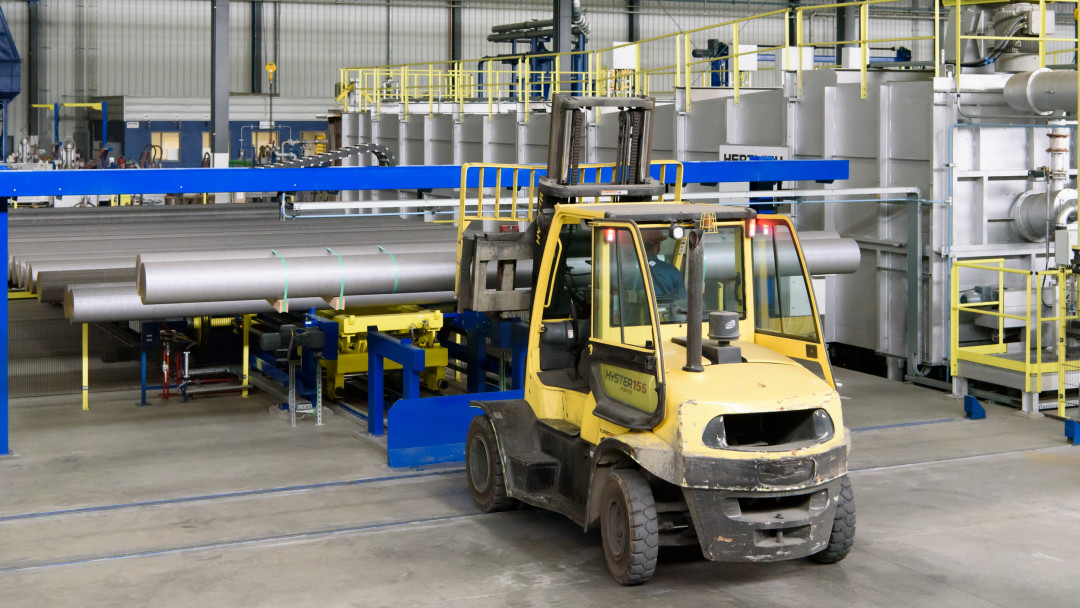
Exlabesa is expanding production at its aluminium recycling plant in the Spanish province of A Coruña and is once again relying on technology from Hertwich Engineering, a company of the SMS group. Hertwich is supplying a continuous homogenising furnace including an air cooling station, a long billet stacker and a semi-automatic PET strapping system. The new furnace complements the second melting furnace already installed and is specifically designed for the production of recycled aluminium from post-consumer scrap.
In 2018, Exlabesa had already commissioned a second continuous homogenisation plant and later also a multi-chamber melting furnace at this location, both of which were supplied by Hertwich. With the now agreed expansion, the capacity for continuous homogenisation at the plant in north-western Spain will increase by 30,000 to around 80,000 tonnes per year.
The recently commissioned state-of-the-art melting furnace is specifically designed for the production of recycled billets from post-consumer aluminium scrap that has reached the end of its life cycle. The subsequent expansion of the foundry, which centres on the new Hertwich continuous homogenising plant, will significantly increase the capacity for processing new scrap. This will make Exlabesa less dependent on the procurement of primary aluminium and at the same time conserve resources. These investments underline Exlabesa's commitment to greater sustainability and the reduction of CO2 emissions by promoting a cleaner and more efficient industry based on the principles of the circular economy. At the same time, they consolidate Exlabesa's position as one of the most advanced foundries in the world, able to meet the growing demand for this type of product.
‘Finding solutions that are tailored to the individual needs of our customers is one of the strengths of Hertwich Engineering,’ says CEO Gerold Keune. ’Our expansion of the continuous homogenising plant at Exlabesa fits perfectly into the existing production environment. Last but not least, the project is an investment in the sustainability of aluminium production and at the same time underlines our commitment to long-term cooperation and partnership. We believe in strong alliances with our customers, based on trust and shared goals."
The new plant is designed for aluminium billets with a diameter of 178 to 406 millimetres and a length of 7.0 metres, as well as for all alloys from Exlabesa's extensive portfolio. A major advantage of the Hertwich continuous billet homogenising plant over batch homogenising is the uniform treatment of the billets: In the homogenising furnace, the billets cast from molten aluminium scrap are subjected to continuous heat treatment at temperatures of up to 590 degrees Celsius. The precise temperature control during heating and holding in the furnace ensures that the billets have a uniform structure before they enter the air cooling station. This process guarantees high billet quality with optimal metallurgical properties while at the same time reducing the energy required for billet homogenisation. At the end of the production line, the billets are stacked and strapped with plastic straps.