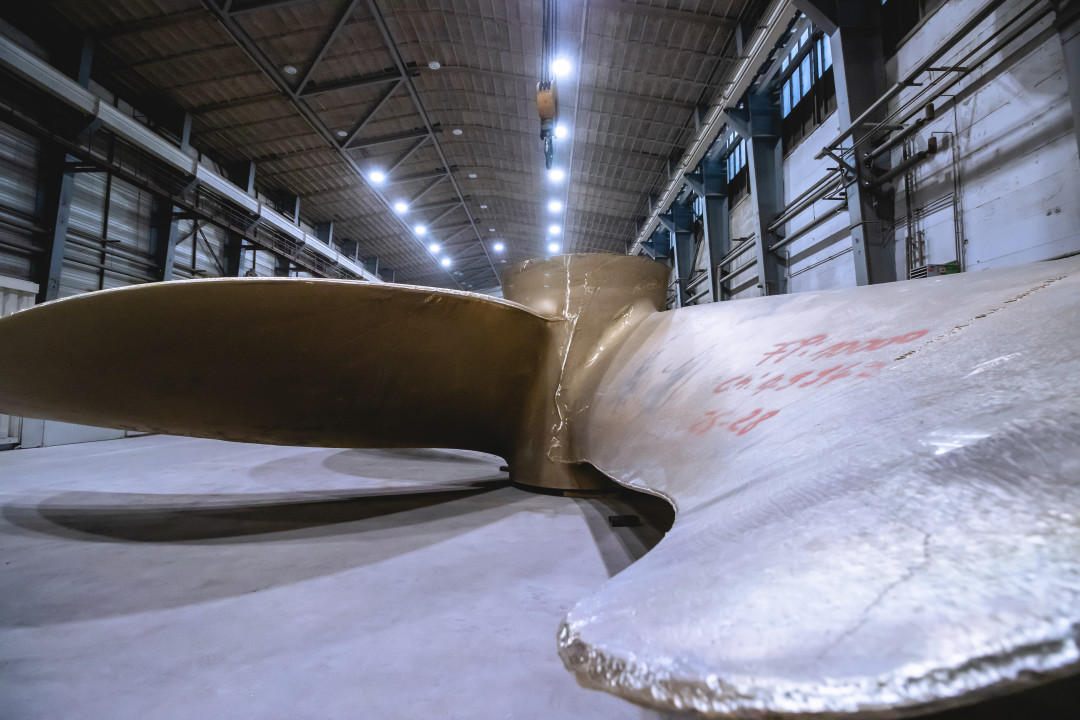
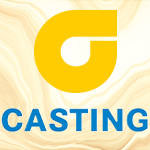
Mecklenburger Metallguss GmbH is a dynamic company specialising in the large-scale production and international distribution of ship propellers. With a wealth of experience spanning 75 years, the company is one of the global players and operates successfully among the top ten international propeller manufacturers. The company is confidently looking to the future and is expanding its portfolio by introducing new product lines.
BY CHRISTIAN THIEME, HAMMINKELN
About an hour's drive south of Rostock lies Waren, the centre of the Mecklenburg Lake District. The spa town, with around 21,000 inhabitants, borders on the Müritz, the largest lake in Germany. The local harbour serves as the starting point for numerous passenger ships that call at the banks of the Müritz and attract tourists to the region all year round. Although Waren is known as a maritime town, many visitors do not immediately realise that ship propellers for the world's largest container ships are also manufactured here.
Today's Mecklenburger Metallguss GmbH (MMG) has been producing ship propellers at this location for 75 years. Although the site can look back on an even longer history, the maritime focus only developed in the post-war period. In 1948, the Soviet military administration demanded an increase in shipbuilding capacity. Due to its favourable location near the coast and its extensive expertise with qualified personnel, the foundry in Waren was commissioned to produce cast parts for mechanical and plant engineering as well as propellers and equipment such as portholes and hatch covers for shipbuilding. Today, MMG is an internationally renowned high-tech company and is one of the world's leading manufacturers of ship propellers. Looking confidently to the future, the foundry is endeavouring to further strengthen its position and develop additional business areas.
