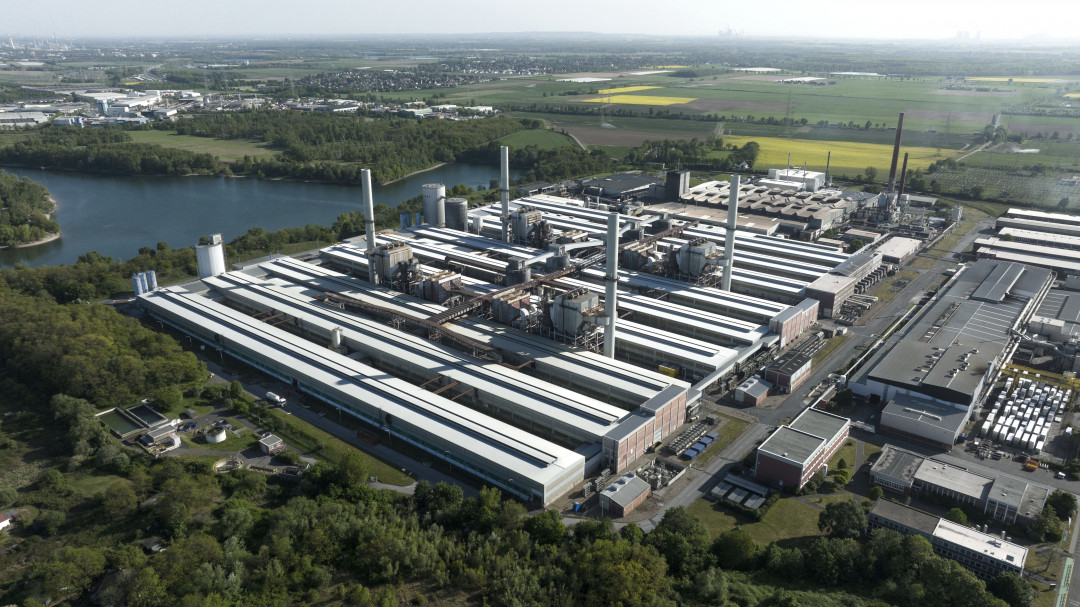
Speira is investing 40 million euros in further recycling capacity to develop the Rheinwerk and realise up to 1.5 million tonnes of CO2 savings per year at the site. The direction has been set for a long time: ‘We want to be the number one in aluminium recycling in Europe,’ explains Boris Kurth, head of the can business at Speira and of the recycling and foundry operations at the Rheinwerk. ‘Over the past 20 years, we have already built up significant recycling capacities at the site and Europe's most modern sorting plant for can scrap, thereby replacing the highly energy-intensive primary production of aluminium. We are consistently pursuing this path and emphasising our commitment to the circular economy with the fourth recycling furnace for the Rheinwerk."
The new furnace will be built in 2025. Production is scheduled to start at the beginning of 2026. At the same time, the third of four existing casting plants will be converted and optimised for recycling alloys. This will enable the Rheinwerk to further reduce its ecological footprint and will then have a recycling capacity that – compared to the primary production of the same quantity – saves up to 1.5 million tonnes of CO2.
The new furnace and the conversion of the casting plant are a step that will be followed by others. ‘We are developing the Rheinwerk, with its strategic location in the heart of Europe, into the leading “recycling hub”, a real hub for our industry. This is our long-term goal for our complete transformation,’ explains Kurth.
A third of the shut-down smelter will be home to the new scrap storage facility. This will not only provide storage space, but also facilities for sampling incoming scrap and preparing it for melting. ‘The long halls enable us to think and plan big. This huge new scrap storage facility will create space for the “feed” for all our recycling furnaces – not just the new one,’ Kurth says. ‘We need to sample the scrap that has already completed a life cycle. These “post-consumer scraps” are a source that we want to use much more.’ In addition, the storage areas for dross are being expanded in the foundry. Dross is the oxide layer that forms when liquid aluminium cools and is separated out to be recycled again.
The new recycling furnace will then be used to melt aluminium alloys that are processed into beverage cans after rolling. This is a market in which Speira can demonstrate its own sustainability ambitions particularly well. This is because the beverage can is a very fast-moving product, with a life cycle of only around 60 days from production to filling, retail sale, consumption by the end consumer, disposal and recycling. This means that the same aluminium can passes through Speira's recycling plants many times a year, and the ecological benefits of the latest technology can be utilised particularly often and particularly efficiently. This is why Speira is also committed to constantly improving the recycling rate for beverage cans: under the umbrella of the European Aluminium Association, the company is working with other manufacturers to research recycling-friendly alloys and is promoting deposit, return and collection systems for the valuable light metal.