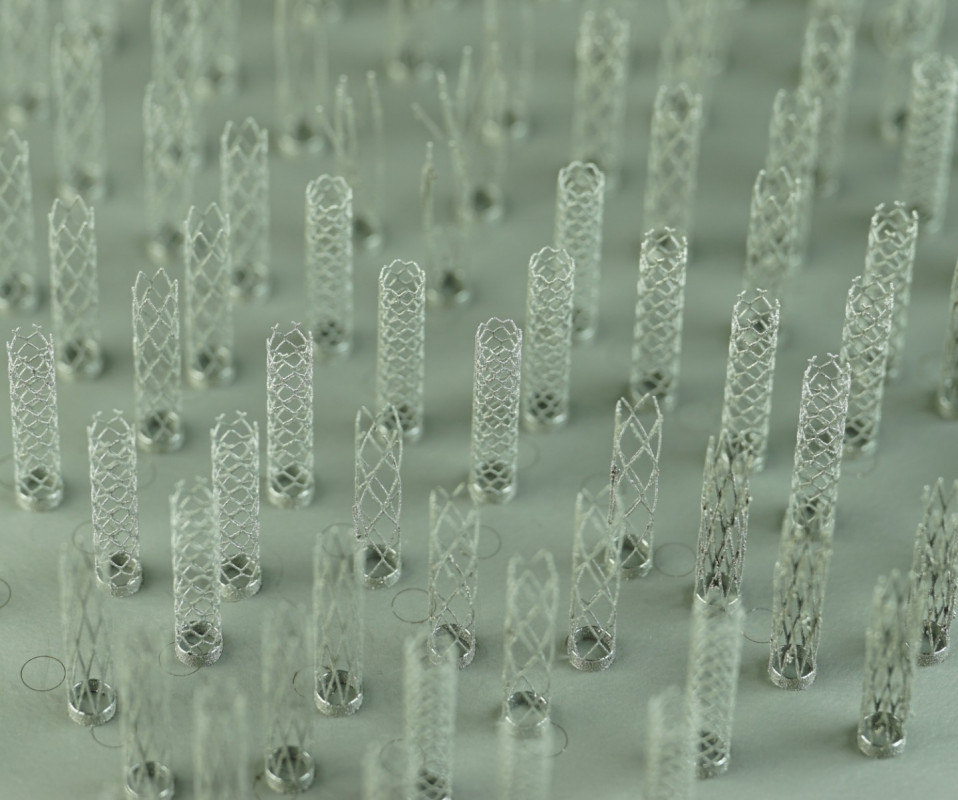
Am Dresdner Institutsteil des Fraunhofer IWU beschäftigen sich wissenschaftliche Mitarbeitende seit nunmehr 15 Jahren mit der additiven Technologie LPBF (Laser Powder Bed Fusion), bei dem ein Laserstrahl schichtweise metallisches Pulver lokal an den Stellen aufschmilzt, an denen das Bauteil entstehen soll. Um mit diesem Verfahren aus Pulver ein funktionierendes Bauteil entstehen zu lassen, bedarf es der Beherrschung der gesamten physischen als auch digitalen Prozesskette. Angepasste Scanstrategien, welche die Abfolge, Länge, Ausrichtung und Abstände der Laserbahnen definieren, sind für LPBF ein besonders erfolgversprechender Ansatz. Sie helfen, Bauteile filigraner, homogener, maßhaltiger und mit verbesserten Oberflächen herzustellen.
Forschung und Entwicklung erfolgen dabei in enger und langjähriger Kooperation mit dem Lehrstuhl Virtuelle Produktentwicklung (VPE) der Technischen Universität Dresden. Eine gemeinsame Softwarelösung, ermöglicht es nun, einzelne Scanbahnen gezielt zu verändern und den Scanbahnen innerhalb eines Bauteils separate Parametersätze (Laserleistung, Lasergeschwindigkeit, etc.) zuzuordnen.
Bei filigranen gitterähnlichen Strukturen gilt es, Stäbe zu drucken, die je nach Ausrichtung im Querschnitt einen Kreis oder eine Ellipse beschreiben. Statt einer Kontur-Hatch-Scanstrategie, bei der der Laser zunächst die Außenkontur abfährt und anschließend die Fläche füllt, kommt in diesem Anwendungsfall eine sogenannte Quasi-Punkt-Scanstrategie zum Einsatz. Dabei werden nur sehr kurze, teilweise gekreuzte, Scanbahnen mit dem Laser abgefahren. Dadurch gelingen gerade bei filigranen Bauteilen wesentlich präzisere Ergebnisse: In jeder Schicht und in jedem Abschnitt ist der Energieeintrag homogen, es bilden sich kaum Anhaftungen. Zusätzlich steigt die Produktivität erheblich, da der Laser wesentlich kürzere Strecken benötigt. Mit dieser Vorgehensweise lassen sich beispielsweise Implantate mit filigranen Gitterstrukturen wie etwa Stents herstellen, die insbesondere am Herzen oder im Gehirn verengte Blutbahnen offenhalten. Für ein möglichst schonendes Einsetzen ist es sinnvoll, auf superelastische Formgedächtnislegierungen (FGL) zurückzugreifen – in diesem Fall auf Nickel-Titan (NiTi).
Über Anwendungen in der Medizintechnik hinaus birgt die additive Verarbeitung von NiTi für Gitterstrukturen noch weiteres Potential. In einem Fraunhofer-internen Forschungsprojekt wurde ein Spann- und Halteelement für sprödbrechende Werkstoffe wie etwa Keramik entwickelt. Es weist ein lokal superelastisches Verhalten auf und verteilt die Punktbelastung auf eine vergrößerten Auflagefläche, um kritische Spannungen zu verhindern.
