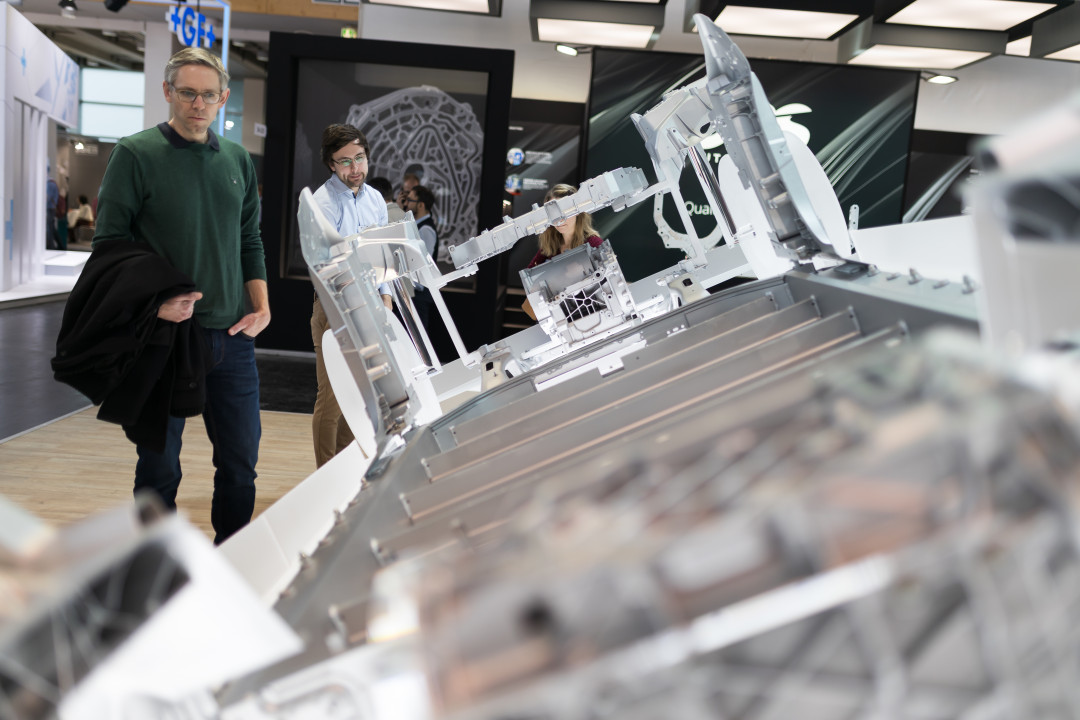
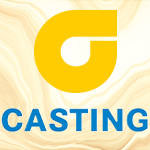
EUROGUSS 2024 was characterised by rising visitor numbers and full stands with intensive business discussions, but also concerns, especially from a German perspective: about the slowing e-car economy and the increasingly poor location and framework conditions for production in this country.
BY KATHARINA KOCH, KRISTINA KRÜGER, CHRISTIAN THIEME, MARTIN VOGT AND MONIKA WIRTH
The Nuremberg trade fair company released the formal key data for EUROGUSS just in time for the end of the die casting trade fair: 60 per cent of exhibitors came from abroad, with Europe continuing to lead the way. The focal points were Italy, Turkey, Spain, Austria and Switzerland. The turnstiles at the two trade fair entrances counted 14,341 visitors, significantly more than the 10,700 at the last edition - which, however, was also postponed from January to June 2022 due to the coronavirus pandemic. The figures are comparable with the 2020 edition of EUROGUSS - which was marginally better attended at 14,599, but did not have to contend with the onset of winter, which tends to discourage visitors and was widely publicised in the media. "In my view, the figures are all the more significant for the relevance of EUROGUSS," says Christopher Boss, Executive Director EUROGUSS, interpreting the popularity. "We were able to give the die casting industry a home and orientation in difficult times."
