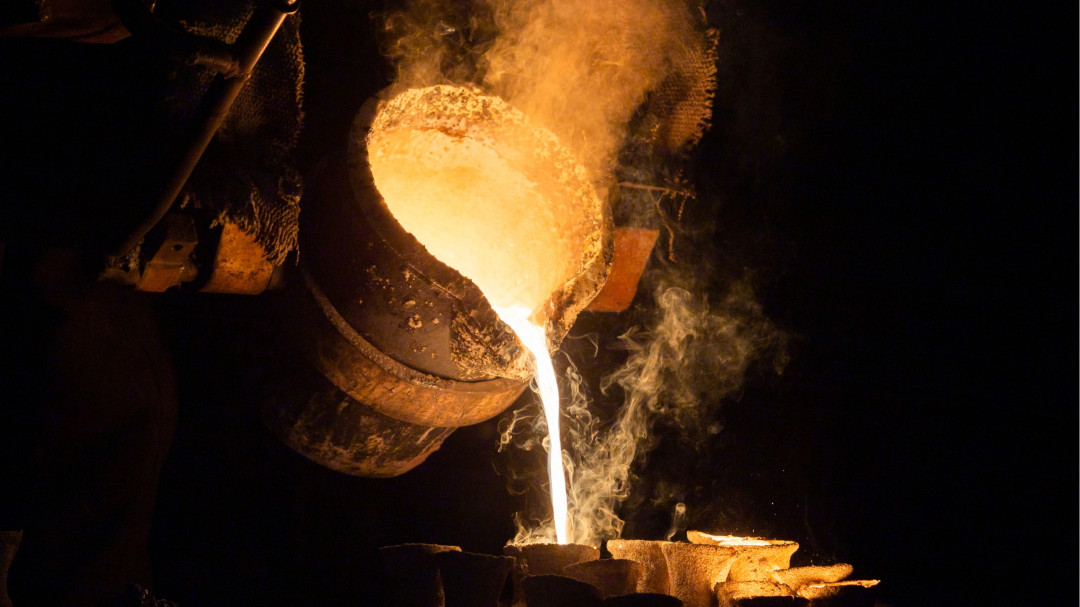
Rising energy prices, increasing political regulations, climate change: the foundry industry is facing major challenges. The ENGAGEMENT project is researching how the company's own CO2 footprint can be reduced by digital methods. The German Federal Environmental Foundation (DBU) is funding the joint project of the University of Applied Sciences Kempten for two years with around 188,000 euros.
Casting, an indispensable manufacturing process in industry, is particularly energy-intensive and thus has both ecological and economic impacts on companies. The ENGAGEMENT joint project supports foundries in recording their in-house energy and material consumption and calculating the CO2 footprint of their castings. ‘Reducing the company's own CO2 footprint is essential for the foundry industry in the long term,’ explains project manager Professor Frieder Heieck.
The team is therefore developing a digital guideline for process analysis, which will also include the ‘Carbon Footprint Calculator FRED’ for recording and optimising CO2 emissions. Particularly in times of a shortage of skilled workers and demographic change, the project also makes an important contribution to securing and passing on company-specific knowledge. The integration of an assistance system ensures that the expertise of the process experts in the companies is retained and can be used in a targeted manner. The German Foundry Association makes the results available throughout the industry. This way, all companies should benefit from these newly developed methods and sustainably reduce their carbon footprint.
In addition to the IPI – Institute for Production and Information Technology at the University of Applied Sciences in Kempten, the research consortium includes the Federal Association of the German Foundry Industry (BDG), Pinter Guss GmbH, the Kempten-based iron foundry Adam Hönig AG, ABP Induction Systems GmbH and the Vesuvius Group.