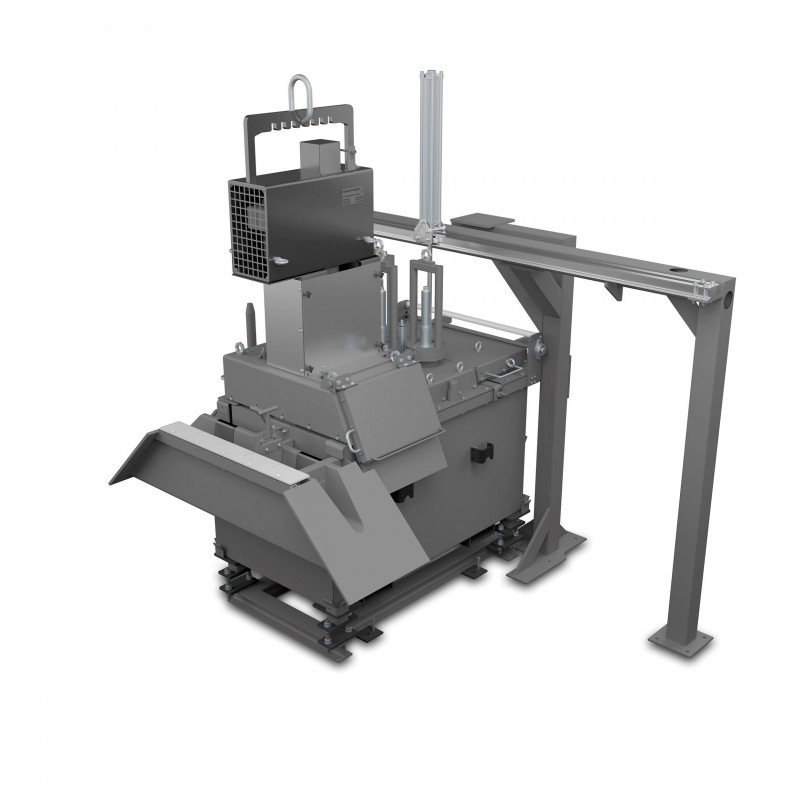
At this year's ALUMINIUM Exhibition in Düsseldorf, the German company Drache is presenting a world first for use in continuous and mould casting: the first filter box to combine degassing, temperature management and filtration of liquid aluminium in a single compact system unit. It enables extensive process optimisation, particularly in applications where plants operate at low casting speeds and where long casting times of several days or weeks are the norm. The Drache Filter-Kombibox is provided as a complete solution with gas dosing and control.
This is the world's first all-in-one solution for treating liquid aluminium that combines degassing, temperature control and filtration in a single compact unit. Designed according to the two-chamber principle and supplied as a complete system with gas dosing and an electrical cabinet including control system, it opens up a wide range of possibilities for modernising processes in the continuous and mould casting of aluminium. ‘Particularly in plants with low casting speeds and in applications that require longer casting times without interruptions, our new filter combi box can make a decisive contribution to simplifying processes, ensuring quality and increasing efficiency,’ says Kai Maldaner, Commercial Director at Drache. Typical examples include wire or strip casting plants and mould casting applications, where it is essential that the casting station is continuously supplied with liquid aluminium.
Drache has designed the new filter combi box as a space-saving system in which the liquid aluminium flows through two chambers. While the highly efficient degassing (and cleaning) of the melt is carried out by a purging unit with a graphite rotor, adjustable immersion heaters ensure that the metal always maintains the desired temperature for the process. Finally, a vertically positioned ceramic foam filter from Drache's Ceralu® line takes over the filtration and also calms the metal flow of the cleaned aluminium as it exits the filter combi box. In terms of efficiency, the new filter combi box sets standards. The results are above average in both particle reduction and hydrogen reduction.
The latest findings in process engineering and user requirements have been incorporated into the development of the new filter combi box from Drache. All system components are of high quality and take into account the increasing quality requirements in aluminium casting. For degassing, for example, a graphite rotor is used that has high chemical stability and excellent corrosion resistance. In addition, it has excellent non-wettability with liquid aluminium.
Three powerful, adjustable immersion heaters with a power of 12 kW are at the heart of the temperature control system. A partition wall made of silicon carbide (SiC) ensures efficient temperature equalisation between the process chambers. The complete inner lining of the steel housing, on the other hand, consists of Drache Fused Silica (DFS), a high-temperature material developed by the Diez-based company specifically for use in aluminium casting. It is considered the premium solution for fireproof components and linings, is characterised by excellent thermal shock resistance, very good non-wettability and high chemical resistance. In addition, the material has very good strength at a relatively low thermal conductivity.
‘At ALUMINIUM, we will show that our new filter combi-box not only offers a high degree of process reliability, but also considerably simplifies all maintenance and servicing work,’ emphasises Kai Maldaner. A specific example of this ease of operation and service is that not only – as mentioned – the graphite rotor can be changed during operation, but also the ceramic foam filters. And aside from the numerous lids and flaps, it is possible to remove all units individually with or without the cover from the combi box. Drache also offers the option of equipping its new combi box with a filter lifting system or a customer-specific temperature control unit.