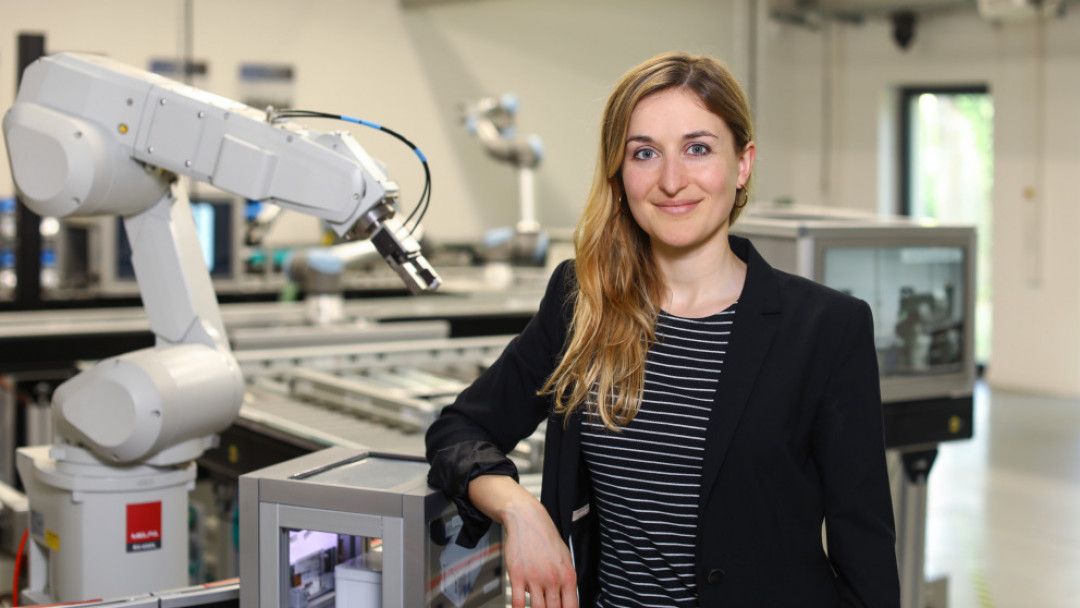
To what extent is it true that digitalisation in "Industry 4.0" improves energy efficiency and thus reduces energy intensity in industry? A team from the Research Institute for Sustainability (RIFS) analysed ten sectors of industrial production in China between 2006 and 2019 to find out. The conclusion of the study: contrary to what politicians and industry postulate, digitalisation in China does not appear to automatically unleash energy-saving potential in the manufacturing industry.
China accounts for 30 per cent of global value creation in the manufacturing industry, making it the country with the largest share of global industrial production. Industry 4.0 - the comprehensive digitalisation of industrial production - is now expected to help boost economic growth and achieve energy-saving targets at the same time. However, there is disagreement in the scientific community as to whether Industry 4.0 can unite these two goals. A study by the Research Institute for Sustainability (RIFS) analysed ten Chinese manufacturing sectors between 2006 and 2019 for correlations between Industry 4.0 and energy indicators. Although several studies have already analysed the impact of digital technologies on energy consumption, few of them have done so in the Chinese context.
"In addition, the concept of Industry 4.0 has hardly been recognised in previous studies," says lead author Stefanie Kunkel. "For example, the concept of Industry 4.0 has been greatly simplified in some studies - for example, robots have been equated with the use of artificial intelligence. The knowledge and innovation dimension of this technology has been ignored." Previous studies have also rarely analysed overall energy consumption and have mostly focused on relative energy consumption or energy efficiency. This could lead to the goal of an absolute reduction in energy consumption being lost sight of, although this is important for the decarbonisation of the industrial sector.
Is there a significant correlation between Industry 4.0 and energy consumption?
The main aim of the study is to understand the extent to which the degree of use of Industry 4.0 is related to the overall energy consumption and energy intensity of the manufacturing sector in China - and whether the thesis that Industry 4.0 contributes to efficiency and therefore energy savings can be supported by statistical analyses.
