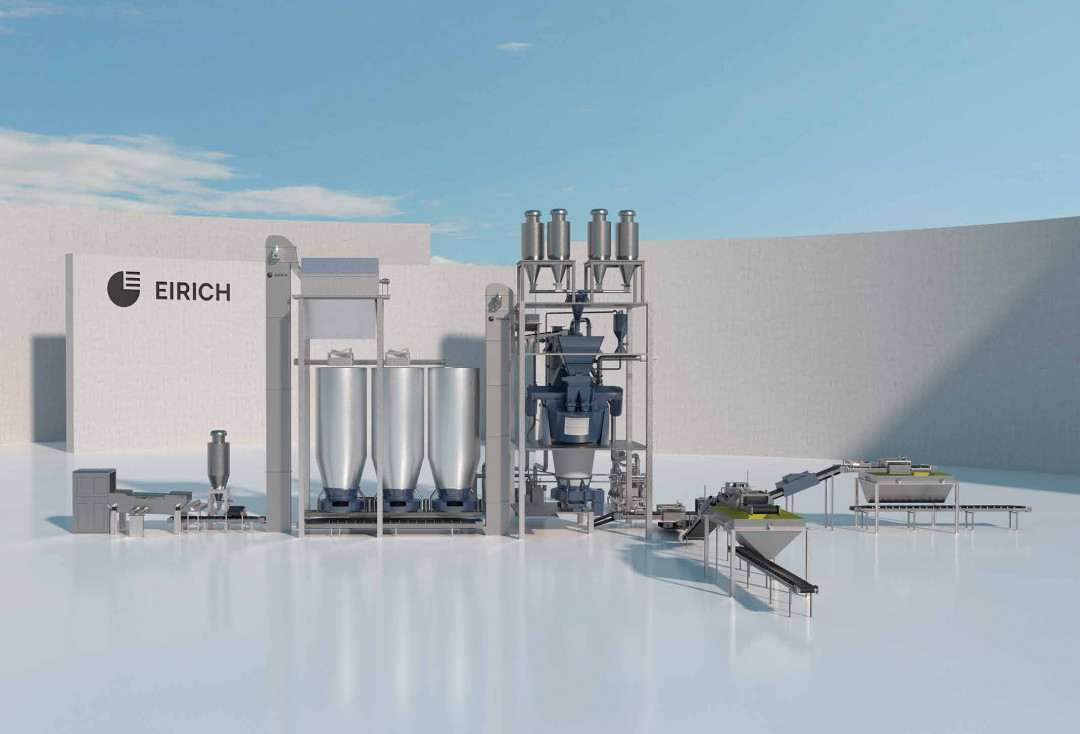
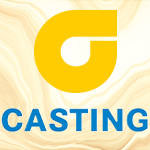
Skills shortages in the industry, rising energy costs, and shortages of raw materials are all presenting the foundry industry with major challenges. As a result, this energy-intensive industry is being forced to carefully scrutinize its processes in order to remain competitive. The key to success: innovative drive technologies, self-optimizing systems, and intelligent sand management.
By Marie-Luise Liepe
The foundry industry plays a major role as a supplier of products in a wide range of fields – including the automotive industry, machine construction, and other industries. But it also faces a large number of challenges. A shortage of qualified specialists, high current energy prices, and the global scarcity of raw materials are all piling the pressure on the foundry industry. Traditional companies now face the challenging task of critically analyzing their processes – after all, this industry is one of the most energy-intensive of all. On average, an energy demand of 2000 kWh per t of good casting is to be expected. Based on this number, the foundry industry in Germany uses a total of 11 billion kWh of energy every year.
And, every year, the foundry industry also consumes over 100 million tons of sand. Although this natural resource is the foundation upon which optimum casting results depend, the importance of the quality of the molding material and smart use of the raw material in production has often been overlooked in the past. And yet, focus is generally shifting toward technologies and processes that are more frugal in their use of resources, and there is a strong development toward sustainability and protecting the environment.
Forward-looking technology for mixers for the preparation of molding materials
High-productivity molding lines need to be supplied with molding sand in a way that allows system availability to be maximized. The goal is always to keep operations as reliable as possible under fluctuating boundary conditions. Here, the quality of the molding material plays a pivotal role. Even under very varying loads, it should always be consistent and reproducible, and in particular it must be cooled back down homogeneously to < 42 °C. Emissions must be reduced while increasing the environmental compatibility of the line at the same time (fig. 2). In foundry engineering, the Evactherm method developed by Eirich, which takes advantage of thermodynamic effects, has been used since the early nineties to ensure precise recooling and optimal preparation of bentonite bonded molding sand.
