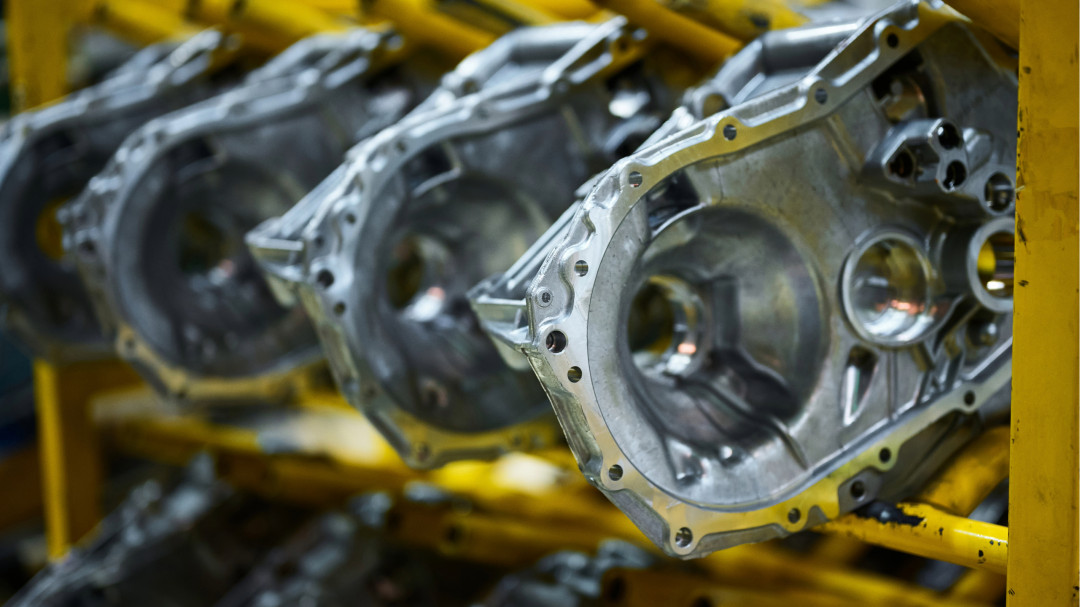
BY PROFESSOR DR KLAUS EIGENFELD
The individual phases of human development are characterised by the main materials used at the time. Thus, human life developed from the Stone Age, which began around 200,000 years ago with the predominant use of stone tools and wood, to the ceramic age, in which artificially produced ceramic masses were already being used in a wide range of applications. A significant leap forward was made in the Copper and Bronze Ages with the mastery of metalworking techniques and their use in everyday life. The third major period in the simple chronological division of the three-period system is the Iron Age. In southern Europe, it extends from around 800 BC to around the time of Christ, and in northern Central Europe from around 750 BC to the 5th century AD. This was the period in which the industrial revolution took place, a revolutionary transformation of economic and social conditions, as well as working and living conditions, that continues to this day. It began in the second half of the 18th century and especially in the 19th century, initially in England, and then spread throughout the world.
This enormous change was characterised by three major fields, in addition to the social changes:
- the mechanisation of manual labour through machines,
- the generation and conversion of mechanical energy, primarily through the steam engine and the use of electricity,
- the large-scale industrial use of the raw materials coal and iron.
This was accompanied by the beginning of a new era of mobility. The expansion of the railway network, steam navigation, the beginning of individual motorisation and the conquest of the third dimension, aviation, opened up new and wide fields of activity for technology. The predominant idea was that of lightweight construction, since reduced masses are considerably more economical to move. This was the beginning of a ‘new era’, the age of light metals.
Light metals are now elements with a density of less than 5 kg/dm3. Table 1 shows the complete list of all light metals with their densities in kg/dm3 at 20 °C.
Lithium 0,53 | Magnesium 1,74 | Aluminium 2,70 |
Kalium 0,86 | Beryllium 1,85 | Scandium 2,99 |
Natrium 0,97 | Francium 1,87 | Barium 3,65 |
Rubidium 1,53 | Caesium 1,90 | Yttrium 4,47 |
Calzium 1,54 | Strontium 2,63 | Titan 4,50 |
Table 1: Density of light metals in kg/dm3
However, of the elements listed, only magnesium, aluminium, titanium and, to a lesser extent, beryllium are of any relevance as independent construction materials. If we look at the history of the discovery of these light metals, it is striking that they were all discovered between 1754 and 1798. However, only aluminium and magnesium were the first to be used for technical applications, with the material magnesium – the German metal – playing a special role in Germany due to political and economic circumstances.
Magnesium
Magnesium is the lightest metal for technical construction applications, with a density of 1.738 kg/dm³ at 20 °C. It is a chemical element with the symbol Mg and atomic number 12. In the periodic table of the elements, it is in the second main group and thus belongs to the alkaline earth metals. Its mass fraction in the earth's crust is approximately 1.94%, making it one of the ten most abundant elements. This means that magnesium will be available in sufficient quantities for the future. Pure magnesium has only very low strength and hardness. This means that it can only be used for technical applications in the form of alloys. The modulus of elasticity is approximately 45 gigapascals, which means that components designed for rigidity must take this into account. It is not possible to reduce the weight of magnesium compared to aluminium in terms of density; realistically, weight savings of around 20% can be assumed. Magnesium has a hexagonal crystal structure and therefore has only a low formability at room temperature due to the lack of slip planes. In technical forming processes, the workpieces must therefore be preheated accordingly. The melting point is 923 K (650 °C) and the boiling point is 1383 K (1110 °C). The low melting point and the fact that it is not aggressive towards iron-based materials means that magnesium can be melted cheaply in iron crucibles and cast in permanent moulds. Its thermal conductivity is 160 W/mK, which is significantly lower than that of aluminium (235 W/mK). This means that magnesium alloys cannot be used for components that are subject to high thermal loads, such as cylinder heads of internal combustion engines. The same applies to electrical conductivity. Magnesium has a standard potential of -2.372 V, which means that it is highly electronegative (Mg2+ + 2e- Mg). When exposed to air, magnesium forms an oxide layer that, unlike aluminium, is not completely covering. It is therefore not highly resistant to corrosion. For many applications, particularly in corrosive environments, additional surface protection is therefore necessary.
