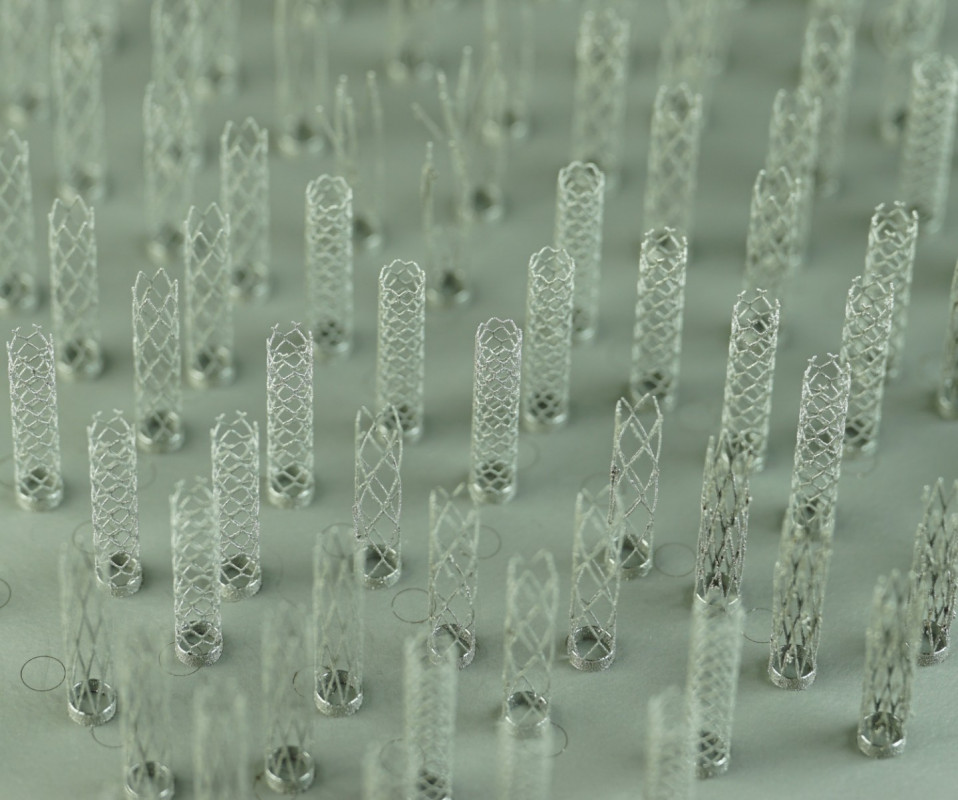
At the Dresden branch of the Fraunhofer IWU, research associates have been working for 15 years on the additive LPBF (Laser Powder Bed Fusion) technology, in which a laser beam melts metallic powder layer by layer locally at the points where the component is to be created. Mastering the entire physical and digital process chain is essential to turn powder into a functioning component using this process. Adapted scanning strategies, which define the sequence, length, orientation and spacing of the laser paths, are a particularly promising approach for LPBF. They help to produce components that are more filigree, homogeneous, dimensionally accurate and with improved surfaces.
Research and development in this area is carried out in close and long-standing cooperation with the Chair of Virtual Product Engineering (VPE) at the Technical University of Dresden. A joint software solution now makes it possible to modify individual scan paths in a targeted manner and to assign separate parameter sets (laser power, laser speed, etc.) to the scan paths within a component.
In the case of filigree lattice-like structures, the aim is to print rods that describe a circle or an ellipse in cross-section, depending on their orientation. Instead of a contour-hatch scan strategy, in which the laser first traces the outer contour and then fills the surface, a so-called quasi-point scan strategy is used in this application. In this process, only very short, partially crossed scan paths are traced with the laser. This results in significantly more precise results, especially for delicate components: the energy input is homogeneous in every layer and in every section, and there is hardly any adhesion. In addition, productivity increases significantly because the laser only has to travel much shorter distances. This approach can be used, for example, to manufacture implants with delicate lattice structures, such as stents, which keep constricted blood vessels open, particularly in the heart or brain. To ensure that insertion is as gentle as possible, it makes sense to use superelastic shape-memory alloys (SMA) – in this case, nickel-titanium (NiTi).
Beyond applications in medical technology, the additive processing of NiTi for lattice structures offers further potential. In an internal Fraunhofer research project, a clamping and holding element was developed for brittle-fracturing materials such as ceramics. It exhibits local superelastic behaviour and distributes the point load over an enlarged contact surface to prevent critical stresses.
