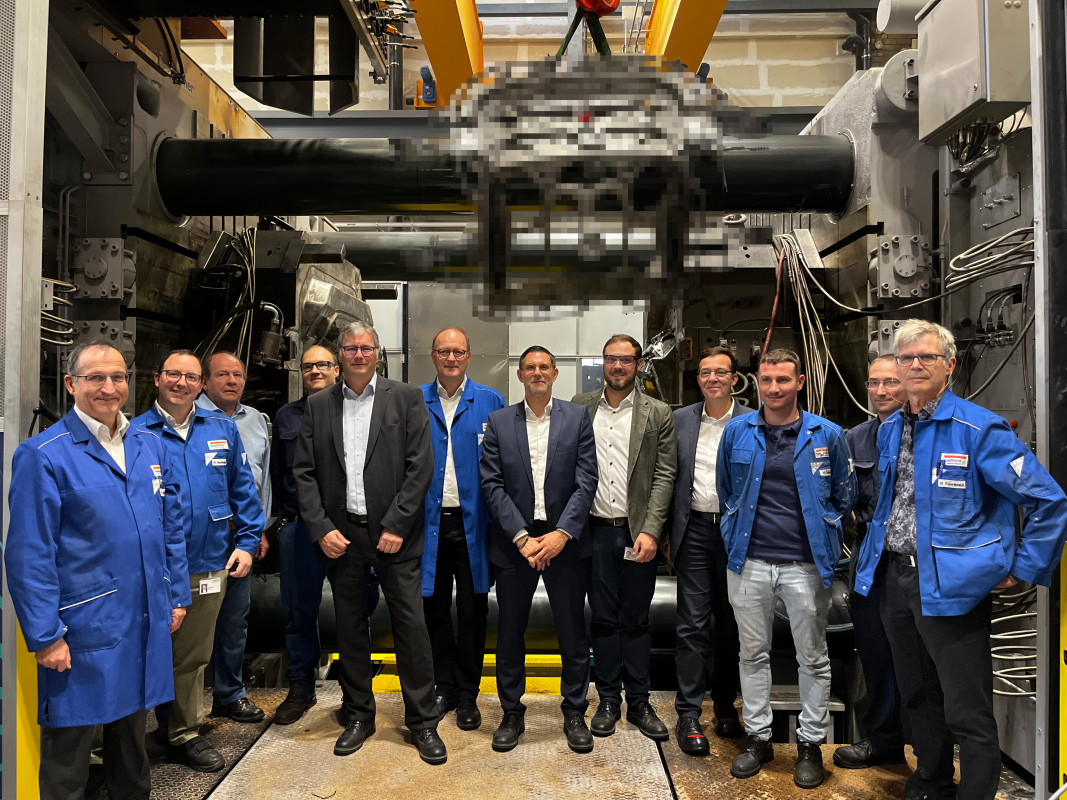
Two years ago, the starting signal was given for the innovative die casting process, in which Handtmann has invested millions. About a year and a half after the groundbreaking ceremony, a series part was cast for the first time on the new megacasting machine on 25 October 2024.
Handtmann, headquartered in Biberach an der Riss, is the largest family-run light metal foundry in Europe, with five production sites worldwide in Germany, Slovakia and China.
Megacasting typically refers to the casting of very large metal parts that require special casting techniques and machines. Megacasting is already an up-and-coming technology internationally, particularly in China and the USA. The pressure die casting process has the potential to revolutionise the automotive manufacturing process.
Handtmann is entering the production of large structural parts with the successful commissioning of a Carat 610 extended from Bühler AG with a clamping force of 61,000 kN and a shot weight of up to 128 kg of aluminium.
For electric vehicles, for example, large battery casings or battery frames up to two metres in length can be produced in aluminium. Complete front or rear sections of a car can also be cast in a single piece. Handtmann has already launched the first projects with German carmakers.
With this investment, Handtmann is demonstrating its entrepreneurial spirit and innovative orientation. Megacasting is an important element of the Handtmann strategy for supporting its customers in the transformation and is deliberately being established at the headquarters in Biberach in order to strengthen the competitiveness of the German automotive industry. Investments in new processes and technologies are the key to ensuring long-term growth, innovation and competitiveness in Germany and Europe.
Megacasting has allowed Handtmann to enter new product areas. In line with the motto ‘We deliver transformation’, Handtmann will continue to increase its competitiveness and reposition itself as a reliable die caster and development partner with over 150 years of experience.
Dirk Seckler (Managing Director Sales and Technical Development, Light Metal Casting division): ‘We recognised early on that we would have to transform ourselves from a pure built-to-print company to an innovative competence and solution provider. This also includes actively shaping the transformation through innovation. By entering the megacasting business, Handtmann is taking on a pioneering role. We are the competent partner for our customers in the transformation of the automotive industry.’
To commission the new megacasting plant, the complete casting cell and the upstream and downstream processes in production were reorganised and optimally aligned with each other. This is a basic requirement for implementing efficient production.
Heiko Pfeiffer (Executive Vice President Production, Light Metal Casting Division): ‘The introduction of megacasting in the automotive industry marks a turning point in vehicle production. The ability to produce large and complex structural components in a single casting allows us to reduce production time, improve material efficiency and increase the structural integrity of vehicles. Megacasting is a key driver of innovation and competitive advantage in modern production processes.’
The advantages of large components cast in a single piece primarily include the reduced manufacturing complexity with a reduction in purchasing and logistics costs. Production process steps are saved and labour-intensive joining and finishing steps such as welding and milling are avoided. Weight in the body is saved, which is particularly relevant for electric vehicles. Megacasting is also of interest from a sustainability point of view, because larger components made of one material offer advantages in vehicle recycling.