Discovery
Magnesium was already known in the form of its compounds in ancient times. The name magnesium probably comes from the Greek and means either magnet stone or magnesia, after a region in Greece, or magnesia, after a city in what is now Turkey. Magnesium carbonate was usually referred to as magnesia alba, and magnesium oxide as magnesia.
It was the Scottish physicist and chemist Joseph Black (1728-1799) who carried out the first fundamental research into these compounds. In 1755, in his dissertation ‘De humore acido a cibis orto et Magnesia alba’, he described the difference between calcium carbonate and magnesium carbonate, magnesia alba. He interpreted this as the carbonate of a previously unknown element. For this reason, we can call Black the first discoverer of magnesium, although he never produced it in metallic form himself. Half a century later, in 1808, Sir Humphrey Davy (1778-1829) produced magnesium by electrolysis of magnesium hydroxide. However, he did not produce it in its pure form, but as an amalgam, because he used mercury in his process. It was not until 1828 that the French pharmacist and chemist Antoine Bussy (1794–1882) heated dry magnesium chloride with potassium as a reducing agent and produced small amounts of pure magnesium. In the chronological sequence, the English chemist Michael Faraday (1791–1867) then produced magnesium by electrolysis of molten magnesium chloride. Based on this work, the German chemist Robert Wilhelm Bunsen (1811-1899), who is best known for developing the Bunsen burner, developed electrolysis cells for the production of new elements in the years 1840-1860. In addition to magnesium, this also involved numerous other metals such as chromium, aluminium, manganese, sodium, barium, calcium and lithium in elemental form. Together with Gustav Robert Kirchhoff, he also discovered the two light metals caesium and rubidium in 1861. Building on this work, the German magnesium industry began to develop, and for many years up to the end of the Second World War it was to be the world leader in this field.
Industrial production
Like most metals, except for the precious metals, magnesium does not occur naturally in its pure form, particularly due to its electronegativity. As a mineral, it occurs primarily in the form of carbonates, silicates, chlorides and sulphates. A magnesium-containing mineral even forms an entire mountain range, the Dolomites in Italy, in the form of dolomite. The most important minerals for magnesium production are dolomite CaMg(CO3)2, magnesite (magnesia) MgCO3, olivine (Mg, Fe)2 [SiO4], enstatite MgSiO3 and kieserite MgSO4 · H2O. Other sources include serpentine Mg3[Si2O5] (OH)4, spinel MgAl2O4 and carnallite KMgCl3 · 6 H2O. In addition to its discovery site in Staßfurt in Saxony-Anhalt, this mineral has been found in Germany in the potash mines of Heringen and Philippsthal and in the Werratal in Hesse, among other places. Some of these deposits then became the sites of magnesium smelters, as will be explained later.
Another almost inexhaustible reservoir of magnesium is salt water, for example classic seawater. This contains more than 1 kg/m3 of magnesium. However, this situation is used in a different way. Dead Sea Magnesium Ltd. at the Dead Sea in Israel used the highly saline water to extract bromine salts for photographic and pharmaceutical purposes. Large deposits of magnesium-containing salts and minerals such as carnallite remained. Magnesium production then began with these, which is now fed by highly saline brines. In principle, two different process types are mainly used to produce metallic magnesium:
- fused-salt electrolysis
- thermal reduction
By fused-salt electrolysis of molten magnesium chloride in Downs cells: Downs cells consist of large iron troughs that are heated from below. Graphite rods inserted from above serve as anodes, which are surrounded at the tips by a ring-shaped cathode. The metallic magnesium collects on the salt melt and is skimmed off. The resulting chlorine gas collects in the upper part of the cell and is reused to produce magnesium chloride from magnesium oxide. To lower the melting point of magnesium chloride, calcium chloride and sodium chloride are added to the molten salt.
It should be noted that electrolysis to produce metallic magnesium is very energy-intensive. Today, around 35 kWh are required to produce 1 kg of magnesium. However, when aluminium parts are substituted, it should be noted that, due to the technological properties, around 20% of the weight can be saved, which puts the energy consumption into perspective.
Small-scale production began in Germany at the Aluminium und Magnesiumfabrik A.G. in Hemelingen near Bremen in 1886. In 1893, Elektro-Chemische Werke GmbH, Berlin, built a chemical factory to produce caustic soda and chlorinated lime. In the same year, Chemische Fabrik Elektron AG, Frankfurt/Main, a subsidiary of Chemische Fabrik Griesheim, decided to establish a branch in Bitterfeld; the two companies then merged in 1894. In 1925, this became the IG Farben group, and magnesium production increased rapidly. In 1944, the workforce numbered around 16,000 due to the war.