Economy for e-cars "Made in Germany" is sluggish
Which gets to the heart of the situation: in addition to all the technical and specialist issues, political and economic developments are hanging over the European and, in particular, the German market, which are causing die casters massive concern. Following the judgement of the Federal Constitutional Court, the German government announced the abrupt end of subsidies for the purchase of e-cars shortly before Christmas in a panic of cutbacks, which is further torpedoing the already sluggish sales of e-cars "Made in Germany" - with drastic consequences for the die casters supplying them. "We need predictable quantities because we have invested massively in this area," says Klaus Bruchner, Managing Director at Schüle Druckguss, for example. "When will electromobility take off?" asks Wolfgang Schmidt from the management team at Handtmann, against the backdrop of major investments and corresponding production volume expectations for e-parts, "What we are currently seeing is that combustion engine components are ramping up at an above-average rate."
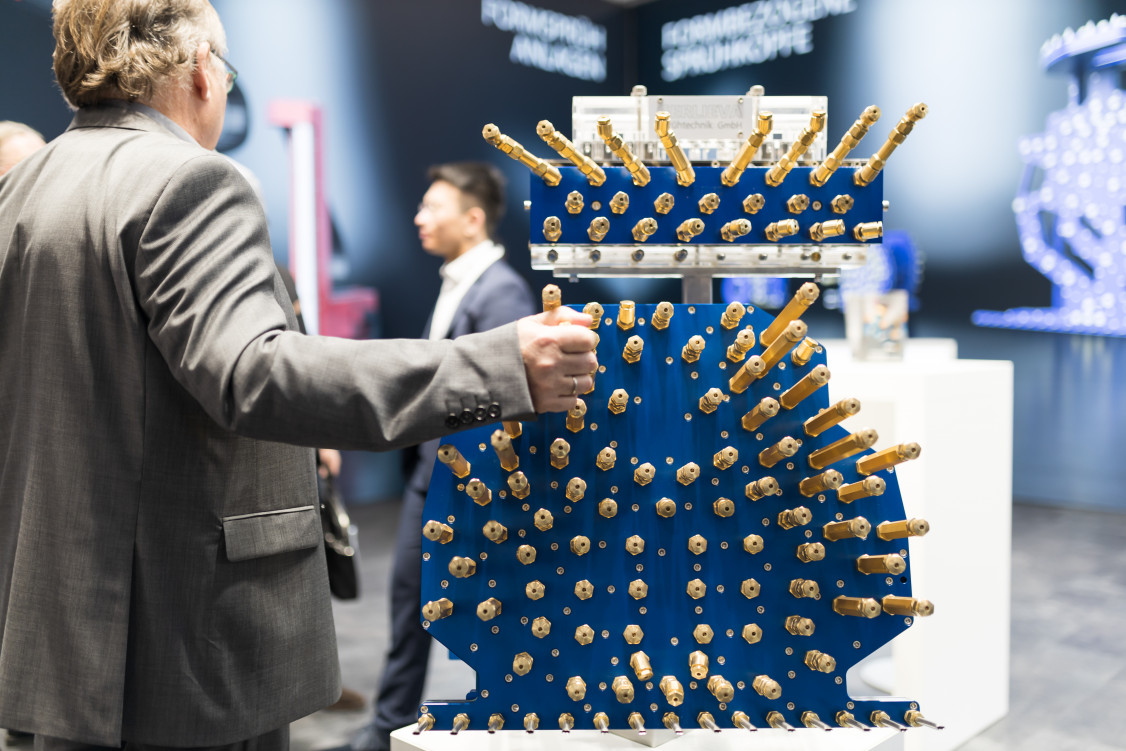
There is still potential for die casting
These are undoubtedly bizarre market caprices that are difficult to calculate from a business perspective and have a highly volatile effect. These market dynamics - also caused by political factors - are taking place against the backdrop of an unstable economic policy situation, particularly in Germany. "A lot has to happen. We expect politicians to improve the conditions for business locations, reduce bureaucracy and ensure that the industry receives an appropriate, good electricity price," says Gerd Röders, Managing Director at G.A. Röders. The longing for stable, reliable framework conditions can be heard in every conversation. Bureaucracy with ever new laws and requirements, high electricity prices - these are the most important issues.
