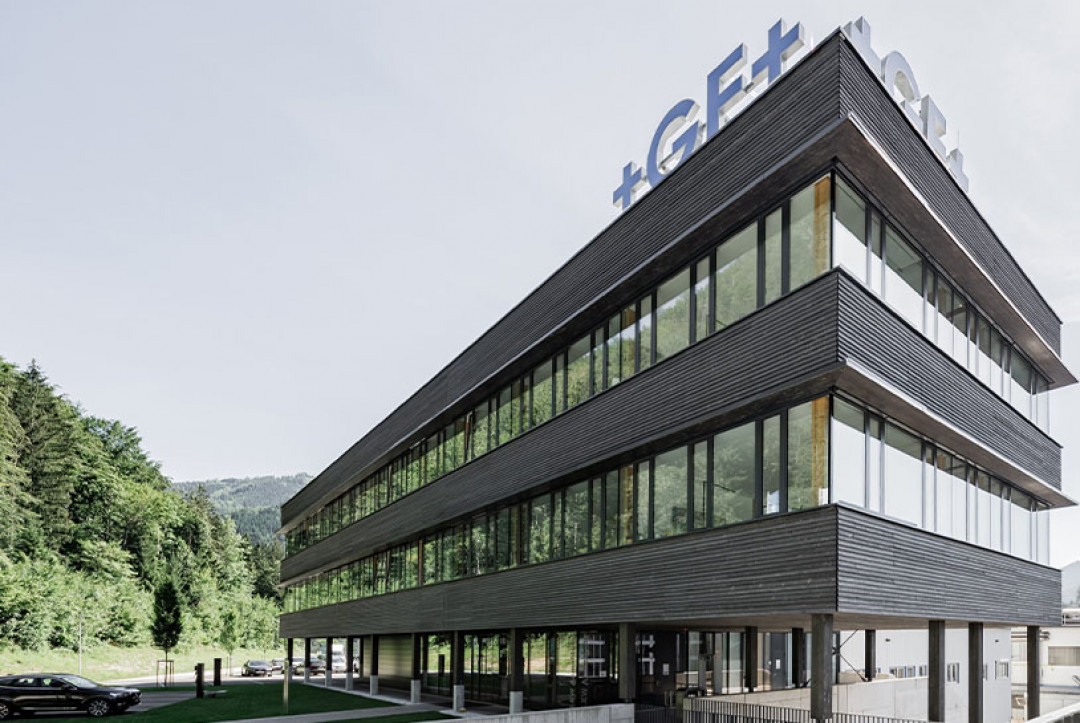
Fast set-up times are crucial in order to reduce costs, remain flexible and guarantee high quality. GF Casting Solutions relies on new systems from Emco for this purpose.
GF Casting Solutions from Altenmarkt in Styria specializes in magnesium and aluminium die-casting solutions for the international automotive industry. With around 650 employees, the company is an important regional employer in the light metal die casting sector in Austria and beyond.
The parts produced by GF Casting Solutions are mainly developed for car bodies, interiors and powertrains. The focus is on lightweight construction and ready-to-install solutions. The demands on the tools, which can weigh up to 70 tons, are becoming ever greater. Fast set-up times are a key factor here.
“We were able to reduce production time by two thirds”
GF Casting Solutions relies on CNC lathes from Emco in Hallein near Salzburg to manufacture the spare parts required for the die-casting tools. Specifically, the Hyperturn 65 Powermill G2 and, since this year, the EMCOTURN E65 CNC turning center are used here. “From the initial technical discussions to the sales process and delivery, the collaboration with Emco worked perfectly. I have also known Emco machines since I was a trainee and we knew that we were buying machines that would deliver what they promise and also work very well in terms of accuracy,” says Thomas Klade, Team Leader of Contract Manufacturing at GF Casting Solutions.
The EMCOTURN E65 lathing center is mainly used to produce screw cores. “With this machine, GF Casting Solutions has succeeded in significantly reducing processing times. The parts are collected in a pot and unloaded via the parts collection conveyor, which also eliminates door opening times. A bar loader can also be installed, which enables partially autonomous production,” explains Leopold Zenz, Head of Sales for Emco in Austria, who also highlights the special features of the machine: ”It is a universal lathe with a 65 mm spindle opening, counter spindle, radial turret with twelve driven tools and a Y-axis with an 80 mm stroke.”
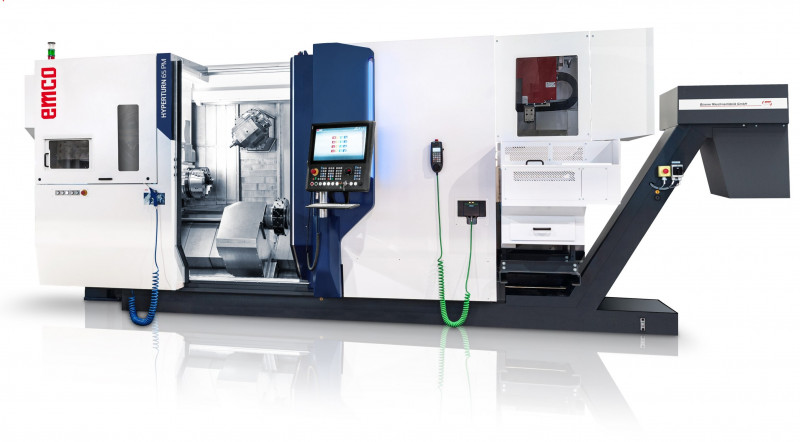
For team leader Klade, one of the biggest advantages of the new system is the time saved. “If you give the system an order to produce 15 pieces, for example, they are produced fully automatically within a certain period of time and engraved according to the requirements of our plant in Altenmarkt,” he explains. “They are then transferred to a conveyor belt via an ejector. In between, no more handling is required and we were able to reduce the production time by two thirds.”
Featured photo: GF Casting Solutions
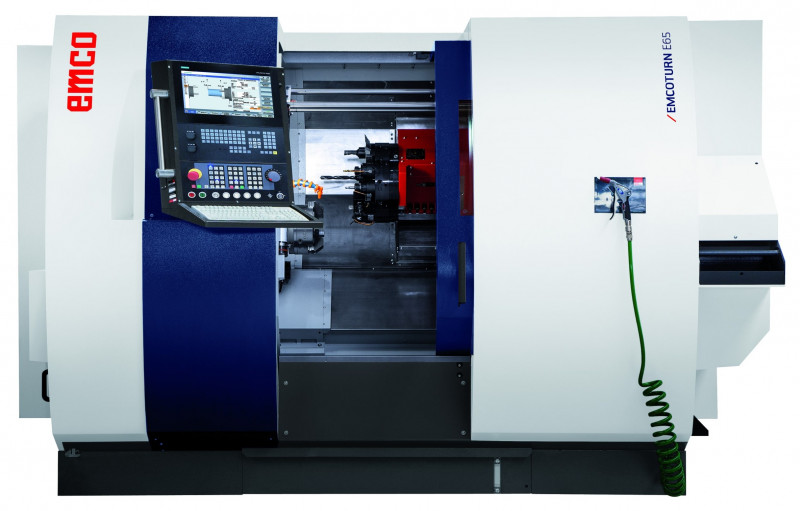