At the same time, Wintershall A.G. built a magnesium production plant in Heringen an der Werra, which began operations in 1935. The brand name was MAGNEWIN: MAGNEsium from WINtershall. Further processing such as forging and extrusion for profiles was also carried out here.
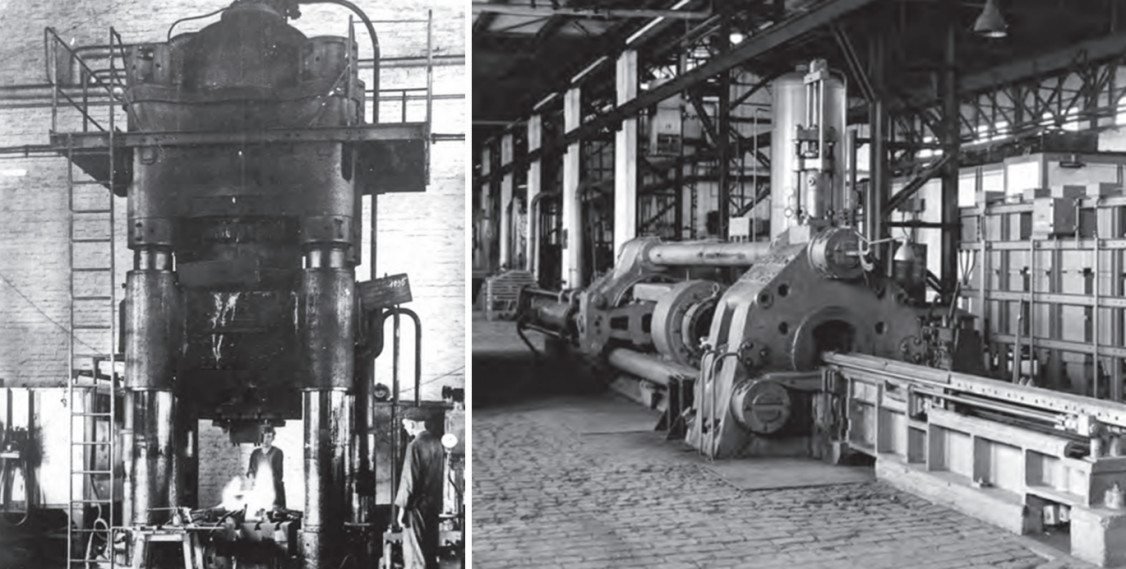
In 1938, the Societá anonima italiana magnesio SAIM in Bolzano was established as Europe's second largest magnesium plant at the time, due to the start of production of the VW Beetle with magnesium engine and gearbox housings. During the war, 8,000 tonnes per year were produced using electrolytic methods with the abundant supply of electricity from Montecatini, and in the 1960s, 35,000 tonnes per year were produced, primarily for VW AG. The company went bankrupt in 1991. However, magnesium activities were also initiated outside Germany. For example, Magnesium Electron Ltd. was founded by I.G. Farbenindustrie AG in Swinton near Manchester in 1938. Today, the company mainly supplies special alloys, particularly high-strength and high-temperature alloys.
The demand for magnesium and for further production sites increased due to the war. From 1940, an expansion of light metal production, in particular of magnesium from seawater (content ~ 1.30 – 1.35 kg/dm3), which had already been started by Norsk Hydro, was therefore carried out under the management of I.G. Farbenindustrie A.G. However, production in Porsgrunn did not get off the ground, as the almost completed facilities were almost completely destroyed by an air raid by the Royal Air Force in July 1943 and were not rebuilt at the time. This did not take place until after the war, when Norsk Hydro rebuilt them.
However, as primary production increased, so did the expansion of the downstream production steps. One example of this is the company Edmund Becker & Co. A.G., Metallgussgesellschaft MEGU in Leipzig W 35, which from around 1923 was the largest magnesium foundry in the world, with a wide range of products, and also presented itself with extensive magnesium brochures and at events and trade fairs. However, mechanical production was also not inferior to the volume of previous production. Mahle, from 1924 Elektronmetall GmbH, from 1938 MAHLE KG, plant Stuttgart Bad Cannstatt, was dedicated to the production of pistons and the series production of magnesium aviation components, during the war also using forced labour.
Products
The properties of magnesium alloys are optimally suited for a large number of applications. The low density is ideal for moving masses. The main areas of application are hand-held machine tools, transport technology and, in particular, aircraft construction. The good damping properties, especially with coarse-grained sand casting, similar to cast iron with lamellar graphite, opened up areas of application in machine tool beds. The excellent behaviour in die casting, coupled with a significantly longer mould life compared to aluminium, then opened up a wide range of applications for the material.
Mechanical engineering
Examples of hand-held machines include drills, angle grinders, circular saws, nibblers and many more. Since robot technology did not yet exist, series processes such as spot welding also had to be carried out by hand. Here too, every gram of weight saved was helpful, which is why the electron arm was used for a spot welding gun. However, magnesium casting was also used for large machine tools. The Hettner radial drilling machine had a gearbox housing with spindle bearings made of this material. Another outstanding example is the machine bed and headstock of a Boehringer lathe, where the high damping capacity of magnesium, among other things, played a role. In addition, the lower weight of the machine also made it easier to transport and thus suitable for use in mobile workshops in the military sector. Explosive rams, known as ‘Delmag Frogs’, weighing 100, 250 and 500 kg were used for soil compaction, particularly for road construction. The cooling jackets and cylinder heads of these devices were made of magnesium sand casting. Components for Hollerith machines and spinning machines were also made of magnesium casting. The bodies of the Hollerith machines had a base plate and machine feet made of electron sand casting, while the stiffening supports were made of pressed electron sheet metal. Since spinning machines in particular have high operating speeds, reducing the weight of moving masses is urgently required. In 1938, for example, hooded wings made of electron chill casting were used in gill spinning machines (dry spinning frames) from the company Haas u. Kellhofer in Singen. A less well-known application for electron casting was in forming dies. These were used in the forming of steel sheet, but especially aluminium sheet. The counterparts were often made of hard rubber. The main customer was the aircraft industry, as the quantities were manageable. After the production sample was discontinued, the dies were melted down and cast into a new one.
