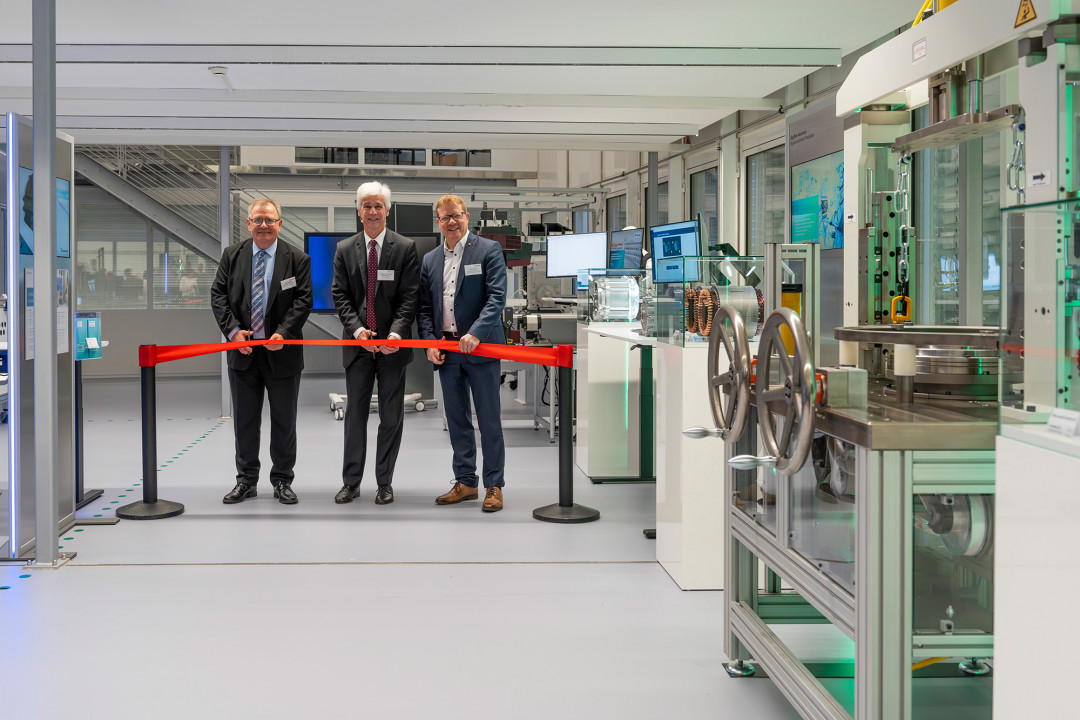
A new real-world laboratory was opened at the Berlin Centre for Production Technology (PTZ) as part of the 4th ReTraNetz-BB network forum. The laboratory supports the transformation of the automotive and supplier industry in the Berlin-Brandenburg region and offers a forward-looking space for the mobility transition.
The German automotive and supplier industry is coming under increasing pressure. Plans for redundancies and site closures are symptoms of a profound change in the industry due to the switch from combustion engines to more sustainable alternative drives. At the same time, new vehicle concepts are gaining in importance, for example for electrically powered small and micro vehicles, and creating additional pressure to innovate. This development poses substantial challenges for established manufacturers and suppliers, because it requires rapid but strategic adjustments along the entire value chain. What form should these take in order to remain competitive and innovative in the long term in a global market environment that is rapidly moving towards emission-free mobility? The aim of a new real-world laboratory at the PTZ Berlin is therefore to support the vehicle and supplier industry in the digital transformation towards more environmentally friendly and efficient production.
Prof. Dr. h. c. Dr.-Ing. Eckart Uhlmann, Director of the Fraunhofer Institute for Production Systems and Design Technology IPK and of the Department of Machine Tools and Manufacturing Engineering at the Institute for Machine Tools and Factory Operation IWF at the TU Berlin, officially opened the laboratory today at the start of the 4th Network Forum of the Regional Transformation Network for the Vehicle and Supply Industry Berlin-Brandenburg (ReTraNetz-BB). ‘The ReTraNetz-BB real-world laboratory offers practical support and empowers companies to successfully master the transformation. The network partners have clearly identified key challenges facing the industry, including energy monitoring and the shortage of skilled workers. The laboratory thus provides an important basis for future research projects, as well as for university teaching and the training and further education of skilled workers,’ said Prof. Uhlmann.
The laboratory offers everything needed to achieve these goals: modern manufacturing and assembly technologies for developing innovative process chains, a test environment for validating and optimising new technologies, and targeted knowledge transfer through practice-oriented training programmes. The digital production assistant researched in the laboratory could make a decisive contribution to overcoming the shortage of skilled workers. This assistance system can accompany skilled workers as a multilingual digital colleague through their daily production routine, independently of their level of training or language skills. In practice, it can be thought of as an app running on an edge device, such as a tablet. It communicates with the respective specialist via voice or text and provides data-based and real-time information on work organisation or processes, as well as specific step-by-step instructions for troubleshooting.
To ensure long-term impact and success in the transformation of the automotive and supplier industry, it is essential to maintain efforts to innovate in this area. Interested companies have the opportunity to use the laboratory as a test environment for their own developments. A modular Industrial Internet of Things (IIoT) infrastructure enables the flexible integration of new technologies. Production assistance systems and comprehensive energy monitoring support employees and help identify energy-saving potential.