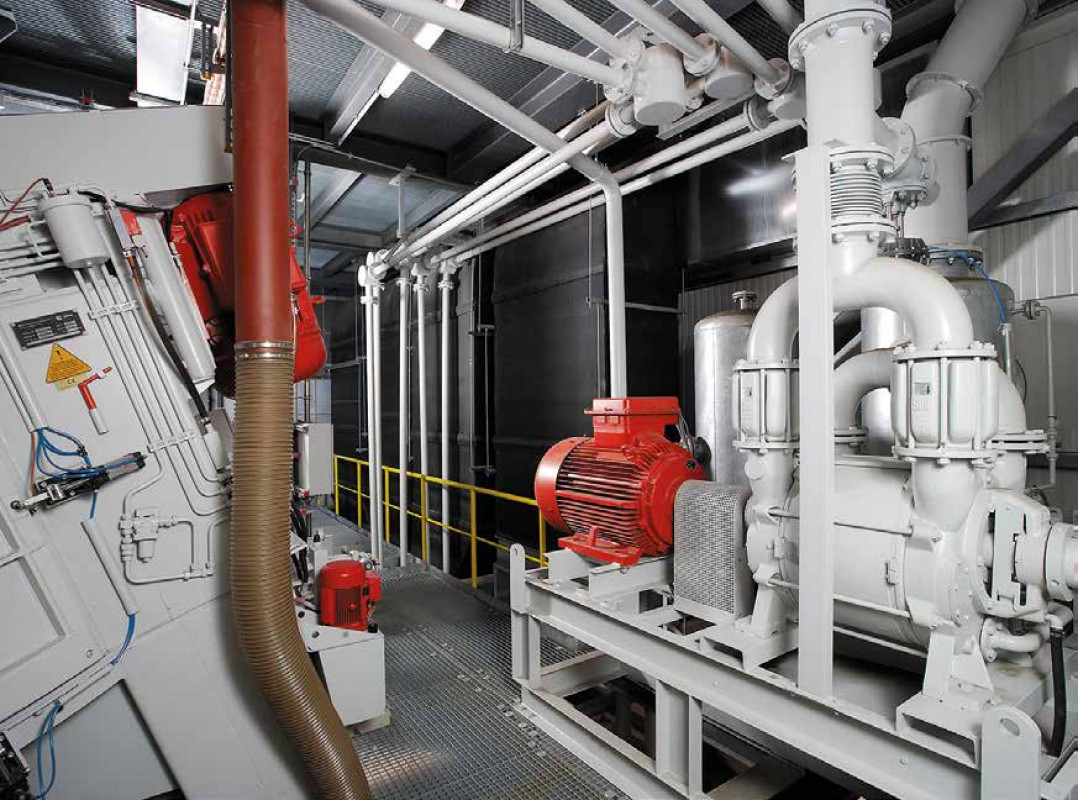
This technology has now established itself, and over 70 mixers are running at different plants around the world. The closed system combines cooling and mixing in just one unit (fig. 1).
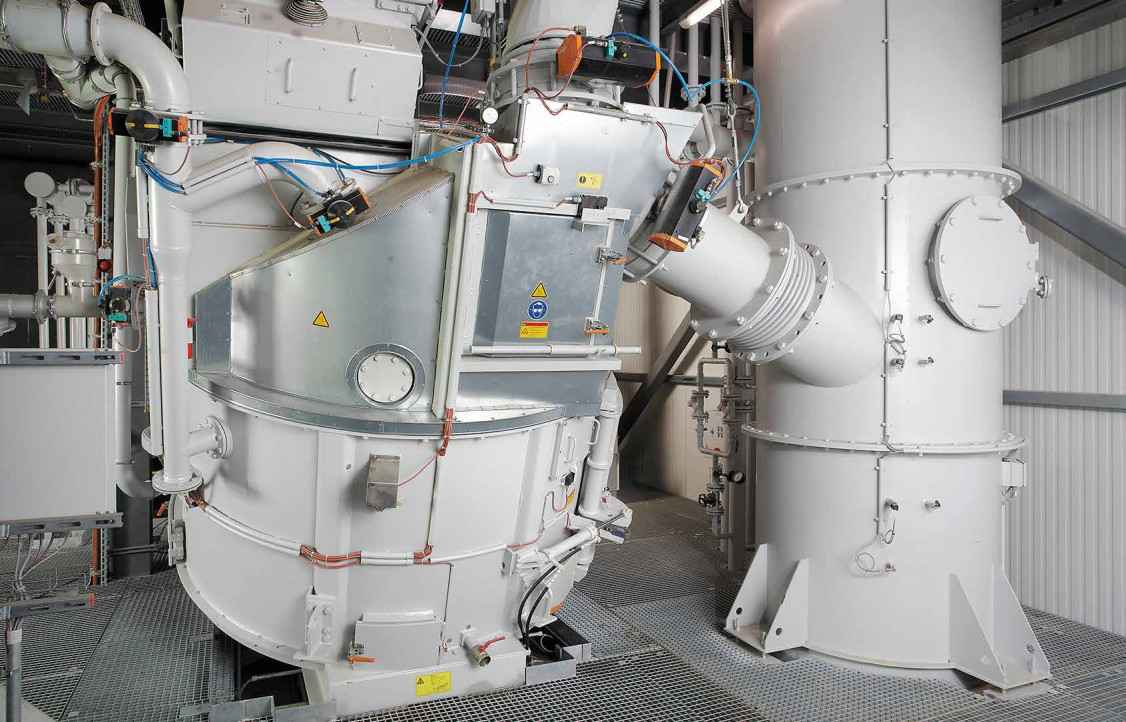
As a result, the fines remain in the system and do not need to be filtered, transported away, or placed in landfills in what would otherwise be a laborious and complicated process. No vapors remain in the pipe system, which ensures that the system does not drop below the dew point. The necessary cleaning work in the dust extraction pipes is also reduced to a minimum. The most striking characteristic of the Evactherm technology is the ability to design dust extraction systems to be significantly smaller and more efficient. This aspect alone enables foundries to drastically reduce their emissions and significantly reduce the number of trips to the landfill site. The reduced energy consumption also benefits the foundry industry in times dominated by an energy crisis and high demands in the energy industry.
This challenge can also be solved with another technology: Thanks to their high torque output, state-of-theart torque motors are perfectly suited as direct drives for the mixing tool. They optimally transmit the force to the tool. In the process, it does not matter whether this is for a conventional Eirich intensive mixer or an Evactherm mixer. Due to the high torque, the torque motor can replace the asynchronous drive and transmission (gears or belt). The result is an even and powerful torque. The motor offers maximum efficiency and maintains its rotational speed in all operating phases – no matter whether the load is 10 or 100 percent. This is in stark contrast to asynchronous drives, where it is possible that the belt can slip at higher torques. This in turn leads to downtimes and repairs, which cost the company time and money in particular.
Thanks to the integrated torque drive in the mixing tool, foundries will benefit from reduced maintenance requirements, lower noise levels, reduced vibrations, and noticeably lower energy consumption. In order to directly illustrate the advantages of a torque motor as the rotor drive in comparison to an asynchronous motor using a V-belt as the drive, we compared two otherwise identical mixers that were running the same process with the same machine filling. The measurements in the field show that the setup with the torque drive consumes up to 25 % less energy. For foundries, this means huge savings in terms of energy and therefore cost.
Proactive management of the sand cycle