Transport technology
The rapidly increasing mobility in Germany called for means of transport that were suitable for series production, could be manufactured cost-effectively and with existing resources. Magnesium casting with the possibilities of functional integration was a natural choice here. In addition, magnesium was produced in the country itself. With these conditions, a wide range of projects were then tackled, some of which had questionable conceptual ideas. One such project was the ‘cast-iron two-wheeled car’ from MOTAG, Leipzig 1923/24. The vehicle, which was presented at the 1923 Berlin Motor Show with two-cylinder OHV engines with a capacity of 500–800 cc, was available with either air or water cooling. The engine and gearbox housings, the multi-part frame with integrated petrol tank, mudguards and various other parts were made of cast magnesium and weighed around 43 kg. Nothing is known about sales success. A few years later, in 1926, the ADLER - Werke vorm. H. Kleyer A.G., Frankfurt am Main, then produced the Standard 6 and 1928 Standard 8 car models with a very high magnesium cast iron content.
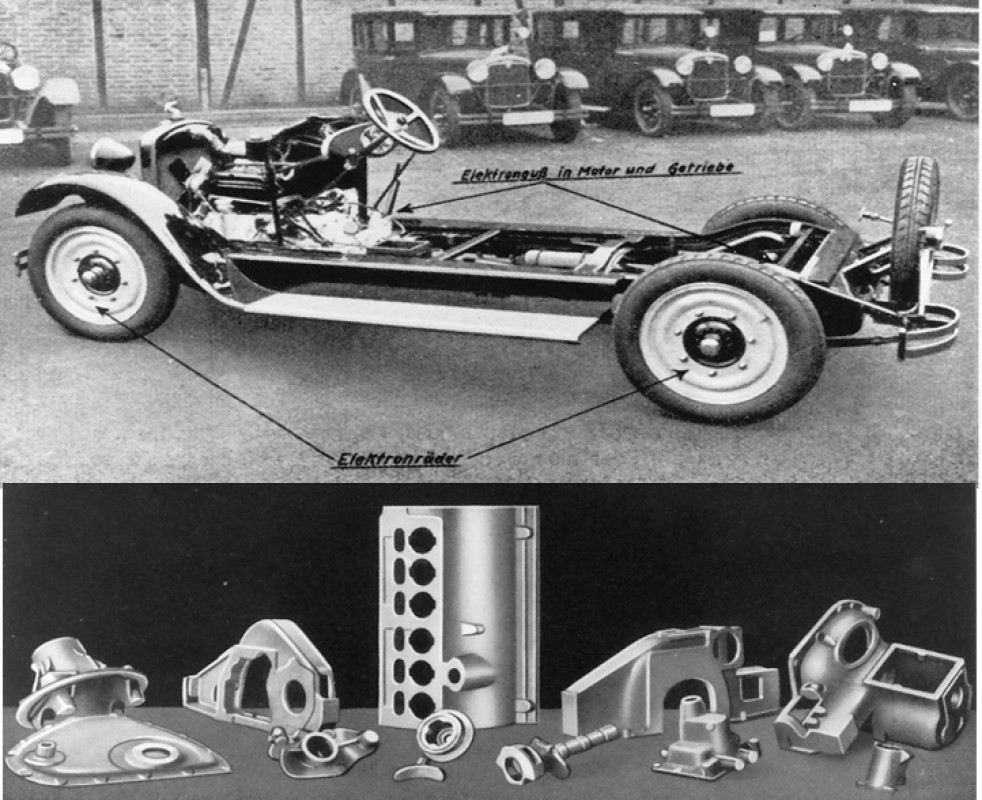
In doing so, ADLER was able to draw on its experience in the aviation industry, as we will see later. The two vehicle types featured sand-cast disc wheels, crankcases, chain cases and chain case covers, flywheel housings, gearboxes with various covers, as well as the rear axle gearbox and, in die-cast, which was then called injection moulding, bearings, tappet guides and covers. The weight of the magnesium parts was 73.8 kg for the 6-cylinder and 86.8 kg for the 8-cylinder. A total of almost 30,000 6-cylinder engines were sold. Another engine manufacturer also took a new approach when it presented a water-cooled engine block made of cast magnesium in 1927.