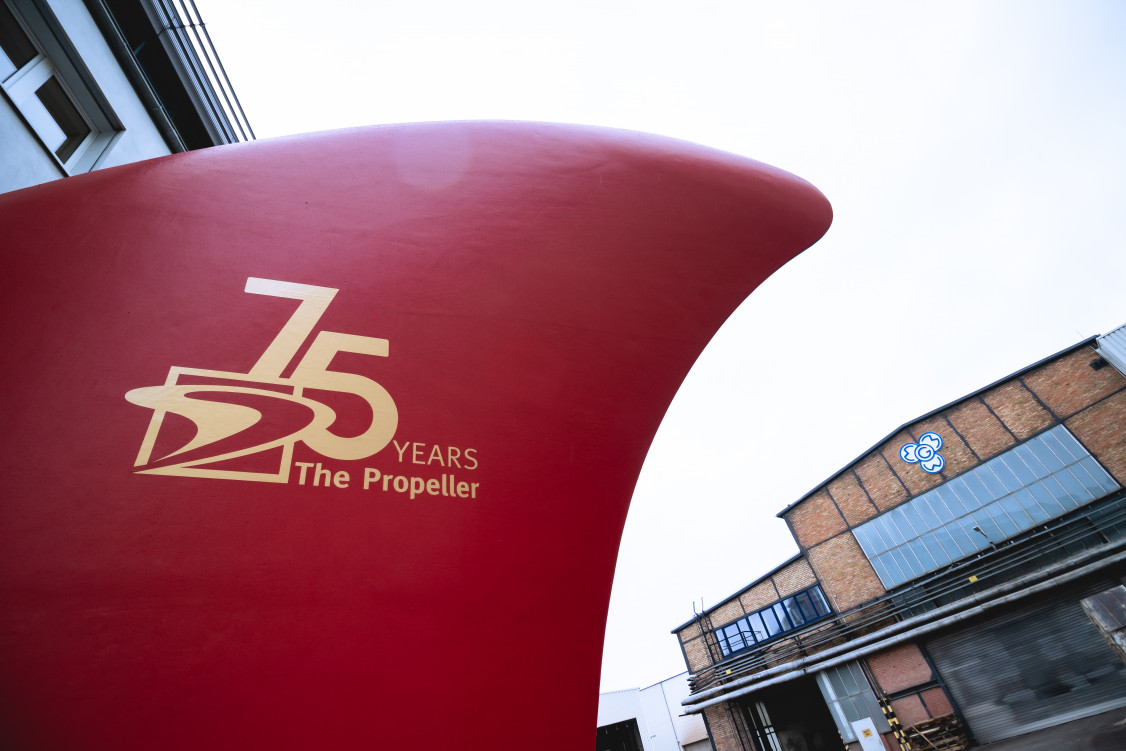
The green product attracts employees
"We celebrated our anniversary here at the site on 23 September 2023," reports Dr Lars Greitsch, Managing Director of the company. "We were able to welcome over 3,000 guests to the open day and showcase our company." The company is currently growing, is proud of its expertise and employs just over 200 people. "In the last 18 months, we have taken on around 40 new employees and have had no staff shortages," adds Greitsch proudly. More jobs are to be created in the future by opening up new business areas.
"The region offers us the advantage that we don't have to compete with many industrial companies for employees, and we have an outstanding product. In dialogue with other companies, we have noticed that young people tend to want to work in green industries. In contrast, traditional mechanical engineering and the automotive sector are having far more difficulties," Greitsch notes. He attributes this to the company's own contribution to more environmentally friendly shipping on a global scale, particularly in the retrofit sector.
Growth course thanks to international regulations
This year, the company is approaching the turnover mark of 100 million euros, its second-best result since 2015. "The business situation is positive, as shipping companies worldwide are under pressure to reduce their energy costs and CO2 emissions," explains Greitsch. This pressure on owners is the result of various factors. According to the guidelines of the International Maritime Organization (IMO), a specialised agency of the United Nations, new ships have had to meet an Energy Efficiency Design Index (EEDI) for many years. "This means that every new ship has to go through a certification process to ensure that its efficiency meets certain standards. This is checked during the final model test before the ship is built. In addition, the IMO has started to apply the energy efficiency index to existing ships on the same mathematical basis, which has led to the Energy Efficiency eXisting ship Index (EEXI)," says Greitsch.
