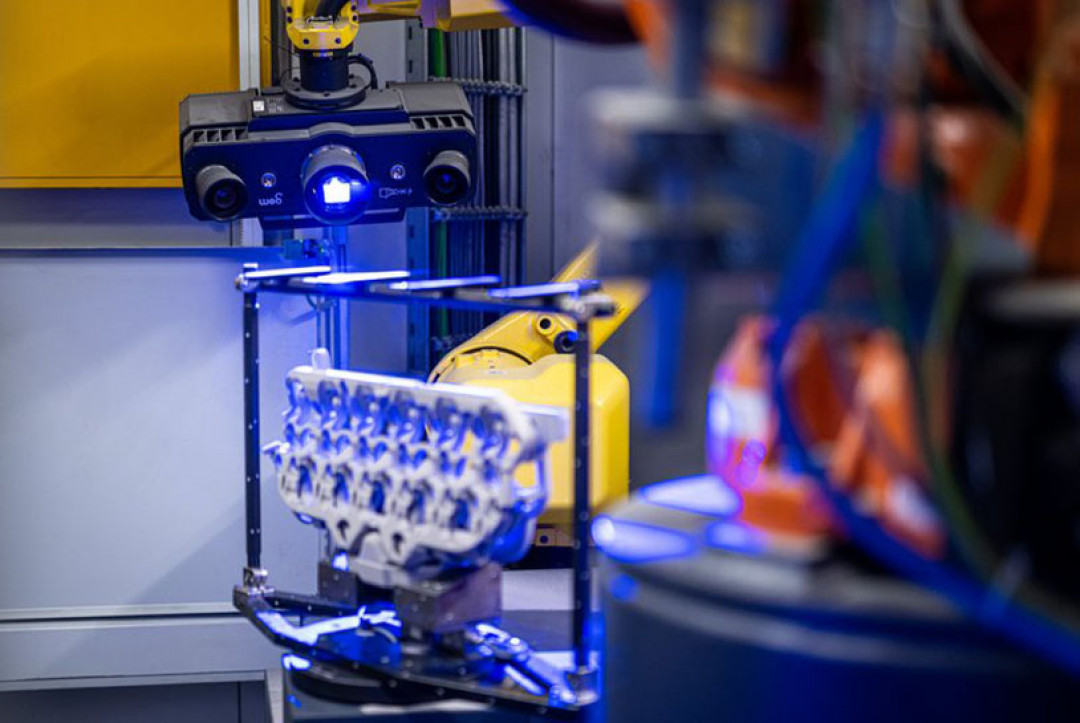
Mit eigens entwickelten Drucklösungen steigt Laempe in den Bereich der additiven Fertigung ein. Sechs 3D-Sand-Drucker inklusive Peripherie hat das Unternehmen nun an die Gießerei der BMW Group in Landshut geliefert.
Mit der erfolgreichen Entwicklung und Abnahme einer vollautomatischen Großserien 3D-Drucklinie für die Herstellung von Sandkernen an die Gießerei der BMW Group in Landshut (Bayern) vervollständigt Laempe sein Produkt- und Serviceportfolio. Die 3D-Drucklinie wurde eng in Zusammenarbeit mit dem Automobilhersteller sowie dem Partner R.Scheuchl GmbH entwickelt. Die BMW Group stellt damit bereits gedruckte Gussformen für Bauteile der neuen Sechszylinder-Generation her.
Laempe startet Verkauf von 3D-Sanddruckern
Die sechs 3D-Drucker, die Laempe nun übergeben hat, sind mit umfangreichen Automatisierungslösungen versehen. Nach Angaben des Unternehmens beinhalten die Anlagen eine 3D-Vermessung und Kernentnahme, wodurch sie ohne manuelle Schritte auskommen. Die Technologie, die von 2016 an bis heute zur Serienreife gebracht wurde, wurde am Laempe-Technologiestandort in Schopfheim (Baden-Württemberg) entwickelt und in Barleben (Sachsen-Anhalt) produziert und richtet sich in erster Linie an Gießereien. Nach der erfolgreichen Übernahme der 3D-Drucklinie durch die BMW Group beginnt ab sofort der Verkauf der Lösungen.