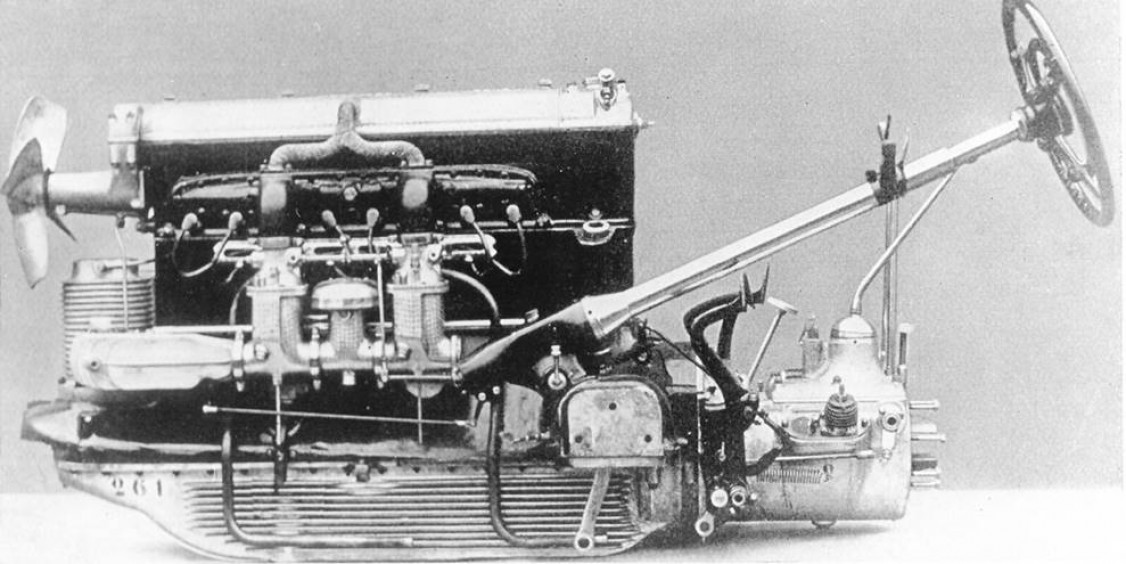
To prevent corrosion, sodium dichromate was added to the cooling water. However, engine components that were subject to extreme mechanical and thermal stress were also made of magnesium. Mahle GmbH, which was renamed Elektronmetall GmbH in 1924, also advertised magnesium pistons for use in series-produced engines on a poster from that year. As early as 1921, magnesium pistons had already proven their performance capabilities by taking first, third and ninth place in the 500 Miles of Indianapolis with Dowmetal pistons (USA). Another magnesium highlight was the Bugatti Type 57 Aerolithe experimental car at the 1935 Paris Motor Show, whose body was made entirely of magnesium sheet metal. Since there were no suitable welding processes for distortion-free welds on thin sheets at that time, the joints were folded and riveted, which can be seen on the wings and roof. In contrast, the omnibus trailers of the German Reichspost were produced in series, with a structure made entirely of magnesium. Pressed magnesium profiles were connected by deep-drawn magnesium sheet metal joints, thus representing an early form of ‘space frame’. This was planked with magnesium sheet metal that had been deep-drawn at a preheating temperature, which at the same time took over part of the structural strength. Four people could easily lift the entire structure.
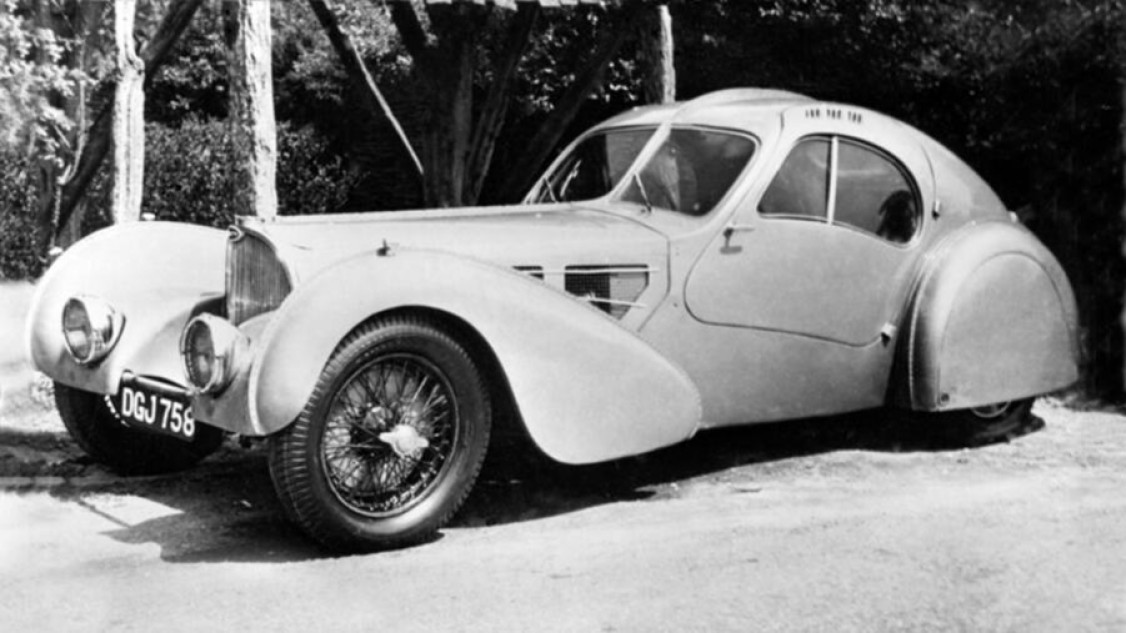
In the high-performance sector, there were also numerous examples of magnesium castings. The DKW Ladepumpen racing motorbike from 1939, for example, had a 350 cc 2-cylinder 2-stroke double-piston engine with a crankcase, cylinder and cylinder head, various covers and wheel hubs made of electron castings. The engine produced 32 hp at 6250 rpm and won the European Championship in 1939. The BMW compressor racing machine with 500 cc from 1939 was also extremely successful. The engine housing, gearbox housing, compressor housing, cylinder head cover, wheel hubs and a number of smaller parts were made of magnesium castings. In road races, the engine produced around 60 hp at 7000 rpm, while in record attempts it delivered 108 hp at 8000 rpm. With this motorbike, Schorsch Meier became the first non-British rider to win the 500 cc race at the Isle of Man in 1939. BMW also used magnesium in motor racing. The BMW 328 ‘Mille Miglia’ from 1940 had magnesium pistons and magnesium brake anchor plates.
