layer-by-layer processing of data is important for 3D printing, which enables control via a network and thus greatly reduces local data storage. Experimental comparisons show that the new format is processed at a similar speed to proprietary formats from machine manufacturers - and therefore considerably faster than other open formats such as G-code.
Perspective: Integrating process monitoring, control via networks
The OVF also has strengths when it comes to process monitoring: in order to compare the contour of the workpiece with target data during machining, access to the design geometry must be guaranteed on the one hand and the possibility of comparison with 3D measurement data must be provided on the other. This is a central motivation for the development of the new format: OVF allows system developers to couple LPBF systems with an image processing system of their choice and link the data. This not only helps with quality assurance, but also makes it easier to compare the performance of different LPBF systems. This option is also available if several LPBF systems, including process monitoring, are controlled via a network.
Application in microstructuring
The automated comparison of target and actual data and the support of machine control via the network are also relevant for ablative processes such as laser micromachining. For this reason, researchers at RWTH Aachen University and Fraunhofer ILT are also interested in the use of the OVF format beyond the additive community. One example is the multi-beam process, which drills many small holes simultaneously. A camera system then checks whether these have been drilled through or whether there is still material residue. By comparing the camera data with the target geometry, a decision can be made as to whether and where reworking is necessary. The instructions for reworking can then be programmed directly in OVF.
For the community, with the community
Openness was an important concern for the programmers in the project. As researchers, the aim is to develop an optimal, manufacturer-independent solution based on input from the 3D community. The definition of the format is therefore available on GitHub. Tools for converting other formats into OVF are also available there. The platform also contains validation software that can be used to check OVF data records. A slice viewer that visualizes the individual slices is also planned.
You can find the OpenVectorFormat on GitHub here
The new format is already in use in the laboratories at RWTH Aachen University and Fraunhofer ILT. The researchers are in talks with manufacturers of 3D processing software and scanner manufacturers who want to integrate the format into their software.