Fine cellular structures, which are needed to manufacture bone implants, can be optimised with the help of a geometry-related scanning strategy during the generation of the manufacturing data, as shown by the example of a demonstrator of a short humeral implant produced at the Fraunhofer IWU. The definition of different areas with specific topographical properties (bridges, cellular and fully solid areas) is done by an automated geometry recognition. These sub-regions are assigned different scanning strategies and laser parameters. Compared to the conventional manufacturing process (one scanning strategy and one laser parameter set per component), the dimensional accuracy and distortion can be significantly improved. For high dimensional accuracy of the cellular structures, it is essential to consider all geometry and process parameters holistically.
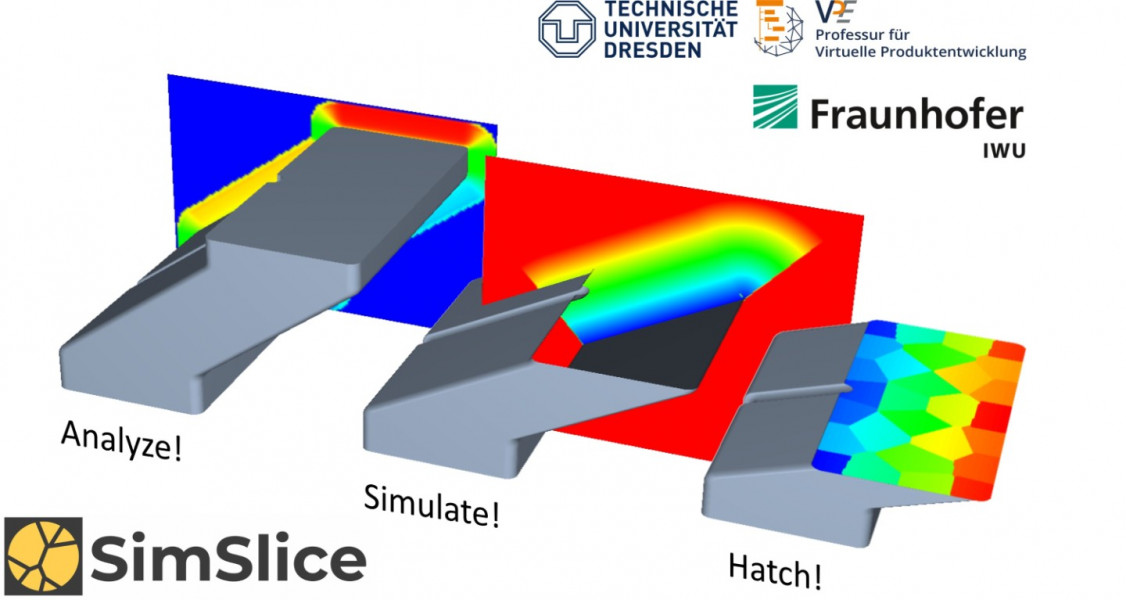
The LPBF process allows a high degree of freedom in the design of geometries. The reliable production of overhanging areas with high quality (freedom from defects, dimensional accuracy, surface roughness) is particularly challenging. Overhangs occur when higher levels overlap underlying levels during layer build-up. In this case, support structures that the component does not need for its function are often unavoidable.
Together with the Technical University of Dresden (Professorship for VPE), the Fraunhofer IWU is developing an approach to ensure consistent manufacturing quality with minimal distortion even in the overhang areas, yet without modifications to the manufacturing plant and with fewer support structures. The key to success is a combination of automated analysis of the geometry to be produced, thermal simulation of the manufacturing process and a sophisticated so-called Voronoi-based scanning strategy. The analysis of the geometries to be produced reveals points that require an adjustment of the manufacturing parameters: for example, the pattern of the scan paths, partial exposure area sizes, the alignment of scan vectors or distances between the scan paths. The partial exposure areas are generated using Voronoi diagrams, a mathematical method that subdivides the scan plane into cells of different sizes based on seed points, i.e. starting points for the growth of the partial exposure areas.
The great advantage here is that the size of the cells can be continuously varied via the distance between the seed points and automatically adapts to the geometry of the component cross-section. To avoid manufacturing defects, the laser parameters should also be adjusted to take into account the geometry-dependent temperature profile during scanning and exposure. A rough thermal simulation based on a newly developed approach serves as a basis for this. Although this leads to slightly less accurate simulation results, it is considerably faster.