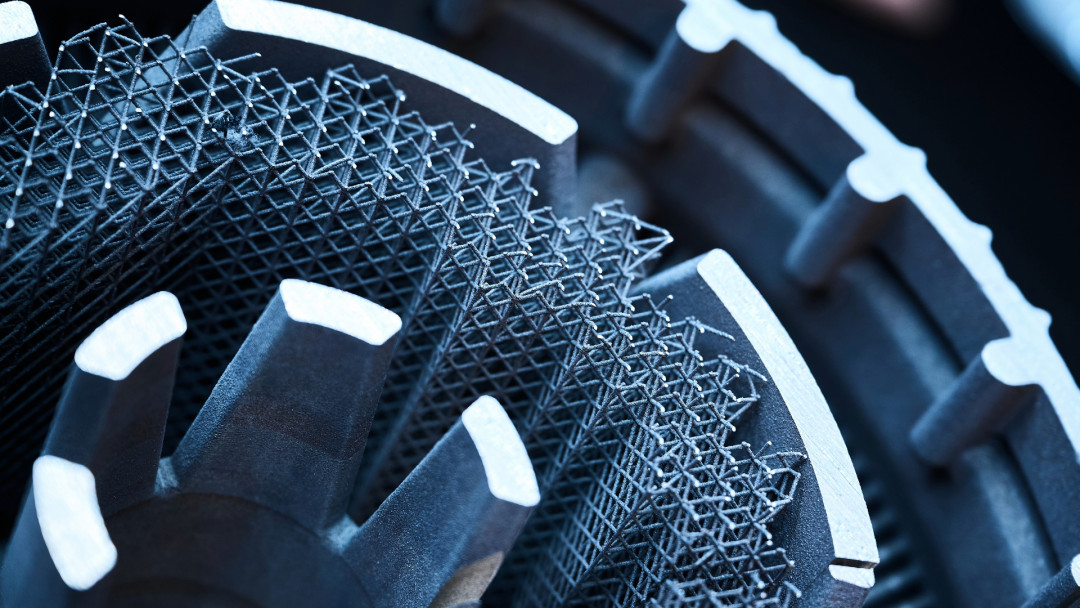
Additive manufacturing technologies enable an almost unlimited variety of products with increasingly sophisticated materials and "imprinted" functions. In the metal sector, laser powder bed fusion (LPBF) offers enormous freedom in terms of material selection, geometry and integrable functions. The current focus of research at the Fraunhofer IWU is on revolutionary printing strategies for delicate structures such as high-quality medical implants and for particularly thin-walled, highly efficient heat exchanger structures that utilise valuable heat. Printed aluminium wheel carriers can be both highly resilient and economical to produce.
Filigree lattice structures with integrated function; première for new exposure strategies that enable particularly high-quality implants
LPBF can be used to implement functionalities in sophisticated products and manufacture them highly economically in small and medium quantities - without any complex supply or process chains. The functional integration can be realised through the integrated sensors or actuators or through the processing of so-called functional materials. This results in a fascinating variety of applications and products with high utility value. The researchers at Fraunhofer IWU are focussing on the needs of medical technology, among others. One such research focus is implants with filigree lattice structures such as stents, which keep constricted blood vessels open, particularly in the heart or brain. For the gentlest possible insertion, it makes sense to utilise so-called superelastic shape memory alloys (SMA), which only take on their full expansion once they have reached the constriction in the bloodstream. During transport to the constriction site via the catheter, the stent is elastically strongly "folded", the catheter can be correspondingly thin, whereby the intervention remains particularly gentle (minimally invasive). When the catheter is withdrawn, the stent returns to its original shape. On the one hand, the lattice structure of the stent enables the compact transport shape and, on the other hand, permanently stabilises the construction of wires that are only 100 - 200 micrometres (0.1 - 0.2 millimetres) thin. The production of the stents using the LPBF method avoids a lot of waste: the spaces between the grids are not printed; in the case of a cylinder produced by forming, these must then be cut out using a precision laser. The printing process also allows the production of several, even different stents in the same batch. For example, stents used for brain aneurysms (strokes) can be printed specifically for each patient. As pathological protrusions in the vessels are individualised, such custom-made products can help to reduce the risk during surgery and improve the chances of recovery.
In cooperation with the Chair of Virtual Product Development at Dresden University of Technology, the researchers are working on new exposure strategies that further improve the quality of printed stents. In the LPBF process, metal powder is applied in many layers, with the laser melting the material at precisely the points where the component is to be formed. The way the laser passes over the powder material is determined by the exposure strategy. In the case of the stents, the aim is to print rods that describe a circle or an ellipse in cross-section, depending on their orientation. If the laser is perfectly parameterised in terms of speed, power and focus diameter to the optimised laser paths, much more precise results are achieved, especially with filigree components: the energy input is homogeneous in every layer and in every section, and hardly any adhesions are formed. In addition, productivity increases many times over, as the laser requires much shorter distances.
Heat exchangers: maximum efficiency with thin-walled, multi-curved structures
Heat exchangers are required for the targeted transfer of thermal energy from one medium to another. As the number of possible applications is vast, these components must be precisely matched to their purpose and location in terms of heat transfer capacity, pressure retention and geometry. This is the only way to optimise their performance for the respective application - the efficiency of the selected heat exchanger solution often has a significant influence on the energy balance of the overall system. Additive manufacturing processes are virtually predestined for the production of application-optimised, highly efficient heat exchangers. The thinnest possible walls and large, multi-curved surfaces for heat transfer enable decisive improvements in efficiency. Metallic 3D printing using the LPBF process utilises the design freedom inherent in the principle for the fast and resource-efficient production of such wall structures. The performance characteristics in fluid-based applications, such as high-temperature heat exchangers and two-phase vapour chambers, benefit in particular from these structures, which can be easily realised using 3D printing. High-temperature applications often require highly resistant materials that can be processed economically, primarily using the LPBF process. This project is funded by the European Union under grant agreement no. 101102316.
Printed aluminium wheel carriers: highly resilient, economically producible
As part of the Campus FreeCity project to research a networked fleet of modular robot vehicles, the EDAG CityBot, a multifunctional robot vehicle consisting of a tractor and variable additional modules, is being created. After a test phase, it will be used in particular for passenger transport or cleaning tasks. Together with Fraunhofer IWU and Constellium, EDAG developed a process chain for the CityBot for rapid component development and determination of suitable manufacturing processes and materials by means of automated engineering. A concrete example is the wheel carrier component that connects the wheel to the chassis and steering motors. Different transport tasks and corresponding loads require a customised component design; LPBF in combination with the aluminium alloy Constellium Aheadd CP1 proved to be economically and technologically advantageous: in terms of processability, production speed and mechanical properties of the product. Fraunhofer IWU developed the LPBF process parameters for a standard industrial printer. The practical test of the CityBot will start shortly in the Deutsche Bank Park in Frankfurt am Main. The funding body for Campus FreeCity is the Federal Ministry for Digital Affairs and Transport.