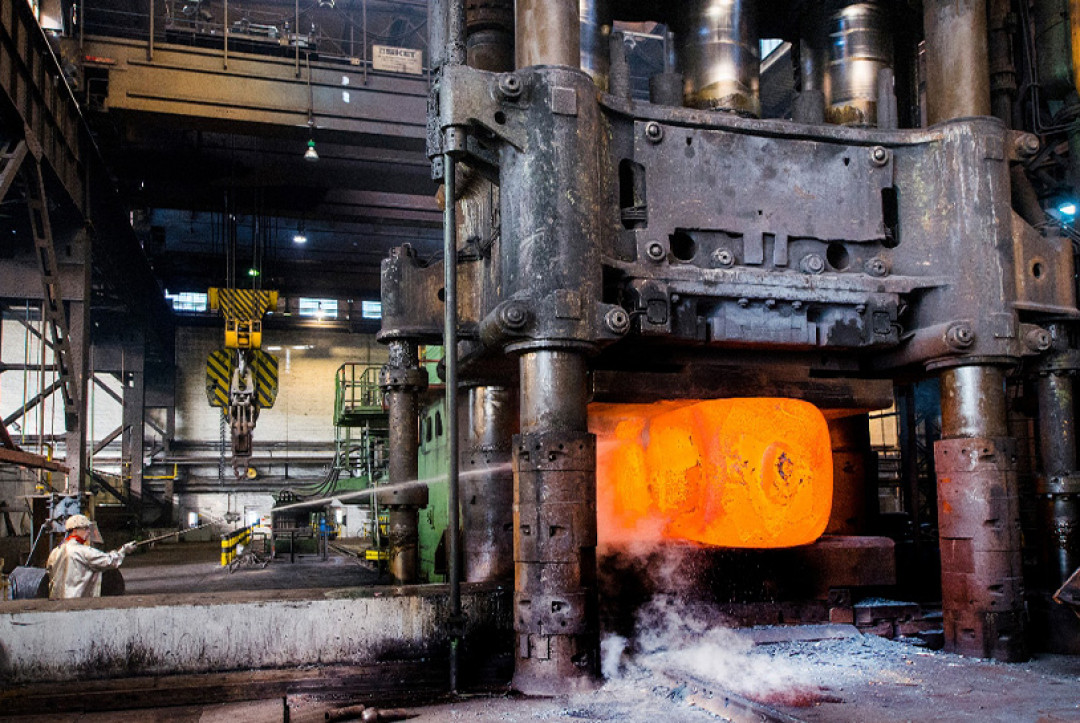
Schmiedewerke Gröditz and Kind & Co Edelstahlwerk intend to work more closely together in future. The sister companies from the GMH Gruppe are committed to providing new solutions for customers in the aluminium die-casting industry.
Since September last year, Kind & Co. has been part of the GMH Gruppe, which Schmiedewerke Gröditz has belonged to for more than 25 years. This integration enables both companies to optimally dovetail their expertise. Now one of the first projects has emerged from this collaboration. Its centerpiece is a die-casting tool with a total weight of 30 tonnes. Schmiedewerke Gröditz manufactures the large mould inserts using the upsetting/reverse forging process – with individual weights of 8.3 and 9.6 tonnes. At the same time, Kind & Co supplies the smaller mould inserts with a precise fit and ensures the final hardening treatment of all inserts in a state-of-the-art vacuum furnace. This process guarantees maximum durability and outstanding performance from the moulded parts.
The collaboration also includes the expertise of a renowned German mould maker, which is responsible for designing the mould, and an international die-casting manufacturer, which is responsible for production. The result: an end-to-end process chain that combines quality and efficiency and offers pioneering solutions for the automotive sector.
Sustainability at centre of cooperation
"The integration of Kind & Co. into GMH Gruppe was an important step in further expanding our position as the third largest forging group in Europe. This project shows how integration and collaboration can promote innovation and set new standards", emphasises Dr Alexander Becker, CEO of GMH Gruppe. "Together, we offer our customers solutions that impress - through quality, sustainability and cost-effectiveness".
In addition to technical excellence, sustainability is at the centre of the cooperation. GMH Gruppe relies on resource-saving production processes: The primary material is melted from recycled steel scrap in electric arc furnaces, which reduces CO2 emissions fivefold compared to conventional blast furnace processes. In addition, the material cycle is closed by recycling the moulds at the end of their useful life.
Featured photo: GMH Gruppe