Many companies see digitalization as an important step for future successes and are attempting to optimize their processes in order to strengthen their own market position. For the family-run company Eirich, optimization of production processes and intelligent networking of equipment and systems is a step toward improved efficiency and sustainability. This creates flexible production structures that are extremely valuable in such a dynamic market. With its digital product portfolio, Eirich has also taken the issue of closeness to the customer to a new level. From rapid procurement of replacement parts to technical support provided by experts from Eirich, the company is aiming to offer its customers even better service and direct accessibility through digital offerings.
The family company sees the digital transformation as a natural further development of the industry. It is important to face up to these challenges – in times of skills shortages, how can a preparation plant always operate optimally as a system without needing to draw on the experience of seasoned experts? The necessary knowledge needs to be implemented by the machine supplier in the system. At the same time, this is also a great opportunity to take oneself and one’s customers to the next level. With digital service solutions and innovative process analysis software, added value is generated in order to reliably improve production processes in the long term.
The ever increasing requirements in terms of quality, reliability, and savings potential also require system control with systematic quality assurance. This is why, in addition to product quality, for many companies high manufacturing efficiency is an increasingly important factor in order to successfully strengthen their competitiveness on an international scale. This is where digital technologies and automation come into play. Sand management is a vital aspect for the industry, and it is embodied in the Eirich control concept with comprehensive data integration. This system ensures networking of parameters relating to production and to the control systems at all levels. Information relating to the process, product, and quality is available online, where it can be accessed from any location. The scope of the control system also includes the inline tester QualiMaster AT1 (fig. 3). This unit supplies measurements of compactability and shear strength for each batch in just 40 seconds. The software “SandReport” records and analyzes the entire molding material preparation process and receives all relevant batch data from the molding material system – the moisture correction system AC1 and the inline tester AT1. The digital tool includes full production analysis and ensures the quality of the molding material through traceability. Via the graphical representation, the customer always has a clear overview of the recorded values.
