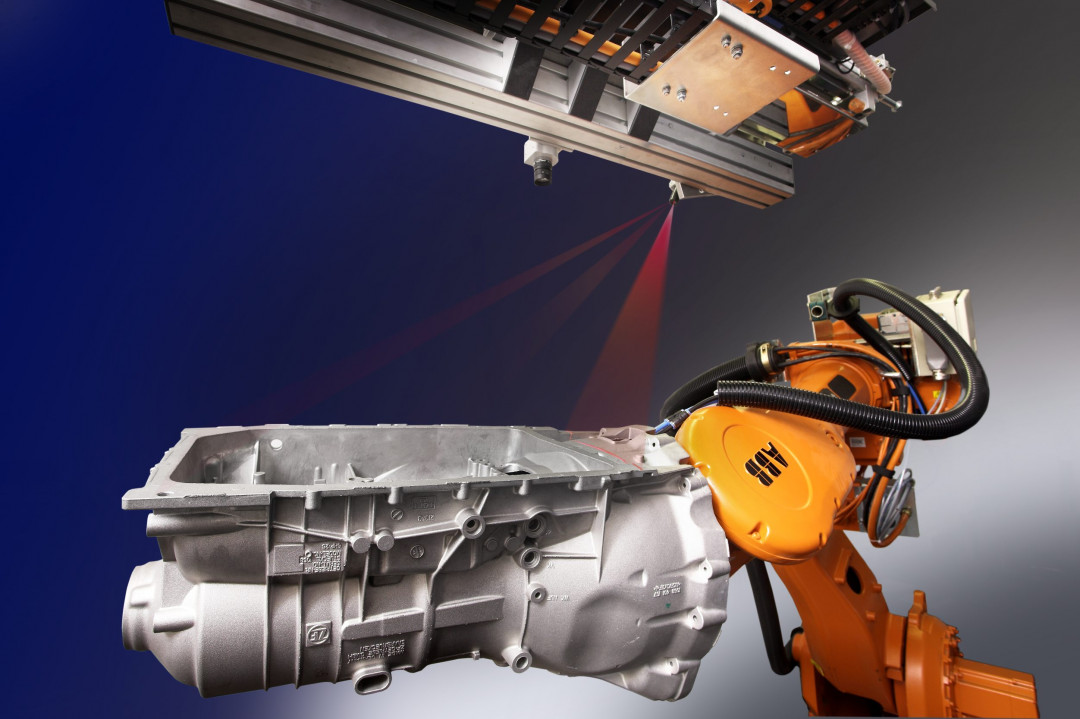
In 2018, Laempe acquired and integrated inspectomation, a company that specializes in automated image processing. With the help of its self-developed core products Core-Vision, Disc-Inspector and Flexinspector, defects, damage and other faults on sand cores and castings can be detected automatically using camera technology.
This reduces or completely eliminates the need for manual inspection during production. The products and solutions in the field of image processing can be perfectly integrated into the automation solutions of Laempe Mössner Sinto – this is exactly what the leading company in core production technology will be demonstrating at GIFA. The solutions in image processing develop their full effect when they are integrated holistically into the overall process. For this reason, customers, which primarily include foundries, not only receive a pure image processing solution, but a holistic complete solution from a single source. This includes image processing, mechanics, programming, commissioning and service. In addition to the complete solutions for traditional foundries, inline monitoring and core measurement for 3D printing processes are currently in preparation.
Core-Vision is an image-based camera system for the automatic detection of defects on sand cores as well as sand molds and is used for the fully automatic detection of break-offs, gaping cracks, missing cores and other visible larger defects (> 2 x 2 x 2 mm). In contrast to traditional methods, which often only work with a single image under diffuse illumination, the Core-Vision system takes a series of images with differently directed illumination. The resulting series of images provides comprehensive 3D information about the shape of the object being inspected.
The Disc-Inspector system is primarily aimed at manufacturers of brake discs. The product uses a mixture of 2- and 3-dimensional imaging processes to inspect the ventilation channels and all visible surfaces of a brake disc for casting defects or damage. Holes, break-offs, burrs in channels as well as full and partial occlusions in channels can thus be detected automatically. With the Disc-Inspector system, 100 percent of the brake discs produced can be inspected in a cycle-retaining manner. The changeover effort is minimal and all available types can be inspected. The Disc-Inspector solution is a future-oriented modular system including a system configurator. This means that customers can adapt the system to their individual needs, depending on what is to be inspected on the brake disc. The Disc-Inspector is currently used by many well-known manufacturers of brake discs and in foundries worldwide.
The Flexinspector system can check all visible surfaces of a casting for casting defects or damage using a 3-dimensional imaging process. If the system is calibrated accordingly, the dimensional accuracy of parts can also be verified. The inspection is carried out in a tactile manner and covers any number of part types. Customers, especially foundries, can create, update and adjust inspection programs themselves. The Flexinspector system – like the Disc-Inspector and the Core-Vision – is delivered and commissioned as a turnkey system. The Flexinspector is 100 per cent cycle-retaining, reduces waste, increases efficiency and can be used flexibly. Since, strictly speaking, it is a similarly designed system to the Disc-Inspector, the Flexinspector combines the same advantages. It is used, among other things, to inspect gearbox housings and cylinder heads at world market leaders.