Feine, zellulare Strukturen, die für die Herstellung von Knochenimplantaten benötigt werden, können mit Hilfe einer geometriebezogenen Scanstrategie während der Erzeugung der Fertigungsdaten optimiert werden, wie das Beispiel eines am Fraunhofer IWU hergestellten Demonstrators eines Schulterkurzschaft-Implantats zeigt. Die Festlegung unterschiedlicher Bereiche mit spezifischen topographischen Eigenschaften (Brücken, zellulare und vollsolide Bereiche) erfolgt dabei durch eine automatisierte Geometrieerkennung. Diesen Teilbereichen werden unterschiedliche Scanstrategien und Laserparameter zugewiesen. Im Vergleich zum üblichen Fertigungsvorgehen (eine Scanstrategie und ein Laserparameter-Satz pro Bauteil) können die Maßhaltigkeit und der Verzug wesentlich verbessert werden. Für eine hohe Maßhaltigkeit der zellularen Strukturen ist es essenziell, alle Geometrie- und Prozessparameter ganzheitlich zu betrachten.
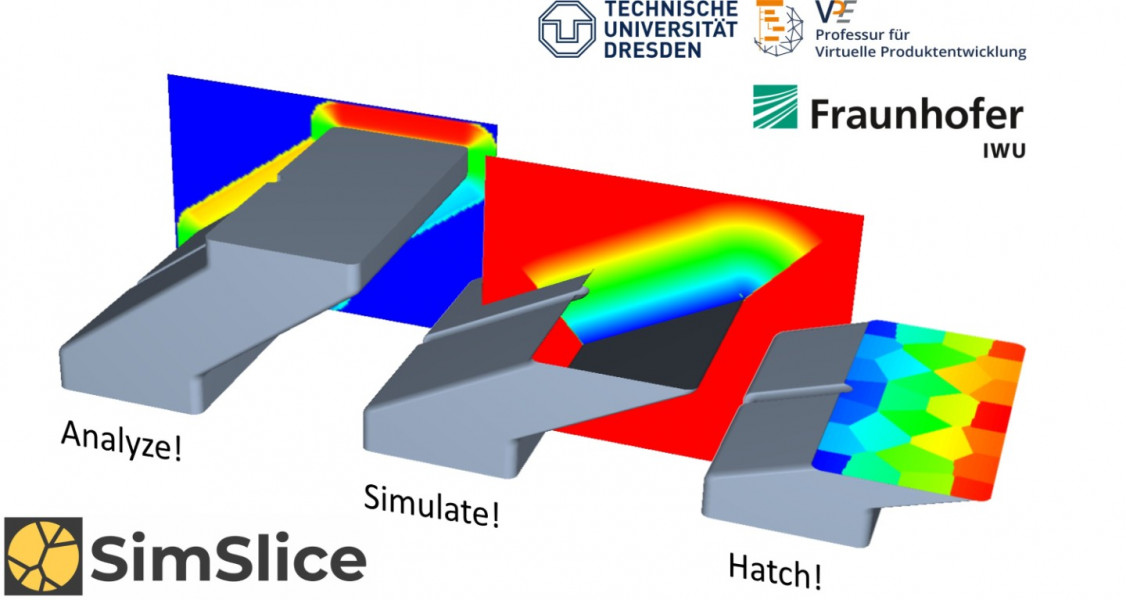
Das LPBF-Verfahren ermöglicht eine hohe Freiheit bei der Gestaltung von Geometrien. Besonders anspruchsvoll ist die zuverlässige Fertigung von Überhangbereichen mit hoher Qualität (Defektfreiheit, Maßhaltigkeit, Oberflächen-Rauheiten). Überhangbereiche entstehen, wenn beim Schichtaufbau höhere Ebenen darunterliegende überragen. Dabei sind oft Stützstrukturen – die das Bauteil für seine Funktion nicht benötigt – unvermeidlich.
Gemeinsam mit der Technischen Universität Dresden (Professur für VPE) entwickelt das Fraunhofer IWU einen Ansatz, um eine gleichbleibende Fertigungsqualität mit minimalem Verzug auch in den Überhangbereichen zu sichern und dennoch ohne Modifikationen an der Fertigungsanlage und mit weniger Stützstrukturen auszukommen. Der Schlüssel zum Erfolg ist eine Kombination aus automatisierter Analyse der zu fertigenden Geometrie, thermischer Simulation des Fertigungsprozesses und ausgeklügelter sogenannter Voronoi-basierter Scanstrategie. Die Analyse der zu fertigenden Geometrien zeigt dabei Stellen auf, die eine Anpassung der Fertigungsparameter erfordern: beispielsweise das Muster der Scanpfade, Teilbelichtungsflächengrößen, die Ausrichtung von Scanvektoren oder Abstände zwischen den Scanpfaden. Die Erzeugung der Teilbelichtungsflächen erfolgt mittels Voronoi-Diagrammen, einer mathematischen Methode, die basierend auf Saatpunkten, also Ausgangspunkten für das Wachstum der Teilbelichtungsflächen, die Scanebene in unterschiedlich große Zellen unterteilt.
Der große Vorteil hierbei ist, dass die Größe der Zellen über den Abstand der Saatpunkte stetig veränderbar bleibt und sich automatisch an die Geometrie des Bauteilquerschnitts anpasst. Zur Vermeidung von Fertigungsfehlern sollten zusätzlich die Laserparameter angepasst werden, um den geometrieabhängigen Temperaturverlauf beim Scannen bzw. Belichten zu berücksichtigen. Als Basis dafür dient eine überschlägige thermische Simulation, die auf einem neu entwickelten Ansatz beruht. Dieser führt zwar zu geringfügig ungenaueren Simulationsergebnissen, ist dafür aber wesentlich schneller.