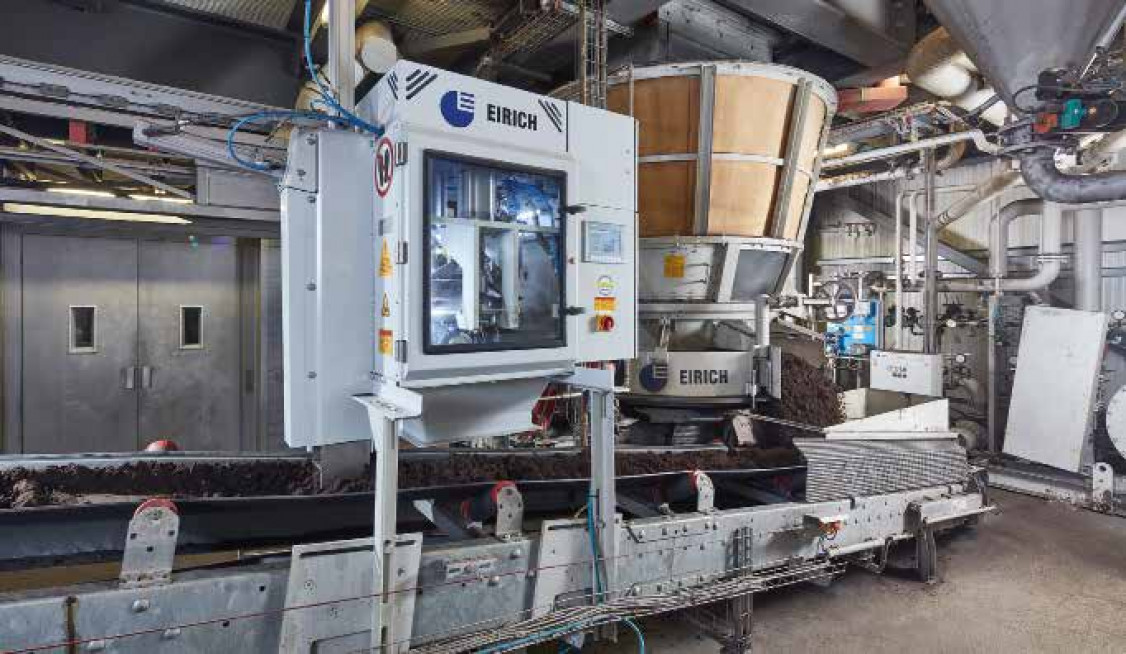
Intelligent sand management is implemented via the software “SandExpert” with predictive calculations of new sand and additives via the daily mold order analysis. If the mold is changed, the composition of the molding material is automatically calculated by the software. This is done using the values from the database of molds so that the return sand quality remains identical regardless of the castings produced. As a result, the right molding material for the relevant production requirements is always available at the molding line. The return sand is refreshed with the same amount of bentonite, new sand, and additives that it will lose during the subsequent casting process. This saves resources and time, putting an effective raw materials management system in the hands of the caster – with maximum flexibility in production planning and stable processes, as well as reproducible results. In addition to measurements of compactability and shear strength, QualiMaster AT1 also includes the option to measure other important process parameters like gas permeability, springback, and deformability.
Current outlook in the industry
The skills shortage is accelerating the drive to digitalization in the foundry industry. Just as in so many other areas, the lack of experts is the limiting factor for production capacities in companies. In order to counter this, innovative technologies that support near-automated production will need to be deployed. With the route of digitalization, forward-looking foundries are also creating the basis for high-tech production facilities and underlining the pioneering role of the industry.
The target of climate neutrality by 2050 also presents the foundry industry with major changes. For casters, maximum energy efficiency, major reductions in emissions levels, and effective processes are therefore the most important levers for the path into the future. Maschinenfabrik Gustav Eirich has been a dependable partner to the industry for many years and has understood this need. Over many decades of working with foundries across the entire globe, a profound understanding of the importance of the molding material in foundries has evolved, and this has allowed the company to offer tailor-made plant engineering and control systems for molding sand preparation.
In the future, there is also potential for applications to be widened in the mobility sector and in the area of machine construction. The energy and mobility transition is presenting many manufacturers with new challenges – but the foundry industry can already offer suitable solutions for these challenges today. Companies that face up to these challenges in good time and are able to meet these new casting demands will have a great opportunity for future growth and will secure themselves a competitive advantage at an international level.