The first retrofit pilot project was carried out in Waren in 2013. This involved replacing old propellers with more efficient ones or adding efficiency-enhancing measures, for example. There are now two different regulations in this area that shipping companies must comply with. "The IMO has issued an index for all larger merchant ships, which must be verified once and is not fulfilled by most ships," summarises Greitsch. "However, engine throttling is often sufficient to comply with the limit values." MMG benefits from the resulting lower top speed, as more efficient propellers are required for a faster journey.
"The Carbon Intensity Indicator (CII) is added to the one-off index on an ongoing basis," adds Greitsch. The CII is a measure of a ship's energy efficiency and is expressed in grams of CO2 emissions per load capacity and nautical mile. This is not calculated from the ship's technical data, but from the fuel consumption, which is set in relation to the theoretically possible cargo volume. "It is therefore a kind of transport efficiency". There are four different efficiency classes. Ships labelled E, for example, must submit an action plan that must be implemented within one year.
In addition to the internationally applicable regulations, there is further pressure from major customers who supply end customers. "Containers are booked by companies such as Amazon and Co. End customers, on the other hand, expect environmentally friendly transport," explains Greitsch. As a result, shipping companies have to achieve better efficiency classes so that the ships continue to be booked. However, the managing director notes that the classic B2B sector, such as oil tankers, is not under as much pressure.
The foundries benefit from the continuous improvement processes. In the immediate term, they offer solutions through retrofit projects, while in the long term there is demand for new ship propellers. Currently, the production quota in the retrofit sector in Waren is around 60 per cent, and the trend is rising, as Greitsch explains.
Between 70 and 90 propellers leave the factory every year. The export quota is 95 per cent, with numerous shipyards in Asia being supplied. "We see a further increase next year. However, development also depends on the new construction sector. We are already talking about projects that will start at the end of 2024 and beyond. We hope that things will then continue at a steady pace."
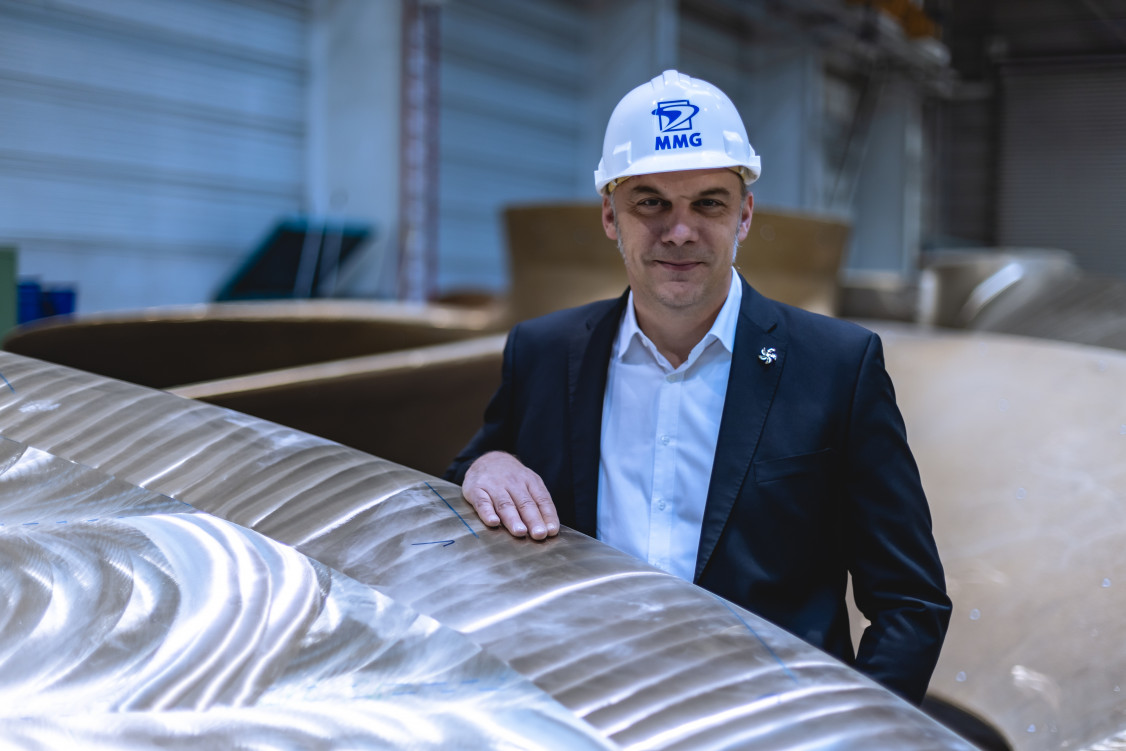
The shipping industry in transition
Efficiency is the key word in the industry. In addition to traditional optimisations to the drive train, supporting drive systems such as Flettner rotors and wingsails are increasingly being used. However, the founder is certain that they will not be able to completely replace the classic engine. The requirements for manoeuvrability and redundancy in various ship categories make emission-free shipping practically impossible. New engines that run on synthetic fuels such as methanol are therefore particularly in demand. "Maersk recently commissioned the first container ship that can run on methanol. Further ships have already been ordered," adds Greitsch. The lower energy density of the fuel makes efficiency a key driver of innovation. MMG is already contributing its own expertise to the construction process at an early stage.