The use of magnesium castings was given a major boost by the development of pressure die casting. The good flow properties, lower heat content compared to aluminium cast alloys and the resistance of the mould steel to attack by magnesium played a convincing role here. In addition, the progressive development of pressure die casting machines naturally supported their widespread use. The picture shows a hot chamber pressure die casting machine of the Mahle type and its basic structure. Magnesium die-cast parts for automotive engineering in the years 1934 – 1940, such as the inner structure of the steering wheel, the steering shaft housing, gearbox covers, tappet guides and even water pump wheels, were produced in large quantities. Further die-cast products are listed in the chapter Magnesium in everyday life.
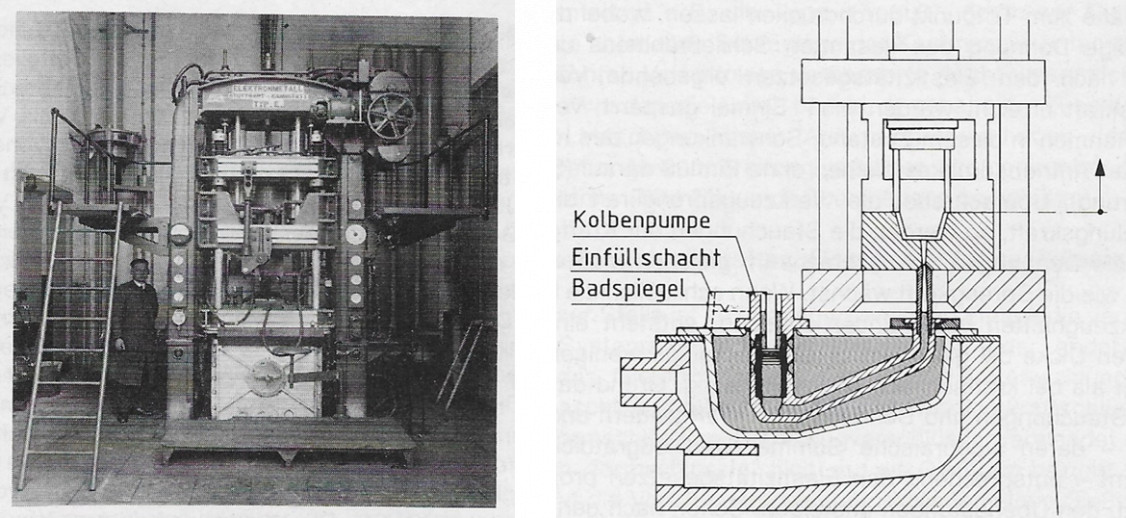
Aviation
The early days of aviation naturally placed high demands on lightweight, high-performance power sources and lightweight, high-strength structural elements. Since there were no suitable aluminium alloys available at the beginning of the 19th century, there were wide fields of application for wrought and cast magnesium alloys. The availability of the material and intensive research and development activities in Germany then led to military aircraft being superior to the Allies at the beginning of the Second World War due to their lower weight with identical engine power.
The first development in the field of aviation came from the ADLER Werke vorm. Heinrich Kleyer A.G. in Frankfurt/Main. In 1909, they presented a 6-cylinder airship engine with 75 hp and a crankcase made of cast magnesium at the International Aviation Exhibition (ILA) in Berlin.
The development of aircraft engines progressed rapidly. The Bayerische Motoren Werke A.G. in Munich, whose logo depicts a stylised rotating propeller, also played a significant role in this. In 1926, they developed a 24.4-litre 6-cylinder in-line engine with 4 valves per cylinder, a continuous cylinder head and cylinder block made of cast aluminium; the crankcase and camshaft housing were also available in electron cast. The engine developed over 320 hp and was not only installed in aircraft but also in tanks on a trial basis. Further examples of the progressive development are engines from the manufacturer Argus Motoren Gesellschaft mbH in Berlin-Reinickendorf. The Argus As 410 (1933) is an air-cooled, overhead (crankshaft at the top) 90° V-8 engine with a crankcase and attachments made of electron castings. With a displacement of 12.7 litres, it had a starting power of 240 hp at 2000 rpm. A total of 28,000 AS 410s were produced. It was used in the Swiss Pilatus P2, among other aircraft. A smaller engine with an Elektron crankcase is the HM 504 4-cylinder inverted air-cooled engine from Hirth Motoren GmbH Stuttgart-Zuffenhausen, which was built in 1934 with a displacement of 4 litres and a starting power of 105 hp at 2350 rpm. It was used in smaller sports aircraft and around 6,000 were built. A highlight of the use of magnesium in aircraft engine construction is the control unit for single-lever control of the BMW 801 14-cylinder double-row radial engine from 1940. The control unit automatically set all engine-relevant parameters such as e.g. ignition timing, throttle opening, injection quantity and propeller position, flight altitude and engine temperature, correlating to the boost pressure or engine speed set by the pilot with the ‘power selector lever’, thus relieving the pilot. The casing was made of cast magnesium with thin (6 mm) pre-cast pressure oil channels in the casing contour, manufactured using smoothed multi-layer spring cores. But magnesium was not only used in engine construction. An excellent example of magnesium sheet and profiles in the structure is the experimental aircraft L 81 ‘Electra’ from Albatros Flugzeugwerke GmbH Berlin Johannistal from 1932. With borrowings from the construction principle of the Zeppelin, the structure was made of magnesium tubes and profiles and, for the most part, perforated magnesium sheet. The wing structure of the L 81 Electra is shown in Figure 39. The elevator and rudder followed the same design principle. The outer skin was a painted fabric covering. Other magnesium components included the engine mount, landing gear, struts, fuel tank and seat frame. The BMW Va engine already mentioned was used. In the following years, many components were mass-produced in Elektron for use in civil aviation, such as wheels and brakes for various aircraft types. Unlike today, the use of materials was also presented in a way that was effective for advertising purposes, as the advertising for magnesium parts for the Focke-Wulf ‘Condor’ by Wintershall ‘Magnewin’ proves. The Focke Wulf Condor shown here was used for regular passenger flights between Berlin and New York.