The term energy intensity or relative energy consumption describes how much energy a sector consumes per euro of manufactured goods. To answer the research question, Kunkel's team carried out a panel data analysis that included data from ten industrial sectors over a period of 14 years (2006 to 2019). These sectors included the textile industry, plastics production and the food industry, among others.
Digital rebound and growth versus efficiency effects
As far as total energy consumption in the manufacturing industry in China is concerned, the results showed that there is no significant correlation between the degree of Industry 4.0 and energy consumption. "The relationship is positive, but not significant," says Kunkel, explaining her study. For example, the use of robots instead of manual labour in textile production, which is currently less digitalised, could increase energy consumption in textile production. So-called "digital rebound effects" often occur when the efficiency gains achieved through digitalisation lead to cost savings. The resources saved could be fully or partially reinvested and compensate for some or all of the efficiency gains. In addition, digitalisation generally has a growth-promoting effect, which generally also increases energy consumption.
However, there are other studies that contradict the results of Kunkel et al. because they found that robots and industrial digitalisation have the effect of reducing the energy intensity of industry - i.e. an efficiency-enhancing effect. However, Kunkel's team was only able to prove a negative correlation between Industry 4.0 and energy intensity for sectors that are already highly digitalised. One explanation for this could be that in a sector that is already heavily characterised by the use of digital technologies, such as the transport sector, Industry 4.0 innovations can be better integrated into the manufacturing system and efficiency potentials become more apparent.
As a limitation, the authors point out that previous studies have not taken into account digitalisation-related offshoring and that reductions in energy intensity may have been incorrectly attributed to digitalisation itself. In order to partially capture such effects, Kunkel et al. included the "CO2 imports" indicator as a proxy for the energy intensity of imported goods. They found significant positive correlations between CO2 imports and the extent of Industry 4.0, which could indicate that increasing CO2 imports into manufacturing are associated with an increasing degree of Industry 4.0. However, further research is needed to understand the underlying dynamics.
Conclusion
One conclusion of the RIFS study is that a focus on the mantra of "increasing energy efficiency through digitalisation" may be ineffective for sustainability goals and the decarbonisation of industry if this leads to an overall increase in total energy consumption due to growth and offshoring dynamics. Other factors should be considered, such as impacts on industrial relocation, sector-specific impacts of different digital technologies, human capabilities to implement innovations and steer them towards sustainability, as well as the simultaneous integration of renewable energy in industrial manufacturing. In addition to energy variables, the RIFS team also recommends including other sustainability indicators such as resource consumption and e-waste caused by digital technologies in the sustainability assessment of Industry 4.0 in future.
Study results also relevant for other countries
Industrial manufacturing will account for 37 per cent of global energy consumption in 2022. China is the largest contributor to this increase in consumption. A reduction in energy demand and the environmentally friendly organisation of industrial production in China is therefore of great importance for climate protection worldwide. Against this backdrop, analysing the connection between energy and Industry 4.0 is highly relevant for industry representatives and political decision-makers beyond China. This is because the European Union and countries in other regions of the world also hope to be able to address the goals of sustainable development through digitalisation. However, this will not succeed automatically, but must be managed.
Conclusion and recommendations
Firstly, through international cooperation and agreements such as supply chain agreements, innovations in the field of Industry 4.0 in the manufacturing industry should be geared towards reducing energy and resource requirements along the entire value chain. This can prevent Industry 4.0 from leading to an increased relocation of energy-intensive manufacturing processes to countries with lower environmental standards. Secondly, the mechanisms by which certain technologies influence energy consumption in industry should be better understood through increased research involving practitioners. This will make it possible to decide which innovations in the field of Industry 4.0 contribute to reducing the absolute global environmental impact and how this can be promoted by both politics and industry. Thirdly, a consistent orientation of Industry 4.0 towards sustainability goals can help to direct the growth-promoting effect of Industry 4.0 towards goals such as decarbonisation and the promotion of the circular economy.
Publication: S. Kunkel, P. Neuhäusler, M. Matthess and M.F. Dachrodt: Industry 4.0 and energy in manufacturing sectors in China. Renewable and Sustainable Energy Reviews, Volume 188, 2023.