At least in the German market - after all, the die casting business model is not fundamentally in question; on the contrary, it is booming. "We are convinced that there are many opportunities to advance the die casting process even further. In the housebuilding and infrastructure sectors, for example," says Alexander F. Marks, Managing Director at Oskar Frech GmbH, citing the example of sanitary fittings. "We still work a lot with brass components here, which are produced using gravity die casting or low-pressure die casting. The transition to zinc die casting offers enormous opportunities in terms of unit costs." Growth potential that is actually being utilised in some areas. "We have succeeded in winning many new projects for the foundry in Kitzingen," says Franken-Guss Managing Director Josef Ramthun, "We will be investing heavily to even expand our capacities."
Gigacasting is running - especially in China
And, of course, there is the perennially trending topic of mega- or gigacasting, which refers to the casting of particularly large car body parts on machines with a particularly high clamping force. Germany's automotive industry, for many years the global flagship and market leader for combustion models, is still struggling in this area. Young manufacturers such as Tesla or some Chinese car manufacturers and also Volvo - which is known to be in Chinese hands - are more radical here.
Fittingly, machine manufacturer Bühler from Switzerland announced its latest deal on the fringes of the trade fair: Chinese automotive supplier Duoli Technology is buying four new Carat 920 machines. The order is one of the largest single orders for the Bühler Group's megacasting business. The two-platen technology with clamping forces of 10,500 to 92,000 kN is specially designed for the production of large and complex parts such as front and rear underbodies in one piece.
Well-received guided tours gave visitors to the trade fair an overview of where Giga-Casting is heading. Presentations by practitioners on the implementation of the new technology were fully booked. For example, Volvo Cars reported on "Lessons Learned" at the Die Casting Day - the company is currently in the process of bringing Gigacasting to series production maturity in plants in Sweden and Slovakia. And the largest machine ever to be seen on the exhibition grounds in Nuremberg, a huge deburring press from the North Bavarian mechanical engineering company Aulbach Automation abk Pressenbau, was one of the crowd-pullers.
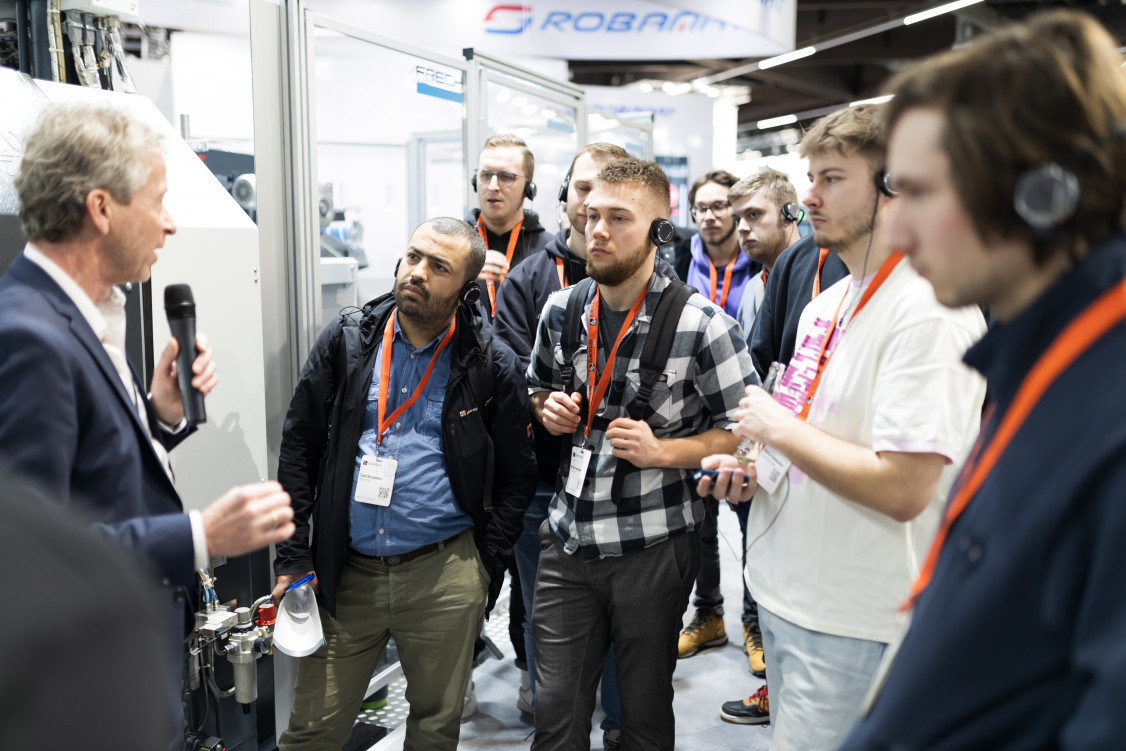
Exciting topics such as automation and AI
The dynamism in the die casting industry was unmistakable at EUROGUSS. The exhibitors not only presented impressive exhibits, but were also convincing in terms of content. Topics such as automation, production interlinking and the use of artificial intelligence are increasingly taking centre stage. Topics that offer foundries new opportunities. Production processes can be linked ever more easily through the use of highly flexible driverless transport systems and robot or portal solutions.