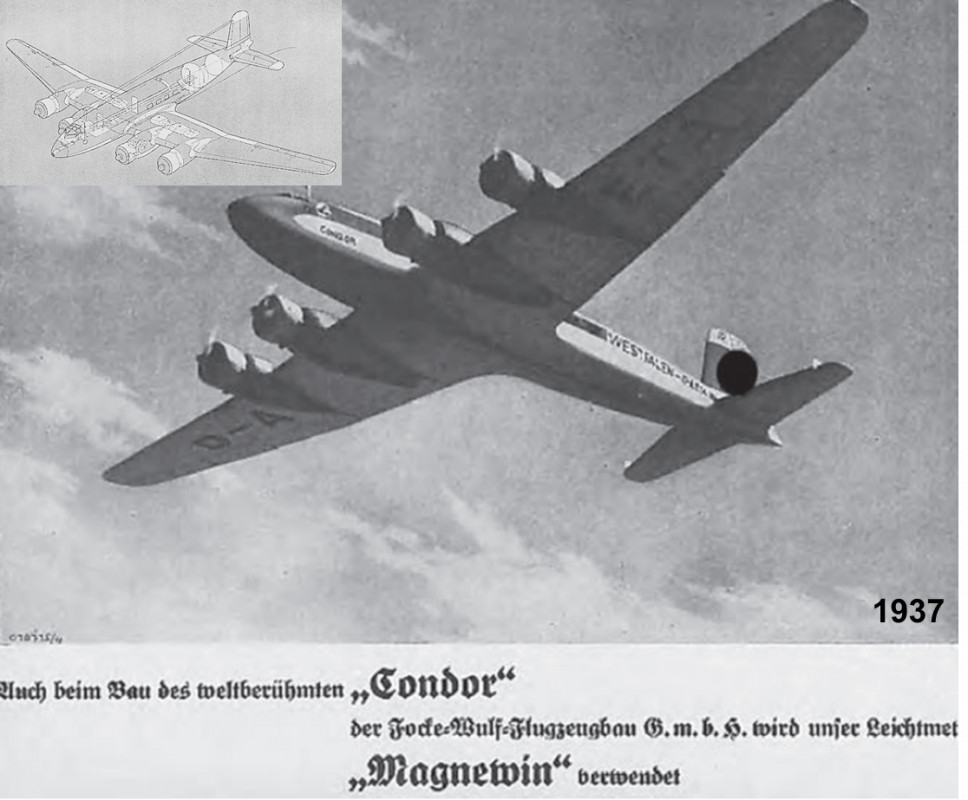
Everyday life
But magnesium parts were not only used in the field of mobility. A large number of cast or moulded electron components were also used in everyday life. Medical technology is one example. The company Electr.-Ges. ‘Sanitas’ in Berlin N 24, Friedrichstr. 131 d manufactured medical apparatus using magnesium casting. The picture shows an X-ray machine with a frame and arms made of cast magnesium. In addition, components for dentist's chairs, dentist's workplaces, adjustable beds and a number of other medical parts were cast. The book cover from England for a loose-leaf collection is also made of magnesium sand casting. In contrast, the low-cost die-cast parts, which were produced in large quantities from the mid-1930s, conquered everyday life. One example of this is the Zeiss field glasses with their magnesium cast structure. Other parts include ticket printers, radio housings, camera housings, rollers and printing plates for ticket printers, electric motor housings for household appliances, typewriter frames.