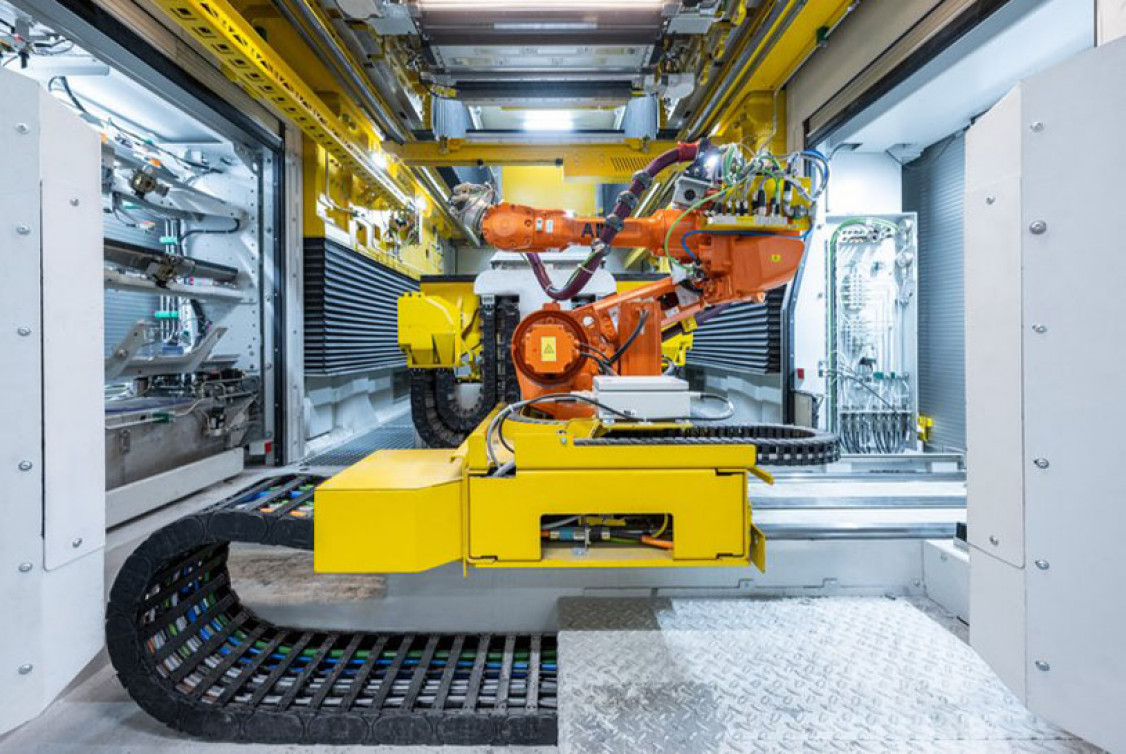
Laempe bezeichnet seine 3D-Drucker mit ihren hohen Bi-Direktionalen Druckgeschwindigkeiten als "die effizientesten Kernsand-Drucker der Welt". Der Aufbau ist gießereitauglich ausgeführt und verwendet etablierte Industriestandards. Zudem wurde bei der Anlage immer die gesamte Wertschöpfungskette berücksichtigt. Dies beginnt bei der Rohstofflagerung und der Formstoffaufbereitung, geht über den eigentlichen Druck bis zum Auspacken, Reinigen und Vermessen der gedruckten Bauteile. Außerdem ist die Laempe 3D-Drucklinie „offen“. Das heißt, Kunden sind nicht an bestimmte Rohstoff-Lieferanten gebunden. Bereits der Einzeldrucker ist zudem so ausgelegt, dass er jederzeit zu einer vollautomatischen Lösung erweitert werden kann. Darüber hinaus hat Laempe mit der „Laempe Printing Wizard Software” ein Tool entwickelt, das Slicing, Skalieren und Morphen von Druckjobs optimieren soll.
In das Entwicklungsprojekt floss Laempe zufolge ein "mittlerer zweistelliger Millionenbetrag". Dieser sei größtenteils aus dem Projekt mit der BMW Group finanziert und "zu einem erheblichen Teil aus dem EIgenkapital von Laempe" gestemmt worden.
Vom klassischen Kernschießen zur additiven Fertigung
Die BMW Group hebt die Leistungsfähigkeit der neuen 3D-Drucklinie hervor. Die Technologie überzeuge durch eine "außerordentlich hohe Druckgeschwindigkeit und das bidirektionale Druckverfahren, das eine effiziente und präzise Fertigung ermöglicht". Dank der umfassenden Automatisierungslösungen sei die Anlage in der Lage, die anspruchsvollen Anforderungen der Großserienproduktion "nahtlos" zu erfüllen.
„Mit unserer innovativen 3D-Drucktechnologie erwarten wir zukünftig, dass sich viele weitere Anwendungen vom klassischen Kernschießen in die additive Fertigung wirtschaftlich überführen lassen. Damit bieten wir unseren Kunden und Partnern einen echten Wettbewerbsvorteil sowie eine zukunftsweisende Lösung, die uns neue Wachstumschancen ermöglichen. Als einziger Anbieter entwickeln und betreiben wir sowohl Kernschießmaschinen als auch 3D-Drucker, wodurch wir die Kostenstrukturen beider Technologien genau kennen”, sagt Andreas Mössner, einer der Geschäftsführer von Laempe.
Hybirde Kernfertigung für Flexibilität
Mit seiner Lösung ermöglicht Laempe die „hybride Kernfertigung“, die Gießereien die Wahl lässt: klassische geschossene Kerne, additiv gedruckte Kerne oder eine Kombination aus beidem. Darüber hinaus bietet Laempe das flexible „pay per part“-Modell über das Joint-Venture INACORE (Partner: R.Scheuchl GmbH). Das Unternehmen in Ergoldsbach (Bayern) verfügt bereits seit mehreren Jahren über eine Reihe von Kernschießmaschinen sowie einen Laempe-Drucker und beliefert seine Kunden mit gedruckten beziehungsweise geschossenen Kernen.
Beitragsbild: Laempe Mössner Sinto/Team Timo Lutz Industriefotografie