In shipbuilding, it is customary to carry out a model test with a true-to-scale model. However, MMG has been using simulations in the design process for ten years. "Simulation for Design (SfD) has many advantages, as we don't have the negative scale effects from the model test, for example," explains the foundryman. The use of simulations significantly reduces costs for the owner when it comes to new construction projects. Greitsch emphasises: "It is particularly important for us to always consider the overall system in the ship, especially when auxiliary systems support the drive. We have to do a lot of convincing here so that we are involved in the design process at an early stage in order to achieve optimum efficiency".
Challenges in Germany
As far as Germany is concerned, the company is sceptical about the future. "Although we are currently also affected by rising energy costs, we can pass these on to our customers. In the long term, however, I see problems, as it will become a disadvantage for the location," states the Managing Director. The company is particularly concerned about the issue of heavy goods transport. "It has to be said quite clearly that we have a problem in the transport sector. With our unit weights of up to 110 tonnes, some bridges in need of renovation are becoming impassable for us and we are receiving light-hearted cancellations. What's worse is that there is no time horizon for when relevant bridges will be renewed. We would like to see much more solution-orientated cooperation in this area. Mecklenburger Metallguss GmbH supplies the ship propellers mainly by land to Hamburg, from where they are shipped all over the world. Alternatively, the company could use Rostock as an alternative, but this would incur high additional costs for reloading - costs that not every customer wants to bear and which would further increase the price pressure on the suppliers, as many of their competitors are located directly in the Asian shipyards.
The company has no problems with raw material shortages, as it has developed an effective model: "Basically, we have the advantage that we can use all kinds of scrap, as we have our own laboratory and can therefore alloy it ourselves. With the quantities that we produce here, we prefer to use old propellers that are melted down. In the retrofit sector, we negotiate with our customers that we get the old propeller back when we deliver a new one. This process has a double benefit: The shipowner saves money and does not have to worry about disposal. MMG takes care of the scrapping and returns the metal to its own plant, where it is reused in the material cycle. Thanks to the international alloy standard, foundries often only have to alloy minimally in order to fulfil their own high requirements.