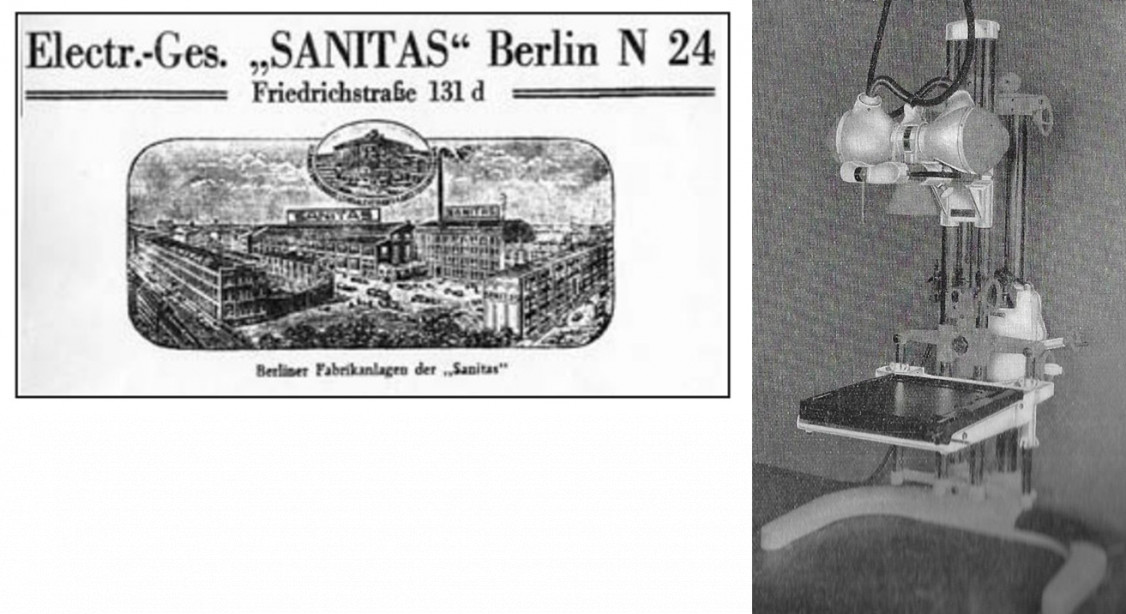
References
[1] SCIENTIFIC-TECHNICAL NEWSLETTERS of the companies EDMUND BECKER & CO. A. G. and METALLGUSSGESELLSCHAFT mbH Leipzig W 35.
[2] ELEKTRON: I. G. FARBENINDUSTRIE AKTIENGESELLSCHAFT ABTEILUNG ELEKTRONMETALL, Bitterfeld
ELEKTRON – NACHRICHTEN: I.G. Farbenindustrie Aktiengesellschaft, Abteilung Elektronmetall, EN 1 – EN 21, 1935 – 1944. This series of publications, which was made available to magnesium customers, contained instructions and advice on the topics of melting and casting, alloys, heat treatment, moulding material and mould production, operating instructions and accident prevention regulations for Elektron foundries
[3] Material MAGNESIUM, based on lectures at the Magnesium conferences in Berlin and Frankfurt am Main in 1938 and 1939, VDI-Verlag GmbH, Berlin NW 7
[4] In autumn 1939, Anton Doppelfeld edited the book ‘DER REICHSVERBAND DER DEUTSCHEN LUFTFAHRT-INDUSTRIE’ and published it by WIKING VERLAG GMBH BERLIN W 35. This volume presents aircraft companies, engine manufacturers and suppliers, many of which were involved in the production of magnesium castings, wrought and rolled products.
[5] Adolf Beck: Magnesium and its alloys, Julius Springer Verlag, Berlin 1939. Adolf Beck was the head of the central laboratory of I.G. Farben A.G. Bitterfeld. His book was the standard work on magnesium, which remained valid for many decades. It covered the chapters on raw materials and production, physical properties, strengths, chemical behaviour, corrosion and surface protection, melting and casting, forming, machining, design guidelines and magnesium as an alloying element in great detail over 520 pages.
Incidentally, a similarly structured book was published in Hungary by Emöd Gyula and Solti Màrton: MAGNÉZIUMÖNTÉSZET, Nehézipari Könyv és Folyóiratkiadó Vállalat, Budapest 1953 (MAGNESIUM CASTING, Book and Journal Publishing Company for Heavy Industry) with reference to Adolf Beck.
In 1943, Walter Bulian and Eberhard Fahrenhorst published the book ‘Metallography of Magnesium and its Technical Alloys’ with Springer Verlag Berlin. Dr W. Bulian was head of the metal laboratory at Wintershall A.G. and Dr E. Fahrenhorst was his assistant.
André Caillon published the book ‘LA FUSION INDUSTRIELLE DU MAGNESIUM ET SES MOULAGES EN SABLE’ in France, which was published by the Publications scientifiques et techniques du Ministère de l'Air N° 130, 1938. The book deals in detail with casting technology, including how to avoid errors.
[6] Joseph Black painted by David Martin 1787, National Galleries of Scotland
[7] Sir Humphry Davy in a painting by Thomas Phillips from 1821
[8] Antoine Bussy von Pierson, photographer, National Library of Medicine
[9] Michael Faraday, oil painting by Thomas Phillips, around 1841/42
[10 ] Robert Wilhelm Bunsen, photogravure by J. B. Obernetter, around 1885
[11] Dirk Hackenholz: Die elektrochemischen Werke in Bitterfeld 1914-1945, LIT Verlag, 2004
[12] Kali und Steinsalz, published by VKS e.V., issue 3 /2013
[13] Museodellatecnica tecneum, SAIM Gesellschaft - Magnesiumwerk, (Societá anonima italiana magnesio, Bolzano
[14] Norsk Hydro: Company history 1929 - 1945
[15] Mahle Innovation - the engine of history, Mahle GmbH, 2014
[16] Bugatti Revue 36, Editor Jaap Horst, Volume 13, Issue 5
[17] Dr.-Ing. Karlheinz Lange, BMW Mobile Tradition: The History of Engines – Engines that Made History
[18] VDI-Zeitschrift 54 (1910) No. 10
[19] www.luftarchiv.de