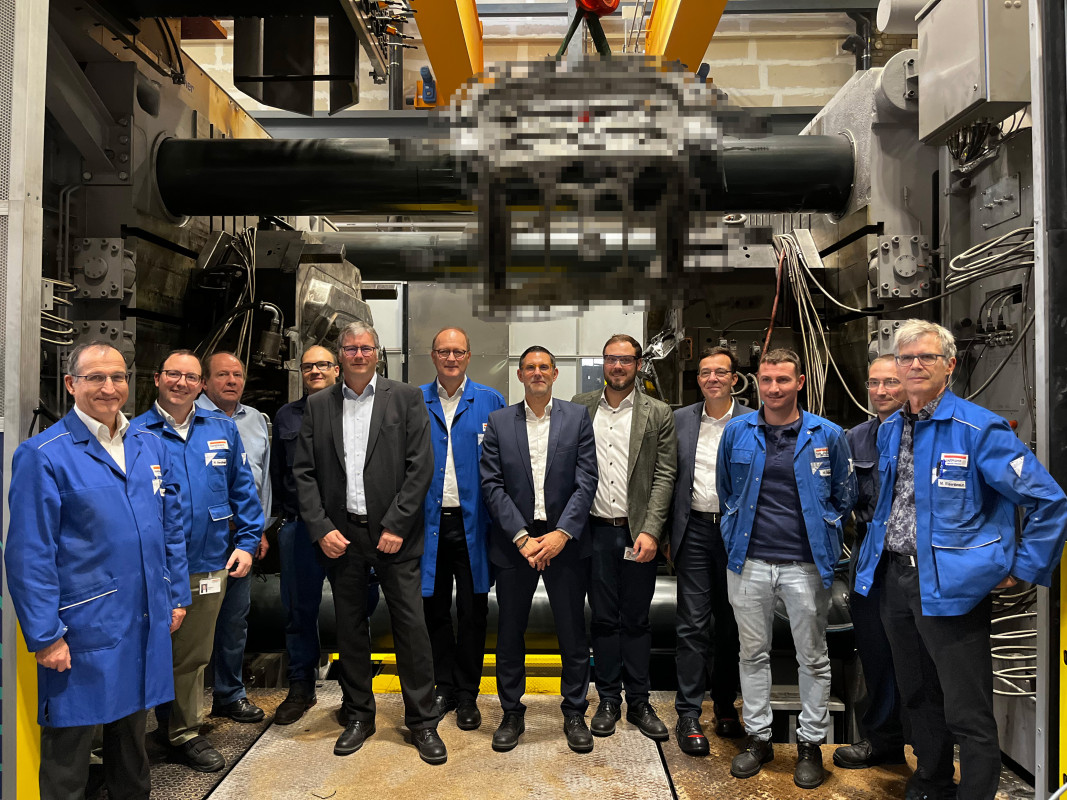
Vor zwei Jahren fiel der Startschuss für das innovative Druckgussverfahren, in welches Handtmann Investitionen im Millionenbereich getätigt hat. Ungefähr eineinhalb Jahre nach dem Spatenstich wurde am 25. Oktober 2024 zum ersten Mal ein Serienteil auf der neuen Megacasting Maschine gegossen.
Handtmann ist die größte familiengeführte Leichtmetallgießerei in Europa mit Hauptsitz in Biberach an der Riss und weltweit fünf Produktionsstandorten in Deutschland, der Slowakei und China.
Megacasting bezeichnet typischerweise das Gießen von sehr großen Metallteilen, deren Herstellung spezielle Gießtechniken und Maschinen erfordert. International ist Megacasting bereits eine aufstrebende Technologie, insbesondere in China und den USA. Das Druckgussverfahren hat das Potenzial, den Herstellungsprozess von Automobilen zu revolutionieren.
Handtmann steigt durch die erfolgreiche Inbetriebnahme einer Carat 610 extended des Herstellers Bühler AG mit 61.000 kN Schließkraft und einem Schussgewicht von bis zu 128 kg Aluminium in die Produktion großer Strukturteile ein.
Für Elektrofahrzeuge können beispielsweise große Batteriegehäuse oder Batterieahmen mit bis zu zwei Metern Länge in Aluminium hergestellt werden. Auch komplette Vorder- oder Hinterwagen eines Automobils können damit an einem Stück gegossen werden. Die ersten Projekte mit deutschen Automobilherstellern hat Handtmann bereits gestartet.
Mit der Investition beweist Handtmann sein Unternehmertum und seine Innovationsorientierung. Megacasting ist ein wichtiger Baustein der Handtmann Strategie zur Unterstützung seiner Kunden in der Transformation und wird bewusst am Hauptsitz in Biberach etabliert, um die deutsche Automobilwirtschaft in ihrer Wettbewerbsfähigkeit zu stärken. Investitionen in neue Prozesse und Technologien sind der Schlüssel, um langfristiges Wachstum, Innovation und Wettbewerbsfähigkeit am Standort Deutschland und Europa zu sichern.
Für Handtmann gelingt durch Megacasting der Eintritt in neue Produktbereiche. Gemäß dem Leitmotto „Wir liefern Transformation“ wird Handtmann seine Wettbewerbsfähigkeit weiter steigern und sich als zuverlässiger Druckgießer und Entwicklungspartner mit über 150 Jahren Erfahrung neu positionieren.
Dirk Seckler (Geschäftsführer Vertrieb und Technische Entwicklung, Geschäftsbereich Leichtmetallguss): „Wir haben früh erkannt, dass wir uns vom reinen „Built-to-Print“ zum innovativen Kompetenz- und Lösungsanbieter transformieren müssen. Dazu gehört auch, die Transformation durch Innovation aktiv zu gestalten. Durch den Einstieg in das Megacasting übernimmt Handtmann eine Vorreiterrolle. Wir sind in der Transformation der Automobilbranche der kompetente Partner für unsere Kunden.“
Zur Inbetriebnahme der neuen Megacasting-Anlage wurden in der Produktion die komplette Gießzelle sowie die vor- und nachgelagerten Prozesse neu ausgerichtet und optimal aufeinander abgestimmt. Dies ist eine Grundvoraussetzung, um eine effiziente Produktion umzusetzen.
Heiko Pfeiffer (Geschäftsführer Produktion, Geschäftsbereich Leichtmetallguss): „Die Einführung von Megacasting in der Automobilindustrie markiert einen Wendepunkt in der Fahrzeugproduktion. Durch die Möglichkeit, große und komplexe Strukturbauteile in einem einzigen Guss herzustellen, können wir die Produktionszeit verkürzen, die Materialeffizienz verbessern und die strukturelle Integrität von Fahrzeugen erhöhen. Megacasting ist ein wesentlicher Treiber für Innovation und Wettbewerbsvorteile in modernen Produktionsprozessen.“
Die Vorteile von großen Komponenten aus einem Guss umfassen vor allem die reduzierte Fertigungskomplexität mit Senkung von Einkaufs- und Logistikkosten. Verfahrensschritte in der Produktion werden eingespart und arbeitsintensive Füge- und Nachbearbeitungsschritte wie Schweißen und Fräsen vermieden. Gewicht in der Karosserie wird eingespart, was insbesondere bei Elektrofahrzeugen von hoher Relevanz ist. Auch aus Nachhaltigkeitsaspekten ist Megacasting interessant, denn größere Bauteile aus einem Material bieten Vorteile im Fahrzeugrecycling.