Solutions such as "Cybernetics", a technology from Austrian machine manufacturer Fill, are implemented in the company's own machines and enable the monitoring of complex individual processes or ensure seamless component traceability through to automated system optimisation using AI. Data visualisation through customer-specific and platform-independent dashboards provides an optimal overview and enables detailed analyses in real time.
Reis Robotics also returned to the trade fair under the motto "We are back". Following the takeover by KUKA in 2013 and the subsequent rebranding, the company was recently acquired by a consortium consisting of the Italian technology company CT Pack, the Aretè Cocchi Technology Group and the Swiss investment company FAI Holding. Reis Robotics presented its "ROBOTstar" robot controller, which is operated via an external tablet and enables precise simulation of moulding cells. This facilitates precise system monitoring without the operator having to enter the cell. The company is also planning to use Siemens hardware in the control components in the future in order to offer extended analysis and processing options for system parameters, which will be important for the digital product passport, for example.
Sand caster at the die casting trade fair
Pinter Guss from Lower Bavaria is also focussing on these developments. As a sand caster, the company was an exotic exhibitor at the trade fair, but felt encouraged to visit the fair by the good response from customers, reveals Dipl.-Ing. Felix Jaruszewski, Managing Director of the company. The presentation focussed on special components for rail and medical technology, including the housing of a DNA scanner. The company is particularly active in research projects such as "ReGain", which aims to digitally link foundry production systems in order to increase efficiency, flexibility, resilience and sustainability. The aim is to develop a new digital manufacturing concept that supports environmental sustainability in the foundry industry in line with the 2021 update of the European Green Deal. ReGAIN aims to lay the foundation for the creation of a standardised digital product passport for each foundry product and make it available within the framework of Catena-X, an open data ecosystem for the automotive industry.
The Wilhelm Funke metal foundry exhibited as an expert for prototypes and pre-series. At the joint stand with Voxeljet, the foundry demonstrated its expertise in rapid prototyping. Thanks to advanced sand printer technology, Wilhelm Funke is able to go from digital data set to finished product in just five working days. The technology is mainly used for gearboxes for cars, motorbikes and helicopters. The company pays particular attention to the production of highly complex components that are characterised by their functional integration - a focus that is proving very popular in Nuremberg. "We have surprisingly good discussions here and many interested parties come to us with specific projects," says Quality Manager Florian Topp.
