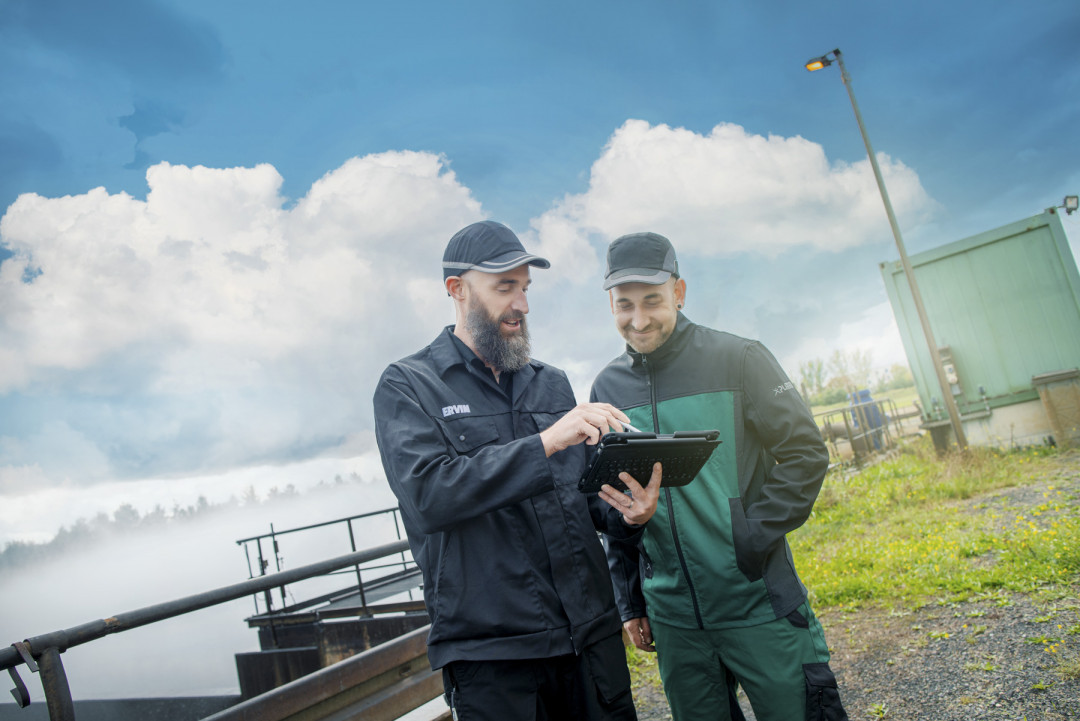
Ervin Europe has announced a series of innovative measures to achieve net-zero emissions by 2030 (15 years earlier than required by the German government). Highlights of the Ervin sustainability programme include switching from natural gas to hydrogen as an energy source, generating electricity from renewable sources, and helping customers reduce their Scope 2 and Scope 3 emissions.
While sustainability has become an increasingly important topic for many companies in recent years, the idea of sustainability is not new at Ervin. The company started out in the early 1920s with an innovative approach to recycling steel scrap. Its use has led to improved productivity, reduced resource consumption and reduced waste in its customers' blasting process, creating a circular economy. Family-owned for over 100 years, Ervin has always taken a sustainable approach to sales, production and growth.
Dr Wolfgang Assmann, Managing Director of Ervin Europe, explains: ‘When our founder, John F. Ervin, invented the process for manufacturing abrasives from scrap steel, it was important to him to do more with less. This philosophy was passed down from his descendants to the family members who run the company today. As a family-owned business, Ervin has the freedom to make the right decisions for the long term, while also bearing responsibility for the future. This means that our sales, production and growth plans have always been sustainable and always will be. Measures already taken, as well as future ones – including the switch from natural gas to hydrogen – enable us to help customers increase their sustainability by reducing their Scope 2 and Scope 3 emissions.’
In 2014, Ervin opened a new production facility for steel grit abrasives in Glaubitz, Germany. The central location of this modern, efficient plant in the middle of Europe helps to minimise not only logistics costs but also to reduce Scope 3 emissions from rail and water transport. Warehousing enables Ervin to reduce transport.
Ten years after the opening, René Spandler, Plant Manager, reports a number of interesting initiatives: ‘Ervin uses electric arc furnaces to melt the steel scrap, which results in much lower carbon emissions than the production of crude steel. However, we have actively sought opportunities to utilise alternative renewable and greener energy sources. A new wind turbine now supplies our plant with renewable electricity and will reduce our Scope 2 emissions by 20%. We are already using oxygen to reduce our Scope 1 and Scope 2 emissions. Ervin is also proud to be a partner in the recently announced Hydrogen Network Central Germany. This will enable us to replace natural gas with hydrogen starting in 2027 and achieve a significant reduction in Scope 1 emissions, as no CO2 is emitted when hydrogen is combusted. Compared to 2023, these measures will reduce our carbon emissions in production by 80% within four years.’
Ervin's production process uses over 98% recyclable raw materials to create the highest quality abrasives, which consistently deliver the best possible results for Ervin's customers. Paul Abram, Technical Director, says: ‘The combination of high durability and high energy transfer of our abrasives means that our customers use less abrasive per component and generate less waste, making their blasting processes more sustainable.’ Thanks to this approach, Ervin is able to work with its customers to reduce Scope 2 emissions from their blasting process.
"Waste disposal is becoming an increasing pan-European issue as governments introduce new laws and fines to encourage companies to reduce their waste. Comparative tests repeatedly show that Ervin products reduce the amount of material used in blasting by at least 10%. Consequently, waste is also reduced by 10%, so Ervin customers benefit twice over: from cost savings due to the long service life of our steel and stainless steel abrasives and from a reduced environmental impact. In our production plants, the size, hardness and microstructure of our abrasives are strictly controlled. The greater energy transfer results in higher cleaning performance and lower costs for our customers, including lower energy consumption,’ adds Paul Abram.
It is not only the product quality that can bring benefits to customers, but also the service and support on site. Paul Abram continues: ‘Our sales and technical team regularly visits customers and uses the Ervin test centre in Glaubitz to work with customers to optimise machine settings and abrasive selection to maximise productivity and reduce blasting costs. Many customers who have converted to Ervin abrasives report a reduction in rework, which significantly reduces costs and maintains good working relationships with their customers.’
Ervin recently launched a new mineral-based degreasing additive, AMAPURE. Oil or grease from the workpieces often gets into the operating mixture, which can lead to an excessive loss of usable abrasive. Amapure absorbs the oil and grease, cleaning the operating mixture and thus extending the service life of the abrasive, the workpieces and the equipment. At the same time, waste and costs for the customer are reduced.
Ervin is also keeping pace with modern packaging trends. As the only abrasive manufacturer to have delivered its standard material in recyclable paper bags since the 1960s, Ervin is way ahead of its competitors. Ervin's production facilities are working closely with leading packaging suppliers to reduce or eliminate non-recyclable packaging materials. Across the entire Ervin Europe organisation, there are many other initiatives in place to operate in a more sustainable way: from company vehicles running on electric power, to increased use of video conferencing, to an ongoing programme of digitising information to reduce paper use, improve accuracy and make better use of precious resources. Ervin continues to invest heavily in its employees and communities.
Wolfgang Assmann explains: ‘We are entering the second century of our company's history and our commitment to sustainability is as strong as ever. The programme of action we have put in place, and our constant search for further improvement opportunities, will see us achieve a net zero emissions position by 2030, 15 years earlier than required by the German government. We are sure that John F. Ervin would be very proud of what we have achieved and excited about our future plans.’