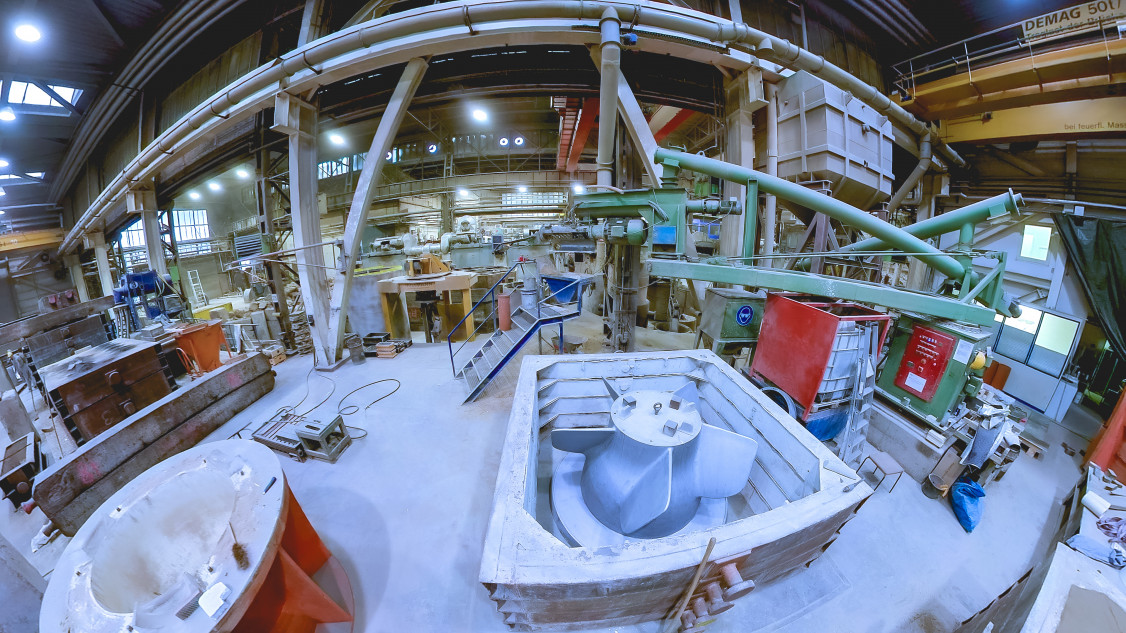
Additive manufacturing and new product branches
In addition to its established business, MMG is also working on future-oriented projects. "On the one hand, we will offer aluminium in large castings in the future. We have gained a lot of experience in centrifugal casting and are now expanding our portfolio to include larger tonnages. We are also introducing additive manufacturing," explains Greitsch. Additive manufacturing is starting with copper-based materials and will later include stainless steel and aluminium. "In collaboration with a partner, we will offer stainless steel propellers, which are necessary for ice-going ships, for example." However, the company would also like to be able to offer smaller propellers at better prices in the future and thus tap into another market.
MMG is using the Wire Arc Additive Manufacturing (WAAM) process for this. The first models of the propellers were presented at Formnext in Frankfurt (GIESSEREI 12/2023, page 26 ff.). "The challenge is to involve the classification societies that have to certify the product. There are now dedicated departments that specialise in additive manufacturing. It is important that the material properties meet the requirements. We are currently working on providing full proof that we have mastered this production method," explains Greitsch. Another milestone was reached with a drinking fountain for the customer Hamburg Wasser. "The designer created a beautiful shape with internal water channels," says Greitsch. The challenge lay in the organic design of the workpiece produced using the WAAM process. The drinking fountain received a special mention from the Baden-Württemberg International Design Award FOCUS OPEN 2023. A continuation with similar projects is planned, as MMG sees further potential in this new business field.
The implementation of large-scale robotics is also in full swing in Waren. In collaboration with the Fraunhofer Institute for Large Structures in Production Technology (IGP) in Rostock, the company is casting and building its own robot, which will later be used to machine ship propellers. Greitsch emphasises that the aim is to build up expertise that can later be made available to other companies. Thanks to its broader focus, the company believes it is well positioned for the coming years and is looking ahead with confidence.
Ship propellers are giants in the truest sense of the word. Propellers with an impressive weight of up to 110 tonnes and a diameter of more than ten metres are manufactured in Waren. These imposing models are later used on the largest container ships. The largest container ship in the world has space for 24,000 TEU (Twenty-Foot Equivalent Unit). TEU stands for "Twenty-Foot Equivalent Unit" and refers to a 20-foot standard container. Internationally, TEU serves as a standardised unit for counting these standardised ISO containers. Around 12,000 lorries would be needed to unload a ship of this size.