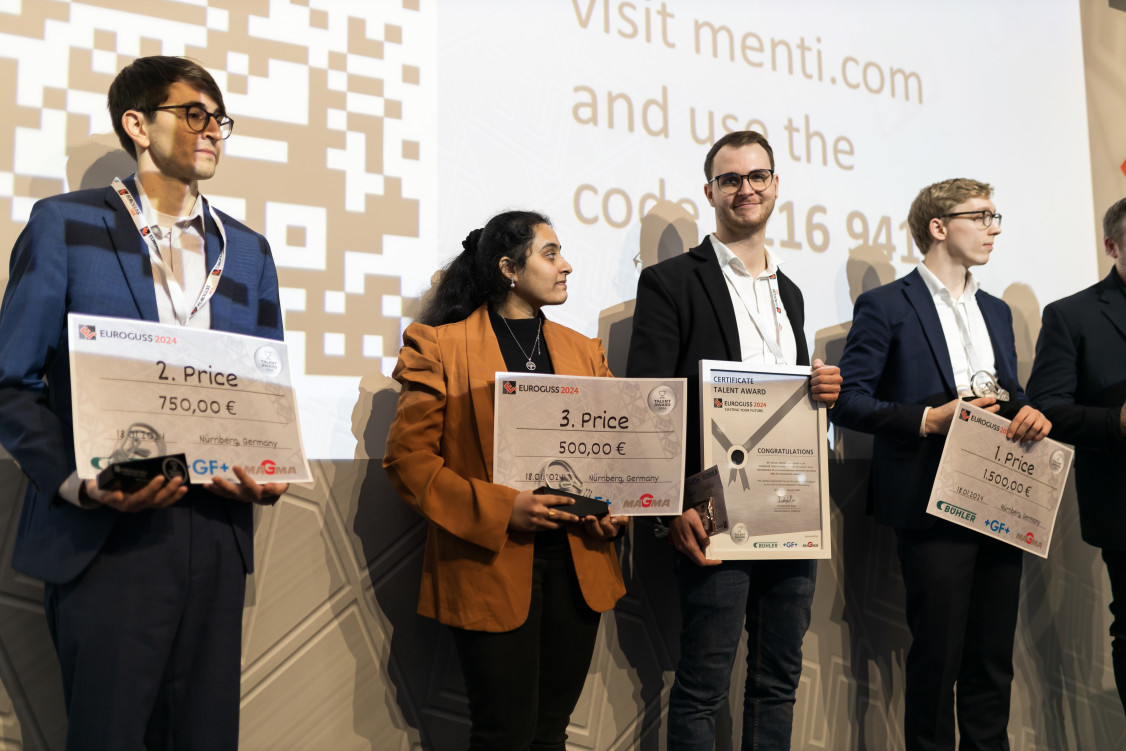
Student Day with Talent Award
The final day of the trade fair was all about promoting young talent in the industry. Under the motto "Student Day", prospective engineers were offered a comprehensive programme with keynotes, specialist presentations and guided tours. A live survey conducted among the participants revealed that the majority of them had little prior knowledge of the topic of die casting - a complete success for the organisers.
In his keynote speech "Casting without limits - what competitive technologies do casting processes have and where are the limits of economic efficiency and feasibility?", Prof. Dr Sven Roeren discussed the challenges and opportunities in the design of die casting machines. He shed light on the tension between technical feasibility and economic viability and provided valuable insights into which production technologies can play to their strengths under different conditions. The students profited Roeren's pragmatic approach and he encouraged them to ask as many inquisitive questions as possible.
The students were able to deepen their knowledge during a guided tour, where they had the opportunity to discuss industry-specific topics directly with experts. The spectrum ranged from research and robotics to temperature control solutions and provided participants with a wide range of insights. A particular highlight was the demonstration of a running die-casting machine at the Frech stand, which gave participants a practical insight into machine technology.
The highlight of the Student Day was the presentation of the Talent Award in the SpeakersCorner. This internationally renowned prize aims to recognise outstanding final theses in the field of die casting and to promote young talent. Five finalists had the opportunity to present their academic work in a presentation and then had to answer technical questions from the audience and presenter Franz-Josef Wöstmann. The submitted abstracts were assessed by an international, high-calibre jury consisting of representatives from industry and research. In addition, the audience had the opportunity to vote for the best presentation. The first prize of 1500 euros was awarded to Danny Rohde from the University of Kassel. Second place went to Michael Moodispaw from The Ohio State University, while Neelima Gottumukkala from TU Freiberg won both third place and the favour of the audience and won the public vote.